USDA research shows dosing very small amounts of oxygen into an anaerobic digester significantly improves biogas quality.
Walter Mulbry, Stephanie Lansing and Craig Coker
BioCycle January 2017
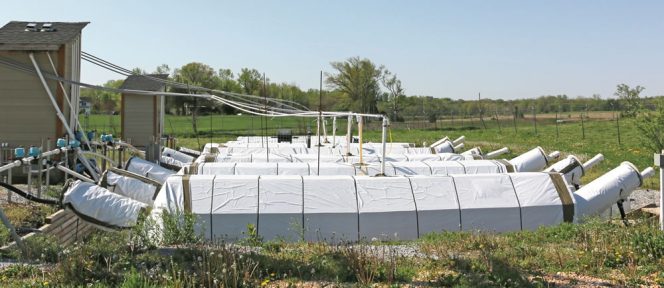
Six field-scale digesters at the BARC Dairy Unit were used to test how the oxidation rates for H2S changed as a function of oxygen levels and retention times.
Photo courtesy of BARC Dairy Unit
Anaerobic digester bacteria populations include species such as Methanosarcina barkeri and Desulfobacter postgatei, which are a type of bacteria that draws its oxygen supply from oxygenated chemical compounds, in this case, sulfates. Sulfates are the oxidized form of sulfur with a chemical symbol SO4. Sulfate is a naturally occurring anion (i.e. negatively-charged ion) in freshwater — both surface water and groundwater — and aluminum sulfate is often added to aid in the removal of particulates from drinking water supplies. Sulfates are also produced by human digestion, from both the metabolism of proteins found in foods, and by the digestive oxidation of food additives and preservatives, such as sodium sulfite and sulfur dioxide. Sulfates are also found in medical products such as Epsom salts (magnesium sulfate).
Because AD operates in the absence of oxygen, it is considered a chemically reducing environment, favoring the growth of microbes that draw oxygen from oxygenated compounds. Hydrogen sulfide, along with other reduced sulfur compounds, are often by-products of the AD of foods, energy crops, and manures, and, to a somewhat lesser extent by sewage sludges (because pre-AD sludge conditioning and thickening release soluble sulfates into the effluent, diverting them from the AD reactors).
The H2S in biogas is the main cause of corrosion of the structures and materials (iron beams and pipes) at an AD facility. The hydrogen sulfide component is oxidized during combustion, leading to formation of acidic sulfur dioxide (SO2), a corrosive gas. Sulfur dioxide causes over acidification of the engine oils during combustion in the gas engine. This results in increased wear, frequent bearing damage, higher consumable costs and longer plant downtimes.
A number of commonly used H2S removal technologies in use at AD facilities are shown in Table 1. Efficiency, capital and operational costs and complexity of these technologies are compared.
Injection of a small amount of air (or oxygen) to biogas (Table 1) promotes growth of sulfur-reducing (oxidizing) bacteria that convert the sulfide compounds to elemental sulfur. Dosing rates are typically one percent (volume/volume, or v/v) for oxygen or 5 percent (v/v) for air. For operation control, precise oxygen dosing is extremely important to selectively convert the sulfide to elemental sulfur and to minimize carryover of oxygen to the AD (particularly with gas mixing systems). Oxygen introduced into the digester may reduce the methane yield or end up in the biogas and form an explosive mixture of methane and oxygen. Air injection is considered to have uneven effectiveness, particularly if the biogas retention time is less than 5 hours.
Microaeration, i.e. the dosing of very small amounts of air (oxygen) into an AD, is a very efficient, simple and economically feasible technique for hydrogen sulfide removal from biogas. With microaeration, sulfide is oxidized to elemental sulfur by the action of sulfide oxidizing bacteria. This process takes place directly in the digester.
Microaeration Research
Researchers at the U.S. Department of Agriculture’s Beltsville Agricultural Research Center (BARC) in Beltsville, Maryland wanted to understand how the oxidation rates for H2S changed as a function of oxygen levels and retention times, and also to understand how biologically active surfaces are involved in the oxidation of sulfide compounds. BARC maintains a 100-cow dairy herd to support dairy research for laboratories that work with dairy cattle. These laboratories perform a wide range of research related to dairy cattle including waste management, mastitis control, genetic improvement, animal health and reproduction.
At the BARC Dairy Unit, six field-scale 3 m3 (105 cubic feet) capacity horizontal plug flow anaerobic digesters have been constructed for research purposes. The digesters contain about 2 m3 (75 cubic feet) of liquid and have about 1 m3 (35 cubic feet) of headspace above the liquid. In July 2016, researchers began evaluating microaeration using pairs of the digesters for each treatment. The characteristics of the dairy manure used for the testing are shown in Table 2.
The biogas produced in the experiment had concentrations of methane (CH4) that varied from 62 to 68 percent, concentrations of carbon dioxide (CO2) that varied from 32 to 37 percent, and concentrations of H2S that varied from 2,900 to 4,500 parts per million by volume (ppmv). The research team analyzed digester influent and effluent samples with a total sulfur analyzer. It calculated daily HH2S emissions as sulfur and determined that 15 to 25 percent of the sulfur coming into the digester as manure is emitted as H2S.
The duplicate-conditions field-scale digesters were fed once daily, five days per week, with 160 liters/day (42.3 gallons/day) of solids-separated manure (typically containing 3 to 4% total solids). The organic loading rate was 1.4 ± 0.1 kg VS/m3/day (0.087 lbs/ft33/day). The hydraulic retention time was 17 days. The field-scale digesters yield about 1 to 2 m3 (35-70 ft3) of biogas daily, which corresponded to a biogas retention time of 12 to 24 hours within the digester. The aeration rates used varied from 2 to 10 percent of air per volume of biogas.
At these levels of aeration, residual oxygen levels within the digesters (representing excess oxygen remaining after reaction with H2S) ranged from 0 to 1 percent (Figure 1). Although one might expect that any amount of excess oxygen would indicate complete oxidation of H2S, the team found that H2S levels in the biogas were consistently less than 100 ppmv only when residual oxygen (O2) levels within the digesters were 0.4 percent (v/v) or higher. The plots in Figure 1 show residual oxygen levels within four digesters used in the study. The top and bottom plots show the same results but the bottom plot (using a log scale) better displays values between 10 and 100 ppmv H2S.
Pulsed Aeration Tests
In a corollary experiment, the researchers examined the impact of pulsed aeration on H2S levels in the field scale digesters. They also studied the influence of biogas flow rate using 225-liter (60 gallon) barrels. In the first test, they varied the frequency of pulsed aeration from hourly pulses to pulses every 2, 4 or 8 hours and kept the total aeration time constant. The H2S levels remained below 100 ppmv (the generally-accepted level for combustion in a gas engine) using aeration pulses every 1, 2, or 4 hours. Pulsed aeration might be useful for digesters at off-grid sites where electricity is not available continuously.
In the second test, researchers varied biogas flow rates from 100 mL/min (0.0035 ft3/min) to 500 mL/min (0.017 ft3/min) in horizontal and vertical barrels. Results (Figure 2) showed that the horizontal barrels (containing about 50% more liquid surface area compared to the vertical tanks) were capable of reducing H2S levels at much higher biogas flow rates than the vertical barrels. Since the barrels were otherwise identical, one possible explanation is that increased liquid/gas surface area leads to more surface biofilm containing sulfide oxidizing bacteria and higher rates of H2S oxidation.
The next steps in the study are to evaluate whether H2S oxidation rates can be increased by enhancing the growth of sulfide oxidizing biofilms on digester wall surfaces. The researchers also want to examine the impact of microcontrollers coupled to low cost oxygen probes to monitor and control microaeration rates, trying to keep O2 levels at around 0.4 percent (v/v). These microcontrollers could transmit digester performance data to outside service contractors to assist small system operators with real-time, data driven management support.
Walter Mulbry is a Research Microbiologist with the U.S. Department of Agriculture Sustainable Agricultural Systems Laboratory in Beltsville MD. He can be reached at walter.mulbry@ars.usda.gov. Stephanie Lansing is an Associate Professor of Environmental Science and Technology at the University of Maryland. She can be reached at slansing@und.edu. Craig Coker is a Senior Editor at BioCycle and CEO of Coker Organics Recycling (www.cokercompost.com) near Roanoke VA. He can be reached at ccoker@jgpress.com.