Biological, physical and chemical approaches are available to battle odors. Most composters would agree that simplest solutions are best. Part IV
Craig Coker
BioCycle August 2012, Vol. 53, No. 8, p. 21
This article series examines the intricacies of odor management: how and where odors are generated, measured, and perceived; how they are managed through good process control; how they are controlled with technology; and how to manage the public outreach related to organics recycling odors.
Biological systems use microbes to consume odorous compounds in the process exhaust air of composting. Many of these same microbes are also present in the compost piles. Physical systems use processes like washing, dilution or filtration to reduce odor concentrations in the exhaust air. For example, scrubbers wash pollutants out of the air in an engineered system similar to how rain makes the air smell clean afterwards. Chemical systems use a designed reaction, like oxidation, to change the chemical nature of an odor. For example, hydrogen peroxide can be used to oxidize hydrogen sulfide (the odor of rotten eggs) to elemental sulfur and oxygen.
Odor treatment technologies share a common objective — to reduce odorous chemical concentrations to below the Recognition Threshold (RT), if not below the Detection Threshold (DT). As noted in Part 3, the RT can be several orders of magnitude higher than the DT, so it can be much more difficult to reduce odors below the detection threshold. But this is where the sharp focus of odor science and the predictive nature of engineered odor solutions run up against the subjective nature of emotional personal reactions to malodors and the regulation of odors under a legal “nuisance” standard rather than a numerical emission limit. Even if an odor has been reduced below the RT, it can still be perceived, and complained about, as a nuisance.
Biological Systems
The primary biological system used for odor control is biofiltration. Biofiltration refers to multiple technologies, including bioscrubbers, biotrickling filters and biofilters. Most composting facilities with a biological odor control system use biofilters, which employ microorganisms to remove odorous air pollutants. The air flows through a packed bed and the pollutant transfers into a thin biofilm on the surface of the packing material. Microorganisms, including bacteria and fungi, reside in the biofilm and degrade the pollutant. The biofilter bed can be a separate unit or can be integral to the compost pile, usually as a cap or covering of the pile or windrow.
In separate bed systems —commonly used with in-vessel and aerated static pile composting — air is introduced through a network of perforated pipes at the base of the bed. These pipes are usually embedded in gravel, which acts both as an air plenum to distribute the exhaust evenly through the bed and as a barrier to keep fines from the organic layer above from clogging the pipes. A thick bed of biofilter media, usually 4- to 5-feet deep, lies on top of the gravel (Figure 1). Biofilters are usually designed for a specific gas retention time to treat the odorous air, which is on the order of 45 to 60 seconds.
With windrow composting, a cap of screened or unscreened compost on top of the windrow can act as an in-situ (in-place) biofilter. This approach was developed in California primarily to reduce odor emissions but it became quickly apparent that it was potentially a method to reduce the volatile organic chemical precursors of ground-level ozone (smog), a significant air quality problem in most of the state. A compost cap consists of 2 to 4 inches of screened compost, 6 to 8 inches of unscreened compost or 12 inches of woody overs. The cap acts as a filter media that odor molecules must pass through so using screened material increases the surface area of the particles in this filter. The advantage of higher surface area is there is more room for microbes to live on the surface of compost particles (so there is greater metabolism of odorous compounds). The drawback, however, is the finer texture of screened compost reduces air flow through this compost cap.
The author has used both screened and unscreened compost caps and they can be tricky to install properly. If the biofilter media is too finely screened and/or gets too far down the sides of the windrow, it can block off the air flow supporting the chimney effect and starve the windrow of oxygen.
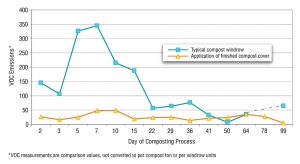
Figure 2. Effectiveness of compost caps on VOC emissions (Source: San Joaquin Valley Unified Air Pollution Control District)
Several different types of materials can be used as a biofilter media. Media normally consist of an organic substrate to house microbial communities and a bulking agent to ensure adequate porosity for air flow without significant backpressure on the blowers (too much backpressure lowers the airflow of a blower). A compost-woodchip mix is commonly used, but some biofilters use a combination of peat, soil, compost and wood chips. One configuration uses lava rock (also known as cinders or foamed obsidian) mixed with peat moss. These rock-peat combinations have been used in the treatment of gases that need long retention times to be metabolized, like carbon monoxide.
Another biological approach is to add a biocatalyst to a pile or windrow. One product on the market is made by Harvest Quest International and has been tested extensively by A-1 Organics in Eaton, Colorado, the largest composting company in the state. “We have worked with A-1 Organics to develop the Modified Static Aerobic Pile (MSAP) approach to composting using our biocatalyst, called HQB,” says Andrew Gregory, Vice-President of Operations for Harvest Quest. “HQB consists of a mix of proprietary thermophilic bacteria belonging to the common actinomycetes group. The HQB are applied to the surface of windrow at the ends of the rows or in the middle and don’t need to be mixed through the windrow. The bacteria spread outward and inward from the points of application at a rate of about 24 feet per day. The key to MSAP is to use a coarser grind, of 3- to 4-inch particle size and not to turn the windrow for the first 30 to 45 days.”
By not turning the windrow during the primary decomposition of organic materials, odor formation and release is reduced. “The population of microbes introduced by HQB is higher on the outside of the windrow initially, which raises the temperature of the outer layers of the windrow,” adds Bob Yost, Chief Technical Officer of A-1 Organics. “This higher temperature environment helps to metabolize volatile chemicals, like a well-functioning biofilter. For it to work properly, the windrow must have good structural porosity and adequate moisture.”
Physical Systems
The main physical approach to odor management is scrubbing, where a water and/or chemical solution is sprayed against the exhaust air to absorb the pollutants in the air into the scrubbing solution. Absorption is the process where one chemical (the odorant) is dissolved into the volume of another medium (e.g., water). Scrubbers work by directing an exhaust air stream against a water-based chemical shower. This solution usually contains chemicals such as sodium hydroxide (to remove reduced sulfur compounds) or sulfuric acid (to remove ammonia). In a scrubber, ammonia and hydrogen sulfide are converted to odorless byproducts by chemical reactions, such as:
Sulfuric acid converts ammonia to ammonium sulfate:
2 NH3 + H2SO4 <—> (NH4)2SO4
Sodium hydroxide converts hydrogen sulfide to sodium hydrosulfide and water:
H2S + NaOH <—> NaHS + H2O
Sodium hydroxide and sodium hypochlorite convert sodium hydrosulfide to sodium sulfate, sodium chloride and water:
NaHS + 4 NaOCl + NaOH <—> Na2SO4 + 4 NaCl + H2O
Ammonia and H2S can be absorbed with 99 percent efficiency in a fraction of a second because the first two conversions above are extremely rapid acid-base reactions. How fast a base can neutralize an acid is just a matter of how quickly they can be mixed. Scrubbers often contain packing media, which work primarily by spreading the liquid over an extended plastic surface to promote contact between the liquid with the passing air. Rings or saddles with more surface area create additional liquid surface, but more plastic surface also means more obstacles to air flow.
Another physical approach is to incorporate a high-carbon wood ash into the compost pile or windrow. The mechanism at work here is adsorption, which is the deposition and adhesion of one chemical (the odorant) onto the surface of another medium, wood ash in this case. “One of my biggest clients, who is located in New Hampshire, markets wood ash generated from several biomass plants in the northeastern U.S.,” says Andrew Carpenter of Northern Tilth in Belfast, Maine. “The properties of the ash vary considerably from plant to plant, and only ash that has a very high carbon content works well for odor control in composting. The high carbon ash is currently used for odor control at four aerated static pile (ASP) biosolids composting facilities in the Northeast. In addition to odor control, the low bulk density (approximately 450 lbs/cubic yard) and the relatively low moisture content improve the physical properties of the compost blend, which otherwise tends toward the moist, high bulk density end of the ideal range for composting. This ash has a surface area of 330 square meters per gram (m2/g), whereas activated carbon is around 500 m2/g.”
High-carbon wood ash has properties similar to activated carbon. It is produced by the incomplete combustion of wood at temperatures above 700°C, and thus contains particles of biochar, which contribute to the odor absorption character of the ash. While the addition of a high pH (about 10.3) wood ash can raise the compost pile pH and shift the ammonia equilibrium towards gaseous ammonia volatilization, this can be managed by reducing the pH of the ash to around 8.6 by exposure to rainfall and CO2 from the atmosphere. Full-scale field research has shown that amending windrows with 12.5 percent and 25 percent high carbon wood ash by volume can reduce odor emissions by more than 73 percent and 88 percent, respectively. (See “Controlling Odors Using High Carbon Wood Ash,” BioCycle, March 2002 for more information.)
A newer physical/chemical odor control approach is using a technology called “nonthermal plasma” (NTP) to remove odorous chemicals. NTP is one of the processes used to make ozone from oxygen, and ozone has been employed for years to oxidize odorous compounds. Nonthermal plasma uses a reactor that consists of two electrodes separated by a void space that is lined with a dielectric material (an electrical insulator that can be polarized by an applied electric field) and is filled with an insulating media. This type of reactor is called Dielectric-Barrier Discharge (DBD). A phenomenon occurs when the voltage through the system exceeds the insulating effect of the media and a large number of electrical discharges occur. In the DBD field in a NTP reactor, the following reactions can occur:
Oxygen is split into ionized oxygen atoms by the electric charge:
O2 —> O+ + O+
Ionized oxygen atoms (radicals) can combine with oxygen to form ozone:
O+ + O2 —> O3
Ozone can react with diethylamine (fishy odor) to form ammonia, water and carbon dioxide:
CH3CH2NHCH2CH3 + 4 O3 —> 4CO2 + NH3 + 4H2O
Ozone can react with ammonia to form ammonium nitrate (a fertilizer component):
2 NH3 + 4 O3 —> NH4NO3 + 4 O2 + H2O
Oxygen radicals can react with carbon monoxide to form carbon dioxide:
O+ + CO —> CO2
This technology is being used at a Transform Compost Systems facility in Ontario, Canada.
Chemical Systems
Chemical approaches to odor control are usually focused on oxidizing reduced-state compounds (like the chemical solutions in the scrubbers discussion above) or on breaking carbon-hydrogen-oxygen bonds to change the structure of a chemical. Others are called “sequestrants” where chemical formulations sequester, or bind, odorous chemicals like amines, ammonia and sulfur compounds. One sequestrant product on the market consists of copper sulfate (an oxidant for the conversion of primary alcohols), benzaldehyde (an almond odor flavoring), and aluminum chlorohydrate (found in deodorants).
Chemical products can be delivered in different ways — applied topically, incorporated into the pile or windrow or applied as a misting spray. The chemical formulations on the market today are proprietary so finding reliable information about how they work is difficult. A lot of controversy exists over whether these formulations work well enough to justify their costs, or whether they work at all.
Few issues in the management of composting facilities will draw more attention, require more time or cost more dollars than managing odor problems. While there are a wide variety of engineered odor control technologies in the marketplace today, most composters would agree that simple is better. A well-designed and operated biofiltration system, coupled with good process design, good process and operational management, and attention to operational details will keep odor problems from becoming off-site public relations disasters.
Craig Coker is a Contributing Editor to Biocycle and a Principal in the firm Coker Composting & Consulting (www.cokercompost.com), near Roanoke VA. He can be reached at cscoker@verizon.net.
Reference
San Joaquin Valley Unified Air Pollution Control District, “Draft Staff Report – Draft New Rule 4566 (Organic Material Composting Operations), June 23, 2011.