Dan Emerson
BioCycle October 2015
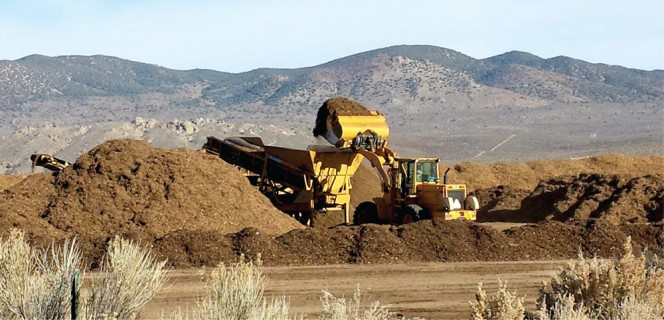
Compost is screened and incorporated into a number of specialty blends. Custom blend recipes are based on analyses of soils in northern California and Nevada.
Photo courtesy of Full Circle Soils and Compost
Ten years ago, entrepreneur Craig Witt pioneered the concept of commercial composting in the state of Nevada, when he launched Full Circle Soils and Compost in Minden. Today, the family-owned business has a well developed product line, complemented by custom blends, and a growing customer base in Nevada and California.
Twenty years ago, the Witt family was operating a 100-year old dairy farm in northern Nevada. Seeking methods to grow more and better alfalfa in the region’s mix of sandy and dense clay soil, Witt spent time in the U.S. and Germany observing and learning about various types of composting processes. Eventually, he began composting manure from the dairy herd, and subsequently expanding to include woody biomass, green waste, tree trimmings, wood construction debris and food waste.
The Witts sold the dairy farm in 2006. Since then, Full Circle has operated a 30-acre composting facility on property belonging to the Northern Nevada Correctional Center. About 25,000 cubic yards of material are composted annually, according to Cody Witt (Craig’s son), who is Full Circle’s director of strategic development. Feedstocks include pre and postconsumer food waste from “all over Nevada, including waste from WalMart and Costco stores,” he notes.
Full Circle is also the organic materials recycler for two refuse contractors, South Tahoe Refuse and Douglas County Disposal. It receives and processes tree trimmings and green waste material from Northern Nevada and the Lake Tahoe area), and LEED-certified drywall waste from building construction. Full Circle helped start the first green waste collection route in Minden. It also receives manure from 1,500 wild Mustangs in the Nevada Department of Agriculture’s Saddle Horse and Burro Training Program.
Manure comprises less than 20 percent of the content of Full Circle’s finished compost, Cody Witt says.
He estimates Full Circle processes somewhere between 1,000 and 2,000 cubic yards of food waste annually. Reducing the amount of food waste in favor of pristine wood and green waste from the Lake Tahoe Basin has helped the quality and uniformity of Full Circle’s finished compost product, Witt explains. Food waste compost is held separately for specific products and handled separately primarily because of high rates of contamination.
Composting Method
In developing Full Circle’s method, Craig Witt combined the teachings of soil scientists, along with composting techniques from Midwest Biosystems, to create a very aerobic turned windrow process designed to produce compost in 12 weeks. To ensure a high quality product, the Witts maintain windrow temperatures of 135°F to 165°F, averaging 140°F for 5 weeks.
Composting is done on a compacted soil base. Piles are turned on average 24 times per cycle, “depending on moisture, CO2 levels, and how hot they get,” he adds. Windrows are about 400 cubic yards each, with an average 15 piles in-process at a given time. Full Circle composts 12 months a year, with the “same exact process” being used, regardless of the season. Most production is done from November to May, sometimes in below-zero temperatures.
Equipment used in the composting operation includes Midwest Biosystems Aeromaster turners with custom water and compost tea application wagons, John Deere loaders, a Morbark 950 Grinder, and CEC 5 x 12 Double Deck Screen. Full Circle also has a vermicomposting operation, housed in 2,000-square feet of greenhouse space. The Witts also maintain an in-house, plant propagation setup, for product testing and quality control. Full Circle has seven employees. It also uses some prison labor, and helps inmates learn about composting practices.
Soil Amendments
Full Circle has developed a line of five staple products: Boost soil amendment, Punch vermicompost extract, Soar potting mix, Kick garden soil, and Protect fertile mulch. Developing and selling custom blends is also a major part of Full Circle’s business. “We pride ourselves on making 100 percent specialty blends, based on specific soil analysis, for any growing scenario — from backyard gardens to huge ag institutions,” Witt explains. For custom blends, trace minerals such as manganese, magnesium, boron, zinc and copper, locally sourced from the region, are added. Custom blend recipes are based on soil analyses conducted in northern California and Nevada.
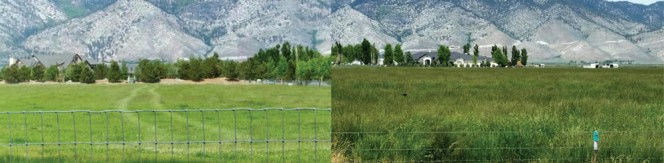
A crop trial was recently completed on an 18-acre grass pasture using Full Circle’s “specialty mineral” compost applied at less than a quarter-inch in depth. The pasture with no compost is on left; the pasture with compost is shown on right.
Photos courtesy of Full Circle Soils and Compost
The Witts recently completed a crop trial on an 18-acre grass pasture, with its “specialty mineral” compost applied at less than a quarter-inch depth. Farmer Gary Casteel’s first seasonal cutting in March showed a doubling of yield from 3 to 6 tons per acre, Witt notes. He hopes the result of that and other farm trials will help Full Circle gain more “market traction” to sell more compost to farmers. “We want to show them their (compost) return on investment will be maximized in the shortest period of time, because we can fix the soil that much,” he says.
In growing heirloom tomatoes in Nevada, Full Circle has been able to routinely produce up to 100 pounds per plant, using its soil mixes. Amateur gardeners using Full Circle products have reported average production of about 50 pounds per plant, Witt notes. A gas station that is one of Full Circle’s product distributors has produced a 75-pound average.
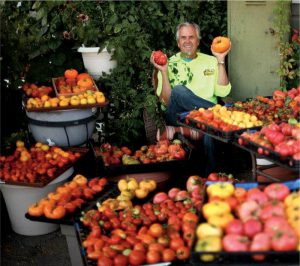
Craig Witt pioneered private composting in the state of Nevada (shown with heirloom tomatoes grown using Full Circle’s compost).
Photo courtesy of Full Circle Soils and Compost
Craig Witt also does consulting work for some large agricultural producers. One is the Alta Group in Mexico, which grows produce for Whole Foods. He’s also consulted on erosion control and revegetation projects for agencies including the California Department of Transportaion and the Tahoe Regional Planning Agency.
Being a composting entrepreneur in Nevada, “not the greenest state on the planet, ” has been interesting, says Cody Witt. “The state has a 20 percent recommended organics diversion rate, but there is no (statewide) recycling mandate.” As a result, educating consumers and government officials “is our main battle,” he adds. “We’re trying to teach people that you don’t just put horse manure in garden soils; they need a specific process and recipe.”
To expedite the education process, Full Circle is rolling out a new branding campaign that will be “simpler for people to understand.” The Witts have also changed their retailing model, closing the retail operation they ran for 25 years, and developing a network of 12 distributors across Northern Nevada and eastern California.
Prior to the 2008-2009 recession, Full Circle had reached the $1 million in annual revenues. Today, revenues are between $500,000 and $600,000 annually, Witt says. Full Circle’s biggest challenge might be the labor-intensive nature of feedstock sorting, he adds. “Last year, we handled 14,000 garbage bags of pine needles; we had to open each bag and sort through them by hand. And materials contamination continues to be a large issue.”
Full Circle invests a great deal of time educating landscapers, waste managers and others who supply material on how they can uphold the company’s feedstock standards. “Keep it clean at the source,” Witt notes. “And we ‘touch’ our product two to three times more than most companies in the process of turning waste into quality products. Our focus is on the health of the soil so our customers can grow the healthiest, happiest plants on Earth.”
Dan Emerson is a Contributing Editor to BioCycle.