To move forward with aaerobic digestion bioenergy projects, developers must find additional sources of bankable revenue such as greenhouse crop production.
Charles Egigian-Nichols
BioCycle March 2013, Vol. 54, No. 3, p. 40
Related articles from the BioCycle Article Archive:
Digester Taps Thermal Energy To Grow Greens
February 2013, Vol. 54, No. 2, p. 33
Greenhouse Grower As Digester Entrepreneur
June 2011, Vol. 52, No. 6, p. 44
The current economic climate for development and financing of agricultural biomass based anaerobic digestion bioenergy projects is problematic due to wide-spread reduction in pricing of energy commodities as well as a decline in energy demand. These factors contribute to unpalatable pricing for bioenergy. In turn, the project financials for revenue leading to reasonable rates of return on capital are not sufficient to convince banks to offer debt on reasonable terms in support of bioenergy projects.
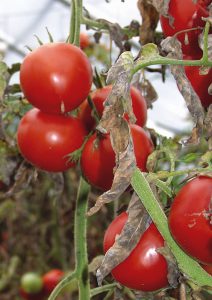
In the greenhouse, crop yield is strongly influenced by light, heat, water and nutrients. An AD bioenergy system can positively influence all of these factors.
To move forward with anaerobic digestion bioenergy projects, developers must find additional sources of bankable revenue. One potential source is the opportunity to combine greenhouse facilities with anaerobic digestion (AD) bioenergy projects. Greenhouses benefit by utilizing the heat, power and carbon dioxide (CO2) from the combined heat and power (CHP) system fueled by the AD biogas. Additional opportunities may be present to recycle nutrients, fiber and water. AD bioenergy projects benefit from a steady, monetized, reliable offtake of various project outputs. Overall CHP system energy efficiency can exceed 90 percent combined electrical and thermal. There also are job creation opportunities related to the greenhouse. Over 1,000 such bioenergy or combined heat and power greenhouse facilities are in operation, primarily in Europe.
The Greenhouse Industry
Table 1 lists several greenhouse/bioenergy/cogeneration installations in the U.S. Reliably combining greenhouse facilities with a suitable AD/bioenergy project starts with an understanding of the greenhouse industry, which splits along lines of growing vegetables or growing flowers (floriculture). Further, the industry is segmented according to size as measured by greenhouse area in acres. Large greenhouse systems cover 40 acres to over 150 acres. Medium size greenhouses cover an acre to up to 40 acres while small greenhouses are less than 40,000 square feet. Also coming into play is the type of greenhouse cover — glass or plastic sheet — as well as the local climate, which drives daylight (crop light requirements are measured in lux, the unit of luminance which is a measure of the total amount of visible light present) and heat or cooling demands.
Local climate is strongly influenced by the site’s latitude, which affects seasons, climate, temperature, humidity and so on. Additional significant aspects of understanding greenhouse operations are their cultivation and growing practices and methods. These range from the traditional hand growing with passive climate control to the newest advances in climate control, roboticized operations, and controlled environment agriculture (CEA). CEA is most often associated with hydroponic production. As with any cropping system, even slight imbalances in any of the many environmental conditions in the greenhouse, in some cases for short durations, may drive significant if not disastrous consequences such as crop losses.
Another significant factor is the market served by the greenhouse operation. In the case of fresh tomatoes (versus processing tomatoes for paste and sauce which are field grown), the U.S. retail and foodservice industry markets have grown steadily while prices have held steady or increased slightly. These markets have grown in scale and are year round in scope. By comparison, floriculture markets tend to be more seasonal responding to consumer cycles and expectations, e.g., poinsettias at Christmas.
Greenhouse growers face many risks associated with production and production inputs. When looking to combine their greenhouse facilities with AD/bioenergy projects, growers will go slow, test, verify, prove and get experience at a small scale and then ramp up. Depending on the range of interactions, the AD bioenergy system may become highly integrated into the greenhouse operation, providing a strong economic motive to pursue this synergistic relationship. At the same time, the operator will demand high reliability.
Integrating Bioenergy Systems
The value proposition between the greenhouse and the bioenergy AD operation is driven by the following factors: High quality CO2, heat, power, water, vehicle fuel, other fertilizers and biomass waste management. In the greenhouse, crop yield is strongly influenced by light, heat, water and nutrients. An AD bioenergy system can positively influence all of these factors. Significant interest arises for the CO2 in the CHP engine exhaust — the air stream after combustion. The exhaust is primarily CO2, especially after it passes through a catalytic converter. The tail gas — left over from the gas clean up process — also contains CO2 (as well as a fair amount of hydrocarbons, making it combustible in a boiler). An actively growing crop can quickly deplete the greenhouse CO2 levels thus limiting crop yield. To optimize and maximize crop yield, growers supplement the greenhouse CO2 levels, typically purchasing food grade liquid CO2 by the tanker load at $80 to $200/ton of CO2.
Taking into account all portions of the greenhouse cost structure, the bioenergy AD project is able to beneficially impact about 40 percent of the greenhouse’s day to day operational costs. If this results in a 10 percent net benefit to the greenhouse, operating costs are reduced by 26.7¢ per square foot. This savings increases the bottom line return by the same amount thus the operator’s return over operating costs increases from $1.14 per square foot to $1.407 per square foot, or 23.4 percent overall increase in value (“Commercial Greenhouse Vegetable Production,” Agri-Facts, 2001).
Carbon dioxide is greater in value to a greenhouse than the heat (about 60%/40% in relative value based on $4 per mmBtu natural gas price). The greenhouse operator has two goals by utilizing the CO2: 1) Maintain adequate levels to allow the crop to thrive; and 2) enrich the CO2 in the greenhouse by double that of ambient levels (350 parts per million to 700 ppm). This is why greenhouses are often located near inexpensive sources of CO2, such as in Texas.
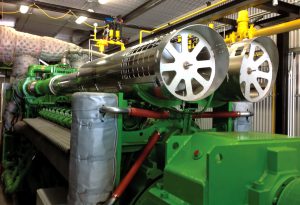
The GE Jenbacher J624 gas engine (above) for greenhouse CHP has a two-stage turbocharger to enable a high level of heat recovery. The cogeneration technology combines the engine, catalytic converter and heat exchanger.
A key issue is quality of the CO2. At one biogas facility in Europe, a trial was conducted using the CO2 in the exhaust from its CHP unit in the greenhouse. The sulfur and other impurities in the biogas caused the test to fail. The sulfur consumed the catalytic converter on the unit’s engine. The converter eliminates any carbon monoxide in the CO2 stream so that employees can safely work in the greenhouse. It is generally recommended that the biogas be cleaned before combustion in the CHP units, versus trying to remove impurities after combustion.
The pipeline quality biogas option also is able to produce excellent synergy with a greenhouse as the tail gas may be cleaned leaving a substantial stream of CO2. While this setup doesn’t provide the thermal energy from a gas engine, the pressure swing absorption process (used to clean the gas to pipeline quality) does yield a combustible gas in the range of 250 to 400 Btu/cubic foot, which is adequate for a boiler arrangement. The overall net is somewhat less heat but there is still thermal energy for the greenhouse. Heat or thermal energy can be captured from the compression processes as well.
Running the numbers based on a conceptual design of a large generation complex illustrates the synergy between the greenhouse industry and AD bioenergy. The design included 28 megawatts (MW) of electricity output, which could supply enough heat for a greenhouse that is 140 to 150 acres in size. This assumes a boiler is available for smoothing out peaks during the winter, with the CHP units operating about 5,000 to 6,000 hours/year. If grow lights are incorporated into the greenhouse, additional heat is produced by the lamps, reducing heat demand by approximately 15 percent during artificial lighting periods. This period is roughly 10 to 12 hours/day in winter months, and may be enough to offset peak boiler demand.
Key assumptions and results in this analysis include:
• The facility will be 85 percent efficient overall in combined heat and power mode (15% total heat losses). This results in 800,000 mmBTU per year provided to the greenhouse. This amount of energy represents 75 percent of the heat consumption of a 140-acre greenhouse.
• The price for the heat includes a 20 percent discount off market rates, assuming a market rate of $4.00/mmBTU. It was assumed that this price escalates with the Consumer Price Index.
•The CO2 and heat value to the bioenergy project is significant and appears to move the project into the black or “Proceed” column.
Charles Egigian-Nichols, P.E. is Vice President of Tetra Tech Bioenergy LLC.