Katrina Mendrey
BioCycle August 2013, Vol. 54, No. 8, p. 32
Composting isn’t new to the Washington State Department of Corrections (Washington DOC). Since 2004, the Olympic Corrections Center in Forks, Washington has been composting its food waste and biosolids. The program has since expanded and became part of the Sustainability in Prisons Project (SPP), a broader initiative by Washington DOC to make the state’s prisons more sustainable and to save money (see sidebar). The missions and goals of the programs complement each other, with both focusing on sustainability at Washington prisons.
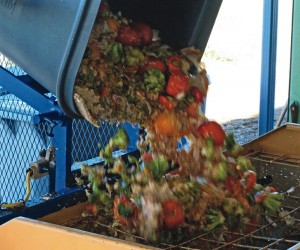
A cart lifter is used to unload food waste into the hopper of the mixer of a new in-vessel composter installed at Cedar Creek Corrections Center.
Washington DOC estimates that 1 to 1.5 lbs/day/offender of food waste are generated. Composting programs receive both pre and postconsumer food scraps. Kitchens typically utilize 90-gallon totes to collect the organics, filling them half-way due to weight considerations. Some composting facilities are equipped with a tote lifter to empty the containers.
The first facilities to begin composting were Olympic, and Larch Corrections Center, both in remote areas that had been former Washington State Department of Natural Resources’ forest camps. Savings from transportation costs and avoided tipping fees made the case for developing on-site processing. For example, at Stafford Creek Corrections Center in Aberdeen, facility managers estimate a savings of $30,000 annually in avoided tipping fees by composting on-site. In 2011, 790 tons of organic residuals were composted at Stafford Creek resulting in 104 cubic yards of finely screened compost that is used to amend soils at the facility’s gardens and greenhouses.
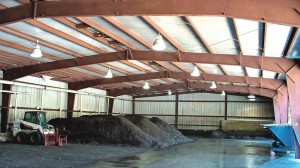
Olympic Corrections Center utilizes aerated static piles to compost biosolids, food waste and amendment.
Job Training For Offenders
As composting along with the SPP program has gained momentum, so has the perception that cost savings aren’t the only benefit. “The program actually started as a way to save money, but I just think it is the right thing to do, and others at Washington DOC feel the same way,” says Heinitz. In addition to waste reduction, the programs provide jobs for offenders while they are incarcerated. Each facility typically employs 3 to 6 offenders who receive $0.42/hour, and gain valuable experience that can be applied outside the prison walls. For example, at Stafford Creek, four offenders are responsible for composting the food waste and yard trimmings produced at the facility.
Jason, an offender at Washington Corrections Center in Shelton, applied for a composting position because he wanted something to do. “When I started I liked the repetition of this job,” he explains. “Now it’s about watching how we can turn something like wasted food into soil.” This spring Jason planted a garden using the compost. The gardens at Washington Corrections Center produce about 15,000 pounds of food annually. Half is used in the prison kitchen while the remainder is sent to a local food bank. Staff encourages offenders to consider a career in composting when they are released. “We tell them, this is the wave out there, you can get a job in this,” says Don Carlstad, a plant manager at Washington Corrections Center.
Compost education reaches beyond the offenders directly involved in daily operations. Waste reduction is a focus of the SPP. Offenders sort recyclables, and they are involved in ensuring food waste is free of contamination in the kitchen. Most facilities include processes for separating liquids and solids. Some have even stopped serving soup to reduce liquids in food waste.
Involving offenders in the work also benefits the compost program, points out Heinitz. “They have been instrumental in solving many of the problems encountered early on in our composting venture. For example, at one facility that installed a drum, it took about 6 to 9 months to get the process down. During that time, offenders, who were there every day, would see what was going on and come up with ideas of their own to fix the situation. Some of the challenges had to do with moisture content and maintaining the necessary level of heat.” These lessons learned from earlier operations have assisted other facilities in getting programs started.
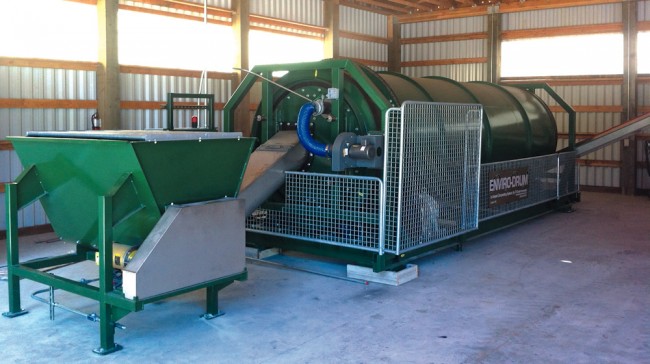
Larch Corrections Center is located in a remote area at a former forest camp. Savings from transportation costs and avoided tipping fees made the case for developing on-site composting capacity (Wright Environmental system shown above).
Since starting with the agency in 2007, Heinitz has managed the design and permitting of four composting operations. “Buy in from supervisors, offenders and facility managers is a huge asset to the composting program,” he notes. “Our biggest challenges are securing funding and permitting facilities.” The permitting can be particularly frustrating because of the unique aspects of a correctional composting operation. Washington DOC’s composting programs cannot market, sell or distribute their products nor do they currently accept outside feedstocks. In addition most operations produce less than 2,000 cubic yards/year of compost. Despite this, some counties still require prisons to obtain permits that are applicable to larger private facilities.
Facility Expansion
Such hurdles, however, have not limited growth of the program. In June 2013, Cedar Creek expanded to a larger facility with capacity to process 2 to 3 tons/day of materials; it will begin processing 500 to 700 lbs/week biosolids soon. Cedar Creek was designed with excess capacity to accommodate noncorrectional government facilities in the area, such as the state capitol campus buildings. The Washington Corrections Center for Women in Purdy also recently completed construction of a new facility that is located inside an existing building. The county permitting agency required that all composting operations — both active and curing — be indoors.
Both Cedar Creek and Washington Corrections Center for Women installed DTE’s EnviroDrum Model 6-20, which is designed for smaller facilities where space is limited and proximity to the public requires more sophisticated odor control. The drums are 6 feet in diameter and 20-feet long. The 5-HP motor is capable of 30 rotations per hour. Odor is managed by maintaining negative air pressure inside the drum with a blower that pulls process air through the rear of the drum. This air is fully contained as it moves through the system to an external biofilter consisting of two feet of finished compost atop gravel.
A mixing unit that feeds the drum has a scale. Food waste is loaded into the hopper of the mixer and weighed. The appropriate amount of bulking agent is added based on a formula that factors in the type of food waste received. At Washington Corrections, a tote lifter will empty directly into the hopper of the mixer. At Cedar Creek, which is incorporating biosolids along with the food waste, the wastewater treatment plant is about 200 yards from the composting site, so biosolids will be transported, likely using a fork lift, and added to the compost drum weekly. Wood chips are used as the bulking agent.
Typically, material takes 3 to 5 days to pass through the drum. Active compost unloaded from the drum at Cedar Creek is conveyed to a curing area consisting of three bays, where it stays for about two to three weeks before being ready to use. “This is a much shorter timeframe for compost production,” notes Heinitz. “At Olympic Corrections Center, which uses aerated static piles, the first phase of active composting is 3 to 4 weeks, during which material is mixed 3 to 4 times. Then it cures for another 4 to 6 weeks. The drums reduce the timeframe by about half.”
Other features of the drum include a programmable logic controller (PLC) to allow for automated loading, and monitoring systems that track internal temperature and moisture. These readings can be accessed online allowing for remote management of the system. Such monitoring also can demonstrate that Process to Further Reduce Pathogens (PFRP) can be met inside the drum, further reducing the space requirements of a composting operation. “One of our goals in using this system is to demonstrate to the Washington Department of Ecology we can meet pathogen reduction requirements inside the vessel,” says Heinitz of the new system.
Heinitz hopes that the composting facility design/footprint utilized at Cedar Creek will allow for expansion of additional on-site composting operations, not just at corrections facilities, but other similar-sized institutions. “If we can show that composting can be achieved using less space, then maybe we can encourage others to start similar programs resulting in greater waste reduction for the community as a whole,” he concludes.
At the moment, however, his goals for the program are focused on opening composting operations to accept feedstocks from communities outside the prison system including schools and local governments. For example, Washington Corrections received a grant from Mason County that covered half of the capital costs with the intent that some of the county’s source separated organics would be processed there. The permit for that operation was written to allow these off-site materials to be composted at the corrections center. Such a service would provide these organizations with the same cost benefit as the prisons, and the community at large with the environmental benefit of waste reduction.
Taking the vision a step further, Heinitz is also exploring options for distributing the compost product outside the prison fences to help offset costs. This would require a change in current requirements that compost can only be used on-site where it is made. In the meantime, he and his crew of composters will continue to perfect existing operations, producing high-quality compost for use on facility grounds and in other SPP projects.
Katrina Mendrey recently received her Master’s in Soil Science from the University of Washington.