Installation at Vermont Natural Ag Products reduces total composting time, creating more capacity to process food waste from the local solid waste district.
Robert Spencer
BioCycle March/April 2018
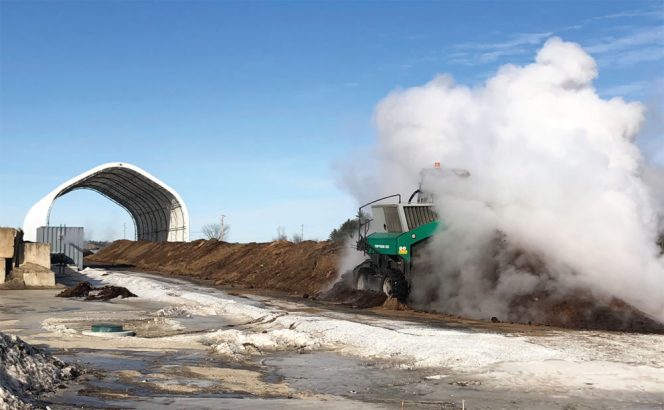
The AGT compost aeration and heat recovery system (CAHR) captures energy in steam in compost windrows for on-site heating uses. Photo by Robert Spencer
Foster Brothers Farm also operates Vermont Natural Ag Products (VNAP), a sister company located on the farm. With a 10-acre composting pad, it is one of the largest composting facilities in the Northeast, processing over 50,000 cubic yards/year of dairy manure, food residuals, forest by-products, horse manure, poultry manure, and waste animal feed. Tipping fees are charged for a small portion of the materials, and the Fosters also pay farmers for manure.
VNAP has brought Foster Brothers Farm back into the renewable energy space, this time by installing an innovative system that recovers heat from active composting piles. After a successful pilot, VNAP expanded its heat recovery capacity.
Composting Operation
VNAP has an extensive market for its MOO DOO® line of soil products, shipping pallets of compost, mulch, and potting soils to garden centers throughout New England. About half of the compost product is bagged, and the other half is sold in bulk. In terms of equipment, a Komptech Topturn windrow turner aerates and mixes the windrows. An Erin screen is used to screen the final compost. Compost is dried in a propane-fired dryer, and then put into bags in an automated bagging operation.
Recognizing that each ton of organic material releases approximately one million British Thermal Units (BTU) of heat and water vapor when it is aerobically composted, the Fosters are now capturing energy from the manure and other organic materials composted on the farm. In 2016 VNAP contracted with Agrilab Technologies Inc. (AGT), based in Enosburg Falls, Vermont, to install a compost aeration and heat recovery system. Thermal energy from its active composting windrows is used to accelerate the composting process in the windrows, dry finished compost prior to bagging, and heat its compost bagging building.
Phase I of the AGT system utilizes the AGT Hot Box 250R™, which consists of a specialized heat exchanger with four aeration zones (controlled by computer) that can pull or push air through windrows. The Hot Box draws energy rich vapor via negative aeration into the specialized heat exchanger. A water-glycol mix is pumped through the heat exchanger to the compost bagging building where it flows through the radiant floor heating system previously heated with oil. Another heat exchanger in the Hot Box uses the circulating water-glycol mix to heat and dry outside air, which is then directed to a windrow of finished compost to dry it prior to bagging.
The four aeration zones are 60-feet long and 20-feet wide; two of the zones are inside a fabric building. The aeration pipes were installed on-grade and spaced so that the windrow turner tires would track between the pipes. The surface of the compost pad is compacted marble aggregate from a nearby quarry. Phase I capital cost was $153,000, and was supported with a $28,325 grant from the USDA Rural Energy for America Program (REAP).
“The temperatures of new aerated windrows climbed to over 140°F within 48 hours with outside temperatures in the single digits, and it was obvious that aerating new batches with hot moist air drawn from negatively aerated windrows was reducing the time required to compost a batch,” notes Robert Foster, President of Foster Brothers Farm and VNAP. “As we continued to run the system last spring we were able to document a reduction from 4 months to 2 months in the time it takes to stabilize our compost, a fact that convinced us to expand the system.”
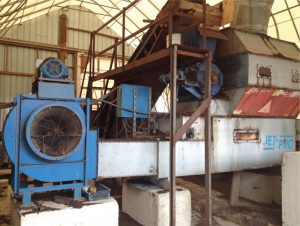
The heat recovery units have cut propane consumption for drying compost prior to bagging (dryer above) and #2 heating oil for building heating. Photo by Robert Spencer
Performance of the AGT system is monitored and recorded for airflow, water flow, oxygen levels, and temperatures. Key observations from Phase I include:
• Documented >131°F in less than 24 hours for a new windrow, compared to 5 to 7 days
• Reduced turning of windrows by 50 percent from 14 to 7 turns, reducing labor and use of diesel fuel
• Heated radiant floor in bagging building, reducing use of heating oil
• Reduced use of propane for compost drying
• Produced a peak hot water temperature of 162°F while circulating at 19 gallons/minute in February 2016
“The Foster Brothers have a long history of innovation, and their experience with composting shows Vermont farmers how this kind of equipment can cut labor and expense on composting manure and on-farm wastes,” says Alex DePillis with the Vermont Agency of Agriculture, Food & Markets.
Brian Jerose, founder and president of AGT, explains that start-up challenges in Phase I were limited to an undersized condensate trap to convey leachate and condensate from the four aeration zones to the composting facility’s storm water system. “We replaced those traps with larger diameter condensate drains installed beneath the windrows,” he says. “So for Phase II, we installed a new, larger condensate tank to serve the four new aeration zones, which then flows to a large detention pond that handles runoff from the 10-acre composting site.”
Because there was no Internet cable at the composting pad, AGT installed a temporary wireless “hot-spot” until a new fiber optic cable was installed. “We can operate our computer controlled systems as long as we have cell phone service at the site,” adds Jerose.
System Expansion
Based on the positive performance of Phase I, VNAP contracted with AGT to install an additional Hot Box with four new aeration zones, this time with no fabric building. That system came on line in November 2017. The primary function of Phase II is to expand aeration and heat recovery capacity. All four zones can operate in negative or recirculation aeration modes. Heated glycol/water mix is circulated to the first Hot Box 250-R unit to add more thermal energy to the building heating and drying applications. Additional composting aeration and heat recovery units could provide thermal energy to the newly built dairy barn.
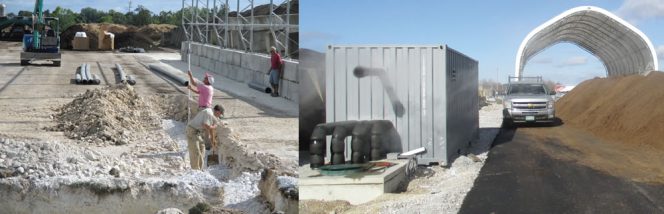
VNAP and AGT built the aeration pad and drainage system (left). The second Hot Box 250-R installed in 2017 has negative aeration, recirculation and heat recovery features (right). Photos by Brian Jerose
Food Waste Integration
VNAP is permitted as a medium-scale food waste composting facility by the Vermont Agency of Natural Resources, and can process up to 5,000 cubic yards/year of food waste. Jim Foster, Jr., Robert Foster’s nephew, was the lead site operator until he was killed in an accident on a nearby farm in September 2017.
Teresa Kuczynski is District Manager for the Addison County Solid Waste Management District (District) in Middlebury, which operates a transfer station and recycling facilities just a mile from VNAP. The District has an extensive program to develop and support organic materials recycling; provide education and training to generators; offer food scraps collection containers to haulers, businesses and residents; and offer grant writing assistance.
“We’ve collaborated with VNAP since 2002 to expand food residuals recycling, and hope to sustain this relationship since they are the only commercial composting facility in the District that is both willing to and has the capacity for accepting pre and postconsumer food scraps,” explains Kuczynski. “We know that the addition of postconsumer food scraps comes with unique challenges that don’t fit neatly into VNAP’s business plan. Despite this, they have shown a willingness to work together to overcome these obstacles, and that’s what makes them such a valuable partner.”
The District assisted VNAP and AGT with the Closed Loop Foundation grant application in 2016 to increase capacity to process food residuals, and to help food scraps generators comply with Vermont Act 148’s mandate that generators utilize an organics facility if it is located within 20 miles of their operation. “It was in our best interest to make sure VNAP had capacity to accept food waste, and we are pleased that the AGT system has increased that capacity to recycle food waste,” adds Kuczynski.
The District’s transfer station has a drop-off area for food scraps, with no fee for residents to use. To cover hauling and tipping fees, the District charges commercial generators $1.25 for 5 gallon containers, $11 for 35 gallon containers, and $15 for 48-gallon containers. “We have collected about 6 tons/year of food scraps in each of the five years we have been accepting them, ” she notes. “However, now that Act 148 is applying to smaller quantity food waste generators, we estimate the transfer station will receive 10 to 12 tons in 2018.”
Casella Waste Management sends a truck to the District’s transfer station to haul the food scraps to the VNAP composting facility. (VNAP picks up leaves and yard trimmings collected at the transfer station.) Food scraps processed at VNAP also come from 16 towns that utilize “fast trash“ drop-off sites where haulers park a truck for a few hours each week, setting out recycling and food scraps collection containers. Haulers also collect commercial food scraps directly from generators in the District, which are tipped at VNAP. (One innovative company, Draft Trash, uses a team of horses to collect trash, recyclables, and now food scraps in Middlebury.) According to Foster, about 350 tons of food residuals were composted last year at a tip fee of $35/ton.
To reduce contamination of VNAP’s compost from the plastic stickers on fruit and vegetables, the District started an innovative program in January 2018 to encourage residents to remove PLU stickers. With a grant from the High Meadows Fund, a special card was designed for residents to put PLU stickers on, and when it is full, the card can be redeemed for a bag of MOO DOO® compost.
Robert Spencer is a Contributing Editor to BioCycle. We extend our condolences to the Foster family, who note that Jim Foster “was admired and respected by many in the agricultural and composting industries, and was know for his energy, hard work and ingenuity.”