Further separation concentrates nitrogen and phosphorus in the solids. The liquid “tea water” contains mainly dissolved solids, including ammonia and potassium.
Peter Gorrie
BioCycle March/April 2018
The mass of manure produced on American livestock farms — totalling about one billion tons per year — is both valuable and a nuisance. On one hand, manure is an important source of nutrients and organic matter to grow crops and maintain healthy soils. On the other, it’s smelly, of potential concern for air and water quality and, when produced in excess of a farm’s needs, difficult and expensive to transport and apply.
Interest in exploring technologies that enhance manure’s benefits while reducing, or even eliminating, the problems associated with it, is high in the $35.5 billion/year dairy industry. The sector is under pressure to produce more milk and cheese for a growing population, while that population sprawls across farmland, leaving less space to spread manure. “There is a tremendous opportunity to generate environmental and economic benefits from manure by-products, but further innovation is needed to develop more effective and affordable technologies,” the U.S. Environmental Protection Agency (EPA) states in a background paper for its ongoing Nutrient Recovery Technology Challenge.
Reducing complaints and environmental risks is crucial to giving dairy farms a “social license” to operate, according to Newtrient LLC, a Rosemont, Illinois company founded by 12 milk cooperatives representing nearly 20,000 U.S. dairy farmers, to develop nutrient recovery technologies. These technologies separate manure’s components into as many useful and benign products as possible. Three examples from dozens of U.S. and Canadian dairies engaged in some form of advanced nutrient recovery are:
• Edaleen Dairy Farm in Lynden, in northern Washington State, anaerobically digests manure from 1,800 Holstein dairy cows to produce energy, bedding for the stalls, nutrient rich cakes that can be transported to distant fields, and a liquid residue called tea water that, within limits, can fertilize and irrigate feed crops.
• The massive Prairie’s Edge Farm in Fair Oaks, Indiana, goes a step further with the manure from its 15,000 Holsteins. It ships the nutrient cakes to a facility where it is processed to create a series of custom products.
• SeaBreeze Farm in Delta, south of Vancouver, British Columbia, has 350 Holstein cows and is seeking ways to make further processing of the nutrient cake viable for smaller operations.
“There’s lots of valuable components in manure,” says Frank Engel, marketing director for Trident Processes LLC, based in Abbotsford, British Columbia, which developed the technology to produce the nutrient cake at SeaBreeze and Prairie’s Edge. The question is: “How do you come up with a process that creates it into a more manageable format?”
The conventional approach to manure management is to collect it from barns and spread it over the farm’s fields. Its high water content can make it too expensive to ship any distance, requiring that it be applied near where it is generated. If a farm’s land base is small, and no neighbors are able or willing to take the manure, it risks being applied in amounts far beyond what crops require. In that case, the excess nutrients, primarily nitrogen and phosphorous, could run off into surface streams and lakes, or seep into groundwater. In addition, manure’s odor can impinge on nonfarm neighbors, and as it decomposes it releases methane, a potent greenhouse gas. To avoid these impacts, governments restrict manure application rates and impose limits on herd size so farms won’t exceed those rates.
Anaerobic digestion (AD), a technology installed at all three of the dairies mentioned above (details on each in the sidebars), starts to deal with these issues: The biogas is burned to generate electricity or upgraded to become the equivalent of natural gas. And the residue, digestate, can be applied as a fertilizer and soil amendment, used as feedstock for composting, be processed into animal bedding or, on at least one Connecticut farm, formed into biodegradable planting pots. But it contains enough nutrients to still be subject to application restrictions, and its weight continues to limit the distance it can be shipped off-farm.
According to the U.S. EPA AgSTAR program, there are about 250 anaerobic digesters on U.S. farms, including just over 200 on dairy operations. But even as AD slowly gains acceptance, it is increasingly recognized as just the start of an effective nutrient recovery system.
Advanced Nutrient Recovery
The main aim of the technologies beyond AD is to extract the solids and nutrients from the feedstock, creating a relatively clean, clear liquid and a material with concentrated solids and nutrients. Advanced systems can be operated with an anaerobic digester, in which case digestate becomes the feedstock, or without AD, using preconditioned raw manure. Tradeoffs between the two approaches are discussed in a sidebar.
Primary Solids Separation
In either case, the first stage of advanced nutrient recovery is primary solids separation, which involves putting the feedstock through technologies such as a slope screen, rotary drum screen or screw press, to extract large, nutrient-poor fibers — 20 to 40 percent of the total solids. If the manure has gone through an AD, the fibers can be used on-farm as animal bedding, or sold as bedding, a soil amendment, or a substitute for peat moss. Without an AD, they must undergo composting before producing such products.
Fine Solids Separation
After primary solids separation, the resulting liquid is treated to remove most of the remaining solids that are rich in nutrients and too small to extract with simple mechanical processes. Several technologies are available, but centrifuge, pressure membrane, or flocculation appear most suited to handle the chemical make-up and pH of dairy manure. Dissolved Air Flotation (DAF) is one type of flocculation process used in wastewater treatment to remove and recover suspended solids. In a DAF system, used by the three dairies, polymers, compounded to bond with the small solids and their associated phosphorous and organic nitrogen, are added to the feedstock, creating clumps, which can be removed in various ways.
Solids “Drying”
The solids are then further dried. The three dairies squeeze them in a moving disc press, which produces “nutrient cakes” with 22 to 25 percent solids content. The cakes can be applied as a fertilizer and soil amendment. They are, in theory, dense enough, relative to their nutrient value and moisture content, to transport further distances.
Tea Water
The remaining liquid, known as tea water, contains mainly dissolved solids, including ammonia and potassium. Its lower nutrient and solids content are conducive to keeping storage lagoons clean and applying it as irrigation water to nearby fields.
Partitioning the manure into solids and liquid gives farmers flexibility in targeting nutrients to particular fields and crops to reduce costs and potential environmental losses. Newtrient, LLC characterizes Edaleen Dairy’s results as follows: “Reduced energy to mix, dredge, pump and haul liquid manure; greater flexibility in targeting specific fractions and types of nutrients to individual fields/crops; and with potential export off the farm, reduced acreage, haul and/or application costs to meet dairy nutrient management plans.”
Fertilizers And Nutrient Concentrates
A further step is to utilize the nutrient cake to manufacture a fertilizer. Adding different combinations of nutrients creates a range of products targeted to particular crops and portions of the growing season.
Research is underway on techniques to remove more of the remaining nutrients from the tea water. Possible approaches include vacuum evaporation and pressure-driven membranes, which can partition the tea water into a liquid nutrient-concentrate and a “clean water,” potentially suitable for stream discharge, and requiring no costly storage and/or field application. But both would add significant capital and operating costs.
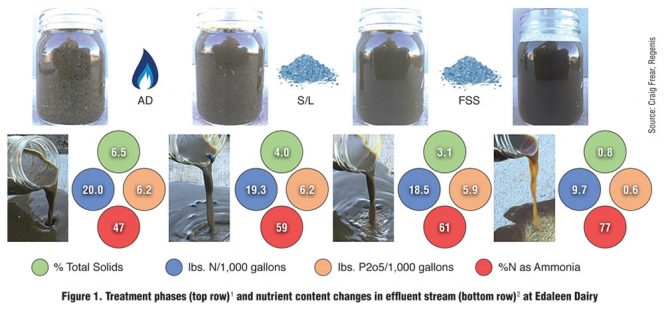
Figure 1. Treatment phases (top row)1 and nutrient content changes in effluent stream (bottom row)2 at Edaleen Dairy Source: Craig Frear, Regenis
1From left to right (jar contents and treatment phase): Raw manure diluted with parlor/wash water prior to AD (anaerobic digestion); Anaerobically digested effluent prior to primary S/L (solids/liquid separation); Effluent after primary S/L and prior to FSS (fine solids separation); Effluent after DAF (dissolved air flotation) treatment. 2Total solids and nutrient content and visible changes in liquid (from left to right): Raw manure; digested effluent; after primary solids separation; “tea water” after FSS.
Figure 1 illustrates the phases of nutrient recovery at Edaleen Dairy, starting with raw manure diluted with parlor/wash water and ending with the tea water (effluent after DAF treatment). Total solids and nutrient content are listed for each phase.
Recovery Economics
Costs are, in fact, a point of discussion. Engel says the payback time for the SeaBreeze nutrient recovery system is only two or three years. But most see financial concerns as a major impediment. Every step toward cleaner, more consistent manure products is increasingly expensive, notes Craig Frear, director of research and technology at Regenis in Ferndale, Washington, the company that developed Edaleen’s system.
“At this time the economics for small operations would be very challenging, unless niche markets are found for the recovered products,” says an EPA spokesperson. “High costs can be especially prohibitive if lenders are unwilling to finance technologies without a proven track record of technical and economic performance.”
AD can earn money through feedstock tipping fees, sales of renewable natural gas (RNG) to utilities, and environmental incentives, where they are available. As well, digestate can be cheaper to process for nutrient recovery. But using raw manure avoids a digester’s costs. A careful review of scale, costs, and revenues is required to determine whether AD should be used as a first step before nutrient recovery.
As an example of the higher costs associated with greater treatment beyond AD, primary solids separation — removing the large fibers — costs $23 to $55/cow to acquire the equipment and probably double that to install, as well as $8 to $16/cow/year to operate, according to a report coauthored by Frear, which bases its figures on a 1,500-head herd. But savings from not having to buy bedding, along with revenue from off-farm sales, can make this technology profitable. Even smaller farms might be able to afford it.
Cost increasingly becomes an issue with further stages of nutrient recovery. Capital expenses for centrifuge and flocculation systems, to create nutrient cake, range from $90 to $168/cow for equipment only, and operating costs range from $30 to $55/cow/year. Manure management cost savings resulting from their installation don’t offset those costs. The key is to develop markets for the nutrient cakes.
According to the EPA background paper, markets for off-farm sales of the cake are “extremely limited” and “struggle to compete pricewise with commercially available fertilizers,” even though commercial products lack micronutrients and organic matter. “As a result, even well-functioning technologies may not generate a positive return on investment for producers because there are few steady markets for the nutrient products they generate within an economic distance.”
One major benefit, albeit difficult to quantify, is that, with more controlled fertilizer application, the new nutrient products might let farms on limited acreages stay in business, or even expand their herds, without having to move or acquire additional land to deal with their manure. “If you can continue to operate where you are because you can segregate your nutrients out and haul them away, what is that value?” asks Carl Ramsey, the farm’s operations manager at Prairie’s Edge.
There is a good market for the granulated products produced by Midwestern BioAg, a fertilizer manufacturer, where Prairie’s Edge sends its nutrient cake (see sidebar), since they are consistent, easy to apply and, unlike commercial fertilizers, add organic matter to soils. Still, to date, only a large farm like Prairie’s Edge can afford to be involved with that technology. “They are getting a nice price,” Frear notes. “It’s a beautiful product. The problem, again, is scale. At 1,800 head you’re not going to be able to install that system and pay for it.”
A centralized processing plant to service several farms might solve the scale issue, but it raises a “chicken and egg” situation, he adds. What comes first: a commitment from several farms to install a DAF or similar system, or someone willing to invest in a central facility.
For now, government incentives appear to be important to kick-start nutrient recovery, from AD to more advanced technologies. California has shown the potential, Frear says. Programs like the carbon cap-and-trade system and low-carbon fuel standard (LCFS) have spurred significant growth in both AD and non-AD approaches to greenhouse gas reduction and associated environmental benefits. Last year alone, 18 new AD projects in California were awarded grants for development while grants for non-AD (e.g., composting) will soon be announced. Importantly, availability of LCFS credits has led to the development of large projects outside of California, which pipe their RNG into the state.
For some, the ideal is for nutrient recovery to stand alone as good business, without incentives. But that will require significant progress in the development of markets for coproducts as well as technology costs and performance.
Still, those involved say working to overcome nutrient recovery’s challenges is worth the effort: “While not a magic bullet, (nutrient recovery) technologies, used in combination with enhanced manure and fertilizer application management, have the potential to improve overall manure management — and to provide new options to dairies that are seeking to produce milk both sustainably and profitably,” Frear’s report concludes.
Peter Gorrie was a Contributing Editor to BioCycle at the time he wrote this story.