Municipalities that own a composting plant restructure with a particular focus on energy, increasing the range of waste accepted and improving product quality.
Robin Szmidt
BioCycle January 2018
Inland from the city of Gävle, Sweden on the Baltic coast, the Gävleborg region is crisscrossed with wetlands, lakes and rivers and surrounded by miles of the famous Swedish timber forests. A recent addition to the region, in the town of Forsbacka, is a high solids anaerobic digestion plant that was integrated into an existing in-vessel composting facility that opened in the 1990s to serve the Gävleborg and a population of around 100,000 residents. Its state-of-the-art in-vessel composting (IVC) system was supplied by VAPO of Finland. Inputs were mostly yard trimmings with some putrescibles. It was one of only a handful in Sweden approved for treatment of material such as food waste under the European Animal By-Products Regulations.
Around 2013, it became apparent that process modifications were needed, even though operation of the facility was technically good, with compost quality meeting the needs of local markets. The composting process relied on very high aeration rates and air circulation, which was proving costly. High aeration also meant inclusion of a high proportion of wood such as landscaper hardwoods that could be recirculated through the mix, rather than the more plentiful local softwoods.
In 2014, the municipalities that own the plant decided to restructure the business with a particular focus on energy, increasing the range of waste accepted, improving product quality, enhancing site environmental protection — particularly in terms of allowed greenhouse gas emissions as methane slippage — and integrating the site with other energy interests of the management group. The site operator, Gästrike Ekogas AB, a company owned by Gästrike återvinnare and Gävle Energi, set a key objective of generating a target of 25 Gigawatt hours (Gwh) per year of energy as biomethane. Designing the plant to an energy target rather than tons per annum of waste was a new approach to facility development and unusual in the organic waste sector, where design capacity tends to principally reflect seasonality and local waste collection issues. To achieve that energy output, a throughput capacity of up to 38,500 tons (35,000 metric tons) was necessary.
The quantity of food waste collected in the Gävleborg region was 485 lbs/person (220 kg) in 2015. In 2016, that number rose to 529 lbs/person (240 kg). The new facility had to continue the success it had achieved processing commingled yard trimmings by handling as much food waste as possible while generating quality products for established markets.
Selecting HSAD
Climatically, the Gävleborg region typically receives substantial snow during the cold, dark winters. This meant a guaranteed construction “window” of only six months. It also meant that in operational terms, production of large volumes of low value liquid digestate would not be welcome in an area with limited agricultural production. The decision was made, therefore, to build a high solids anaerobic digester (HSAD) versus a wet AD system with greater volumes of low solids digestate.
The footprint of the existing site — about 5 acres — was adequate to accommodate the addition of the HSAD. The compost hall is about 170-feet by 130 feet, and the digester, including input pipework and other support infrastructure, has a footprint of 115 feet by 40 feet (the digester body itself is about 33-feet wide).
After a competitive bid process, Thöni Industriebetriebe GmbH of Austria was selected as the technology supplier. The core technology is the latest TTV horizontal thermophilic plug-flow digester that employs a horizontal steel digester equipped with a massive single end-to-end paddle mixer. This crossflow paddle mixer slowly turns the input material to facilitate the process and release biogas. Operational temperature within the digester is about 131°F (55°C).
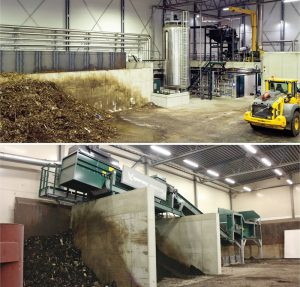
All inputs are combined in a mixing unit in the reception hall (top). Recirculated digestate and make-up water is added as required to achieve 33 percent dry solids content. After a retention time of 30 to 35 days, digestate is dewatered and composted for 7 to 10 days then screened (bottom). Photos by Robin Szmidt
Construction started in Spring 2016 and the main buildings and digester were completed around the time of the first winter weather in late autumn that year. Indoor fit-out continued during the winter and the first waste was received at the new plant in Spring 2017. The facility processes 25,000 to 38,500 tons/year. To minimize the carbon footprint of the site and maximize energy efficiency, a number of novel energy strategies were adopted. These include:
• Air-to-air heat recovery between different building zones linking to the air handling and odor treatment system. The reception hall and dewatering are integrated in one zone and the IVC tunnels and end product screening are integrated in another zone. The air-to-air heat recovery recycles the heat, thus much less energy is used in total.
• Heat recovery from the digestate output zone links to underfloor heating of the reception area to allow acceptance of frozen winter material. Heat exchangers modulate energy management in the post-digestion composting facility.
Feedstock Preprocessing
Input material such as commingled yard trimmings and food waste is received in the indoor hall and roughly shredded using an Allu hydraulic bucket-screen to about 2- to 3-inches in particle size. The objective is more to crush the feedstocks than to shred them. This avoids turning a relatively small number of contaminants such as plastic bags into large numbers of small pieces that are then difficult or impossible to remove. After coarse shredding and removal of larger items, material is fed to the digester via a metered bunker.
Yard trimmings collected by themselves are received in an outdoor area, shredded using a Willibald high-speed shredder and transferred to the main reception area. This material normally is processed via the digester although it can be bypassed straight to composting if the operator prefers, e.g. during peak periods. There is also a heated tank for reception of liquid fats, oils and grease. All inputs are combined in a mixing unit controlled by the overall computer system. This ensures the correct consistency is fed to the digester with the addition of recirculated digestate and make-up water as required. Input material is around 33 percent dry solids (DS) and is loaded into the digester via a heated input pipe.
HSAD And Composting Operations
The TTV digester has an active volume of digestate of 2,950 cubic yards (2,250 m3) and a typical retention time of about 30 to 35 days, depending on seasonality. The digester operates in the thermophilic temperature range and continuously receives input material, seven days a week.
While this type of high solids digestion technology is well known across much of Europe, it is the first time that such a large digester has been built in Sweden. A critical issue was the permitting and approval of the facility under local conditions. In Europe, material that contains or may contain animal by-products (ABPs), such as food waste, is specifically regulated and must be treated hygienically. Under European regulations, ABPs can be treated either according to a standardized regime of time, temperature and particle size, typically 1 hour at 158°F (70°C) and approximately half an inch (12 mm) maximum particle size. This method is best suited to liquid treatment and wet AD systems.
For treatment of solids, which are more suited to management via HSAD and composting, the process can be tested for biological efficiency and hygiene. In this case, the project team negotiated a specific regime with the local regulator to approve the site for destruction of known pathogenic marker organisms such as E.coli and Salmonella. This has never been done before under Swedish conditions and requires ongoing liaison between the operator, the technology supplier and the regulator, the Swedish Board of Agriculture (Jordbruksverket).
Digestate is discharged from the TTV digester by a solids pump and then directed to the dewatering system. A first-step vibrating screen separates out the free liquid and the remaining material is further separated using a Thöni screen-screw press, to approximately 12 percent DS liquid, which is directed to a settling tank and then storage. The solid fraction, about 37 percent DS, is transferred to the IVC tunnels, where this fraction undergoes a full but quick “active” aerobic composting process under positive aeration. Most of the biological energy has come out as biogas but the remainder that can only degrade aerobically does so. The process will peak at about 140° to 150°F (60-65°C) within 7 to 10 days.
Exhaust air finally exits the system via an acid scrubber and biofilter. Overall, the HSAD process integrated with composting creates a final product in around one-third the time of the previous composting only facility. The finished material at around 55 percent DS is then completed as high quality compost after screening and air-sifting. The air circuit for the IVC tunnels recovers heat and recycles air from within the buildings to maximize energy and process efficiency, minimizing loss of heat and potential odor.
Compost And Digestate Products
The final products — solid composted digestate and fertilizer-grade liquid digestate —have to be tested for natural populations of Salmonella sp., enteric bacteria and specifically E.coli, under the regime known as SPCR120, before it can be sold as a product. SPCR120 (Table 1) is one of the most rigorous product standards in Europe. In addition to maximum values for potential toxins such as heavy metals, the inert material thresholds are high, not just in weight values but also visible impurities such as plastics (Table 2). This is an approach increasingly considered by standard setting agencies across Europe. The test laboratory is required to unfold each item in the sample to determine the potential visibility, i.e., the visibility test is not what you see (e.g., rolled up ball of plastic foil), but what is seen when every single item of contamination is unrolled and unfolded.
The visibility threshold is extremely challenging, particularly if the sample were to contain a lot of shredded plastics. This is why the project team at the Forsbacka HSAD-composting facility opted for a front-end crusher-screening rather than fine shredding, coupled with post-digestion separation of remaining contaminants. The composted digestate also has to pass a seed germination test.
Buyers of the Forsbacka facility’s horticultural grade compost (sold in bulk) were mostly landscapers, who also would purchase soil blends, e.g., turf mixes. At this time, the operator is working on reestablishing and increasing those markets and also expanding to more agricultural outlets for the high density liquid fertilizer (liquid digestate).
Long term compost analysis data for the site at Forsbacka are not yet available but it is generally expected that the value of the composted digestate will be about 2 percent nitrogen (DS) and NPK 3-1-2 and with a dry solids content >55 percent. This is suitable for land application or use in horticulture, such as high quality turf and soil mixes or bagged product.
When the project was first suggested, local farmers were keen to consider HSAD liquid digestate because of its organic nature, fertilizer value and known crop productivity benefits compared to more commonly available wet-AD liquid digestate, which typically has only a few percent dry solids and low fertilizer value. The relatively high DS content of HSAD liquid digestate, at around 12 percent, was initially a cause for concern because of worries about the risk of blockage of spreading equipment. However, this is not normally the case as flowability and viscosity, rather than DS content, are key.
Liquid digestate fertilizer values of around NPK 7-1-1 at 6 to 7 percent N (>10% DS) are expected, depending primarily on the percentage of food waste in the input material. Over time, as farmers become more relaxed about the ease of application and benefit from the value of high solids, the market is expected to expand. Irrespective of markets for the fertilizer-rich liquid, local regulations and the reality of a cold winter climate mean that the site has to plan for a short summer season when digestate can be applied to land, with about 6 to 8 months of storage capacity required.
Currently, after transport, the digestate is cost neutral to farmers. In the future, the expectation is that sales will be based on N equivalence so there is a motivation to increase the fertilizer value. This is linked to the overall increase in food waste in the mix.
Managing The Process Transition
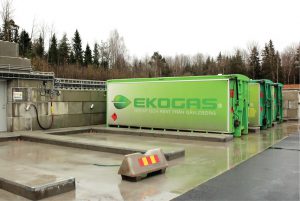
A biogas absorption upgrade system produces biomethane at about 99 percent methane, which is pressurized and stored for delivery via a road tanker (fuel tanker station shown). Photo by Robin Szmidt
Transformation of the Forsbacka facility and its market position was not without hiccups. During construction, the site was offline for as short a time as possible, however this did have an impact on the business. Supply of feedstock was interrupted and despite trying to maintain customer loyalty, current inputs are not exactly as envisaged. Around six months after the new facility began receiving waste, food waste only content was less than expected and the amount of commingled yard trimmings and food waste was higher. As a result, the operational team has had to adapt and overall it has been a good stress test of the site to ensure that it has flexibility to cope with future changes.
On the energy side, biogas accumulates first in the buffer headroom above the digestion matrix within the TTV digester body. A controlled flow of biogas is then accumulated in the gasholder over the liquid storage tank. The biogas is then routed to a Puregas Solutions biogas absorption upgrade system to produce biomethane at about 99 percent methane.
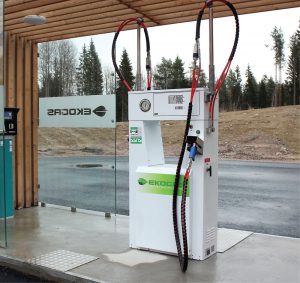
A separate pressurized storage and fueling station (above) is available for customers at the integrated AD and composting facility. Photo by Robin Szmidt
The site does not have access to a gas pipeline network so the biomethane is pressurized and then initially stored on site for delivery to customers via road tanker at 200 to 250 bar (compression). A separate pressurized storage and fueling station is also available for customers at the site. The gas-filling station routinely serves the refuse collection vehicle fleet that brings fresh waste to the facility. Local residents and private individuals can fill their vehicles using a credit card at the unmanned 24/7 fueling point. With limited access to a traditional gas network, the local community is increasingly benefitting from tankered, distributed, biomethane as a “virtual pipeline.”
Dr. Robin Szmidt is founder and director of Target Renewables Ltd., a unique UK-based consultancy for the international AD sector. He has worked on a number of projects with major AD vendors and investors in Europe and North America. Dr. Szmidt has a PhD in compost microbiology, and a product use background in agriculture and horticulture.