All Treat Farms composts digestate from the anaerobic digester servicing the City of Toronto’s residential organics collection program.
Peter Gorrie
BioCycle August 2015
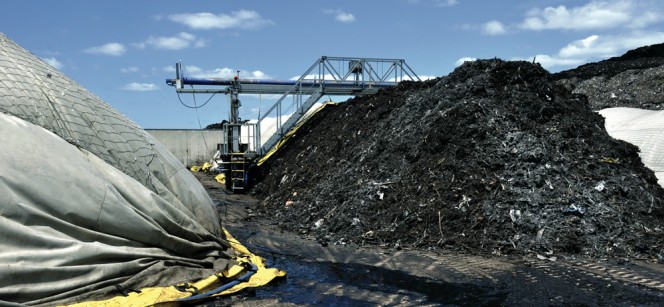
Digestate and amendment are composted in aerated windrows under a Gore Cover™ system. Photo by Peter Gorrie
Twice a day, a 42-ton truck pulls into the yard at All Treat Farms, near the rural town of Arthur, in southwestern Ontario. The driver backs the sparkling steel rig up to the loading door in a cavernous building, opens the tailgate and pushes a button that activates the trailer’s walking floor. Greenish-brown material starts to flow from the truck and down a 13-foot drop on to the floor inside. The unloading is quick and, even next to the truck, because air is drawn into the building, free of odors. This is the start of the process that turns digestate from the City of Toronto, Ontario’s 83,000 tons/year Disco Road Organics Processing Facility into high-quality compost (see “Toronto Expands Anaerobic Digestion Of Source Separated Organics,” February 2015).
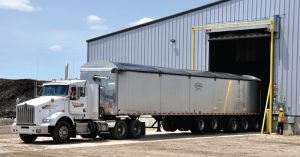
Under its 10-year contract with the City of Toronto, All Treat Farms agrees to accept up to 33,000 tons of digestate and 44,000 tons of leaf and yard trimmings annually. Photo by Peter Gorrie
Toronto began curbside collection of residential source separated organics in 2002. At the outset, the organics were processed at the city’s Dufferin Organics Processing Facility, an experimental prototype anaerobic digester with an annual processing capacity of about 27,500 tons. “They were having trouble moving the digestate from the Dufferin plant,” says All Treat’s president, George White. “Nobody wanted to take it. Toronto approached us to see if we could help them come up with a solution. We said we’d try it.”
Agreeing to compost the digestate was a gamble since, particularly at the start, it was a difficult feedstock. But All Treat believed it could take the plunge because of its long experience in composting. The company was started 60 years ago when White’s parents, LaVerne and Freda, decided to shift from “farming to selling” so, as he puts it, they would no longer be working seven days a week. The enterprise began with dehydrated and bagged manure. Then, to reduce odors and improve the product, the Whites added composting.
In the early 1980s, All Treat ventured into producing bark chips and fines, the latter an alternative to peat moss, using residuals from Ontario’s forest industry that, until then, were burned or landfilled. “This is where we developed our composting expertise,” White explains. “Bark fines could make a great growing media but if they were not composted properly they would kill plants.” The enterprise reduced the mining of wetlands for peat moss and created a market for forestry wastes. It uses both Peterson and Rotochopper grinders for size reduction.
All Treat expanded into composting residential leaf and yard trimmings in the 1990s, followed by source separated organics from the food processing industry and paunch manure, the stomach contents of animals from slaughterhouses. (The company no longer processes paunch.) With this experience, All Treat felt prepared to tackle digestate. “When we first started, it was quite a moist material,” White recalls. “It had a low solids content and it was quite odorous.”
Digestate Composting
The initial major alteration at All Treat’s 100-acre site, which has adjacent commercial and residential neighbors, was construction of an enclosed receiving hall to contain odors. The project was required as part of the request for proposals issued by Toronto. The design, with the trucks staying outside the building and dropping their loads on to the recessed floor, is intended to keep the tires from picking up and spreading the smelly material, White explains.
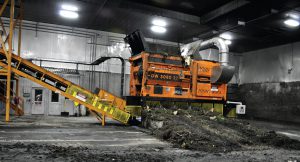
Digestate is mixed with carbon sources using an Ecoverse DW 3080 stationary shredder/blender in the enclosed receiving hall at the composting facility. Photo by Peter Gorrie
Composting digestate requires several stages — a process that can last more than eight months. After being unloaded in the receiving hall, it is shredded and combined with carbon sources. All Treat bought a low-speed Doppstadt DW 3080 stationary shredder/blender for this intake operation. “You have to blend the rougher carbon materials with the higher organic feedstock, but you don’t want to make it into balls, which won’t compost properly,” White explains. “We’re trying the best way of blending it to achieve a good mix and porosity.”
The mixture then goes into a Gore Cover™ system, where it sits in windrows on aerated concrete pads under a semipermeable cover for eight weeks. It’s turned after the fourth and sixth weeks by being moved, with loaders, to a different pad. The material is then cured in open piles for three to six months. The piles are wedge-shaped, allowing loaders to aerate them by pushing the compost forward. Other nitrogen-rich, high odor materials, including raw source separated organics and grass clippings, also go into the Gore system.
Odor control in the receiving and blending hall is performed by an energy efficient 3-stage scrubber from Netherlands-based AEC Systems BV, which completes six air exchanges per hour. Counteractive misting, in which fans spray a fog of water and odor-neutralizing microbes, is used around the outdoor piles when high humidity or other conditions warrant it.
But, White explains, a crucial part of odor control is related to management: “Controlling what goes in, controlling your process, housekeeping. Housekeeping is extremely important. That means no standing water, processing material as soon as it arrives, dealing with spills instead of letting them sit. And creating proper mixes is very important.”
Organic material delivered to Toronto’s Disco Road digester contains 12 to 14 percent contaminants, including the plastic bags that Toronto residents are permitted to use to reduce what city officials call the collection program’s “yuck factor.” The feedstock is preprocessed through the BTA™ Hydromechanical Pretreatment System patented by Germany’s BTA International and licensed in Canada and the United States by CCI BioEnergy. That step removes both the light and heavy contaminants. “They’ve come a long way,” White says. “The digestate is a lot better than it used to be. At one time it was all over the map. Now it’s fairly consistent.”
Cured digestate compost is taken into an enclosed building to be screened and go through the final process for removing the bits of plastic. All Treat has, over the years, built a system of fans, vacuums and screens to remove as much of the plastic as possible. The massive and complex system, at the back end of the process, gets the plastic airborne, then, vacuums it out of the air. “This is all from our many years of experience,” White says. “We bought different pieces of machinery and put it all together. Some was custom built for us. The aim is to remove as much of the plastic as possible.”
After screening, the compost is stored outdoors, ready to be bagged or shipped in bulk. Some reblendng can be done at this stage. All Treat makes a wide variety of compost products in “recipes.” “If we do everything right we produce compost that meets the requirements for nonrestricted use,” meeting the standards of Canada’s Compost Quality Alliance and the Ontario’s Environment Ministry, White notes.
The company bags some of its compost products, either under its own name or retailers’ brands. It also sells in bulk to soil blenders, landscapers and government agencies for uses such as sports fields, parks and highway margins. Some formulations include grass seed and fertilizer so the material can, for example, be sprayed from trucks at new subdivisions to create fast-growing lawns without sod.
Compost from digestate is rarely used in bagged products, which are mainly sold to home gardeners, White says. Most of it goes to topsoil blenders and for use on roadsides. Organics from food wastes have higher sodium levels, he explains. “Everyone uses salt. It’s our biggest concern.” The sodium is passed into the digestate and can’t be removed so “we control where it goes.” Grasses, for example, are more salt-tolerant than most garden plants.
Increasing Flow
Under its 10-year, $64 million (Cdn) contract with Toronto (awarded in 2012), All Treat agrees to accept up to 33,000 tons of digestate and 44,000 tons of leaf and yard trimmings annually. At present it is receiving only about 17,500 tons of digestate. But that will increase when the Dufferin AD facility goes back into operation after refurbishment, which will increase its capacity to 60,000 tons/year of source separated organics.
The City of Toronto now claims a 90 percent participation rate among single-family homes and low-rise residences in its Green Bin curbside collection program. Its focus now is on extending collections to high-rise buildings. Getting high-rise residents to participate is a challenge, since, for example, if a building lacks sufficient trash chutes they might need to carry their organic wastes to a central bin.
A potential solution is to move to single-stream collection, in which residents would dispose of all their wastes in one container and they would be sorted at a central facility, or perhaps at the front end of a digester. “The city is looking at various methods to increase diversion,” explains John Baldry, manager of processing operations for solid waste management services at the City of Toronto. “The combining of organics and recyclables option will be determined once our Long Term Waste Management Strategy is determined. Should we decide to go forward with the combination of materials, we will assess the technologies available and determine what we will target to produce material to be made into compost.”
White agrees that single stream collections would solve the problem of high-rise participation, but “it’s anybody’s guess what the quality of the product (digestate) would be. I’d expect more contamination, but I don’t know.” On the other hand, he adds, “Toronto goes a long way out of its way. They know if you clean it up well at the front end you’ll have a better back end.”
In the meantime, All Treat isn’t planning major changes but will work to improve its process, White notes. “We are always looking at better ways of getting the plastic out. We probably never will stop looking, until we get it to 100 percent organics. We’ll always look at adding new technology.”
Peter Gorrie is a Contributing Editor to BioCycle.