Facility in London, Ontario is ramping up to process 71,500 tons/year of food industry residuals. Digestate will be heat-dried into fertilizer products.
Peter Gorrie
BioCycle September 2013, Vol. 54, No. 9, p. 56
A new anaerobic digester opening in London, Ontario — owned and operated by Harvest Power based in Waltham, Massachusetts — runs solely on a challenging mix of organic wastes from food processors, grocery stores, restaurants and other sources in the industrial, commercial and institutional sector. The London facility is the company’s most recent project to come online. “I view energy and organic fertilizer production from food waste as the logical next step for the industry,” says Paul Sellew, Harvest’s CEO.
Paul McMenemy, a former Wall Street energy investment banker, oversees the London facility. McMenemy, an Ontario native, teamed up with Sellew, an entrepreneur in the organics recycling industry, to create Harvest Power and develop anaerobic digesters. With backing from Kleiner Perkins Caufield and Byers, True North Venture Partners, Waste Management Inc., Generation Investment Management, Germany’s Munich Venture Partners and other prominent investors, the company has expanded rapidly. After five years, it is running 40 facilities in 13 states and two Canadian provinces (many acquired through acquisitions), employing nearly 600 people.
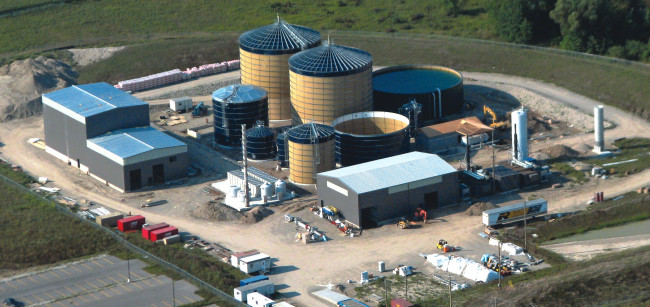
Harvest Power’s new anaerobic digester in London, Ontario includes three holding tanks for incoming feedstocks, a thermophilic acidification reactor that heats substrates to 131°F where they are held for three days and two mesophilic digesters.
Anaerobic digestion is a growing component of the business. Harvest coined the term “Energy Garden” for its facilities using this technology. The name is intended to “introduce the general public to the concept of growing energy and dovetails with a by-product of anaerobic digestion, natural fertilizers,” he explains. In Richmond, British Colombia, on Canada’s West Coast, the company operates a commercial-scale high-solids anaerobic digester that uses a batch two-stage technology (supplied by Gicon) to process mixed yard trimmings and food scraps, with a solids content of up to 40 percent. Feedstock is sourced from the residential and commercial sectors. It has been operating at full scale since May 2013. Another Energy Garden under construction in central Florida, will, like the London facility, process low-solids materials such as food scraps.
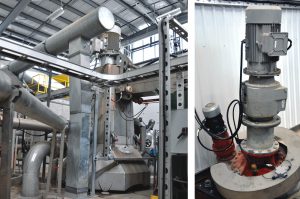
A DODA bioseparator processes all incoming liquids — packaged and unpackaged — except for the fats, oils and greases. The unit has a wet-feed, inline contaminant removal system with a bag breaker (right). It uses mechanical paddles to sort and remove inorganic materials.
London Operations
The 10-acre London site stood out as a location for the Ontario venture. A local company, Stormfisher Biogas, founded by business school graduates from London’s University of Western Ontario, had begun to develop an anaerobic digestion facility there. Greenhouse Gas Services, based in Virginia, acquired the project in 2009, but backed out because it lacked financing. Harvest acquired the project in 2010. “It was perfect for us,” says McMenemy, now the company’s regional vice-president in Ontario. The facility is completing commissioning and is scheduled to go into full production this fall. The project was designed and built by Ovivo, a unit of Montreal-based GLV group.
Located in an industrial and agricultural area, the site has only a few residential neighbors within a mile, and nearly all participate in a Public Liaison Committee that receives regular updates about the project. Facility development has proceeded without controversy. Connections to the electricity grid and natural gas pipeline network are at the property line. Stormfisher had acquired all the necessary permits and was approved for the Ontario government’s original feed-in tariff, the Renewable Energy Standard Offer Program (or RESOP). Under 20-year contracts, it pays a premium price for electricity supplied to the grid from wind, water, solar, biogas and other renewable sources.
At the start, the facility will take in more than 71,500 tons/year of food industry residuals. In addition to the electricity, heat energy will be captured for warming the digesters and other on-site uses. Dry digestate will be shipped offsite to be processed and pelletized into fertilizer for the residential market, at a rate of about 5,200 tons/year.
The decision to handle only food industry organic wastes makes life both easier and more complicated for McMenemy and his seven-member staff. On one hand, the facility doesn’t need to worry about the culture and behavior shift required with source separated organics collected from homes. On the other hand, the complex variety of materials trucked to the site from about a 90-mile radius — including fruit and vegetable scraps, grains, fish, meat, bones, fats, grease, oils and dairy by-products — make it crucial that the feedstocks be carefully blended to ensure the correct pH and energy levels in the digesters. While biosolids and manure have less energy content, at least “you know what you’ve got,” McMenemy notes. But with food industry residues, “getting the recipe right is difficult.”
The existing digester tanks could handle 25 to 30 percent more feedstock, and the site has permitted space for enough additional digester capacity to accommodate up to 200,000 tons annually. However, expansion is some time off, he adds, as Harvest must ensure it has an adequate and dependable supply of feedstock. In addition, the RESOP contract limits the facility to 3 MW of electricity generation and, because of capacity limitations, the grid currently won’t accept a larger amount. That means any additional methane generated would have to be purified into natural gas. At its current low price, that’s not an attractive proposition.
Trucks enter an indoor unloading area, and outer doors close before drivers are allowed to tip their loads into a below ground bunker. Then, they must wait 20 minutes for a complete air exchange before the doors are opened and they can depart. Air from this area and the rest of the facility is treated through a BioRem Inc. biofilter before it’s released into the atmosphere.
Apart from loads of fats, oils and greases (FOG), the feedstock in the bunker is blended with process liquids and pumped into a DODA bioseparator. The separator has a wet-feed, inline contaminant removal system that uses mechanical paddles to sort and remove inorganic materials such as plastic bags and retail packaging. These materials are recycled if possible or sent to landfill, while the clean slurry of feedstock continues through the rest of the process.
First, the slurry goes into one of three holding tanks. FOG, having bypassed the bioseparator, goes directly to one of the tanks. The remainder goes into the other two. From there, they’re sent to a tank called the Thermophilic Acidification Reactor (TAR), where they’re warmed with waste heat from the engines to 131°F and held for three days. Next, material flows from the TAR into the two digester tanks operated at mesophilic temperatures (around 100°F). Retention time in this phase is six weeks. When it’s complete, digestate is transferred to a bubble tank.
The biogas fuels two 1.425 MW GE Jenbacher combined heat and power (CHP) units, sized to produce the maximum amount of electricity the facility is permitted to add to the provincial grid. The digestate is pumped from the bottom of the bubble tank and run through a centrifuge to separate the solids and liquids. The solid portion or cake, now 20 to 25 percent solids, is dried to 92 percent solids using heat from the CHP unit. The drying process destroys any remaining pathogens in the material, which will then be pelletized to make three grades of fertilizer. The products will be bagged and sold through lawn and garden shops, under the Harvest brand name.
For now, the liquid portion of the digestate goes through an on-site water treatment plant before being discharged into London’s sewage system. However, additional options are being investigated for a high quality liquid organic fertilizer.
Fertilizer sales are expected to account for about 10 percent of the London facility’s income, McMenemy says. About half will come from electricity generation and 40 percent from tipping fees, which are now comparable to those for landfilling.
Peter Gorrie is a Contributing Editor to BioCycle.