BioCycle September 2013, Vol. 54, No. 9, p. 12
Richmond, Virginia: Compost Builds Soil At Redskin’s Training Camp
Torrential rains that inundated the Washington Redskins’ new training camp in Richmond in August led to some positive publicity for North Carolina-based McGill Compost and its turf-building premium compost product. Talk show hosts on a local sports radio station expressed their amazement
at how well the facility’s two practice fields held up under the heavy rain, while surrounding areas of the park — where no compost had been applied — were a soggy mess. Earlier this year, Earthworks and Sprinklers, Inc., a Richmond-based sports field builder, tilled McGill SoilBuilder Premium Compost into the existing soils at the Redskins’ new training camp fields in downtown Richmond. “We’ve been spreading the word that adding compost to fields is a more effective choice than bringing in large quantities of topsoil, which may have relatively low organic content,” says Gary Gittere, sales and marketing manager for McGill Premium Compost. “They can blend two inches of compost into four to six inches of soil and create a really good medium for sodding — like was done on the Redskins’ fields.”McGill has two composting facilities in North Carolina and one in Virginia. It processes over 300,000 tons/year of municipal and industrial organic wastes and pre and postconsumer food waste annually in the U.S., according to Gittere. McGill plans to capitalize on the positive exposure it’s gained from the Redskins case study. “We’re in the process of building a relationship with the landscaping firm that manages the Redskins practice fields, planning to expand its use of McGill’s compost on other athletic fields they manage,” Gittere adds. A feature article on compost use on athletic fields and golf courses will be in the October issue of BioCycle.
Howard County, Maryland: SSO Composting Underway
The Howard County Bureau of Environmental Services opened a pilot-scale composting facility in March 2013 to process residential food waste from its pilot curbside collection program. The $800,000 facility, located on a three-quarter acre site at the county’s Alpha Ridge Landfill, is sized to process 8,000 tons/year of source separated organics (SSO). It is using the AC Composter covered aerated static pile system supplied by Engineered Compost Systems. The county’s first collection pilot was conducted from September 2010 to January 2011, and included 34 volunteer households (of 200 targeted). Approximately 23 percent of the residential trash in the pilot area (Elkridge and Ellicott City, Maryland) was comprised of food scraps. A key purpose of the pilot was to test different size curbside collection containers (for food waste only). No meat, fish, bones or dairy were accepted.
Based on data and feedback from the initial pilot, Howard County expanded the service to a pilot area of 5,000 houses; 35-gallon green carts were provided (food soiled paper and small quantities of leaves and grass can be included). The county estimates that 5 tons/week of food scraps will be diverted. It plans to expand curbside collection service to 10,000 homes in Elkridge and Columbia later in 2013. The net cost of processing the food scraps and yard trimmings at the Alpha Ridge facility (cost of collections, transport and processing, minus revenues from sale of finished compost) is estimated at $16/ton. The county was paying $35.33/ton to a contractor to haul food scraps to a composting facility in Delaware, prior to opening its own site. That fee was expected to rise to $65/ton.
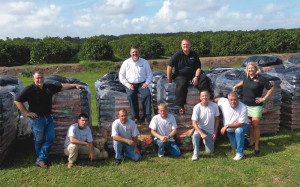
Garick LLC and Faith Farm Ministries collaboration provides job training for recovery program residents
Okeechobee, Florida: Compost Packaging And Job Training
A collaboration between Garick LLC, owned by Waste Management, and Faith Farm Ministries has resulted in a new packaging plant that teaches job skills to Faith Farms’ residents while bagging compost for retail sale. Garick LLC operates two Waste Management composting facilities in central Florida — one in Okeechobee and the other in Apopka — that process yard trimmings and source separated organics, including food waste. Faith Farm Ministries is a faith-based, long-term residential recovery program for people with addiction, and has a long history of creating enterprises that provide clients with “resume-worthy” job skills. Together, Garick and Faith Farm have invested in and built a compost packaging facility on the ministry’s Okeechobee campus. Compost comes from the Okeechobee and Apopka facilities and is bagged under the Organic Valley™ Brand. A potting mix is made as well. Bagged products are sold in all Faith Farm stores, as well as other retail outlets. “We are excited to be part of the organics recycling story here,” says Allen Patterson of Faith Farm in Okeechobee. Adds Ray Stamper, general manager of Garick’s Florida operations: “This is an excellent opportunity to mutually grow our businesses, further our commitment to green initiatives and support this mission.” Both the Okeechobee and Apopka composting operations utilize covered bay aerated systems supplied by Engineered Compost Systems.
Edmonton, Alberta, Canada: Tracking Data At Large-Scale Composting Facility
The City of Edmonton’s composting facility processes 200,000 tons/year of mixed residential waste with 100,000 tons/year of biosolids, making it one of the largest cocomposting facilities in North America. The facility produces about 80,000 tons/year of compost. Incoming feedstocks are loaded into rotary drums that kick off the composting process, followed by aerated bay composting indoors. Curing is done in a large area outside, which is roughly three-quarters of a mile from the Research & Development (R&D) building where the facility manager’s office is located. During the winter month’s, with temperatures way below the zero degree mark, operators would have to go outdoors to retrieve process data from 8 wireless EcoProbes supplied by Reotemp. The EcoProbes have a 1,000-foot line of sight. To relieve operators of having to retrieve data outside during the winter, Reotemp mounted an antenna on top of a maintenance shed that is part way between the R&D building and the curing piles. A second antenna was mounted on the roof of the R&D building. Compost Watch, a Windows-based software designed for use with the temperature probes, was loaded on the operator’s computer and connected to the antenna. The operator is able to see real-time temperatures from the curing piles, historical data and graphs, battery status and high/low temperature alarms and warnings.
Goshen, Indiana: Low-Cost, Low-Tech Campus Composting
In 2010, Goshen College, located in the town of Goshen, decided to stop sending the food waste generated in its dining hall to the landfill. It began with a trial run, which was deemed a success, and has since evolved into a permanent program. An insulated wooden box was constructed behind the dining hall’s dumpsters. Wood chips are received from local tree trimmers, and mixed with the food waste in a 2:1 ratio to provide airflow. On-site composting lasts for at least three weeks, heating to more than 140°F. Once full, the composter is transported to an on-campus location and replaced by an empty box. Materials are further composted for up to three more months, then screened using a pivot screener designed and constructed by Natasha Weisenbeck, now a senior at Goshen. “It hangs on a 20-degree angle and hits bumpers, allowing the compost to fall through the screen,” she explains.
Screened compost is used in a small garden managed by the dining service contractor, AVIFresh, with vegetables and herbs served in the cafeteria. On a typical weekday, the campus of 200 students generates 75 to 100 lbs of plate scrapings and kitchen scraps. Student volunteers, organized by the college’s environmental club, help run the program. Between reduced waste collection fees and garbage bag savings in the kitchen, the college saves an estimated $1,800/semester. “What I like about this approach to composting is its simplicity and community engagement,” says Glenn Gilbert, Goshen College’s sustainability coordinator about the decision to use a low-tech system. “The college has chosen to rely on student involvement, creating a simple system that is easily replicable almost anywhere.”
Chicago, Illinois: Truly Local Farming, Composting
FarmedHere, started in 2011, is a vertical urban farming company in Chicago that uses indoor aquaponic and aeroponic growing systems that yield USDA certified organic produce and local jobs in a sustainable farming environment. Stacked grow beds (up to six high) are used to create vertical growing space. Instead of soil, water from tanks of hormone-free tilapia delivers nutrients to the plants through either an aquaponic or aeroponic system. These systems are combined with controlled water pressure, humidity and atmospheric pressure to create optimal growing conditions. All produce is packaged and delivered locally in the Chicagoland region. More recently, FarmedHere partnered with The Resource Center, a nonprofit environmental education organization, to establish a program to convert all of FarmedHere’s organic waste into compost. The compost is then used to feed other urban farms across Chicago. “We have been searching for an optimal solution to our organic waste since the inception of our new farm in 2012,” says Jolanta Hardej, the CEO and cofounder of FarmedHere. “The Resource Center is a perfect fit. They provide a superior service, pick up our waste and turn it into compost, which feeds other farms in the city. It is a ‘closed loop’ arrangement, just like the reuse of water in FarmedHere aquaponic grow systems.”