Alternatives can be compared and evaluated on the basis of Net Present Value — a method of predicting future cash flows (in and out) in today’s dollars. Part I
Craig Coker
BioCycle December 2015
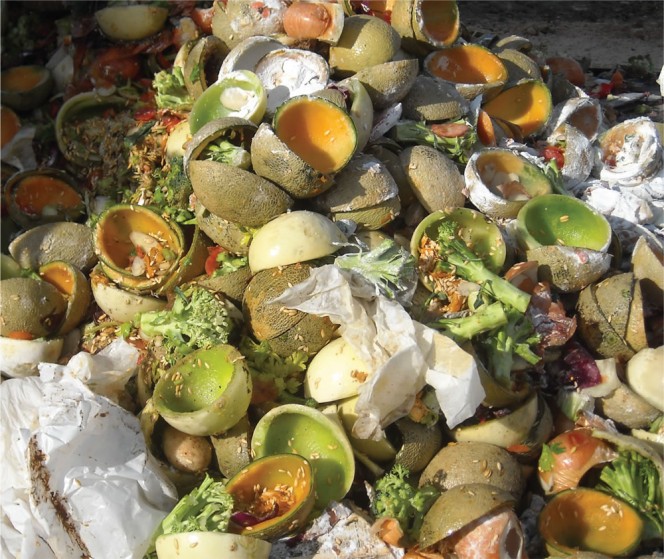
Example of food scraps generated at Virginia Polytechnic Institute and State University (Virginia Tech), which generates about 600 tons/year.
When developing and operating organics recycling facilities, the multiple variables that must be considered typically require evaluation of alternatives. Variables include available sites, climate, topography, types of feedstocks, proximity of neighbors, construction materials, equipment makes and models, or even different approaches to organics recycling in terms of on-site facilities versus off-site merchant composting or digestion services.
One tool for comparing and evaluating alternatives is on the basis of Net Present Value (NPV) — the difference between the present value of cash inflows and the present value of cash outflows. Expressed more simply, NPV predicts future cash flows (in and out) in today’s dollars. NPV is used in capital budgeting to analyze the profitability of a projected investment or project. A positive NPV indicates that the projected earnings generated by a project or investment (in present dollars) exceeds the anticipated costs (also in present dollars). Generally, an investment with a positive NPV will be a profitable one and one with a negative NPV will result in a net loss. This concept is the basis for the Net Present Value Rule, which dictates that the only investments that should be made are those with positive NPV values.
NPV analysis is based on the time value of money, i.e., a dollar to be received today is worth more than a dollar to be received at any future time. Money has a time value because of the opportunity to earn interest or the cost of paying interest on borrowed capital.
In the organics recycling universe, often multiple alternatives will have positive NPV. So how do you choose among them? Making a decision requires that the outcomes of feasible alternatives be arranged so that they may be judged for economic efficiency in terms of the selection criteria. For an organics recycling program producing a constant amount of compost or biogas annually, the best selection criteria is that which has the lowest positive NPV. With a constant output (e.g., 5,000 cubic yards/year of compost selling for $25/cy in today’s dollars), one would select the combination of inputs (capital cost, operating costs, avoided costs) that had the least NPV (again, in today’s dollars). This approach was used to evaluate alternatives for food scraps recycling at two universities in recent studies conducted by the author.
North Carolina State University
North Carolina State University (NCSU) is located in Raleigh. NCSU operated an on-campus composting facility for its landscape debris until about seven years ago. Since then, NCSU has been relying on third-party composting facilities to process both food scraps and landscaping debris. The former composting site is now used for storage of landscaping materials. “We were a little concerned about the sustainability of continued long-distance hauling of our food scraps and are interested in evaluating the possibility of restarting composting operations at the old site,” explains Analis Fulghum, Program Manager for NCSU’s Office of Waste Recovery and Recycling.
Composting food scraps in North Carolina requires a different permit than just composting vegetative debris, so the old site would need some improvements. Seven alternatives were evaluated for a projected diversion of 500 tons/year of food scraps and 500 tons/year of landscaping debris. Alternatives included: continued reliance on outside merchant composters; renewing operations at the old site with new storm water management systems and three different levels of site upgrades (minimal regrading, aggregate composting pad and asphalt composting pad); generic aerated static pile (ASP) design using concrete block bunkers; and two technology-vendor offerings — an ASP bin system and an agitated bed system.
The economic analysis was based on NPV evaluation of the seven alternatives, all with a 10-year economic life. Capital costs were estimated on a facility planning level of accuracy (i.e., +50%/-30%), and included site improvements, optional composting pad upgrades, storm water management systems, equipment additions and replacements, and vendor-supplied estimates for the two in-vessel technologies. (This facility planning level of accuracy means that at this very preliminary stage of facility design, capital costs might rise up to 50%, or decline up to 30% from the estimate presented. This variance drops as facility design, construction estimates and actual contract bids are completed). Operating cost estimates for the windrow and ASP alternatives were developed based on estimates of materials handling time and distance; for the in-vessel technologies, vendor estimates for their technologies were combined with materials handling estimates for the other processing steps. Avoided costs for current NCSU purchases of compost for use on campus were also considered.
For alternatives that have the same economic life (10 years) and produce the same output (approximately 1,275 cubic yards (cy)/year of compost), the alternative with the lowest NPV value is usually the best alternative, neglecting noneconomic factors. Other assumptions used in the NPV analysis are shown in Table 1.
The NPV analysis is done by taking all capital costs (both initial and subsequent due to equipment upgrade, repair or replacement), add in annual operational costs, subtract avoided costs, inflate the operational and avoided costs over the planning period, then discount all costs back to the present and sum the total (Table 2). Table 3 provides the relative results of the NPV analysis for the Inwood Road site (location of former composting facility) as compared to the current diversion program (Alt. 1).
Alternative 2, windrow composting at Inwood Road with minimal pad improvements, is the most attractive alternative, but is only 1.8 percent less than the current outsourced diversion program. “Our risk with continued reliance on outside parties for managing diverted wastes is that we have no control over future issues or decisions that could jeopardize those outlets, so we are proceeding with a pilot study at the old site to demonstrate to our state regulators that composting operations can be restarted with no adverse environmental impacts,” explains Fulghum. The university is exploring implementation of Alternative 2 at this time.
Virginia Tech
Virginia Polytechnic Institute and State University (Virginia Tech) has been diverting preconsumer (i.e. kitchen prep) and postconsumer (i.e. plate scrapings) food scraps from its dining hall to an outside third-party merchant composter since 2009. The composter notified Virginia Tech in May 2015 that it could no longer provide a composting option for Virginia Tech and was terminating the contract. “The decision to terminate the contract took us by surprise,” says Rob Lowe of Virginia Tech’s Environment, Health and Safety office. “Being forced to landfill the food scraps is in direct conflict with both our Sustainability Plan and our Climate Action Commitment. We found another merchant composter about 55 miles away but they can only take about 20 percent of the food scraps generated.”
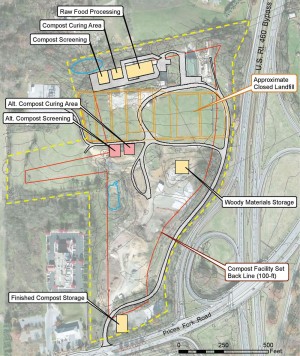
Schematic of a potential on-campus composting facility at Virginia Tech using a portion of a former landfill site on a nearby parcel owned by the university. Image courtesy of Drapen Aden Associates
In September, Virginia Tech engaged the author to examine alternative options for composting, based on a preference for using a portion of a former landfill site on a nearby parcel owned by the university. Using diversion data since 2009, the evaluation was based on composting 600 tons/year of food scraps and 600 tons/year of landscaping residuals (which are currently ground and used on-campus). Alternatives were developed considering on-campus composting approaches, discussions with state regulators about likely permitting issues, and the availability of off-campus composting and disposal alternatives. Seven alternatives were evaluated:
Alternative 1 – No action; Continue with current system
Alternative 2 – 100% to transfer station for disposal at landfill
Alternative 3 – 100% to merchant composter with rented containers
Alternative 3A – 100% to merchant composter with Virginia Tech-owned containers
Alternative 4 – Aerated Static Pile on campus
Alternative 5 – Agitated Bed Composting on campus
Alterative 6 – Windrow composting off site
Capital and operating cost estimates were developed for the alternatives. In turn, each alternative was evaluated with an economic analysis based on Net Present Value (NPV) consideration of costs over a 10-year economic life. A 10-year project life was chosen because it is a reasonable term of contract for an external service provider, a reasonable life expectancy for an on-campus composting facility (although they can, and do, operate longer) and a reasonable period of time in which to forecast future options.
Costs included the following:
Capital costs were estimated on a facility-planning level of accuracy (i.e. +50% / -30%) and included site improvements, compost processing improvements and equipment, storm water management systems, and vendor-supplied estimates for an on-campus in-vessel technology and an off-campus merchant composter option.
Operating costs for the windrow and ASP alternatives were developed based on estimates of materials handling time and distance;
Operating costs for the in-vessel technologies relied on vendor estimates for the specific technology, which were combined with materials handling estimates for the other processing steps.
Haul costs were included, both for in-campus collection and temporary storage at the old landfill site, as well for hauling to off-campus disposal or composting options.
Avoided costs for current Virginia Tech purchases of compost for use on-campus were also considered.
The assumptions used in the Virginia Tech study were similar to the assumptions used in the NCSU study. Table 4 shows the relative results of the NPV analysis comparing the alternatives to the current diversion program.
The least cost alternative is landfilling 100 percent of the Virginia Tech pre and postconsumer food scraps; the second least cost alternative is the no-action alternative of diverting about 20 percent to the existing merchant composter and landfilling the remainder. However, neither of these alternatives is consistent with Virginia Tech’s Sustainability Plan nor its Climate Action Commitment. The other four alternatives are consistent with those two guidance documents and of the four, diversion of 100 percent of the food scraps to a new merchant composter is both the least expensive and the most highly-ranked when considering noneconomic selection criteria.
This NPV analysis method can be used to evaluate both programmatic and facility-specific alternatives over the useful economic life of the alternatives under consideration. Part II of this article series will examine methods for the noneconomic evaluation of alternatives.
Craig Coker is a Contributing Editor to BioCycle and a Principal in the firm Coker Composting & Consulting (www.cokercompost.com), near Roanoke Virginia. He can be reached at craigcoker@comcast.net