Mississippi Topsoils, Inc. in Minnesota has built its expertise and product markets around composting poultry solids and woody materials.
Dan Emerson
BioCycle May 2015
In 1998, Brad Matuska and Mathias Miller founded Mississippi Topsoils, Inc., based near Cold Spring, Minnesota, to compost solids from GNP Company, a nearby poultry processor. With a startup investment of about $500,000, they installed a NaturTech in-vessel system on a 5-acre site. Operations began in 1999. The in-vessel system “provided the level of control we needed over variables like the weather, dust and odors,” Matuska explains. The system has 12 composting vessels made from modified (sealed), steel roll-off containers, each with 2 tons/day of capacity, and three biofilters. Mississippi Topsoils has found success marketing its Soil Essentials line of quality soil amendments to all types of growers in a five-state area.
Early on, the founders made a decision to not accept yard trimmings to avoid herbicide-contaminated grass, and because leaves and grass “just blocked up our mixer and composting system when mixed with the solids,” Matuska recalls. Also, the area has a number of other processors that handle yard trimmings, including the City of St. Cloud, Tri-County Organics, which does source separated organics, and surrounding cities including Sartell, Sauk Rapids and St. Joseph.
Mississippi Topsoils composted 5,213 tons of material in 2013, and 5,500 tons last year, a little more than half of its annual permitted capacity of 9,360 tons. The solids from GNP’s wastewater treatment plant are about 12 percent solids. Amendments are placed in an Oswalt 525 truck-mounted vertical mixer, which is driven to GNP to collect the solids several times per week. Wood chips, along with overs from the screening process, are used as amendments.
Before opening for business, Matuska conducted pilots to determine how the solids would compost. “But, until you get into full-blown production, you don’t know how it’s going to behave,” he notes. He also did growth trials in an on-site garden, comparing the results of applying the Mississippi Topsoils’ product on one plot, yard trimmings compost on a second, and nothing on a third. “We were blown away by how well it performed,” Matuska recalls, adding that the results were confirmed by customers, some of whom shared photos of “giant tomato plants.”
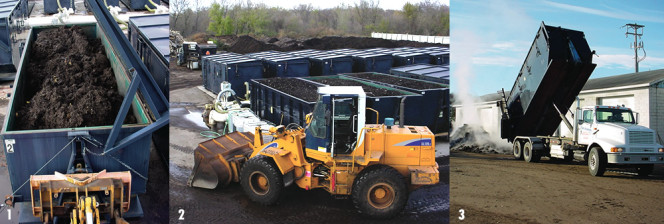
Amended poultry solids are loaded into NaturTech composting vessels (1) for negatively aerated composting. Mississippi Topsoils has 12 vessels (2). After 2 to 3 weeks, a vessel is unloaded (3) and material is further composted, first inside a building and finally in windrows. Photos courtesy of Mississippi Topsoils
Finetuning Operations
An early challenge was achieving the right carbon-to-nitrogen ratio. “While there’s a ton of immediately available, soluble nitrogen in the poultry solids, there wasn’t a lot of carbon immediately available in the wood waste, even the sawdust,” he explains. “Much of that carbon is locked up in cellulose and lignin in the wood material — inaccessible to the microbial action of composting because it’s buried inside. We learned we had to run the aeration system at a higher than normal volume of air so we could blow off some of the excess nitrogen, to bring it into balance.”
The entire process of converting the poultry solids to compost takes about a year. It starts with two to three weeks of in-vessel composting under aeration, which is controlled by continuous temperature monitoring. After the in-vessel composting phase, the curing phase begins in a 30- by 100-foot concrete building for about six weeks. Then the material is piled in outdoor windrows about 200 feet long and 15 feet wide, for 8 to 10 months of final curing. The final step is screening to three-eighth-inch using a MultiTek trommel. Loaders are used for moving materials and windrow construction and management.
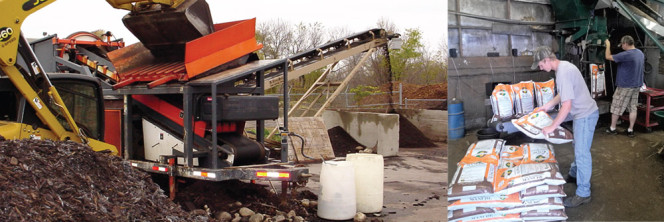
Compost is screened to three-eighth inch using a trommel screen (above). Compost is sold in 1-cubic foot bags (left), which has helped Mississippi Topsoils market its products to independent retailers. Photos courtesy of Mississippi Topsoils
Building markets
Learning to compost on a large scale has not been the most challenging part of building Mississippi Topsoils. “When we started we thought if we made great compost people would fall over themselves to buy it,” notes Matuska. “It’s not true for most (composters). We all need to be better at the sales and marketing side. We found out quickly that, in order to grow the business, we couldn’t continue as a retailer, but needed to become more of a manufacturer. I was a biologist (by training) and I needed to become a business manager.” He is finishing up an MBA at the College of St. Scholastica in Duluth, Minnesota. In 2014, Matuska and current co-owner Dean Miller (Mathias’ son) bought out Mathias’ interest in the firm.
To expand markets, Mississippi Topsoils began partnering with lawn and garden product distributors in several states (Ohio, Iowa, Wisconsin and Minnesota) to market its products to independent retailers. Matuska also learned the importance of offering compost in 1-cubic foot bags, in addition to bulk loads, and added three other products: composted manure, potting soil and planting mix. To supply composted manure, Mississippi Topsoils began taking manure from a western Minnesota dairy farm; 262 tons were composted last year. The company also buys rice hulls from a local distributor, and sells it as an amendment for clay soils, and for use in holiday pots.
Most of the company’s products are certified organic; one exception is the planting mix. Compost production has “stayed pretty consistent over the years,” says Matuska — about 3,700 cubic yards in 2013, and 4,000 cubic yards last year. Overall, Matuska continues, “responding to what customers want as far as quality has been very important as a driver for success. We were set up pretty well from the beginning on the operations side. We invested significantly in levels of control that we needed, but the real learning curve has been how to sell the products. We’ve been expanding into custom blends for individual growers, each of whom has different needs. So that’s been a learning experience, working closely with customers.” One example of a custom blend is adding sand to a soil mix for a southwestern Minnesota nursery, to prevent the wind from blowing over tree pots.
Matuska recently completed a study of the state’s composting industry’s economic impact for the Minnesota Composting Council and the State of Minnesota. It showed about a 30 percent industry growth rate in Minnesota, from 2008 to 2013. “With all of the sustainability and environmental issues surrounding carbon sequestration, lack of organic matter and decreasing tillable land, it’s exciting to be part of an industry that can provide potential solutions for all of these problems,” he notes.
Dan Emerson is a Contributing Editor to BioCycle.