Top: KEITH Walking Floor receiving bin has 10-foot high walls. Photo courtesy of Vanguard Renewables
Nora Goldstein
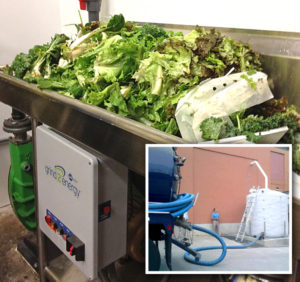
Grind2Energy unit installed at Whole Foods in Andover, MA. Pulped food waste slurry flows into an outside storage tank (inset) that is serviced by a tanker truck.
In 2015, one of the tours during BioCycle’s 15th Annual Conference on Renewable Energy From Organics Recycling in Boston, first stopped at a Whole Foods Market in Andover, Massachusetts, followed by a tour of Jordan Dairy Farm in Rutland (MA). Whole Foods had installed a Grind2Energy system to process produce and other foods that were no longer edible into a slurry that was stored in a tank adjacent to the store. When full, the tank was emptied into a tanker truck, which then went to Jordan Dairy Farm for injection into the farm’s anaerobic digester.
Vanguard Renewables, operating under the name AGreen Energy at the time of our tour, built and managed the dairy digester at Jordan Farms. Today, the company has a total of 6 farm digesters in Massachusetts and Vermont that codigest food waste and manure. It builds, owns and operates the digesters, managing the manure on those farms. The dairies receive a lease payment and utilize free heat recovered from the combined heat and power engines, as well as low carbon fertilizer and bedding material for the cows.
Over the years, competition has grown for clean preconsumer food waste streams like the ones at Whole Foods in Andover. Organics recyclers in Massachusetts and surrounding states recognized that they would need to start handling more contaminated loads of food waste, especially to service generators that had to comply with Massachusetts’ ban on disposal of commercial organics for entities generating 1 ton/week or more. A few companies installed depackaging equipment at transfer stations or other waste receiving facilities, with the slurried food waste then delivered to anaerobic digestion or composting facilities in the region.
Several years ago, John Hanselman, Chairman and CEO of Vanguard Renewables, recognized that to remain competitive and have full access to food waste streams for its anaerobic digesters, it should invest in an organics recycling facility (ORF) to handle all food waste streams. “Generators simply want you to show up and take it,” he told BioCycle in a January 2019 article. “We had the luxury in the early days to get clean streams, but now more players are competing for that food waste. Realistically, as an industry, we should not put that [separation] burden on the generators. We should charge differential pricing, but companies like ours should be able to take all types of loads containing organics.”
Hanselman added at the time that having multiple digesters in central and western Massachusetts gives Vanguard Renewables the insurance that if one digester is down, it has other facilities that can receive the food waste. “Having backup is super critical,” he said. “If we didn’t have redundancy in our processing capacity, the generator gets stuck with having to find an alternative outlet. Our goal from the outset was to beat that. We always have enough AD capacity.”

All operations at Vanguard Renewable’s organics recycling facility are inside a 13,000 sq. ft building in Agawam, MA.
New ORF In Agawam
Fast forward to mid-September 2020, when Vanguard Renewables began commissioning of its totally enclosed ORF with capacity to process 250 tons/day of food waste, both packaged and unpackaged. The facility is in Agawam, Massachusetts, and is centrally located to the company’s farm digesters. Access to two interstate highways is nearby. “We bought a 5-acre piece of land 2 years ago in Agawam, and went through the permitting process with the town and the state Department of Environmental Production,” notes Hanselman. “We believed very strongly that we needed to take every step available to control odors. All operations at the ORF — from unloading incoming vehicles to loading outgoing tanker trucks — are inside our 13,000 sq. ft building. There is a very heavy-duty activated carbon filter to treat all building air.”
He anticipates about a 50:50 split of packaged and unpackaged food waste, the latter with some contamination. Generators to be serviced include restaurants, distribution centers, cafeterias, and a range of packaged food and beverages that are off-spec or no longer edible. “When selecting equipment and the layout of our materials handling and processing line, we wanted something easier and faster than some of the models we had seen,” says Hanselman. “We felt that those models weren’t sustainable long-term for this kind of investment. We may have over engineered the ORF but we are looking for a 40-year operating asset.”
Walking Floor + Turbo Separator
Several years ago, Kevin Pedretti, Business Development & Product Marketing manager at Scott Equipment Company, was trying to solve a geometry problem related to feeding food waste feedstocks into the company’s THOR Turbo Separators. “I was looking for a better way to move organics from Point A to Point B on the inbound to our separators, and started digging around,” recalls Pedretti. “Trucks need to unload on grade, and then have something to dump into, like a sealed receiving bin. I saw use of below grade stationary Walking Floors at transfer stations and thought that could be a possible solution. I connected with KEITH Manufacturing, which specializes in all kinds of Walking Floor conveyors, and learned that it was working with the City of Tacoma, Washington on a pilot project to codigest food waste at its wastewater treatment plant.”
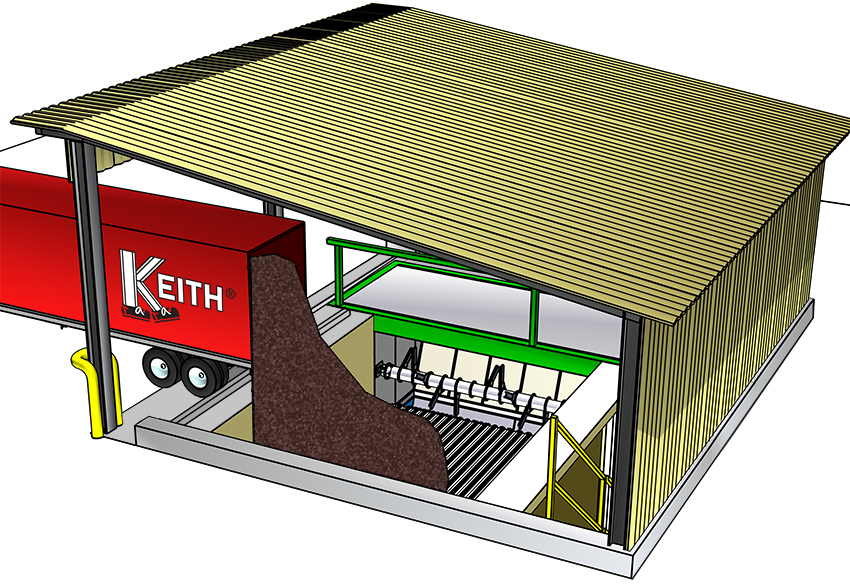
Illustration of a truck on grade unloading onto the Walking Floor bin that is below grade. Rendering courtesy of KEITH Manufacturing
Kevin Desjardins, Stationary Sales Engineer at KEITH, explains that the City of Tacoma was bringing in clean grocery store waste that was loaded onto its stationary floor, which “walked” the food waste to a macerator at the other end. “We had sold a stationary floor in 2011 to the Fremont (MI) food waste digester to meter material to a macerator,” says Desjardins. “Then, at trade shows and elsewhere, we were getting inquiries about using our stationary floor for food waste applications. It is just a conveying system but has the advantage of the KEITH Walking Floor reciprocating slat system. One-third of the slats move under the load, and the other two-thirds remain stationary. This enables good flowability — material that is moving on the floor slats will drag the material that is in between the floor slats as it moves.”
While the City of Tacoma did not go forward with an installation at that time, Pedretti and Desjardins decided to collaborate on putting projects together. The opportunity presented itself with the Vanguard Renewables’ ORF in Agawam. “Kevin put it all together,” notes Desjardins. “Our floor serves as a storage receiving bin for the materials that are unloaded onto it. The floor itself has a variable speed so that material can be synchronized with the downstream components, in this case the Turbo Separator. The speed is determined by how many tons/hour the downstream components can process as well as the volume in the receiving bin at that time. The lower the pile height, the faster it can move; the higher the pile depth, the floor moves at a slower speed.”
The KEITH receiving bin has a solid pan under the floor slats. The bottom of the walls are welded to the pan so that the interior space on the floor contains the material’s free flowing liquid and organics. At the Vanguard ORF, the KEITH Walking Floor bin — 40-feet long by 10-feet wide with 10-feet tall walls — is 4-feet below grade in a concrete formed space that slopes gently to the Scott Mega THOR infeed hopper. “This way, if a load of milk or liquids goes in, it will flow to the discharge end,” explains Pedretti. “There is a sealed plate where the truck dumps so all matter of organics end up on the receiving bin. And there is a kicker plate at the discharge, so liquids do not circle back underneath the Walking Floor system.”
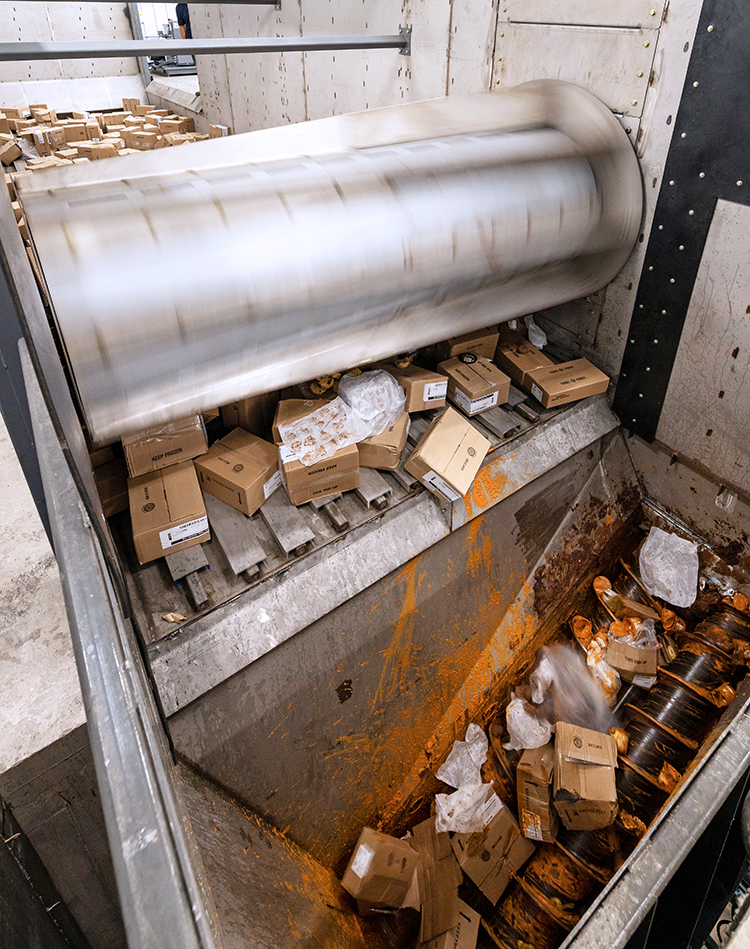
The Walking Floor system at the Agawam ORF maintains a consistent flow of material into the twin-screw hopper of the Turbo Separator. Photos courtesy of Vanguard Renewables
The twin-screw hopper receives the surge of material from the Walking Floor bin and meters it into the THOR depackaging system. An integrated sensor above the hopper signals the Walking Floor conveyor to regulate the volume. The Mega THOR, with a 1-inch thick 316 stainless steel shell has 52 swing hammers that help separate organics from the packaging, adds Pedretti. “The organics pass through punch plate screens that line the bottom of the THOR. They are then diluted with collected liquids from the twin screw hopper and other recycled bulk beverages, then pumped to storage tanks. We can theoretically process >30 tons/hour of material, however the normal mix of usual products is typically from 12 tons/hour (bakery/cookies) to 20 tons/hour (canned foods, vegetables, etc.). So on a 12 to 16 hour processing day, you could achieve rates of 250 tons/day of feedstocks.”
The waste packaging is discharged at the end of the THOR into a short inclined screw conveyor, then drops onto an inclined belt conveyor that deposits the fairly dry mixed packaging into a compactor. The facility is trying to recycle as much of the liquids as possible to minimize the amount of potable water needed to process feedstocks. “We can use a high liquid, low solid feedstock, like pallets of diet soda, to process a load of caramel candies,” explains Hanselman. He anticipates the ORF will have about a 6% reject rate by volume of materials that can’t be recycled.
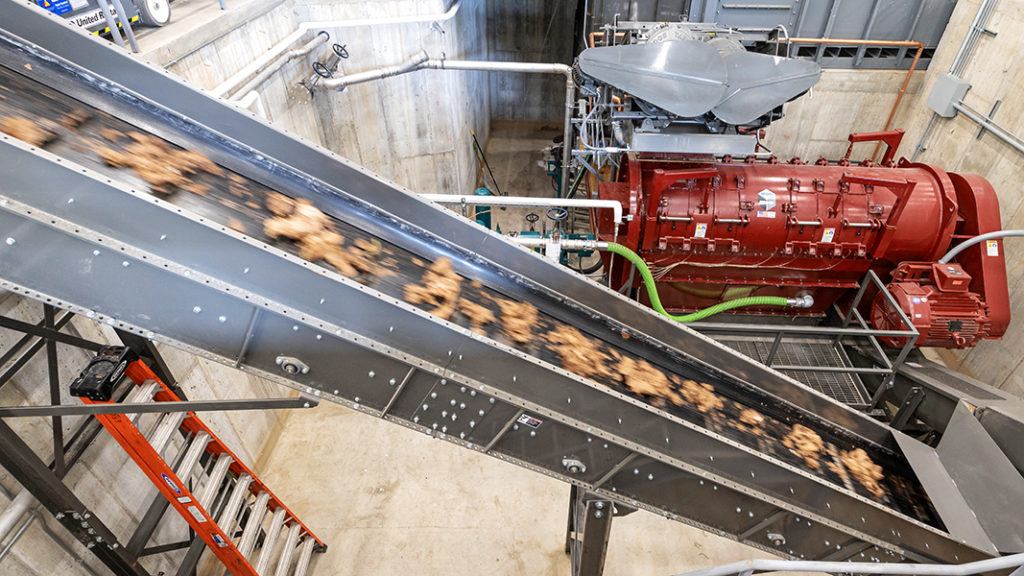
The Scott Equipment Mega THOR (in far right corner) has 52 swing hammers that help separate food waste from its packaging. The organics pass through punch plate screens that line the bottom of the unit. Waste packaging is conveyed to a compactor.
Vanguard Renewables installed a series of tanks in order to calibrate the “strength” of the slurries being taken to the digesters. “We can actually ‘grade’ the feedstocks so we know their energy content and value, e.g., low, medium and high, and then balance out a tank load for a digester,” he adds.