Nora Goldstein
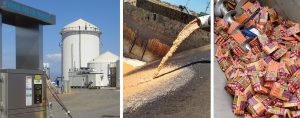
North State Rendering Co., Inc.’s (NSR) anaerobic digestion facility produces RNG for vehicle fuel (left). NSR has accepted clean high strength organics streams (middle) for a number of years, and recently installed a depackager to increase its ability to process packaged food waste (right).
While a graduate student at California State University, Chico, David Meyer was working on a research study to evaluate methods for optimizing biogas production from agricultural feedstocks and food waste diverted from landfills. Funded by a grant from the California Energy Commission, an impetus for the study were two new laws in the state — AB 1826 and SB 1383 — that essentially mandate food waste be recycled. In addition to testing feedstocks in laboratory-scale digester units, Meyer and his colleagues ran full-scale trials at an anaerobic digester (AD) in Oroville, California, that was built in 2012 by North State Rendering Co., Inc. (NSR).
After finishing his graduate degree in 2017, Meyer began working at NSR as the Biogas Plant Operator. Prior to building the digester, NSR disposed of its greasy wastewater in a series of evaporation ponds. As a renderer, the company already had permits in place to process fats, oils and grease (FOG) and food waste from kitchens, restaurants and food manufacturers. “The AD facility was designed to be a food waste digester and also handle excess wastewater and grease scrap generated by the rendering plant,” explains Meyer.
An article in BioCycle, “Anaerobic Digester Good Fit For Rendering Plant” (October 2014), describes the original design and start-up of the facility with capacity to process 100 to 140 tons/day of organic waste streams. Materials reception equipment included a liquid waste reception system with an auger and screen to separate out contaminants. Other feedstocks were unloaded into a hopper with an auger that moved material to a mixer that blended the feedstocks with digestate liquids to bring the solids content to a pumpable consistency — about 10 to 15 percent solids. The mix was then pumped through a macerator and into two heated tanks (40 feet in diameter and 24 feet high). The heated tanks are where the acid-forming phase of the biogas production process takes place. Next, feedstocks are pumped into the main digester tank (64-feet high).
“In the beginning, NSR received 10 to 20 tons/day of food waste,” says Meyer. “The receiving system couldn’t handle the level of contamination. To address the situation, a grind and pump system was installed. It was able to process the material, including the contaminants, and yield a substrate that could go through the digesters. But then the contaminants had to be dealt with on the back end.”
NSR shut down most of its rendering operations in 2016. The digester continued to process FOG from restaurants and other generators, high strength wastewater from food manufacturers, and some food waste. “Due to the California laws that require food waste diversion from landfills in California, NSR decided it would position its biogas facility to handle most of this area’s food waste,” he adds. “That includes all of Butte County, where Oroville is, as well as Yuba City to the South, and possibly into the Sacramento area. NSR primarily works with solid waste haulers that at the moment bring in high strength wastewaters. We still have two collection trucks that previously had been used by the rendering operation. We have a contract with a prison system to collect their food waste.”
Depackaging System
To service a wide range of food waste generators — including those with packaged feedstocks — NSR recognized that it would have to upgrade its preprocessing equipment to remove contamination ahead of the digester. The company looked at a range of depackaging systems, and ended up purchasing the TWISTER Universal Depackager manufactured by DRYCAKE. “The machine is able to take a wide variety of organic wastes without a lot of changeover of screens,” notes Meyer. “We also are attracted to the simplicity of the machine, especially as we only have 4 employees. The unit has 3 motors — 2 augers and the separator motor — and then a pump. So there are only 3 parts to actually maintain.”
Another selling point was the manufacturer’s willingness to customize the machine to fit the space available for it. “We already had a truck ramp and a receiving hopper pit,” he adds. “The TWISTER comes with its own receiving hopper. A crane was used to lower the unit into the pit. Trucks unload directly into the hopper, which is then fed into the depackager’s separation drum. We kept the existing hopper, which is also in the pit adjacent to the depackager, for the clean food waste. High strength wastewater is received in a separate liquid pit with a submersible chopper pump. The slurry coming out of the depackager feeds into the existing equipment that blends all substrates that flow into the digester. Essentially, the TWISTER is a pretreatment step to our existing receiving and processing system.”
The depackager was installed in July, and has been going through commissioning. It is rated at 10 tons/hour, but throughput varies based on the type of food waste being received. For example, if the feedstock is wetter and not much recycled digestate has to be added, throughput is about 15 tons/hour, explains Meyer. If it is drier, and more liquid needs to be added, then the depackager processes about 8 to 10 tons/hour. A digestate recirculation system calculates the amount of moisture needed to process packaged feedstocks.
Renewable Natural Gas
When the AD facility was originally built, NSR installed both a gas engine to generate power for its rendering operations and the biogas facility, and a biogas upgrading system to produce renewable natural gas (RNG). “The goal was to fuel NSR’s rendering fleet with RNG,” recalls Meyer. “A Unison biogas conditioning system was installed that removes the water and hydrogen sulfide and CO2 and then compresses the gas. We can use it for our trucks, and are seeking local fleets that can use the fuel as well. Currently, most of the biogas generated is flared.”
As the volume of packaged feedstocks increases, NSR will consider installing a sorting line to recover the packaging for recycling. As far as recycling the digestate, it is too low in solids at the moment to process through NSR’s screw press separator, so is treated in the evaporation ponds. As more food waste streams flow in, the company will explore digestate markets as well.
Editor’s Note: Mark Vanderbeken of DRYCAKE will give a presentation about North State Rendering Co., Inc.’s food waste preprocessing and AD system at BioCycle REFOR19.