Systems designed to separate packaging from its contents — in this case food and liquids — are being installed at facilities in the U.S. and Canada.
Dan Sullivan
BioCycle June 2012, Vol. 53, No. 6, p. 42
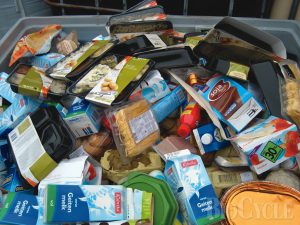
Depackaging equipment for recovering organics is designed to deal with a variety of materials from plastic wrapping and containers, to wax-coated cardboard and even metal cans and glass bottles.
Across Europe, where directives to phase out landfilling of unprocessed organics are in place, the use of depackaging equipment to capture the organics — and sometimes the packaging material around it — for composting or energy production has become standard practice. In the U.S. and Canada, utilization of depackaging and preprocessing equipment for handling packaged food waste is also gaining traction. The practice is bolstered by a growing number of large retailers’ ambitious zero waste policies in tandem with growth in anaerobic digestion (AD) projects to process the material. Each depackaging system works a bit differently, and most can be tailored to clients’ needs.
“We’ve been at this only about six to eight months in the U.S., and we’re still learning the market,” says Pete Lyle of The Dupps Company, a 75-year-old Ohio-based manufacturer of rendering equipment that operates in partnership with Netherlands-based Mavitec to make and market rendering and depackaging equipment across the globe. Mavitec has developed and installed more than a dozen systems related to biogas projects outside the U.S., according to Lyle. The first depackaging system went online in the U.S. just a few months ago at a project run by quasar energy group in Zanesville, Ohio. “There is a lot of interest in depackaging, mostly from third-party waste haulers contracted to take organic materials from large retailers,” he adds. “This is because companies like Kroger and Walmart have established zero waste goals and want a quick solution. We also receive inquiries from food production companies that generate anywhere from 5 to 20 tons/day of packaged food waste that is either mislabeled or else something is wrong with the food product or packaging itself and it needs to be disposed.”
In Europe where the market has evolved for more than a decade, these recovered organics have become a marketable commodity, notes Mavitec Green Energy Sales Manager Bob Schoenmaker. “Everyone is fighting over the organic material, and they are willing to pay for it.” The amount digester operators are willing to pay depends on the dry solids content. “If it has a high dry solids content, they will pay more than if it has a lot of moisture,” he explains. “Fruit and vegetables are typically about 90 percent moisture. They prefer the tacky, sticky product — bakery waste, potatoes, meat and fish. Most of the time, higher dry solids means a higher gas yield.” The average supermarket mixture will produce between 350 and 500 cubic meters of gas per metric ton of recovered feedstock depending on the load, he says, compared to a metric ton of fruit waste, which yields about 150 cubic meters of biogas.
Depackaging equipment has evolved to handle all types of materials, from coated cardboard and plastic to metal cans and even glass bottles. “Glass and metal require higher maintenance; glass will splinter inside the transport conveyors and the separator press and may discharge through the main cage of the press with the organic sludge,” says Schoenmaker. Successful recovery of the packaging itself occurs case by case. “It depends on the variety of packaging,” he adds. “If it’s just one type it’s possible to reclaim the value, but most of the time it’s a mix.”
In The Netherlands, where Schoenmaker says more than 100 biogas projects are actually mandated to accept food waste, depackaging systems are typically installed either at food processing plants, the biogas project, or at third-party recycling businesses that collect, recover and then sell the organic material. One Netherlands-based company, which produces packaged and bottled mayonnaise, catsup and other sauces — as well as a lot of organic waste during the process— installed a Mavitec depackaging system at its plant and is paid up to 10 euros ($12.35 U.S.) per ton for its packaging (all made from the same material) while selling its organic waste stream directly to a biogas plant.
A Developing Market
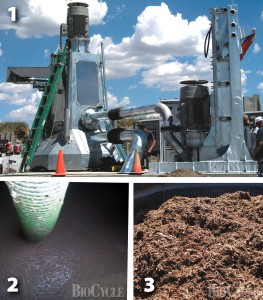
A Doda wet system Bio Separator (1) installed at A1 Organics in Denver depackages incoming organics into a slurry (2) consisting of about 10 percent solids, which gets mixed with bulking agents (3) for composting in windrows.
One fairly new client is Clean World Partners, which is installing Doda equipment in its second industrial-scale food waste to energy project, the South Area Transfer Station Biogas Energy Plant in Sacramento. “We selected Doda because the equipment is already in use in similar applications,” says Kathryn Oliver, Clean World Partners’ environmental engineer. While the wet Bio Separator depackaging system is typically fed with a front-end loader, which Oliver says is labor intensive, “we designed a system whereby trucks can dump the material into a pit and it’s augured directly into the unit. It’s fully automated. The driver only needs to turn it on, and material is metered in at a rate the Doda can process.” While that rate is dependent on the type of feedstock, it’s expected the unit will be able to process 25 tons/day (tpd) of packaged organics within an average of about four hours.
A1 Organics based in Eaton, Colorado, installed Doda equipment to preprocess packaged food waste. “We take the bulk depackaged food waste to our composting site, blend it with prepared bulking agent and process it in aerated windrows,” says Bob Yost, A1’s Vice President and Chief Technical Officer. When asked about challenges related to food waste management, Yost replied that plastic contamination is the biggest barrier. “It is difficult to remove and small amounts may end up in your finished product,” he notes. “The Doda helps remove it before the composting process.” He provides the example of material A1 picks up from a processor that is packing foods for King Soopers, Albertsons, Safeway, Walmart, Sams Club, etc. Some of their waste may still have packaging associated with it, such as a head of lettuce still in its plastic wrap. The Doda separates the food waste from the plastic using a mechanical and hydro process; the liquid stream then goes through the Bio Separator to remove the plastics, thus creating a clean feedstock for composting.
“The Doda is installed at our receiving area in Denver, where trucks enter the facility,” says Yost. Material is unloaded directly into the initial processing vault, which has a 40,000-gallon capacity. After processing, the slurry (about 10 percent solids) is hauled to A1’s composting site. “The slurry is mixed with bulking agents with a front-end loader in an engineered mixing basin along with other feedstocks,” he adds. “The mixture is then placed in windrows by the front-end loader.” The liquid slurry could be sprayed on the windrows; A1 is looking at options to do that. Water removed in the Bio Separator is returned to the vault and remixed with additional incoming material. “At times we have to add supplemental water,” explains Yost.
Investing In The Future
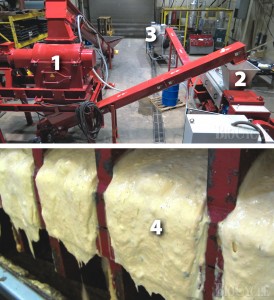
A Dupps Company Depackaging System (above) consists of a shredder (1), a press (2) and a washer (3). Organics exit the press (4).
Feedstocks have included concentrated juice mixes, dairy products and fruit drinks. “It’s been all liquid up to this point,” he notes. “We’re looking at dog food. Before we marketed our services, we wanted to make sure it was working well. It’s more labor intensive than I thought it would be. If we want to recover the packaging for recycling, we have to separate everything [by packaging type], and that often means small, short runs.” Even homogenous materials such as milk can present challenges when considering that the container might be a 1-gallon plastic jug or an 8-ounce waxed cardboard container. “It’s tough to design something that’s a one-stop shop for everything that gets thrown at you,” says Suchan.
The depackaging process begins with loading products into a hopper. An auger moves the material up to a hammer mill where the packaging is coarsely ground and augered to the organics extruding screw press. “Here, a plug forms on the back end of the screw press with the inorganic packaging material, which allows the liquid to be extruded out and pumped into 24,000 gallon receiving pits,” says Suchan. “This step allows the ‘squeeze’ to take place so as many liquids are removed during the process as possible. As the pressure builds, the plug is released and the inorganics fall into the materials bin for disposal. The packaging can then be run through a drum washer — we do not currently have this set-up at the plant — allowing it to be recycled.” The wash water from this drum would also be pumped to the receiving pit. The system can process 3 to 5 tons/hour, depending on a host of variables such as product density and solids content. “On average, 93 to 95 percent or more of the organic product is recovered in our tests. With the wash water you get closer to 97 to 98 percent or more, but you are also adding water to the organic product.”
The new dry digester technology developed in partnership with Ohio State University, combined with the wet digester already in place, will help quasar’s Zanesville facility capture more organics for energy — including corn stover, wood waste, green waste and pallets, says Suchan. Material in the dry digester will be inoculated with effluent from the wet digester system. The only packaging quasar is currently recovering and recycling is cardboard for processing in its dry digester. “As for plastics, we don’t have enough volume to bale and recycle,” he adds. “We would have to keep No. 1 separate from No. 7, and everything in between. If we continue with this process, we will have to get into doing that.”
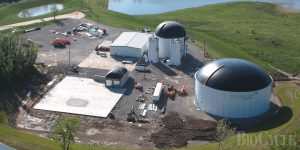
Quasar energy group’s 1MW Zanesville, Ohio, facility includes a wet digester as well as a dry digester developed in partnership with Ohio State University.
On-Line At Ontario Digester
Seacliff Energy in Leamington, Ontario, Canada, is a 1.6 MW anaerobic digestion project that flipped the switch in January 2011 (see “Greenhouse Grower As Digester Entrepreneur,” June 2011). All of its power is sold to the grid and the company buys back what is required to heat its 6.5 acres of commercial greenhouses. On the front end of the digester facility is a mammoth depackaging system from Scott Equipment Company. “It’s a standard Scott Turbo Separator,” says Dennis Dick, who runs Seacliff with business partner Roger Tiessen. “They increased it for our application, and it’s the largest installation they’ve done. It is designed for 15 tons/hour, and we are actually putting through 20 tons. It works better than advertised.”
Scott Equipment has a few projects going on in the states for separation of packaging from organic matter, says Sales Manager Pete Calderon, “but we see a lot more activity in Canada.” Government grants on one end and tipping fees on the other help make current projects in the U.S. and Canada economically viable, he adds.
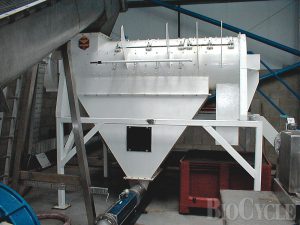
Scott Equipment’s Turbo Separator may be scaled for a variety of applications and can reclaim up to 99 percent of dry or liquid products from their packaging.
The organic slurry from the separator — about 20 percent solids — is pumped to one of two storage tanks (each with 26,400-gallon capacity). The tanks empty into the pretreatment phase of the digester process. “Incoming material is processed the same day — the fresher the better,” adds Dick. “We want to get all the gas potential available. We are currently processing grocery waste, but product destruction — we can offer the security that companies need that their product will indeed be destroyed — is becoming more and more prevalent as companies realize the services we have to offer.”
The liquid digestate is sold as fertilizer under a label certified by the Canadian Food Inspection Agency. The solids are sold as animal bedding and to a local garlic producer for mulch. The University of Guelph nearby is also testing use of the unseparated digestate on neighboring farms. “We like to work collaboratively here in our neck of the woods,” Dick says of the region known as Canada’s Sun Parlour. “The project has generated a lot of excitement, and we’ve formed some good partnerships.”