Maarten van der Zee and Karin Molenveld
Part I of this article summarized the scope and research methods for a recent study at Wageningen University & Research in the Netherlands that analyzed the fate of compostable packaging in an industrial composting plant. The central aim of the study, “The fate of (compostable) plastic products in a full scale industrial organic waste treatment facility,” was to gather more empirical data on whether the disintegration rate of compostable products is sufficient to be compatible with current organic waste treatment practices in the Netherlands. In an industrial organic waste treatment trial, nine different compostable plastic products were tested: organic waste collection bags, plant pots, tea bags, coffee pads, coffee capsules, and fruit labels.
The full-scale trials were conducted at Valor in Sint Oedenrode, which annually processes about 45,000 metric tons of source separated municipal organic waste (GFT). As described in Part I, Valor runs a batch process in aerated “tunnels.” Duration of a single organic waste treatment cycle is 10 to 12 days. Materials goes through 2 cycles. The regular process does not have a separation step before the organic waste enters the composting unit, which means that all (plastic) products present in the organic waste will undergo the composting process. Sieving takes place between the first and second composting cycles.
Part II of this article discusses the results of the full-scale trials. It also includes findings from Wageningen University & Research’s detailed analysis of the composition of the current contamination of GFT by conventional plastics.
Compostable Plastic Products Disintegration
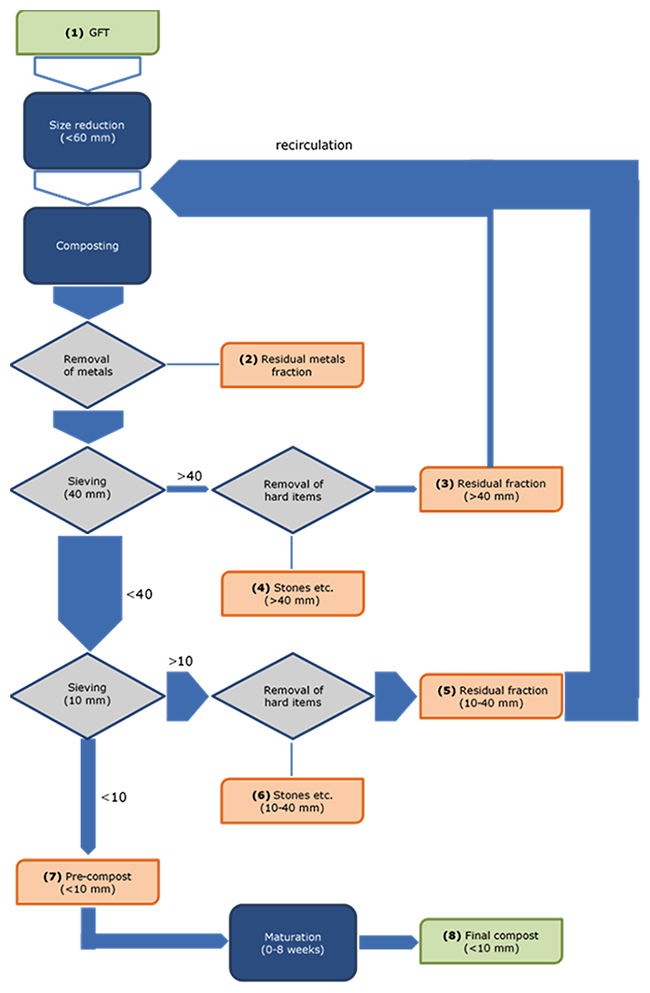
Figure 1. Flow diagram of the various fractions of the first waste treatment cycle. The width of the arrows represent the relative mass of the fractions
About 20% of the biowaste leaving the reactor after each composting cycle of 11 days (i.e., after the first or second cycles of 11 days) was sufficiently small (<10 mm) to be called compost (Fraction 7 in Figures 1 and 2). No compostable products were found in this fraction. The largest sieving fraction (10-40 mm), which was about 70% of the mass leaving the composting reactor (Fraction 5 in Figures 1 and 2), consisted of slowly disintegrating biowaste such as branches, leaves, peels, and paper, which is normally recirculated in the process and composted again.
In this fraction, about 1% of plastics were found, which consisted almost completely of conventional fossil based plastics. Also the coarse sieving fraction (i.e., bigger than 40 mm), which was about 10% of the mass leaving the composting reactor, consisted mainly of slowly disintegrating biowaste (Fraction 3 in Figures 1 and 2). The plastics found in this fraction also consisted mainly of conventional fossil plastics, although some residues of compostable biowaste collection bags were recovered.
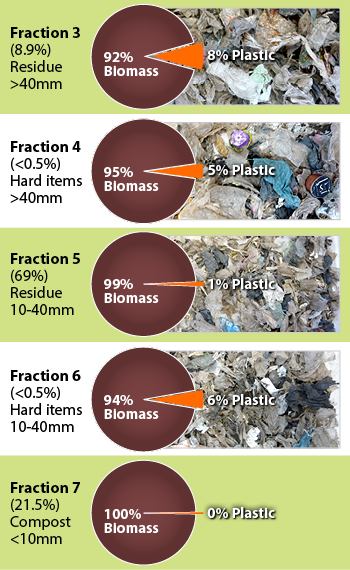
Figure 2. Composition of the various fractions obtained after the first waste treatment cycle. Left side: Amount of plastics and biomass present in the fraction. Right side: Pictures of the plastic fraction (See Annex 10 of the report for more detailed pictures)
Evaluation of the contents of the mesh bags (Part 2 of the 2-part phases of the research trials) showed that most products could be identified in the waste after the first cycle (11 days in the tunnel), except for product D (the full PLA plant pots), which could not be found in both duplicate mesh bags. The mechanical strength of the other products appeared to have decreased during the waste treatment process — this was not measured, but assessed manually.
The GFT in the mesh bags had undergone some degradation, but the origin of a substantial part was still recognizable. For example, the orange peel (opening photo above) and banana skin added as reference materials could also be identified in all recovered mesh bags. After the second composting cycle, and subsequent more detailed evaluation of the contents of the mesh bags, all selected test products showed either substantial fragmentation and loss of mechanical strength or could not be recovered at all.
Observations
A summary of the authors’ evaluation of the disintegration rate and fate of the selected compostable products in the process currently in practice for the treatment of GFT at Valor in Sint Oedenrode is schematically represented in Table 1. The assessment is based on all of our observations during this full scale trial (including the experiences with the mesh bags), and explained in more detail as follows:
Disintegration rate: All selected test products scored positive with regard to their disintegration rate because they all showed substantial fragmentation and loss of mechanical strength within the two composting cycles (Table 1). The full PLA products (product D and product J) score the highest (+++) as they could not be found in the waste anymore after just one composting cycle of 11 days, which is significantly faster than the orange peel and banana skin reference products and most other GFT.
Products C, E, F and H score a little lower (++), because some fragments — although difficult to distinguish from the compost — could still be identified upon close examination of the content of the mesh bags after two cycles of composting. Products A, B and G score the lowest (+) of the selected test objects. With these products, substantial fragmentation and loss of mechanical strength were observed within two composting cycles of 11 days, but fragments were still recognizable as (deteriorated) plastics.
Risk of ending up in discarded residue fractions: Even though the scores of the disintegration rate vary between products, the risk of ending up in discarded residue fractions is considered low for all tested compostable products. Because the Valor facility recirculates the 10 mm to 40 mm residue fraction in most cases, and also recirculates the >40 mm fraction a number of times, it is concluded that the true residence time will be sufficient for complete disintegration so the tested products will not significantly contribute to an increase in residue to be discarded.
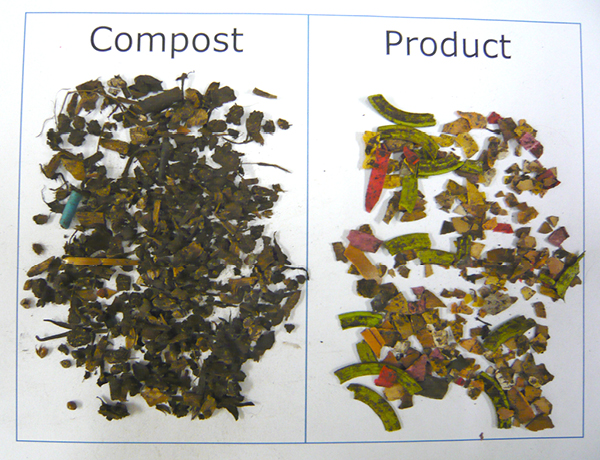
Coffee capsule (Product G) and compost recovered from the mesh bags, 2-4 mm fraction
Risk of visual contamination of compost: Due to the bright colors used in the coffee capsules (Product G), even tiny fragments are conspicuous and recognizable in the generally dark brown compost. Fragments of partially disintegrated coffee capsules are likely to pass the 10 mm sieve in the Valor process and thus may end up in the compost fraction. Based on the fact that the product is certified according to EN 13432, it is likely that degradation of the material will continue during maturation and use of the compost to complete biodegradation. But if the compost is used shortly after its production, which is regularly the case at Valor, the brightly colored particles of product G will contribute to the (visible) contamination of the compost.
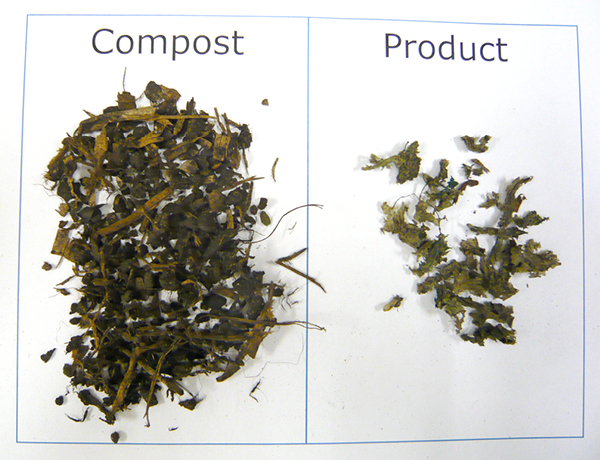
GFT collection bag (Product A) and compost recovered from the mesh bags, 2-4 mm fraction
For all other tested products, the risk of visual contamination of the compost is considered low because in case disintegrated fragments should pass the 10 mm sieve, they will not be easily recognized as plastic contaminants. In the trial, dedicated attention and a trained eye were needed to distinguish the disintegrated compostable products from other organic matter in the compost due to their similar shape and color.
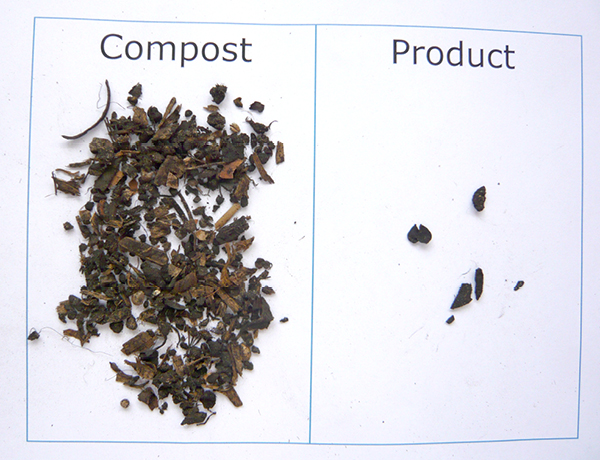
Plant pot (Product C) and compost recovered from the mesh bags, 2-4 mm fraction
Extrapolating the findings to other processes operated in the Netherlands, it is expected that in some waste treatment facilities, some of the selected compostable products will end up in fractions that are discarded. This will depend, however, on the pretreatment processes installed, the residence time in the composting phase, the turning frequency, and the shear it encounters before and during post treatment.
Conclusions
Based on all observations in this study, the researchers conclude that compostable products that comply with the requirements in European standard EN 13432 disintegrate fast enough in Dutch GFT waste treatment systems. Nevertheless, the presence of conventional (noncompostable) plastics in GFT is a real problem for the Dutch biowaste treatment sector and needs to be solved.
Access the full report: “The fate of (compostable) plastic products in a full scale industrial organic waste treatment facility.”
Maarten van der Zee, PhD, is a senior scientist and project manager at Wageningen Food and Biobased Research. He has been working for more than 25 years in the field of biodegradable and/or biobased products. Karin Molenveld is a senior scientist and expertise leader at Wageningen Food and Biobased Research. She focuses on developing new biobased materials and products examining specific end-of-life options for these products including organic, mechanical and chemical recycling