A steady stream of anaerobic digestion facilities are coming on line, most equipped to process food waste. This first of a two-part series profiles several farm digesters. Part I
Nora Goldstein
BioCycle June 2014
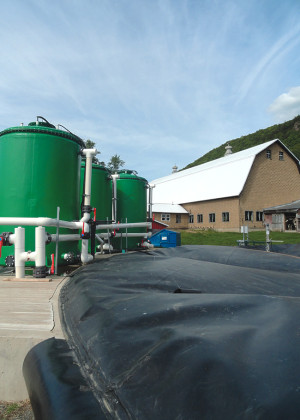
The new digester at Longview Farm in Hadley, Massachusetts has three receiving tanks for food waste. They are separated and stored based on their energy content.
In the past several weeks, we received invitations to two ribbon cuttings for newly installed farm-based digesters — one at a dairy farm in western Massachusetts and another at a swine operation in North Carolina. We also received a press release from the University of California, Davis, about its new food scraps digester on campus. And then there were a few new projects that we had been tracking, but needed to reach out to for details.
A visible driver for project development, especially in New England, are state policies to ban disposal of organic waste streams. Connecticut’s law has been in effect, requiring generators producing >2 tons/week of commercial organics and located within 20 miles of a composting or anaerobic digestion facility to divert those organics. The Massachusetts disposal ban on commercial organics (for those generating >1 ton/week) goes into effect in October 2014. And Vermont’s Universal Recycling Law kicks in July 1 for commercial, institutional and industrial operations generating >2 tons/week of food scraps and located within 20 miles of an organics processing facility (to date, only composting sites are available).
Less of a driver, but still significant, are the renewable energy incentives. All of the farm digesters are selling power to the grid under fairly favorable arrangements. And the three projects profiled in this article all received federal Section 1603 funds (an incentive that is no longer available) to cover a portion of the fixed capital costs.
Part I of this article focuses on agricultural digesters. Part II, to appear in the July issue, focuses on merchant or institutional digesters processing primarily food waste streams (including two in development in Connecticut).
Barstow’s Longview Farm
The anaerobic digester installed at Barstow’s Longview Farm in Hadley, Massachusetts began operating at the end of December 2013, meeting the Section 1603 requirement to be operational in 2013. The digester facility was developed by BGreen Energy, a special purpose company comprised of the facility investors and owners. “It is the same project development model we used under the name AGreen Energy, the entity created for the digester at Jordan Dairy Farm in Rutland, Massachusetts, which began operating in the spring of 2011,” explains William Jorgenson of AGreen and BGreen Energy. “But the shareholders are different. In both cases, the farms have significant ownership in the digesters.” Also in both cases, Casella Organics, a regional resource management and recycling company, is a partner and supplies the source separated food waste as well as operates the digesters.
A 600,000 gallons capacity RCM digester was installed at Longview Farm, along with three receiving tanks for food waste. (Jordan Dairy’s digester was supplied by quasar energy group.) “We take so many different feedstocks and know the energy level of each because we monitor all incoming loads once the baseline testing is done for each source,” explains Jorgenson. “We store these materials based on the energy level, e.g., glycerin goes into the ‘high energy’ tank and whey goes into the ‘low energy’ tank. Then we mix and dose these substrates in to maximize the gas, and thus the power output, of the system.” He adds that the recipe at both the Jordan and Longview dairy digesters is about one-third manure and two-thirds food waste. At Jordan Farm, with 375 cows, that equals about 20 to 25 tons/day of manure and 45 tons/days of food waste. On Longview Farm, with 250 dairy cows, manure is about 20 tons/day and food waste is about 30 tons/day.
“What we are learning, based on our experience at Jordan Dairy, is how much better we can do with energy production given the amount of material received,” notes Jorgenson. “The industry needs to realize that every renewable energy feedstock becomes a determinant of business profitability and that the availability of that feedstock will be more competitive overtime. And we need to plan for the long term — we need to produce as much power out of every ton of feedstock we get as the day will come when we will be paying for feedstock and have to be maximizing energy generation.” Longview Farm started out with a 350 kW engine, with the intention of going to a 500 kW engine within a year. (Jordan Dairy started out with a 350 kW and now operates a 500 kW unit.) Both installations use Guascor engines supplied by Martin Machinery.
The Commonwealth of Massa-chusetts has a net metering law, requiring utilities to pay retail price for all distributed power (such as from anaerobic digesters) put onto the grid. In addition, the distributed power generator retains ownership of the Renewable Energy Credits (RECs), and has the right to sell those as offsets to other entities. “This is huge,” says Jorgenson. “We get paid retail rates for electricity and sell our own RECs.”
In the case of the AGreen and BGreen projects, one buyer of the power is Agri-Mark/Cabot Creamery Cooperative, one of the food processing companies sending feedstock to Longview Farms. Casella Organics initially was hauling whey buttermilk from the creamery to Jordan Dairy, which is 75 miles one way. The new BGreen digester, however, is 15 miles from the Creamery, improving the transportation economics of recycling the material — and Longview Farms is a member of the Agri-Mark dairy cooperative. “The energy credits for power we are buying represent 10 to 12 percent of the total electric bill for the creamery,” explains Jed Davis, Director of Sustainability for Cabot Creamery Cooperative. “From the perspective of Longview being a member dairy, in addition to providing us with milk, they are providing — via a ‘net metering credit allocation agreement’ — some of the load to run our facility. And we are closing the supply chain loop, so to speak, by sending our source separated organics to the dairy’s anaerobic digester.”
Casella arranges the service contracts with food processors and other generators, looking for longer term arrangements, ideally five years. At this time, food waste is only received via tanker trucks at both Jordan and Longview farms. “One lesson we learned early on is balancing our requirements for food waste inputs with those of food processors, who have their own production cycles and seasonal fluctuations,” notes Jen McDonnell, Director of Sales and Marketing for Casella Organics. “We were fortunate in that, given our customer mix, we ‘oversold’ our actual capacity at Jordan Farm, which gave us momentum in aggregating feedstocks to start up Longview Farm. We are managing the materials so each digester is able to absorb the excesses at different times.” Soon the digesters will get material from a Whole Foods Market in the Boston area that is doing the first commercial test of the Grind2Energy™ food waste slurry process (see “Grinding Food Waste For Bioenergy,” September 2013). This is the first retailer to be sending organics to the digesters.
The digester at Longview Farm is permitted under Massachusetts’ new General Permit, which allows it to process up to 100 tons/day of organic materials, including the manure. “There is significantly less expense and time involved in permitting a facility under this new rule,” says Jorgenson. “In exchange, we are required to comply with testing protocols, annual reporting and certify that these protocols are being followed. The Jordan Dairy digester was permitted under a Determination of Need, the previous permit for this type of operation prior to the state’s rule revisions in 2012. Jordan just switched to a General Permit this month.”
Liquid digestate is being stored on the farm to fertilize corn and hay. A plan is being tested to transport the digestate to an off-site storage tank at a nearby farm that has adequate acreage of sweet corn to utilize the nutrients as well. Jordan Dairy Farm grows about 450 acres of corn silage and 450 acres of hay (grass/legume mixes). It utilizes manure/digestate on approximately 350 acres of corn and 200 acres of the hay. A March 2014 progress report from the USDA Natural Resources Conservation Service in Amherst, Massachusetts states that “since applying the manure/digestate fertilizer on their hay lands, the Jordans have noticed that now most of their fields are yielding four cuts of hay rather than three cuts.” Manure/digestate is applied after the second, third and fourth cuts. “With the added fertility and moisture from the manure/digestate, hay yields have increased approximately 25 percent from an average of 4 tons/acre to 5 tons/acre,” notes the report, adding that the Jordans have saved about $40,000 in nitrogen fertilizer expenses by using the manure/digestate.
Homestead Green Energy And Agrirenew
The Homestead Green Energy anaerobic digesters in Plymouth, Indiana began generating power in September 2013. The facility is operated by Homestead Dairy, which has 1,800 milking cows and 300 dry cows. “Homestead Dairy had been researching anaerobic digestion for about five years before it decided to move ahead with a project,” notes Andy Austin of Specialty Concrete Construction, the general contractor for the two tank, complete mix digester facility. “The dairy was interested because of the odor reduction opportunity, as well as a power purchase agreement (PPA) with Northern Indiana Public Service Company (NIPSCO) that was offering a 15-year feed-in tariff contract.”
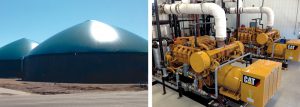
The Homestead Green Energy anaerobic digestion facility (left) in Plymouth, Indiana processes manure from 1,800 milking cows, along with fats, oils and grease. Power generated by two 600 kW CAT engines (right) is sold under a 15-year power purchase agreement.
Two digester tanks, each holding 933,000 gallons, are 85-feet in diameter with 24-foot high walls. Specialty Concrete’s tank system has in-wall heating, i.e., the heating tubes are housed in the concrete wall as well as the floor of the digester tank. “This protects the tubes as they aren’t directly in the substrate,” explains Austin. “The digester runs at mesophilic temperatures and has internal mixing.” In addition to manure, the digester processes fats, oils and grease and waste silage. Retention time in the AD system is 23 to 25 days. Digested effluent goes through a belt press; solids are used for bedding and the effluent is land applied. “Prior to putting in the digester, the dairy was separating out manure solids and using that for bedding,” he adds. “They are much happier now using the digested solids. The bedding is much more homogenous.”
Homestead Green Energy installed two Caterpillar (CAT) 600 kW engines. Heat recovered from the engines is used for the digesters and the manure reception pit. The project received Section 1603 funding to cover a portion of the fixed capital costs. Its PPA with NIPSCO expires in 2028.
Specialty Concrete also constructed the AgriReNew anaerobic digesters at the Sievers Family Farm in Stockton, Iowa, a feedlot with 2,400 beef cattle. The digesters, which use the Organic Waste Systems (OWS) technology, process both bedded pack and scraped alley beef manure along with ground corncobs. It began operating in 2013, and received Section 1603 funds as well. The facility consists of two 85-foot complete mix digesters, a digestate processing system, and a 1,000 kW CAT engine. Electricity is sold to Interstate Power & Light; waste heat is used for heating the digesters, manure scraper alleys, reception pits and for fiber drying. Separated solids are used for compost production. Digested liquid effluent is applied to field crops. The AgriReNew facility recently was given a 2013 Biogas Project of the Year award from the American Biogas Council. OWS provided startup, commissioning and ongoing consultancy to both projects.
Biogas Energy Partners
A Maine-based venture, Biogas Energy Partners, has been assembling the pieces to a 21st century organics recycling company comprised of farm-based anaerobic digesters, food waste collection, renewable compressed natural gas fueling station and greenhouse operations. Its first facility, Exeter Agri-Energy (EAE), is located at Stonyvale Farm in Exeter, Maine, a dairy with 1,000 milking cows, 150 dry cows and about 800 youngstock. Its anaerobic digester, using the CH Four Biogas complete mix tank system, has been operating since late 2011 and is sized to process about 150 tons/day of manure and source separated food waste. “Right now, we are mixing about 20,000 gallons/day of manure with about 10,000 gallons/day of food waste, but are working toward a 50:50 ratio going into the digester,” says Adam Wintle, Managing Partner of Biogas Energy Partners (BEP). Stonyvale Farm owns and operates EAE as a subsidiary, and BEP is the development company responsible for overall business management related to the organics recycling and renewable energy ventures. “We are trying to lay the foundation for extensive growth,” adds Wintle. “A big component of that is sourcing food waste.”
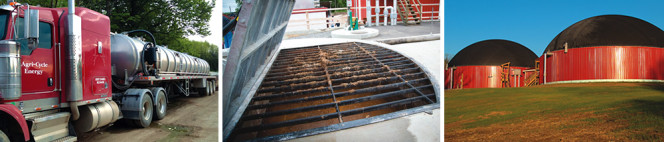
Biogas Energy Partners in Exeter, Maine recently formed an organics collection company that services food processors and commercial food waste generators. Its fleet includes vacuum tanker trucks (left). Incoming food waste is emptied into heated tanks (middle), and then fed with manure into anaerobic digesters at the Exeter Agri-Energy facility (right).
Recently BEP formed Agri-Cycle Energy, an organics collection company that is servicing food processors as well as grocery stores and other food waste generators. It operates, in partnership with a local hauling firm, 8,500 gallon vacuum tanker trucks, 30-ton dump trailers and modified rendering trucks used for solid food waste collection. Separated organics are being collected from Hannaford Brothers and WalMart grocery stores, among others. “All the liquid wastes are emptied directly into three heated tanks (total capacity of 75,000 gallons) equipped with contamination screens and chopper pumps,” notes Wintle. “On the solids side, the rendering truck unloads into a bunker. We purchased a Remu bucket grinder that is attached to a front-end loader. The bucket processes about 3 cubic yards/minute of food waste and discharges directly into one of the substrate tanks.”
The EAE AD system has two 400,000 gallon tanks that operate at mesophilic temperatures. Retention time is in the 25 to 30 day range. The facility currently has a 1 MW biogas engine, but recently has secured a contract (see below) to increase biogas production to 3 MW. It also is moving ahead with a second AD facility to be built at Flood Brothers Farm in Clinton, Maine. “We have local approvals needed to proceed with the facility,” he says. “The farm milks about 2,000 head, producing about 60,000 gallons/day of manure. We’ve sized this project to produce 6 MW utilizing an equivalent daily dosing of food waste to that of the manure. We anticipate having the first phase of the facility in operation within 12 to 18 months.”
Both the Exeter and Clinton facilities secured 20-year fixed rate energy contracts through the Maine Public Utilities Commission’s (PUC) Community-based Renewable Energy Pilot Program, which set aside a total installed generating capacity (all program participants combined) of 50 megawatts. The 50 MW cap has been reached and the BEP projects are the only two AD facilities in the mix (EAE at 3 MW and Clinton at 6 MW) among solar, wind and hydro renewable energy participants. The average price per kilowatt-hour within each contract year cannot exceed 10 cents. “Program participants have to petition the PUC to financially justify why a given project requires 10 cents/kWh to maintain sustainability,” explains Wintle.
The Exeter digester received close to $3 million in state and federal grant funds; almost $1.8 million was from the Section 1603 incentive. Wintle states that without this financing, the anaerobic digestion project would not have been feasible. However now that the plant is up and running, the planned expansion to 3 MW will be funded internally. “We are at a scale where that is feasible,” he says.
BEP plans to service food waste generators in Massachusetts, where the state’s commercial organics ban goes into effect this fall. “Although our AD facility is four hours from downtown Boston, the reality is that we have a lot of favorable advantages by locating our digesters on very large dairies in Maine,” Wintle observes. “Lower cost real estate, fairly easy permitting and extensive land base to manage all the effluent essentially for free works in our favor to a high degree. Our scale and ability to import upwards of 150,000 tons/year of food waste provides a real solution for generators. And to address the transportation expense and environmental concern, we are planning to utilize renewable compressed natural gas harvested from our biogas operations in our long haul fleet vehicles, which will lower our transportation costs by as much as 30 percent and eliminate the harmful fossil fuel footprint associated with burning diesel. Without that renewable fuel option we would probably be more concerned about our ability to be a cost-effective outlet for Massachusetts-generated food waste over the long term with so much uncertainty around escalating fuel costs.”