The Dirt Hugger composting facility utilizes heat recovered from active composting to warm its new office building and mechanics shop.
Nora Goldstein
BioCycle November/December 2018
Founded in 2010, Dirt Hugger operates a source separated organics composting facility in Dallesport, Washington. The site is a nine-acre parcel where owners Pierce Louis and Tyler Miller built a two-stage aerated composting operation, using a Green Mountain Technology aeration system. Dirt Hugger receives about 35,000 tons/year of residentially collected yard trimmings and food waste, commercial food waste (from restaurants, groceries, and schools), whole fruit waste, cherry sludge from fruit processing, beer waste and beer yeast waste (about 18,000 gallons/week), wood waste, and brush. Feedstocks come from generators throughout the Columbia River Gorge region, including the Portland, Oregon metro region.
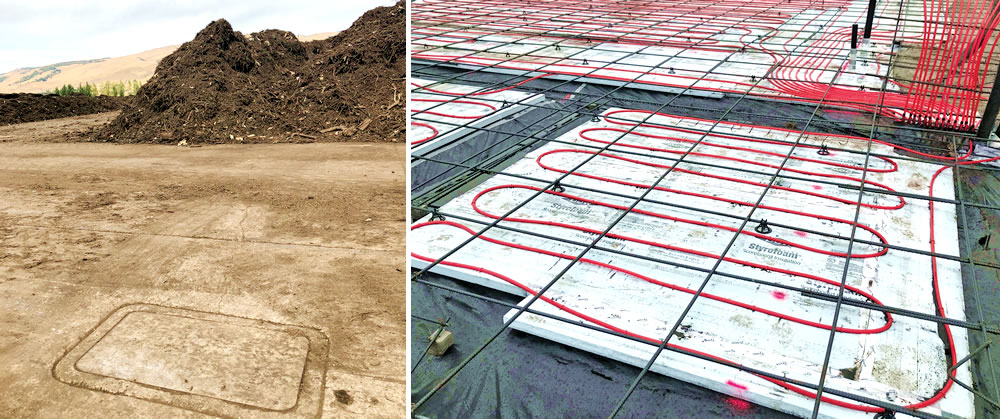
Dirt Hugger’s aeration pad (left) incorporates 5,000 feet of radiant PEX tubing that was placed during construction (right). Glycol, circulating through the tubing, is warmed by the heat generated by the composting process.
The Dirt Hugger site features a half-acre in-floor aeration system capable of positive/negative and reversing aeration. Active composting takes 14 days in an 8-foot high mass bed aerated static pile (ASP); curing is done in turned windrows on 4.5 acres of cement-stabilized soil.
“Four years ago, we placed 5,000 feet of radiant PEX tubing into our aeration pad when it was being built, knowing we would want to use the heat one day,” explains Pierce Louis. “The PEX tubing is right in the center of the 8-inch thick pad. We moved into our new office building in the spring — and it is entirely heated by compost! The aeration pad consistently produces 80°F to 100°F heat, which we then run into the building via radiant PEX tubing poured into our foundation and second story floors. We’ve had a few months of testing and so far it’s working great.”
The new building, which includes offices and a mechanics shop that uses about two-thirds of the building, has 2,900 sq. ft. of floor space. The largest fraction (25%) of a building’s energy consumption is from heating/cooling and this compost heat recovery system eliminates that cost, adds Louis. “This is a very low cost, low tech solution that is simple to install and simple to implement for anyone who has a composting facility and a building. The cost to install the tubing and related equipment — when we built the pad and then the building — was between $10,000 and $15,000.”
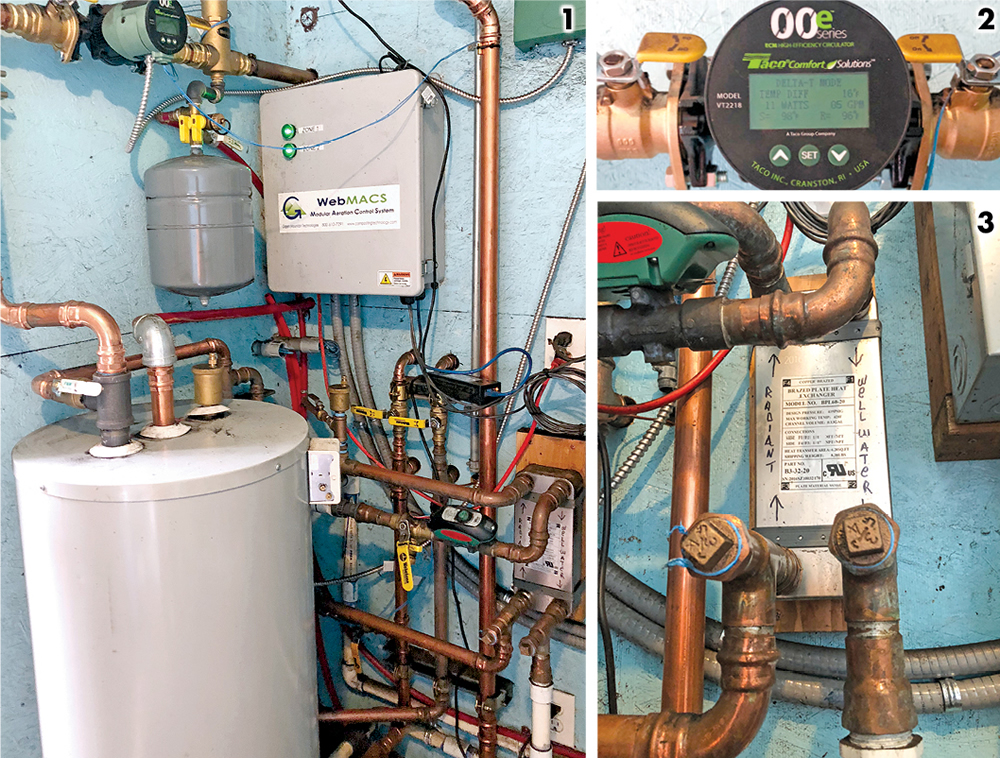
In the “heating loop” warmed glycol, from the aeration pad, circulates into the pump house (1) via two variable speed and energy efficient pumps (2). This building houses the heating/cooling exchange system. Here, warmed glycol preheats domestic hot water that is used in the office and is pumped into the adjacent office/shop building. The system features manual valves (3) to switch between the compost-warmed glycol and well-water cooled glycol.
Heat Recovery Mechanics
Dirt Hugger’s heat recovery and heating/cooling loops are illustrated in the diagram on facing page. The temperature of heat recovered from the aeration pad averages about 140°F, however with heat loss during the transfer, the average temperature coming into the building is 100°F. The heat recovery system has one primary heat loop, coming from the aeration pad going into the pump house, which is then split to preheat the hot water heater for domestic hot water, and also into the shop building to heat the shop and office floors.
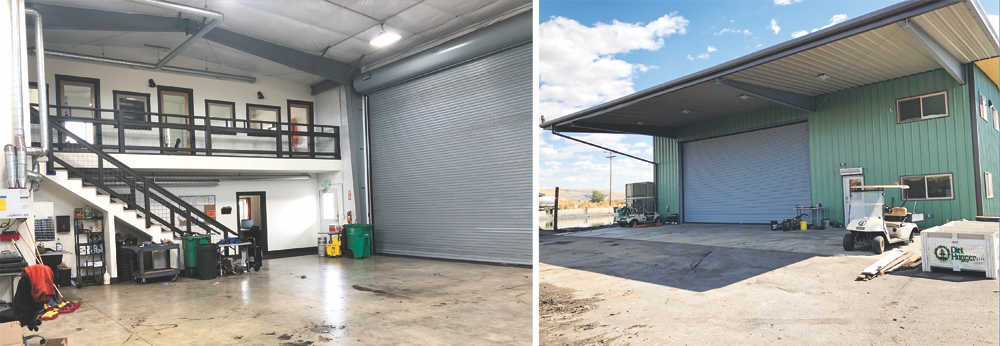
Warmed or cooled glycol circulates through the floors of Dirt Hugger’s office/shop building’s first and second stories (left). This radiant system extends into the covered pad outside the shop (right).
There is also a return loop from the hot water heater and from the shop building that goes back into the aeration pad. During the summer time, when the building requires cooling, manual valves are switched to close off the heat loop going to the shop building, and 45°F well water is run through a heat exchanger to cool the loop going into the shop building.
“Because domestic hot water at 100°F doesn’t meet code, we needed a hot water heater in the shop to bring it to 120°F,” explains Miller. “With the heat recovery from the aeration pad, our total cost to heat the building is equivalent to 40 watts/hour — less than an incandescent light bulb. This energy consumed is to run the two variable speed pumps in the heating loop. We estimate, conservatively, by capturing heat from the aeration pad we save about $300 to $350/month.”