Educational greenhouse at City of Boston yard trimmings site is using heat and moisture captured from aerated static piles to sustain a year-round growing operation.
Gaelan Brown
BioCycle November 2015
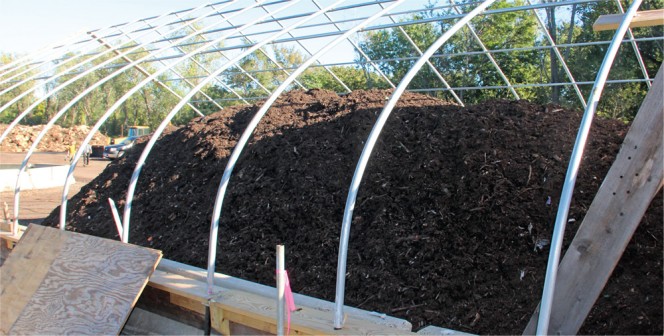
A 250-cubic yard capacity, 3-zone negatively aerated static pile system was installed by City Soil & Greenhouse, LLC at the City of Boston yard trimmings composting site.
Attendees of the BioCycle REFOR15 conference in Boston North Shore last month had an opportunity to tour a unique aerated static pile (ASP) composting system in which heat, water and carbon dioxide are recovered for use in an educational greenhouse at the Mattapan Ecovation Center in Boston, operated by City Soil & Greenhouse LLC (City Soil). The Center is located at the City of Boston Composting Facility that City Soil manages under contract to the Boston Public Works Department. The facility is on part of the Massachusetts Audubon Society’s Boston Nature Center.
The 2,800 sq.ft. composting greenhouse has capacity to recycle approximately 1,000 cubic yards (cy) of organic materials annually. It includes a 250 cy capacity, three-zone aerated static pile (ASP) composting pad integrated with a biofilter to capture odors, and raised growing beds that can be heated with radiant heating loops supplied with hot water from the compost heat recovery system. The system enables year-round greenhouse operation through the cold winter months of Boston without any additional thermal energy inputs. Condensation from the aeration stream is used for crop irrigation along with CO2 emissions from composting that are directed into the greenhouse to increase crop yields. “This greenhouse establishes a national urban model that combines state and private funding with local resources and talent to address a multitude of climate change-related impacts,” explains Bruce Fulford of City Soil.
Mayor Martin J. Walsh’s Office of Neighborhood Services, the City of Boston Public Works Department and the Office of Environment, Energy & Open Space joined community partners in supporting development of the ASP composting system and greenhouse facility. “Each and every single resident and visitor to the City of Boston plays a vital role in the well-being of our environment,” notes Mayor Walsh. “By working together, we can make Boston one of the most sustainable and climate-resilient cities in the country. It starts with us, and this greenhouse is a part of our solution.”
Innovative Technology
The compost aeration and heat recovery system known as The Compost Heat Wagon™ was built and installed by Vermont-based Agrilab Technologies. The patented Agrilab Inside™ process uses a specialized heat exchanger core that heats water as it is circulated, extracting energy from the compost vapors in the aeration stream. The heat transfer varies depending on the vapor flow, water temperature and flow rates. The Compost Heat Wagon at the Ecovation Center has been aerating about 100 cy (50 tons) of material during the first batch of compost produced. As much as 60,000 Btu/hr of thermal energy is being captured, with hot water output temperatures ranging from 130° to 140°F. The unit, when operating under maximum aeration (400 cfm of vapor flow) can produce up to 280,000 BTU/hr.
Fulford has long been a pioneer in researching ways to heat and enrich greenhouses via integration of composting, including a groundbreaking system at the New Alchemy Institute in the mid-1980s. “This system has been a dream of mine for decades,” he notes. “Compost-heated greenhouses can become a pivotal tool to improving the environmental quality, operating efficiency and host community benefits of composting operations in diverse settings.” City Soil is a privately-owned company dedicated to placing Massachusetts at the center of sustainable agriculture and energy innovation by helping to grow Massachusetts’s organic waste recycling infrastructure and by integrating renewable energy production with healthy, productive soils and landscapes that are resilient to the effects of climate change.
One side of the greenhouse at the Mattapan Ecovation Center contains the ASP pad and the other side contains the growing beds. The negative ASP composting pad is connected via ductwork to the Compost Heat Wagons aeration and heat recovery system. The entire system, including the greenhouse, was built in under two weeks, starting with just a gravel parking lot. No concrete or permanent infrastructure was used.
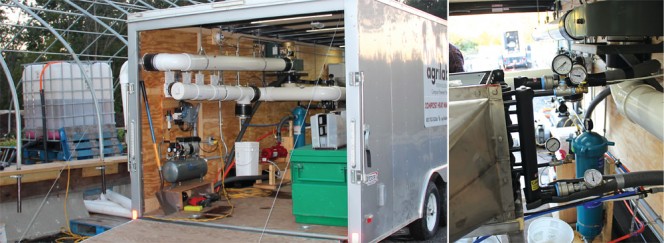
The Compost Heat Wagon™ was built and installed by Agrilab Technologies. It contains the aeration fan, plumbing and ductwork (right) that provide aeration, heat recovery and condensate. Container holding heated condensate is in the greenhouse (shown on far left in heat wagon photo). Photos courtesy of Agrilab Technologies
The biofilter feature is important at this urban composting site so that the facility can increase throughput and responsibly manage urban food scraps from the city’s schools, farmers markets and other sources. The heat exchanger integrated with the compost aeration system cools the compost vapors below 100°F and condenses much of the moisture from the vapor stream before it is exhausted into the biofilter. Hot air pulled from the compost by the Agrilab compost aeration and heat exchange system is transferred to heat water in the greenhouse. Computer-controlled variable speed drives are used to fine-tune the aeration fan and hot water circulation pumps.
The biofilter is inside the greenhouse and consists of a 24-inch deep bed of wood chips and compost-amended soil on top of perforated pipes coupled to the exhaust of the aeration system, and integrated with productive growing beds. The physical structure and biology of the biofilter effectively absorbs and utilizes odorous compounds from the composting material. Odorous off-gases include ammonia; when it is absorbed by the soil in the raised beds, ammonia is biologically converted to ammonium nitrate, and fertilizes plants in the greenhouse. The Mattapan Ecovation Center has already produced tomatoes, culinary and medicinal herbs and green roof plantings. Its is now being used for growing salad greens and propagating perennial plants, fruit crops, and native trees for use in the surrounding landscape and to demonstrate that crops with commercial and ecological value can be produced.
Data sensors and a computer controlled aeration system ensure that the composting piles always have adequate oxygen levels. This speeds up the composting process, eliminates methane emissions, and reduces odors and the carbon footprint of composting organic materials.
The Mattapan Ecovation Center was made possible through a grant award from the Urban Agricultural Program at the Massachusetts Department of Agricultural Resources (MDAR). City Soil partnered with the Suffolk County Conservation District (SCCD) on the grant, and contributed and secured more than $100,000 in materials and services as a match to the MDAR funds for the project. The Center serves as a template for future collaborative projects between City Soil, the City of Boston, Mass Audubon, state government and other stakeholders in creating assets in the regional food system.
Gaelan Brown is Vice President of Sales and Marketing, for Agrilab Technologies, founder of the Compost Power Network and author of the book, “The Compost Powered Water Heater.”