Weis Markets, a regional supermarket chain based in Pennsylvania, is bringing a total of 50 stores onto its food scraps composting program in 2013.
Nora Goldstein
BioCycle January 2013, Vol. 54, No. 1, p. 22
Weis Markets, Inc. has an interest in diverting organics from its grocery stores as part of its overall sustainability goals, but to bring an individual store onto the program is always decided by the economics. “It has to balance out,” says Ginny Frederick, Facilities Manager for Weis Markets. “If it costs too much at a particular location, or the store doesn’t generate enough organic waste, it won’t go on the program.”
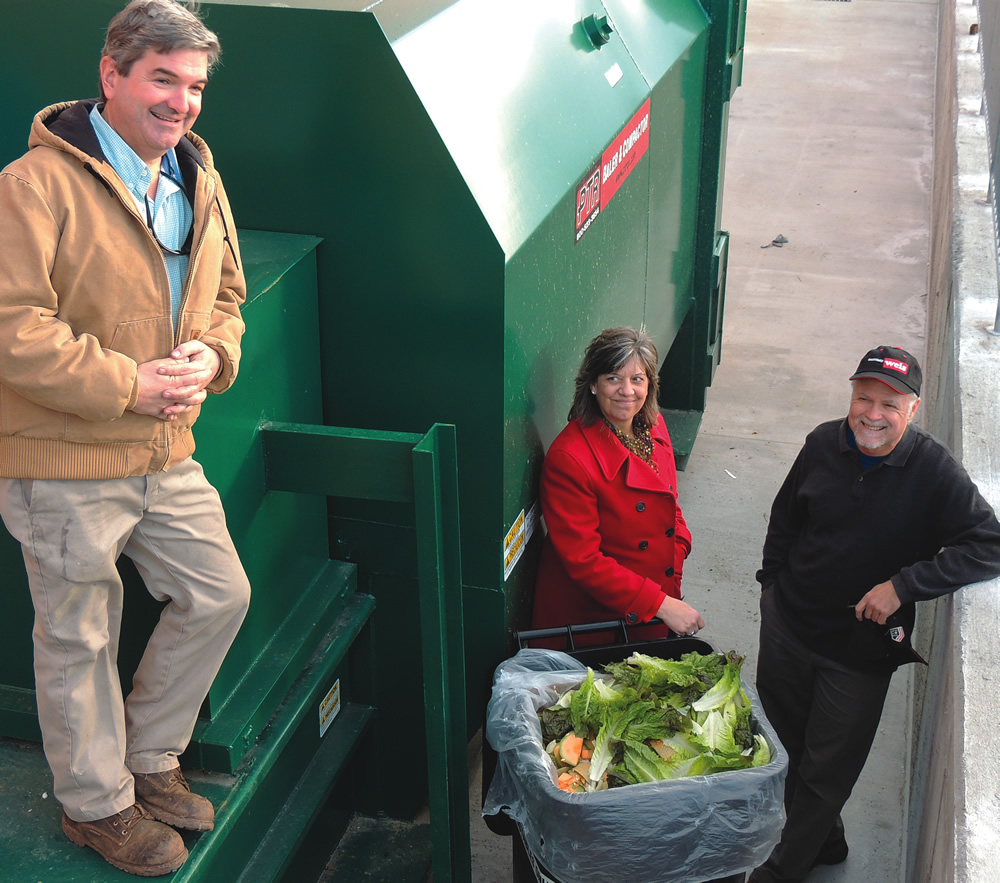
“For stores with compactors we can reduce the size from 40 cubic yards to 20 cubic yards,” says Patti Olenick (center), Sustainability Manager at Weis Markets, Inc. Also pictured are Ned Foley (left), owner of Two Particular Acres and Al Rattie (right) of the US Composting Council.
The company, which is publicly traded, has 163 stores in five states (Pennsylvania, Maryland, New Jersey, West Virginia and New York). In late 2009, Weis initiated a composting pilot using 65-gallon wheeled carts in nine of its stores. “The pilot ran from December 2009 through February 2010,” says Patti Olenick, Weis Market’s Sustainability Manager. “Only produce was being source separated, with the material composted at an on-farm facility. The composting site did not charge a tipping fee for the first 60 days of the pilot. Once the tipping fee was factored into the program costs, the economics were not going to work out. For the stores using dumpsters, it cost more for total trash disposal. For compactor stores, it was less. However there was no reduction in trash collection frequency or the size of the waste containers.” About a half-ton per week per store was being captured for composting.
At the time, Olenick was the organics recycling coordinator for the Pennsylvania Department of Environmental Protection, providing technical assistance to the pilot program. She joined Weis Markets several months after the pilot was concluded. “When I came on board as sustainability manager, one of the projects that Weis wanted to reevaluate was composting,” Olenick recalls. “They wanted me to analyze the data to determine how to make the program work.”
During the pilot, totes filled with produce scraps were stored in coolers until the day of collection. “One of our main interests when we started the pilot was to eliminate some odors from the compactors and outdoor trash receptacles,” recalls Charles Dinsmore, Director of Engineering & Store Service at Weis Markets, who oversaw the pilot. “Storing the totes in the coolers was beneficial for both odor reduction and keeping food waste from freezing in the totes between collections.” For the pilot, only stores with extra cooler space were selected.
Looking back at the experience, Dinsmore adds that the most challenging element he anticipated going into it was proposing a change in accepted operations. “Our fears were quickly dispelled,” he says. “We found that store operations staff were very interested in reducing waste and were happy to see this initiative in the workplace. Associates were commended about how well they separated packaging and other contaminants from the produce. When we started the pilot, we took all the managers from the stores on the program to the composting facility, so they could observe the process. They could see that anything not compostable jumped right out.”
Confidence that store managers and staff were accepting of the change in trash handling was very encouraging. It also was determined that access to cooler storage space was not an issue. “Back room space is precious in stores, but there seemed to be adequate room in the coolers to accommodate the filled totes,” says Dinsmore.
Second Round
Ultimately, Weis Markets decided to test organics separation and collection again. A store audit conducted with the Pennsylvania Recycling Markets Center after the initial pilot found that 50 to 70 percent of its waste stream was packaged and unpackaged food waste. “That was an eye opener for people in the operations department because it was actual Weis waste and data, not an industry-wide metric,” says Olenick. “We gained a lot of valuable data from that waste audit, and plan to do 12 more in 2013.” She adds that recyclables comprise 25 to 40 percent of a Weis store’s waste stream.
For the next composting pilot, Olenick approached Two Particular Acres (TPA) in Royersford, Pennsylvania, which has an on-farm composting permit and collects and processes commercial organics. Working with Ned Foley, owner of TPA, it was decided to bring four Weis Markets on to an organics collection program to reassess the economics. “All four stores were close to Ned’s facility,” says Olenick. “We began in September 2010. We were able to use the 65-gallon totes that had been part of the original pilot.”
Foley collects organics utilizing a recycling truck with a 26,000 pound gross vehicle weight (GVW). Any commercial vehicle with a GVW of 26,000 lbs or less does not require a commercial drivers license (CDL). “Unloaded, the vehicle weighs about 13,000 lbs, and its payload is approximately 12,000 lbs or six tons, for a total GVW of 26,000 lbs,” explains Foley. “Each filled tote averages about 200 lbs, although when meat is in the mix, it can be closer to 600 lbs/tote. There is a lifter on the truck that can handle the weight. We can service about 60 to 65 totes, before we need to go back to Two Particular Acres to unload.”
All food waste must be depackaged. Acceptable items include all produce, bakery waste, deli meats and salads, all floral plants, cut flowers and soil, and coffee grounds and filters. Each department within the stores has its own collection containers that can be stored in a cooler. Each store was given 15 totes. Collection is provided weekly. On average, stores are diverting 1.5 tons/week of food waste. (This quantity is post food donation.)
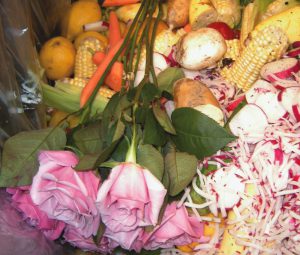
All produce, bakery products, deli meats and salads, floral products and coffee grounds and filters are accepted for composting. Until last fall, meat and seafood also were diverted, but now a renderer services the stores at no charge.
Initially, meat and seafood were included with the other compostables, but last fall, Weis Markets negotiated a new contract with a rendering company that is taking the meat at no cost. (Deli meat still goes to composting, but meat department products are rendered.) “Rendering has always had its own line in a store’s budget because for a long time, it was a revenue generator, not a cost,” explains Olenick. “Then, after the scare with Mad Cow disease, rendering service was less available, and over time, it became a cost to the stores. When the second pilot started, TPA collected the meat, but it continued to show up as its own separate expense. Now, there is no cost, which has helped make the overall economics work.”
Concurrent with the 4-store pilot, Weis was evaluating options and models for expanding the program to additional stores. It considered a reverse logistics model to backhaul food waste from the stores to a distribution center, or placing 4-cubic yard (cy) dedicated organics dumpsters at each store where organics from each department would be consolidated. “We rejected the reverse logistics model because we didn’t like the idea of having large amounts of food waste at the distribution center,” notes Olenick, “and we rejected the 4-cy dumpster option because of potential for vectors and odors, as well as the challenges when food waste is exposed to the elements, such as freezing temperatures.”
Ultimately, it was determined that totes stored in coolers between collections, and then staged outside on the scheduled pickup day, was still the best arrangement. “Stores have a regular pick up day once a week, and associates take the carts outside on that day and set them out so they can be serviced quickly,” she adds, noting that a new security system installed at the stores would have made it difficult for associates to be going in and out to unload the totes into dumpsters anyway. Foley says that initially, he or another driver would go into the stores and pull the carts from the various coolers (or one central cooler), however that was adding too much time per stop.
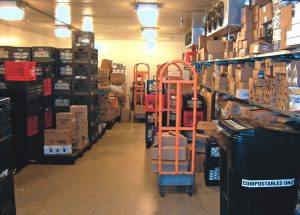
After the two pilots, it was determined that totes stored in a cooler between collections (above), and then staged outside on the scheduled pick up day, was still the best arrangement.
Totes are lined with clear plastic bags, and secured on the lip of the cart with a heavy-duty rubber band. The cart lifter goes up about 4-feet and then tips into the bed of the truck. Associates remove the soiled plastic bag and reline the cart, securing the bag. Carts are cleaned at the stores as necessary. “Because the food waste is stored in the coolers, we aren’t getting a lot of liquid in the totes,” says Foley. “And storing the carts indoors extends their shelf life.”
Over the course of 2011 and 2012, Weis brought several more stores in TPA’s service area onto the program. As of December 2012, a total of eight stores were participating. In addition, the Weis Market in Carlisle, Pennsylvania is working with the student organic farm at Dickinson College to divert the food scraps. “Students at the organic farm come in a pickup truck to get the food waste,” explains Olenick. “We pay them a fee for the service. They needed more organic matter for their farm, so the program is working out very well.” In State College, Pennsylvania, the Weis Market located in the borough of State College is serviced by an organics collection program operated by the town and the Centre County Recycling and Refuse Authority.
Program Economics
A critical goal of the second pilot was to work out the economics of an organics diversion program — both for Weis and Two Particular Acres. “In the early stages of the pilot we charged a tonnage fee on the tipped material and a tonnage fee on the trucking,” recalls Foley. “This yielded a set tonnage fee in the aggregate for trucking and disposal on the total tons collected at the stop. If a store wasn’t fully participating (i.e., it only put out a can or two for a total of several hundred pounds), our costs would increase significantly. We worked with Weis and decided to modify the charge based on a set stop fee and an additional fee per ton for the material collected (a fixed charge and a variable charge).” This fee structure also incentivizes Weis to make sure all the organics in a store’s waste stream are being captured and set out for the weekly collection.
The driver completes a form for each stop, indicating the number of totes set out. The truck is weighed at the composting facility to determine tons collected. That information is sent to Weis Market on a weekly basis. “We have found that we need a minimum of 10 filled totes set out per collection per store to realize the necessary savings,” explains Frederick. “That equates to a minimum of one ton per collection per store. It is also critical that the stores have an adequate number of totes available because otherwise, the organics get thrown away. Some stores, especially during the summer months when there is more produce waste, were requesting twice a week collection. In doing the math, however, it made a lot more sense to give those stores additional totes and stay with once a week collection.”
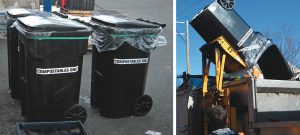
“We have found that we need a minimum of 10 filled totes set out per collection per store to realize the necessary savings,” explains Ginny Frederick, Weis Market’s Facilities Manager. Totes are lined with plastic bags secured with rubber bands (below) to minimize frequency of cleaning.
The weekly reports supplied to Weis also are an indicator of stores’ participation levels in the program. “If a store has been setting out 10 to 15 totes/week and then drops to 2 to 3/week, we follow up right away,” adds Frederick. “It often is an indicator of changes in personnel, and we will conduct another training for the new associates.” Increased contamination in the carts is also reported by the driver, which can be addressed during the next round of training. “The weekly reports are crucial to the success of our composting program, and allow us to monitor each store’s participation,” adds Olenick.
For Foley, finding the route density “sweet spot” — translated into cost per mile to transport food waste — has been his central focus during this pilot project, and the planned program expansion with Weis Markets. “Because we use a small truck, versus the tractor trailers that some dedicated organics haulers are using, our routes are determined more based on store proximity to our composting site,” he explains. “It is more of a milk run approach, where we are keeping our operation fairly small and very local. We can collect, for example, a total of 20 tons in one day, with three unloads, for a cost/mile that makes the economics for this service business work.”
Foley adds that as a commercial composter, he has very little flexibility on his tipping fee for food waste. “In Pennsylvania, I can’t go below the landfill tip fees. We can’t get paid for the carbon we need for composting as that is mostly tied up in the municipal facilities. So we have to make it on the food waste tip fees.”
While the Weis Market program is composting oriented, the company has diverted loads of produce from it distribution center to an on-farm anaerobic digester. “During the summer months, we have a large volume of fruit that the Pennsylvania Department of Agriculture requires us to test before it is distributed,” explains Olenick. “The distribution center is on the collection route of an organics hauler who takes feedstock to a digester in Mifflintown, Pennsylvania, so we arrange for them to pick up our material as needed.”
Expansion To 50 Stores
From Weis’ perspective, this second pilot gave the company the confidence that composting can be competitive with existing trash disposal practices under certain conditions. As a result, Weis Market is adding about 40 stores in Pennsylvania to the organics diversion program in 2013, bringing the total number to 50. “We went through every store and looked at its budget to determine which ones could meet the criteria that composting wouldn’t cost more,” notes Olenick. “Factors evaluated included store size and sales volume. We know that organics are more than 50 percent of the waste stream, so could deduct that from current trash disposal costs. There had to be a reduction in the number of dumpsters and/or the frequency of service for it to work economically. For stores with compactors, we can reduce the size from 40 cy to 20 cy. The cost of composting with the reduced trash service cannot be more expensive than what the store currently is paying for disposal.”
Adds Frederick: “If a store can go from two 8 cy dumpsters to one 8 cy dumpster, we can be comfortable with that. In general, we’ve found the economics easier to pencil out with stores on compactors because they only get serviced once per month, whether they are full or not. With dumpsters, they are serviced several times a week, with a fee charged each time. Where trash hauling costs are higher, reducing dumpster service can be competitive. However, if a store is only paying $200/month for dumpster service, composting is difficult to bring on.”
In general, notes Frederick, waste haulers have been very cooperative in altering their existing trash services. “When we call and say we’ve started a store on a composting program, they work with us on the best price for the remaining trash,” she says. “We sign a contract with the hauler for a set term, but we don’t say that the actual service within that term will stay the same.”
An unintended, but beneficial, consequence of bringing stores onto the composting program is awareness on the part of store managers about the amount of food waste being generated. “Before it was just trash, and could be packaging and other things,” she adds. “When it is narrowed down to just food waste, it becomes more obvious about what waste could possibly be avoided by improved inventory management.” And Olenick emphasizes that there are not extra labor costs involved in source separating the food waste stream. “I wish people would stop asking that question,” she exclaims. “From a labor standpoint, there is minimal difference between throwing items in the trash versus the composting containers.”
The Roll Out
Underpinning the roll out to service the 50 Weis Market stores is the opening of five new composting sites in Pennsylvania. In 2011, Ned Foley and TPA formed a joint venture with The H&K Group to create American Biosoils & Compost, LLC (ABC), a full-service composting and organics recycling company. H&K, a large vertically integrated excavation contractor and construction materials producer based in Skippack, Pennsylvania, operates multiple quarries in the state and several in Maryland and Delaware. As part of the joint venture, H&K made land available at some of its quarries to build the facilities. Five composting sites have been permitted in Pennsylvania (under existing quarry permits). In addtion to the TPA site, ABC expects to be able to service the 50 stores on the Weis Market program. The facilities are located in Easton, Allentown, Douglasville, Hazleton and Lancaster County.
“Our goal is to have a composting site within 20 to 25 miles of each store on the program,” says Foley. “When the collection truck is full, it will go to the nearest composting facility and then continue the collections, perhaps unloading the next time at a different site.” The facilities will receive source separated organics from other haulers as well. ABC has begun engineering work on five additional sites, which the company will start permitting in 2013. “When we are fully built out, we will have the capacity to process about 350,000 tons/year in total,” he adds. “The average capacity of each site is 30,000 to 35,000 tons/year of inbound material. The key is to keep the carbon footprint and the trucking costs low.”
The collaboration between Weis Markets and ABC is ultimately what is making both entitites confident in their investments in the expanded program. “Program permanence comes with positive economics,” says Foley. “One reason we went so long with this pilot with Weis was to get the economics right. We’ve seen grocery chains want to bring all of their stores in a region on line at the same time, which can be a disaster in terms of success of the program. You need to get it right to ensure the economics work for both parties.”
And program permanence, and thus sustainability, comes with those positive economics. Weis Markets’ commitment to composting was a significant factor in ABC investing in composting infrastructure. “The capacity didn’t exist and with Weis’ commitment as one of the anchors to diverting material to our sites, we were able to go ahead and build the sites at the quarries,” he adds.
One of the most satisfying elements of the organics diversion program, concur Olenick, Frederick and Dinsmore, is how receptive store managers have been to the program. “We’ve had no push back from managers,” says Olenick. “Weis Markets has adopted a mission that includes being good stewards of the environment. Organics diversion is a great example of a sustainability program where everyone can get involved and make a difference. And if the stores can show a reduction in their operating costs, that positively affects their bottom line, which is good for the managers and good for the stores.”