More trailer and lift manufacturers are designing equipment specifically for collection and transport of source separated food waste. Part I
Nora Goldstein
BioCycle August 2014
Wet and heavy. Those two adjectives pretty much sum up the reality of collecting and transporting source separated food waste — especially from the commercial and institutional sectors that set out primarily food scraps with minimal amounts of green waste and paper. Wet and heavy translates into leak-proof seals on trailers and lift attachments strong enough to heft a ton or more of food waste at one time.
Some manufacturers of food waste trucks have a long history of servicing the animal rendering industry, thus have experience designing trailers for wetter and heavier feedstocks. Because of the quantity of produce in the food waste stream, however, some customization has been necessary to make bodies liquid tight and design lifting arms that are more efficient, durable and can bear more weight.
Most recently, a truck manufacturer began selling a unit specifically designed for food waste collection. New Way, a division of Scranton Manufacturing, introduced the Rotopac, a fully automated side-loader organics collection truck. It is a mobile compactor with a leak-proof truck body that uses an auger instead of a ram to move material from the 4 cubic yard (cy) receiving hopper into the truck body. “Conventional side load garbage trucks usually have 6 cy hoppers to retain whatever is being picked up while the ram continuously packs until the hopper is cleared,” explains Phil Allen, vice-president of sales at New Way. “The Rotopac only needs a 4 cy hopper because the auger’s throughput is 7 cy/minute, which is about 20 percent faster than a ram.”
While it can be used for collection of commercial organics, New Way discovered the Rotopac is ideal for communities adding source separated organics (SSO) collection to an existing trash collection service. “The initial concept was for organics collection only, but we found out in R&D tests last year that it works just as easily for trash collection,” adds Allen. “The idea is that communities with SSO collection don’t have to buy a second truck. Instead, they can collect organics with the Rotopac on certain days of the week, and trash on the others.”
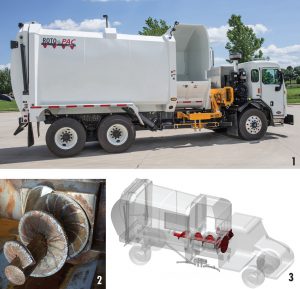
New Way’s new Rotopac (1) is a fully automated side-loading organics collection truck that can be double-purposed for curbside trash collection. It features a 4 cy hopper equipped with an auger (2) that feeds material into the truck body (3) at a rate of 7 cy/minute. Images courtesy of New Way
The 27-cy body can carry a legal payload of 25,000 lbs. The automated arm can lift up to 500 lbs at its maximum reach of 12 feet, thus it can be used to service commercial and institutional accounts on a cart system. “Customers also like having the auger that is self-cleaning, especially as it eliminates the need to clean out behind the ram that most packer trucks use,” adds Allen. “Basically, operators can just open up the tailgate and hose the body down at the end of the day.”
Tackling The Weight
Organix Recycling, LLC, based just outside of Chicago, collects food waste in 29 states and Puerto Rico. The majority of its customers are retailers in the supermarket sector. “Over 95 percent of what we collect is preconsumer food waste, although we do service a few restaurants and manufacturers,” says Rick Shipley, chief operating officer. “Much of what we collect is used to produce animal feed.”
Shipley finds that the best comfort zone for his company and the retailers serviced is use of a 3 cy container for food waste collection. “We think that is the perfect spot. We tried other sizes but the weight of the material we are dealing with got too heavy with larger containers. With the 3 cy, we can put in more than one container at a location, which adds enough capacity that the store can extend out service to get to a good price point to divert their food waste.”
To service the containers, Organix Recycling has found that modified rendering trucks equipped with lifting arms that can bear the weight work best for its purposes. And this is where having a solid working relationship with its trailer manufacturers has been key to its collection and transport success. Organix Recycling has several Travis Trailers and a couple of Mac Trailers, but primarily works with Brown Industrial. “This goes back to the product we are dealing with and its liquid nature,” notes Shipley. “When we started, no one knew what we were getting into. As it turns out, it is very important to put extra strength into the arms and forks — the elements that go into the lifting — because of the weight and liquid shifting in the container.”
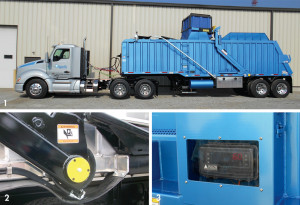
Organix Recycling, LLC, which operates in 29 states, primarily uses trailers (1) supplied by Brown Industrial to service 3 cy food waste containers. A new feature on Brown’s aluminum trailers is a bolt-on arm (2) that is more suited to lifting heavy containers. Customers are also requesting installation of Vulcan scales (3). Photos courtesy of Brown Industrial
Brown Industrial is a third-generation company that has been working in the rendering industry since the 1940s. To service haulers collecting food waste, it customized its rendering trailers for that purpose. Overtime, based on feedback from customers, Brown Industrial has made modifications. “We have done a lot of refining, mostly small changes that our customers pick up on,” notes Craig Brown, co-owner of Brown Industrial. “For example, we found that the arms attached to the shaft could lift the food waste containers, but we were seeing weld failures where the arms attach to the cross shaft on trailers that were only three to four years old that we would normally not see for at least 10 years on our rendering trailers. That resulted from lifting more weight with food waste collection than rendering applications.”
Three years ago, the company started building aluminum units and designed a bolt-on arm for that application, and found that they were stronger than the welded on version. “On our older units, the arms were welded to the cross shaft,” explains Brown “We recently replaced those with removable arms that are bolted on, with a taper lock hub that ties the lifting arm together. We also went to a replaceable bronze bushing on the cross shaft. With the new bolt-on arms, we feel confident we can now work on increasing our lifting capacity. By going to a slightly larger cylinder we can increase capacity about 20 percent. Previously, it could lift 5,000 to 5,500 lbs depending on arm length; now it can go up to 6,000 or 6,500 lbs if necessary.”
The company offers straight trucks, trailers and roll-off units. “Haulers who are just testing the food waste collection market will go with a roll-off chassis, which is a lot more economical than investing in a new truck,” he adds. “We make a roll-off body that has arms on it so they can collect food waste, and use it as a box for other materials at other times.”
Brown Industrial offers both stainless steel and aluminum bodies and trailers for food waste collection. “Because all our trailers are custom-made, we end up blending both metals sometimes, for example using 409 stainless steel for arm attachments, which keeps the units looking better longer,” says Brown. He also says more food waste collection companies are requesting installation of its Vulcan scale weighing system, which it integrates into the unit. “The main reason is to check the weight on the containers,” he notes. “The scale is accurate within 10 to 15 pounds.”
Access And Simplicity
Another innovation in food waste collection is equipment that can turn pickup trucks into collection vehicles. In some cases, this is done by modifying a trailer, pulled by the pickup truck) with a cart lifter and beefing up seals on the trailer bed and gate. In the case of Perkins Manufacturing, it is building upon its Satellite Lifter Systems (SAT) that are mounted to the rear bed of a standard 8-foot pickup truck. Being able to use a pickup truck for collection expands the ability to service collection stops with limited access (or service a resort or university with a food scraps diversion program). The SAT is available in capacities ranging from 3- to 8-cy, regular or split-body configurations and a choice of a grabber lifter or a US hook lifter (as well as a recently introduced slider lifter). The grabber lifter can pick up a large variety of containers whereas the hook lifter can only pick up ANSI Type B carts.
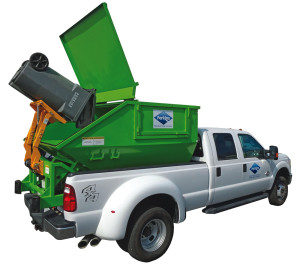
Perkins Manufacturing introduced a hydraulic sealed hard top lid (top of photo) for its Satellite Lifter Systems that provides a tight seal for food waste collection. Photo courtesy of Perkins Manufacturing
This past spring at Waste Expo, Perkins introduced a hard top for the SAT systems. “We usually offer a mesh or vinyl tarp for the SAT units but this year we created a hydraulic sealed hard top, which is great for food waste collection,” explains Cheryl Perkins Waite, president of Perkins Manufacturing. “It is more durable, easy to use with the push of a button, keeps what is in the container more secure and lasts longer than a tarp.”
The food waste SAT unit can carry up to 4,000 lbs, whereas the regular unit was designed for 2,000 lbs, adds Waite. “And after a long period of research and testing, we have found that the vinyl seal remains the best material to prevent leakage. At Perkins, we use a rubber bulb seal with a duometer A73 all along the door edges and top.”
The SAT units can be used in conjunction with a rear load packer truck to transfer material as needed when servicing a food waste collection route. The unit backs up to the rear loader; solids can be transferred without spillage, although liquids are harder to control. “We are working on how to improve and eliminate any spillage,” she notes. “We do have other products that work well with food waste that can get the job done with minimal spillage.”
In addition to access, simplicity is an important feature for food waste collection. This is why some haulers opt only for totes of a specific size. “Almost 100 percent of our collection containers are 64-gallon totes,” says Roy Ferreira of New England Solid Waste Consultants (NESWC). “The way the trucks we use are designed, that is the best option.” NESWC uses Martel truck bodies; it has three 40-cy and one 30 cy unit. The trucks are equipped with a lift that fits three 64-totes at one time.
Each truck typically travels 230 to 250 miles/day on a collection route. The company’s service area includes Massachusetts, New Hampshire and southern Maine. “We service the trucks on a rotation,” explains Ferreira. “Every other week, they are brought in and greased, and every six weeks the oil is changed. We currently rotate tires every six months, and replace all tires once a year.”
Servicing Food Processors
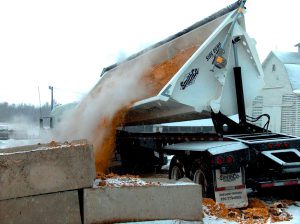
The SmithCo Side Dump trailers have a fully welded tub with no gates, making the unit water-tight. Its side-dumping feature enables the truck to build a composting windrow as it unloads. Photo courtesy of SmithCo
For food waste collection companies servicing food processors, one style of truck available is a side dump trailer. SmithCo Side Dump trailers have a fully welded tub that dumps the material to the side, and because they have no gates, are water tight, explains Rick Lawrence, SmithCo’s national sales manager. “While it’s a smaller niche for us, we have sold our trailers to transport food processing residuals such as peelings and culls. A few years ago, a hauler bought our units to collect food waste from casinos in Las Vegas.”
Lawrence adds that these units can be loaded and unloaded without the driver having to get out of the cab, improving efficiency of collection as well as driver safety. He notes there are also efficiencies if the collection companies are delivering food waste and other organics to composting facilities: “The driver can literally unload directly into a windrow, gradually moving forward as the trailer empties. They are pretty much making the windrow.” The SmithCo trailers can be equipped with lifts or forks, or else park under a conveyor belt that moves material directly into the trailer.