Top: Merck & Co., Inc. installed on-site composting vessels at two of its facilities in New Jersey. The installation in Rahway (above) is inside a building with 32-foot high walls.
Nora Goldstein
Merck & Co., Inc., a pharmaceutical company with its largest New Jersey facilities located in Kenilworth and Rahway, has a comprehensive waste reduction, recycling and sustainability program. Zero waste initiatives include on-site food scraps composting, recycling challenging materials such as lab plastics, and implementation of a reusable coffee mug program.
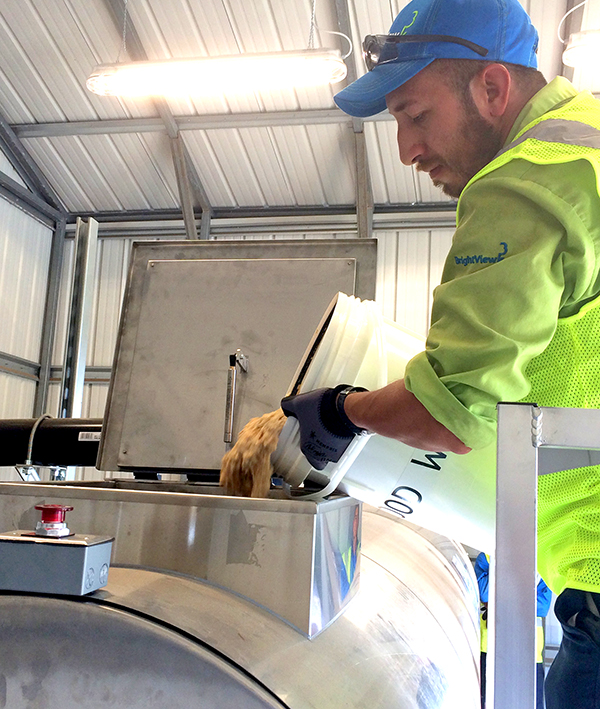
Domino Park uses a waste pulper as a pretreatment/volume reduction step before adding the food scraps to the unit. Photos courtesy of Food Waste Experts
Initially, source separated cafeteria food scraps were being collected by a private hauler and composted off-site. In 2018, a team of engineers at Merck’s headquarters in Kenilworth wanted to improve the soil quality of planters, beds, and turf, utilizing the food scraps and wood chips that were already available. The team explored different technologies and decided to acquire an in-vessel A900 Rocket Composter, with capacity to process 385 gallons/week of food scraps with an equivalent amount of wood chips. The on-site unit, 13.1-feet long, 3.3 feet wide and 5.3 feet high, is located in a dedicated building not far from the cafeteria. It was supplied and installed by Food Waste Experts in Tarrytown, New York. “When sizing a unit for a corporate cafeteria, we estimate, as a general rule of thumb, food scrap generation of 0.625 lb per meal served,” explains Gerardo Soto, founder of Food Waste Experts.
The cafeteria’s food scraps are transported to the in-vessel unit and mixed with the wood chips (generated from tree trimmings on the corporate campus). The residence time inside the vessel is two weeks; it operates on a continuous basis and is loaded daily. The system has a central mixing shaft that provides continuous and uniform aeration to the mass, redistributing heat and moisture as the shaft rotates. The Rocket composter is positioned on an angle, enabling excess liquids from the process to drain off at the back of the unit into a 5-gallon bucket. In addition, there is a fan to extract excess moisture from the top of the composter.
Compost discharged from the vessel needs to cure for an additional 2 to 4 weeks before application to Merck’s green areas. Curing takes place outside in static piles. “Energy usage of the A900 composter is 30 kWh/week,” says Soto. “Operating costs are approximately $0.017/gallon.”
In 2019, Merck bought a second A900 Rocket composter, which it installed at its facility in Rahway in a massive room with 32-foot high walls located about 7 minutes from the cafeteria. Since it began operating, Merck’s Kenilworth site has composted more than 26 tons of food scraps; the Rahway site has composted more than 16 tons of food scraps. In 2020, Merck received the New Jersey Department of Environmental Protection’s Source Reduction/Resource Management/Sustainability award.
Domino Park Installation
Domino Park is a 5-acre public park — built on the site of the former Domino Sugar Refinery — located along the East River in Williamsburg, Brooklyn (NY). In June 2020, the privately operated park began accepting source separated organics — including fruit, vegetables, garden waste, bread, and coffee grounds — from neighborhood residents for composting. Previously, residents in this north Brooklyn neighborhood could drop their food scraps at North Brooklyn Farms, but the farm’s lease ended in late 2019. Then, due to the pandemic, the New York City Department of Sanitation closed its household food scraps drop-off sites on May 4, 2020.
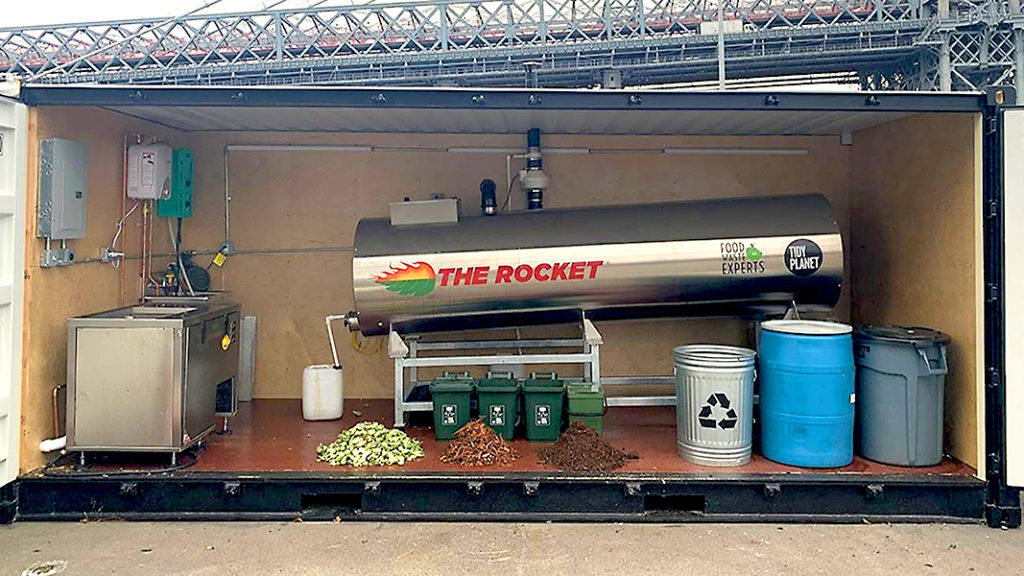
The composter at Domino Park is housed inside a 20-foot container. Residents in the neighborhood can drop off their food scraps, which are processed along with source separated organics and yard trimmings collected in the park.
Food scraps can be dropped off during set hours on Mondays and Thursdays. Domino Park had procured an A900 Rocket composter in October 2019 to compost separated organics generated in the park. Having the unit facilitated accepting food scraps from residents. The composter is housed inside a 20-foot container. Domino Park uses a Waste Station waste pulper as a pretreatment/volume reduction step before adding the food scraps to the unit. After 14 days, material is discharged. Once the finished compost is cured for about three weeks, it is used on the park’s green areas as well as offered to drop-off program participants. The educational component is significant as individuals dropping off food scraps can see how the closed loop process works — from raw scraps to finished compost. About 200 tons of food scraps have been composted since the composter began operating in October 2019.