A variety of turbines and IC engines are designed to operate on biogas. Both types of cogeneration equipment have unique characteristics including their electrical and thermal efficiency.
Kim Murdock-Timmerman
BioCycle September 2013, Vol. 54, No. 9, p. 59
Biogas-to-energy projects are becoming more commonplace. Using the naturally occurring methane from biogas to produce heat and electricity can both lower utility costs at a plant and potentially improve the air emissions. Traditional combined heat and power (CHP), also known as cogeneration, is an efficient approach to generating electricity and thermal energy from biogas at the point of use. The thermal output of a CHP system also can be converted to air conditioning or refrigeration with the addition of a thermally activated cooling system. There are many different turbines and internal combustion (IC) engines designed to operate on biogas. Both types of cogeneration equipment have unique characteristics including their electrical and thermal efficiency. Specifications include electrical output, parasitic load, maintenance costs, exhaust characteristics and heat recovery (thermal output) options.
Initial equipment costs, along with operating and installation costs per kW, should be reviewed before making a buying decision. Overall conditioning of the biogas almost always includes moisture removal and compression. Impurities in the biogas, including hydrogen sulfide (H2S), siloxanes and volatile organic compounds, are also an important consideration in a project. Treatment of the biogas to remove these impurities to appropriate levels will have an effect on the overall operating cost of a system. In general, the conditioning is based on the chemistry and flow rate of the gas and the type of engine or turbine. All cogeneration equipment types have specific inlet fuel parameters. Additional factors to consider in a buying decision are space availability, integration into existing thermal and electric systems, along with grid interconnection requirements and state regulations. Many sites have multiple engines or turbines so that one unit can be shut down for maintenance without losing the entire capacity of the installation.
The appropriate sizing for a cogeneration system can be either electric or thermal limited, depending on the size of the facility and the equipment on site. Defining the current electric and thermal energy usage is the first step in determining which type of cogeneration equipment would be best suited for a facility. Then the site’s potential future requirements for both electricity and thermal energy can be reviewed. Electricity cost (demand and energy) and the amount the local utility will pay per kWh for renewable energy are factors to consider whether producing excess electricity is a viable alternative. While there are some variances in the biogas-to-electricity efficiency of different systems, almost all of the technologies are in the 30 to 40 percent electrical efficiency range.
As a general observation, most anaerobic digester biogas projects are utilizing CHP engines as these operations typically have electrical and thermal energy requirements. Landfills, on the other hand, use turbines and IC engines for electricity production only as they typically have no use for the thermal energy. All units sold today either have the option for integrated heat recovery or can easily be matched up with an external heat recovery unit.
Volume Of Biogas
The volume of biogas produced is one of the variables that helps in determining which cogeneration product best meets the needs of a facility. For many sites, the biogas production varies during a typical week. In those cases, the turndown capacity of the cogeneration equipment (i.e., its ability to handle variations in biogas volume) becomes a factor. Most cogeneration equipment has a 50 percent turndown capacity. This requires biogas conditioning systems to be designed for the higher biogas volume, while still having the ability to effectively operate at lower biogas production levels. For example, if a site is designed for 180 scfm and has two engines that use 90 scfm each, one engine can be serviced while the second one produces electricity at its 50 percent turndown. If this same site (designed for 180 scfm), began operation at 90 scfm and one engine, an additional engine of the same size could be added in the future when the biogas production increased.
Wastewater treatment plants (WWTP) with anaerobic digesters are sized by the “million gallons/day” (MGD) capacity for waste, and the respective amount of biogas that it produces. Many facilities use codigestion of high strength waste (HSW) such as food processing residuals and the base sludge to increase biogas production in digesters with excess capacity. In this process, the energy-rich organic waste will maximize production of biogas per unit of mass. The anaerobic digestion of these biodegradable substrates provides approximately three to four times more biogas production per volume of digester capacity than municipal wastewater alone.
The following is a generic example of the payback for a small digester using a 65 kW turbine installed at a WWTP with and without high strength food processing waste:
Option 1 –Municipal sludge only: The site takes in 1.0 MGD of waste and produces 38,000 ft3/day of biogas with the cost of electricity at $0.075/kWh and the value for heat at $0.80/therm. The total estimated cost for the biogas conditioning system, turbine, site engineering and installation would be approximately $500,000. Based on the value of both power and heat produced by the system, the payback would be 10 years.
Option 2 –Municipal sludge plus high strength food processing waste: The biogas produced would increase to 76,000 ft3/day. The new, total estimated cost, including an additional 65 kW turbine and other small incremental costs would increase to approximately $655,000. But the payback would decrease to 6 years due to the increased power and heat produced.
WWTP Case Studies
Sheboygan, Wisconsin: There are many wastewater treatment plants around the country successfully converting biogas to energy. At the Sheboygan Regional WWTF, the upgrade of its wastewater treatment plant to a Net Zero Energy facility was a five-year process. This facility is located on the western shore of Lake Michigan and serves seven communities in the area. The average design flow of the plant is 18.4 MGD and the digesters on site can produce approximately 750,000 ft3/day of biogas.
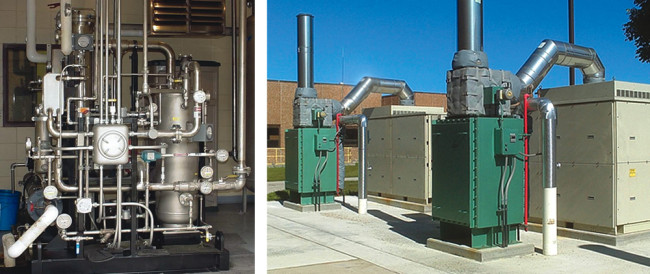
Sheboygan, Wisconsin’s cogeneration equipment includes ten 30 kW and two 200 kW microturbines (several shown above), four heat recovery systems and a biogas treatment and compression system (left).
Janesville, Wisconsin: The City of Janesville WWTF is another example of a plant that makes the most from its biogas. This site is located in southeast Wisconsin and has an average flow of 12.5 MGD. The facility produces approximately 100,000 ft3/day of biogas and uses the conditioned gas to power turbines for electricity and to produce vehicle fuel (Bio CNG technology) for its maintenance vehicles.
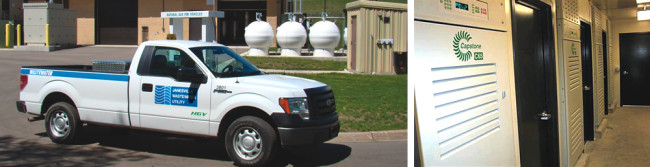
The City of Janesville, Wisconsin utilizes microturbines (right) for electricity, as well as BioCNG equipment to upgrade biogas for vehicle fuel (fueling station above).
Danville, Illinois: The Danville Sanitary District is in the first year of operation of its cogeneration project. This site is located in eastern Illinois and has an average flow of 5 to 8 MGD. The digesters produce 58,000 ft3/day of biogas. Danville utilizes a reciprocating engine to produce up to 150 kW of electricity and 778,000 BTU/hour of thermal energy. The thermal energy is used to supplement boilers that heat both the buildings and anaerobic digesters at the plant. The electricity goes directly into the plant’s control center. The system is expected to save the district $225/day in electricity and $80/day in natural gas expenses.
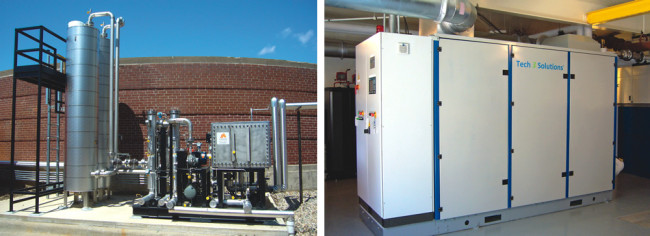
Danville, Illinois is in the first year of operation of its cogeneration project that includes an IC engine (right) and a gas conditioning skid (left).
The case studies included in this article are installations of turbines and IC engines installed at wastewater treatment plants, however the general discussion applies to any type of cogeneration with biogas as the fuel source. Project economics including payback for CHP systems are site specific. To be cost-effective, the savings in power and fuel costs need to be compared to the capital, operating and maintenance costs of a CHP system. Factors influencing the payback period include the types of waste being treated and the chemistry of the biogas (there is no “typical quality biogas”). It also depends on the type of cogeneration equipment as these systems all have different requirements for inlet fuel. As other fuel sources become more expensive, it makes good sense to evaluate the possibility of turning waste into energy.
Kim Murdock-Timmerman is the Biogas and Media Specialist for Unison Solutions, Inc. She thanks Sharon Theiszen, Sheboygan Regional WWTF, Joe Zakovec, City of Janesville WWTF and Thomas Stone, P.E., Danville Sanitary District for their contributions to this article.