Campus analyzes costs, collection systems and logistics to increase diversion of organics, which will be processed at City of Edmonton’s new AD facility. Part I
J. Kwasny, S. Leblanc, K. Yan and D. McCartney
BioCycle May 2016
The University of Alberta (UAlberta) is one of the top five teaching and research universities in Canada and home to 39,000 students and 15,000 staff and faculty. UAlberta has four campuses in Edmonton and one in the nearby city of Camrose. As part of its ongoing commitment to sustainability, the university is working closely with the City of Edmonton’s Utility Services on design and development of a new anaerobic digestion (AD) facility. UAlberta has set a target to capture 75 percent of organics from its waste stream in order to provide 1,650 tons (1,500 metric tons) of source separated organic feedstock to the AD facility. It also outlined a goal in its new Sustainability Plan to reach 90 percent waste diversion by 2020.
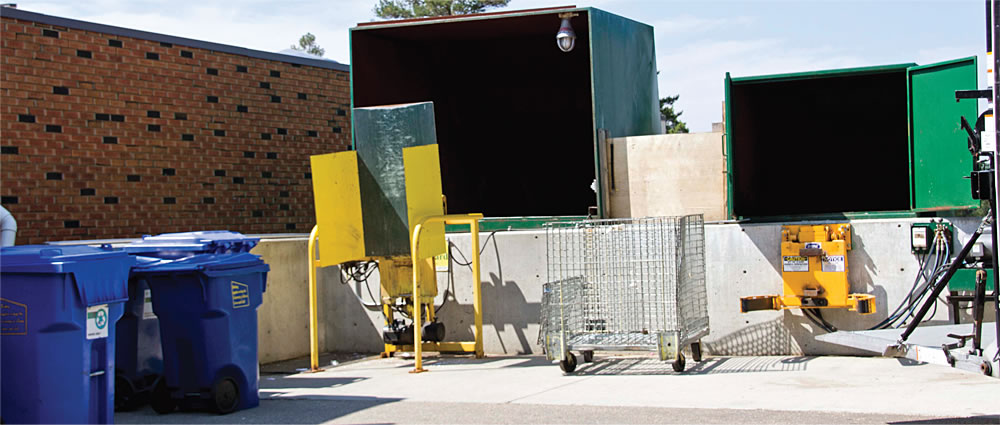
The university uses its own collection trucks to take recyclables in small rolling carts to the on-site recycling transfer station for consolidation. Using a similar internal collection model for organics was shown to be cost neutral. Image courtesy of University of Alberta
To achieve these goals, UAlberta needed to reframe the way it looked at its waste system and pursue a more holistic Zero Waste approach to resource management. The university worked closely with an expert team from the Edmonton Waste Management Centre of Excellence and Tetra Tech EBA. The team brought innovative approaches, sustainable materials management expertise, current examples of Zero Waste best practices, and a change management framework, all of which were critical in studying and redesigning the UAlberta’s solid waste management system.
The City of Edmonton’s high solids digester is scheduled to be in operation by late 2017, creating a sense of urgency to have increased organics diversion in place within a 2017/18 timeframe. This resulted in an expedited planning and pilot project implementation process. Three of the highest organics generating buildings on campus were chosen as pilot sites for the new Zero Waste system. To help design the most efficient and cost-effective system, scenarios were developed and analyzed using a full cost accounting method that looked at current and future scenarios by adjusting factors such as container size, pick up frequency, and hauling process.
Asset And Costing Analysis
UAlberta is committed to sustainability, but like many publicly-funded institutions, it must work within a limited budget. Given these budget pressures, it was extremely important to build a strong business case for expanding organics collection. An asset and costing analysis was undertaken that examined the existing and possible future system on North Campus, the largest of the university’s campuses.
North Campus spans about 285 acres (115 ha) with more than 80 buildings that receive solid waste collection services. The university operates an “internal” collection model for recyclables, whereby university-owned collection trucks take recyclables in small rolling carts to the on-site recycling transfer station for consolidation, followed by removal by the contracted hauler for processing. Solid waste and organics operate on an “external” collection model; solid waste is serviced directly by the hauler from front load bins and compactors at each building, and organics are serviced in rolling carts at each building by the contracted hauler with a per cart fee.
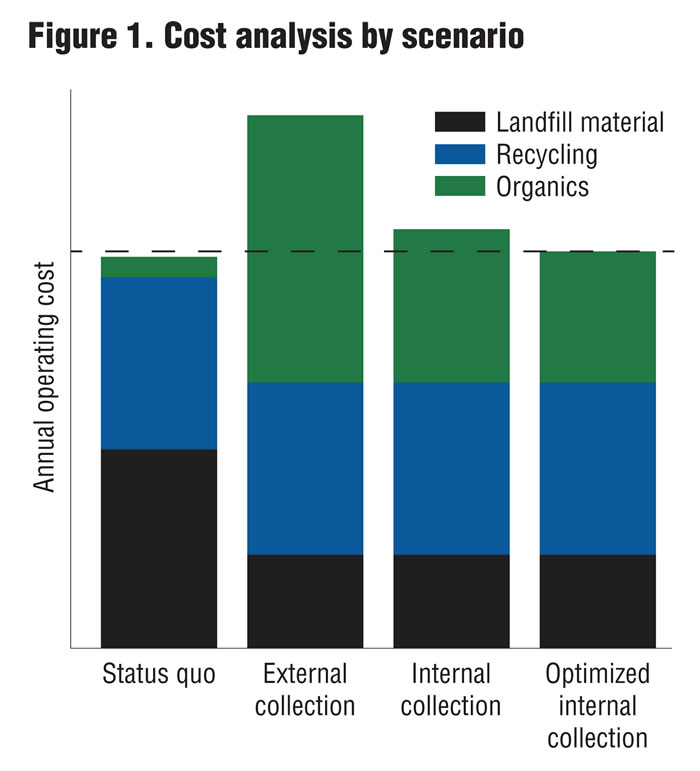
Figure 1. Cost analysis by scenario
The costs of internal collection scenarios for organics collection were compared against the status quo external collection scenario. Importantly, the number of buildings receiving organics collection service in the status quo scenario was only 15, and the intent was to study the impact of expanding organics collection to all 80 buildings on North Campus to reach the target of 1,650 tons. Currently, about 500 tons of organics are being diverted.
The costing analysis determined that expanding the system using the external collection method would result in a 40 percent increase in the total operating budget for waste management (Figure 1). It was found that a shift to the internal collection scenario would make the system more efficient and nearly cost-neutral compared to the current budget, because the organics cost would change from a specialty per cart fee to a standard compactor lift fee. Further scenarios were developed where buildings with particularly high organics generation rates would be given their own front load bin or small compactor to consolidate organics at the source of generation (i.e. immediately at the building), for hauling by the contracted hauler. This targeted change, optimizing internal collection, could result in even further cost savings (Figure 1).
To wrap up the cost analysis, a sensitivity analysis for cost increases over the next 20 years was conducted with variables such as tipping fees, organics capture rates, and fuel prices. Additional factors also were evaluated:
- Collection routes were reviewed and optimized based on service times for the internal collection scenario.
- Greenhouse gas mitigation from organics capture (i.e., sending to AD instead of landfill) was estimated to be 1,800 metric tons of CO2 equivalent per year.
- A triple bottom line assessment was conducted to further validate the social, environmental and economic impacts associated with increased organics diversion.
Zero Waste Pilot Buildings
Change management was kept top of mind during the pilot building planning process. This was especially important because the management systems are unique in the three pilot buildings selected. Other stakeholders included cleaning staff, retail and food tenants, student services, student residents, staff and faculty. Each of these groups was brought in at an early stage in the discovery process to understand their values, knowledge, barriers, and priorities. This really helped build buy-in from different groups during the process. Once roll-out was ready to happen there was a high level of readiness and willingness from all participants.
The three buildings were chosen for their high organics generation rates. Lister Centre is an 1,800 student residence with a full commercial kitchen and a conference center. The Students’ Union Building (SUB) is accessible 24 hours a day as a study space, about 12 hours a day as a cafeteria with multiple food outlets, and it houses services like the bookstore, health center, pharmacy and student services offices. The Housing Union Building (HUB) is a four-block-long residence and mall with both retail and food vendors. Lister and SUB had some organics capture already occurring, while HUB had no existing organics collection.
The programs implemented in these buildings were intended to be pilots that would be monitored, fine-tuned and rolled out across the university. They were developed using a four phase process: characterization, conceptual design, implementation and evaluation.
Phase 1: Characterization
A process map was developed for each building, outlining responsibilities, management structure, and operational practices. Surveys and focus groups were conducted with each of the stakeholder groups to determine their readiness for change, guide conceptual design decisions and inform communications and education efforts. Some key findings showed that each building had inconsistent signage and waste containers, inconsistent material streams collected, and limited organics collection. In addition, there were gaps in knowledge among user groups about how to use the existing waste diversion system and frustration around the inconsistent infrastructure provided. However, there was also a willingness to participate if the system was improved.
Phase 2: Conceptual Design
Workshops were facilitated with representatives from different groups for each pilot building. These workshops were used to set priorities and make decisions. The number of material streams was simplified from six streams to four: Mixed Paper, Recyclables, Organics, and Landfill.
Consistent and user-friendly Zero Waste stations and signage were designed based on examples of systems from across North America. Four-color stations and vivid, graphics-heavy signage were chosen and a Zero Waste brand was developed to support communications.
Floor plans and foot traffic were analysed to ensure Zero Waste stations were placed near high traffic areas, food services, and building egress points. A clear and consistent division of responsibilities was agreed upon for collection, whereby food service staff members take their own materials to central collection points and cleaning staff service public stations and central collection points.
Phase 3: Implementation
The new Zero Waste program was rolled out in two stages, with Lister and SUB in September 2014, followed by HUB in February 2015. Lister and SUB already had back-of-house organics collection and were further ahead than HUB in terms of participation and user buy-in. Zero Waste stations and signage were put in place, on-site training sessions were held with food vendors and cleaning staff, and in the case of HUB, posters and handbills were delivered to residents outlining how to use the new system.
Phase 4: Evaluation
Once the Lister and SUB programs were completed, user surveys, visual monitoring of user behavior, and a series of spot waste audits were conducted. This early evaluation informed a few key changes and modifications before the Zero Waste system was rolled out in HUB. For example, the Mixed Paper stream had a high level of contamination with coffee cups, napkins, and compostable take-away containers. This led to changing the shape of the Mixed Paper opening in the Zero Waste stations installed in HUB, from a rectangle to a diagonal slot. Backboard signage was also made larger and a short list of acceptable items was added to the graphics.
The entire process was a team effort, using both internal and external expertise to build capacity among university staff members who will ultimately expand the program. Lessons learned from the three pilot buildings can inform the expanded campus-wide program roll out ensuring sound decisions are made. The collaborative approach undertaken involved people from the ground up to build buy-in and increase awareness throughout the planning and early implementation stages. With these successful pilots underway, the University of Alberta is well positioned to expand the program and meet its 1,650 tons organics target.
Jessie Kwasny is the Waste Diversion/Recycling Coordinator and Shannon Leblanc is a Sustainability Coordinator, both with the University of Alberta. Kentson Yan is a Research Engineer and Daryl McCartney is the Executive Director at the Edmonton Waste Management Centre of Excellence. Part II of this series will provide more results from continued monitoring and new developments related to program expansion.