An analysis was performed in Italy to better understand the interaction of compostable bags with hydropulping pretreatment systems in wet AD facilities. Results show further recovery potential for the residues, with optimization of overall system performance.
Christian Garaffa and Rhodes Yepsen
BioCycle September 2012, Vol. 53, No. 9, p. 37
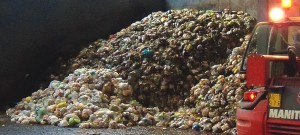
The wet AD plant in Castelleone, Italy, receives about 22,000 tons/year of source separated food waste, collected in compostable bags from households in surrounding towns.
This article addresses both the quality of residential organics being collected, as well as the interaction of the compostable bag with pretreatment systems. In the Italian study presented, compostable bags help maximize organics recycling and facilitate recovery of residues that otherwise would be disposed through landfilling or incineration. An analysis was performed to better understand the interaction of compostable bags with hydropulping pretreatment systems in wet AD facilities. The analysis showed interesting results about the composition of the residues generated in those systems, indicating further organics recovery potential with an optimization of the overall performance of the system.
European Guidelines
The European standard EN 13432 aims “to determine the compostability and anaerobic treatability of packaging and packaging materials.” Packaging that complies with EN 13432 can be recovered by organics recycling, i.e., composting and AD. For nonpackaging plastic items the exact same characteristics are defined in the European Standard EN 14995. To comply with both standards, products must show enough biodegradability, disintegratability and absence of ecotoxic effects. Compostable plastic bags for collection of biowaste are one of the most successful applications of EN 13432 certified materials.
The behavior of compostable plastics in anaerobic environments varies depending on temperature (i.e. thermophilic/mesophilic), solids retention time, composition of the material, shape and thickness of the compostable items being tested. EN 13432 and EN 14995 provide guidance on how to measure anaerobic degradation as a further characterization of the tested material. No pass level is fixed, however, because this is considered optional information in the compliance process. If disintegration and biodegradation are not complete during the fermentation process, they will be completed in the subsequent aerobic composting stage.
Different AD technologies need different configurations of the pretreatment stage to properly condition and feed the substrate into the digester. Table 1 shows some of the more common methods found in industrial AD plants treating biowaste.
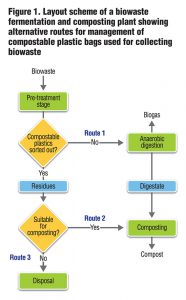
Figure 1. Layout scheme of a biowaste fermentation and composting plant showing alternative routes for management of compostable plastic bags used for collecting biowaste
The bags or fragments of them can entirely or partially follow three different paths in an anaerobic digestion plant:
Route 1: Bioplastic fragments fed into the digester along with the biowaste. After digestion, the digestate with possible remains of compostable plastics is composted for aerobic stabilization and mature compost production.
Route 2: Bioplastic fragments sorted out during the pretreatment stage, skipping the digestion stage and rejoining the aerobic composting stage of the digestate.
Route 3: Bioplastic fragments sorted out during the pretreatment stage and sent to disposal because of high contamination of the pretreatment residues by noncompostable materials (e.g. conventional plastics) or because of the lack of a final aerobic stage for compost production.
Route 1 allows for maximum utilization of compostable plastic bags, and additional organic material sticking to them, both in terms of energy and material recovery. Route 2 allows for maximum material recovery of the bags and other pretreatment residues of biogenic origin. Route 3 represents a nonoptimal situation caused by either external factors like the presence of noncompostable plastic contamination impeding optimal material recovery of the pretreatment residues or internal factors like the absence of a composting stage for the stabilization of the digestate.
Switching from Route 3 to Route 1 or Route 2 leads to a higher efficiency in capture of energy and material resources, but is only possible with minimal contamination rates of the input feedstocks. Certified compostable bags help in reducing this contamination (the bag itself is compostable, and residents using them are conscientious about leaving out other plastics) and allow for maximum advantage of the biowaste potential, including the residues normally generated by the pretreatment processes.
Research Study In Italy
Wet AD has traditionally been used for treating sewage sludge (biosolids) at municipal wastewater treatment facilities or by farmers for processing animal manures and more recently also energy crops (e.g. silage). Wet AD works with continuous feeding systems and pumpable substrates that usually must have total solids (TS) content between 12 and 15 percent and particle size less than a half-inch (<10 mm). The substrate preparation and conditioning method is a key factor for the best capture of the substrate’s energetic potential. One option is to add liquid to the substrate to increase available surface area of the organic matter brought into suspension for subsequent biodegradation and methane production. A well-established pretreatment system to achieve this is the hydropulper, adapted from the paper industry (also called a waste pulper).
This study examines a wet AD plant codigesting agricultural waste and municipal source separated food waste. The facility is owned and run
by Biofor Energia Srl, based in Castelleone, Italy. The company is a joint venture between the publicly owned local waste management company SCRP SpA, and three local farmers that deliver the agricultural waste and take back the digestate to land apply on their farms. The plant was designed and built by Biotec Sistemi S.r.l., a company partner and licensee of BTA International. The concept is based on the BTA® Hydromechanical Pretreatment and BTA’s anaerobic digestion concept for agricultural biogas plants.
The facility has a capacity of 110,200 tons/year (tpy). In 2011, it treated animal manure (75,000 tpy), source separated biowaste (22,000 tpy), packaged food waste (6,600 tpy) and silage (6,600 tpy). Food waste is collected in compostable bags from the households of the surrounding towns and delivered to the waste reception area at the facility. From there the bags are taken by a front-end loader and placed on a conveyor belt that feeds the BTA waste pulper, which is already filled with process water. No shredding or bag opening is necessary as the bags get ripped open during the pulping process. The pulped waste is separated into fractions according to the natural buoyancy and sedimentation of the different materials. Solid organic components are reduced to fibers by shearing forces and brought into suspension.
Fate Of Compostable Bags
One relevant question is where the compostable bags end up during the pretreatment step. How much of the compostable plastic reaches the digester and how much is separated, and in which fraction? To better understand the fate of compostable bags during the pretreatment process of this specific plant and technology, an analysis was performed in December 2011 to assess and quantify the presence of compostable plastics in the three fractions generated by the waste pulper, and additionally in the sand separated by the grit removal system.
First, a waste composition analysis was performed on a load of bagged food waste before the bags were added to the pulper to assess its quality in terms of presence of noncompostable contaminants (mainly conventional plastic bags). Three samples taken randomly from the batch had a total weight of 608 lbs (275.8 Kg) and showed an average contamination rate 1.3 percent (S = 0.52). The three samples included a total of 126 bags of which 5 where made of noncompostable plastic. The remaining 121 bags where certified compostable according to EN 13432.
Out of the 121 compostable bags, 67 were dedicated bags for food waste collection (manufactured for this specific purpose) and 54 were compostable shopping bags reused by households for collecting their food scraps. The significant presence of compostable shopping bags can be explained by the fact that since January 2011, Italy instituted a noncompostable plastic carrier bag ban, which is leading to a progressive reduction in use of noncompostable plastic shopping bags in retail stores and a significant increase in use of certified compostable shopping bags for collecting food scraps (see “Plastic Bag Ban And Residential SSO Diversion,” August 2012).
The second step of the investigation measured the presence and relative amount of compostable plastics in the outputs from the pretreatment stage — the heavy fraction from the pulper; the fine sand fraction produced by the grit removal; the light fraction skimmed off by the rake on the pulper and sampled after dewatering by the screw press; and the organic suspension, sampled after grit removal (before the pasteurization stage).
Samples of each fraction were taken and analyzed in the laboratory to quantify the relative amount of compostable plastics in each fraction. They were processed as follows: Oven drying to constant weight at 58°C; Manual separation of clearly distinguishable plastic fragments (if any); Extraction in chloroform (compostable polyesters are solubilized in chloroform whereas traditional noncompostable polyolefins are not); FT-IR spectroscopy analysis on the extracted fraction to assess the presence of compostable polyesters.
Results of the FT-IR analysis — after drying and chloroform extraction — showed the following:
Heavy fraction: Fingerprint of edible oils and no peaks associated to compostable polyesters.
Fine sand fraction: No peaks associated to compostable polyesters.
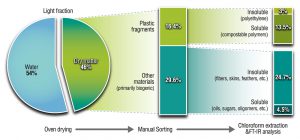
Figure 3. Amounts (percent by weight) in light fraction after dewatering, manual sorting and chloroform extraction with FT-IR analysis
Organic suspension, sampled after grit removal (before hygienization): Fingerprint of edible oils and no peaks associated to compostable polyesters
The most relevant conclusions with specific reference to the final destination of compostable plastics in this pretreatment system are:
• No residues of compostable polyesters have been found in the organic suspension going into the digester (nor in the heavy and sand fractions).
• All compostable plastic bag residues ended up in the light fraction separated by the BTA® Waste Pulper.
• Compostable plastic bag fragments constituted 13.5 percent of the total light fraction, after dewatering by the screw press.
• Share of polyethylene in the light fraction was low (3 percent, due to the high quality of the collected feedstock treated by the waste pulper).
• Composition of the remaining part of the light fraction appears to be made mostly of biogenic materials (fibres, skins, feathers, woody materials).
• Further research is needed to assess the actual compostability of the light fraction as an alternative recovery option compared to disposal or thermal recovery, but 97 percent is potentially recoverable.
Basically this study indicates that all of the compostable bags are raked off the BTA® Waste Pulper. With low contamination inputs, the resulting fraction could be sent to composting (Route 2 in Figure 1), rather than to disposal (Route 3 in Figure 1), improving the overall recycling rate. This study shows how a process that is rejecting the bags along with a significant amount of biogenic material can be optimized by sending the residues it generates to composting.
Christian Garaffa is Marketing Manager, Source Separation and Recycling, for Novamont, SpA, and works with European composting associations and waste consulting companies managing projects with local authorities, private and public waste management companies, retailers and other stakeholders (christian.garaffa@novamont.com). Rhodes Yepsen is Marketing Manager for Novamont North America, Inc. (rhodes.yepsen@novamont.com).