Top: Trenton Biogas processes commercial, municipal, industrial, and agricultural food waste streams in the facility’s digesters. Photo courtesy of Trenton Renewables
Nora Goldstein
The Center for EcoTechnology’s (CET) Northeast Anaerobic Digester Accelerator (NADA) is a two-year project supported by the U.S. Environmental Protection Agency’s (EPA) Funding to Support Anaerobic Digestion in Communities. The NADA project includes development of resources and training documents for source separation and diversion of commercial and institutional food waste to digesters in the Northeast states. CET is a national nonprofit organization that helps people and businesses save energy and reduce waste.
CET was among 12 project proposers selected by EPA in October 2020 to receive grants from a pool of roughly $3 million. The EPA program was designed to help reduce food loss and waste and to divert food waste from landfills by expanding anaerobic digestion (AD) capacity in the United States. The project types selected for funding included feasibility studies, demonstration projects, as well as technical assistance and training. CET was selected by the EPA to receive a grant for the NADA project and over the past two years, has worked with government agencies, haulers, food businesses, trade associations, and other entities in New England and the Mid-Atlantic to provide technical assistance, training, and capacity building that will develop and disseminate AD resources.
Food Waste Digestion Insights
As part of NADA, CET hosted a series of meetings for organic waste haulers across the Northeast and Mid-Atlantic to get their perspectives on the challenges and opportunities to hauling organic material in the region. Haulers heard from their peers as well as local representatives, provided feedback and input into the meeting agendas, and shared their insights. CET also worked with communities such as Cambridge, MA and Middletown, CT on their source separation programs for AD, which included creating a training video for Middletown’s Feed the Earth initiative with Blue Earth Compost. BioCycle Connect, LLC was contracted by CET to work on several NADA resources — a guidance outlining source separation practices to implement when diverting food waste to AD, and “Food Waste Digestion Insights,” which discusses AD fundamentals, and provides examples of service providers — haulers and food waste preprocessing and digester facilities — in the Northeast states. This article is based on excerpts from “Food Waste Digestion Insights.”
A number of anaerobic digesters in the Northeast have been developed or retrofitted to process food waste from institutional, residential, industrial and agricultural sources. In some cases, this infrastructure enables generators of food waste to comply with state disposal bans. There are stand-alone, commercial digesters that process only food waste and codigestion facilities on dairy farms and at wastewater treatment plants. The majority of these digesters accept all types of food waste (vegetative, meat/fish/dairy, pre and postconsumer streams, etc.), and rely on revenues from tipping fees and the increased production of biogas as profit centers, and to offset capital and operating costs.
AD technologies fall into two basic categories: wet and dry. An easy distinction is that any feedstock going into a wet digester must be “pumpable,” whereas material going into a dry digester is “scoopable” using a front-end loader bucket. Currently, there are only wet digestion systems operating in the Northeast states. The region’s several food waste-only facilities including Quantum Biopower in Southington, CT; Rhode Island Bioenergy Facility in Johnston; Trenton Biogas in Trenton, NJ; and the new BioEnergy DevCo plant in Jessup, MD. The other food waste-to-AD facilities in the region are located on dairy farms or at wastewater treatment plants.
Solution Provider Examples
To develop the source separation guidance and Insights resources for the NADA project, input was sought from AD facility operators, organics haulers, and food waste preprocessors about services provided, experience working with various types of generators and food waste, and recommended source separation practices. The business models vary (e.g., collection only vs. AD only) but other factors are consistent among the different operations. For example, digester operators interviewed have variable tip fee pricing, based on factors such as biogas potential of a feedstock (e.g., FOG has high biogas potential), longevity of the contract with the generator, quantity of material to be diverted, and whether the feedstock requires preprocessing or is a liquid feedstock from a single generator that is homogenous and consistent and can be unloaded directly into a storage tank that feeds the digester.
The descriptions below are only a sampling of the solution providers and their business models in the Northeast. Information was culled from interviews as well as BioCycle articles.
Hauler Only
Natural Upcycling, a food waste/organics collection company based in Linwood, New York, services states in the Northeast down to the District of Columbia and northern Virginia. Customers include restaurants, grocery stores, hospitals, universities/schools, cafeterias, food manufacturers, and food distribution centers. Upwards of 100,000 tons/year of food waste are collected. About 75% is recycled via AD and about 25% is composted, fed to animals, or land applied. As a hauler, having food waste that is not contaminated or packaged provides Natural Upcycling more options for where the material can be taken for recycling.
Collection, On-Site Preprocessing And AD
Exeter Agri-Energy, and its sister company, Agri-Cycle, are subsidiaries of Stonyvale Farm in Exeter, Maine, a dairy farm with 2,000 cows. Agri-Cycle provides organics collection throughout New England, servicing commercial and institutional generators. They accept packaged materials as well as source separated food waste. Collected organics are hauled to Stonyvale Farm where Exeter Agri-Energy utilizes a Scott Equipment Turbo Separator depackaging unit to separate out the packaging and contamination, and create a slurry, which is codigested with dairy manure. The biogas is used to generate electricity, and the digestate is recycled for use as animal bedding and fertilizer. The depackaging capability at the digester lessens the requirement for source separation by the generators that Agri-Cycle services.
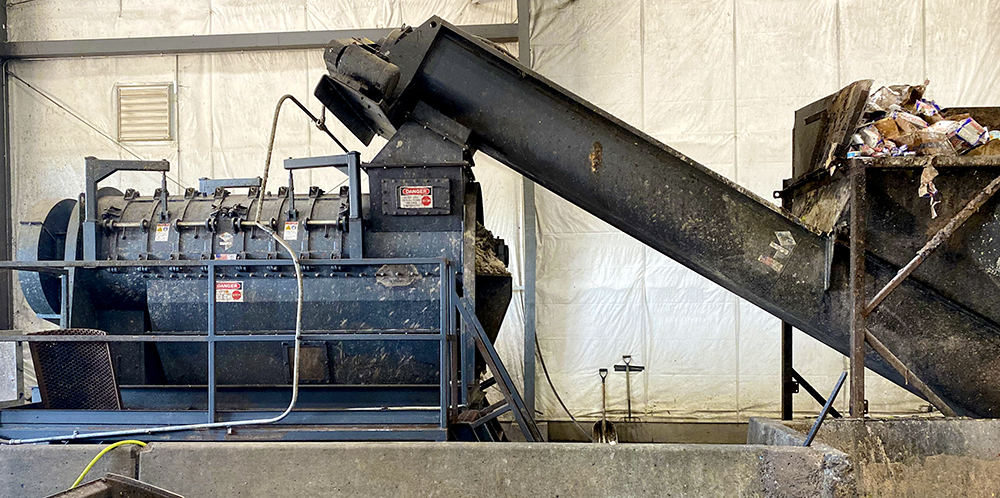
Reinford Farms processes off-spec or out-of-date packaged food in a Scott Equipment Turbo Separator.
Reinford Farms in Mifflintown, Pennsylvania operates an 800-head dairy farm. Its two digesters have capacity to codigest 25,000 tons/year of food waste from clients such as distribution centers, cold storage warehouses, and food manufacturing facilities. The majority of food waste received is in packaging — much of it hauled to the farm by Reinford in its trailers that are parked at the generators’ locations. It also utilizes a Scott’s depackager, and generates electricity with the biogas produced. Digested solids are used to bed the dairy cows and the separated liquid is applied to cropland managed by Reinford Farms.
Collection And Preprocessing
Waste Management (WM) operates three CORe food waste preprocessing facilities (CORe is WM’s proprietary food waste processing system) in the Northeast, located in Boston, New York City, and Elizabeth (NJ). Haulers, including WM, bring food waste to the CORe facilities where it is processed into an “engineered bioslurry” that is transported to wastewater treatment plants for codigestion with biosolids. An example is the CORe facility in Boston, which processes residential and commercial food waste, and then hauls the bioslurry in tanker trucks to the Greater Lawrence Sanitary District (GLSD) in Andover (MA) where it is codigested with wastewater solids. The biogas is used to generate electricity for the plant’s operations; the digested solids are pelletized and recycled.
Off-Site Preprocessing, On-Site AD
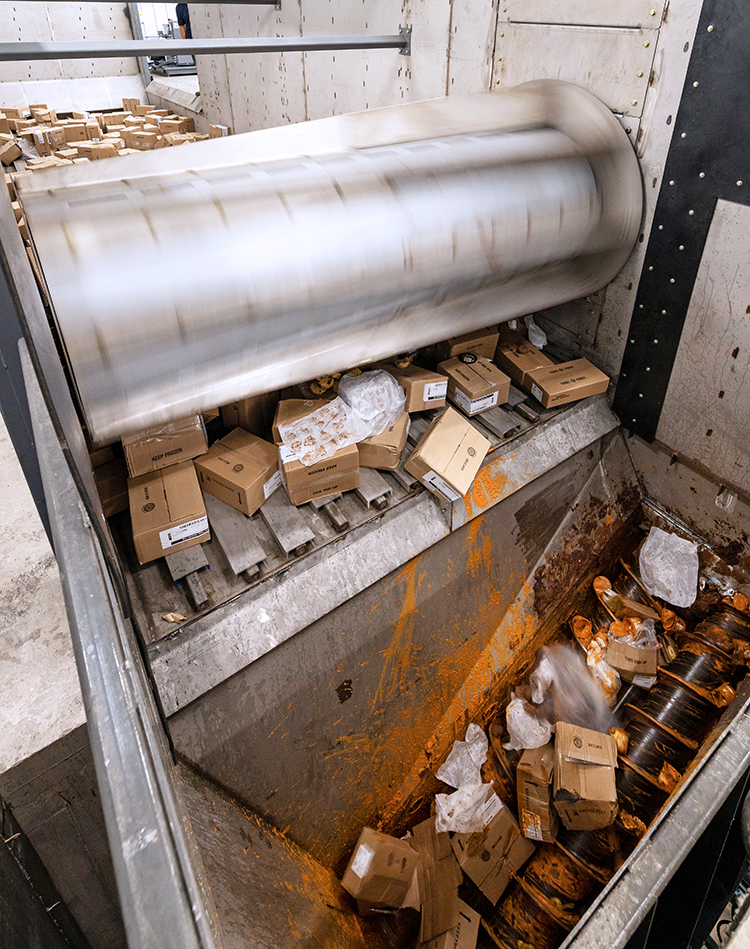
The KEITH Walking Floor at the Agawam ORF maintains a consistent flow of material into the twin-screw hopper of the Turbo Separator. Photo courtesy of Vanguard Renewables
Vanguard Renewables, a digester developer based in Wellesley (MA), builds, owns and operates ADs on dairy farms in Massachusetts and Vermont that codigest food waste supplied by Vanguard with the farm’s manure. The dairies receive a lease payment and utilize free heat recovered from the engines that combust the biogas into electricity, as well as fertilizer and bedding material for the cows.
In 2020, Vanguard opened a fully enclosed organics recycling facility in Agawam (MA) where it receives packaged and unpackaged food and beverage waste, which is processed in a Scott’s depackager that is fed by a KEITH Manufacturing Walking Floor. The slurried food waste is hauled in tanker trucks to farms in Massachusetts and Vermont with Vanguard digesters. The farms in Massachusetts generate electricity from the biogas; the farm in Vermont produces renewable natural gas (RNG), a fossil gas equivalent, that is injected into Vermont Gas System’s pipeline.
On-Site Preprocessing And AD
A common configuration for AD facilities processing food waste on-site is to receive the feedstocks inside a building or enclosed area where it is tipped, inspected for obvious contamination, and then loaded into a depackager or a hopper that feeds a preprocessing line (including depackaging). Examples of facilities with this configuration include:
Trenton Biogas in Trenton (NJ), operated by Trenton Renewables, has capacity to process 400 tons/day of commercial, municipal, industrial, and agricultural food waste streams in the facility’s digesters. Haulers unload directly into hoppers installed below the floor level. Food waste goes through crushers, screens, and magnets to prepare it for depackaging. After depackaging a refinement step separates out glass and other hard, dense material in the slurry before loading into the digesters. Biogas is used to generate electricity and heat; solids separated from the liquid digestate are cured and refined for use as soil amendments.
BioEnergy DevCo’s new food waste AD facility in Jessup (MD) is co-located with the Maryland Food Center, one of the largest wholesale produce terminals on the East Coast. The plant has capacity to recycle 110,000 tons of organics annually to produce RNG for energy and 16,575 tons of soil amendment for agricultural and other land use. Feedstocks accepted include all types of food waste, FOG, and industrial food and beverage processing residuals. Liquid wastes are pumped directly into a storage tank. Solids are unloaded onto an enclosed tip floor and then pushed with a loader into a feeder pit that contains two large hoppers. The hoppers are equipped with triple augers that crush the feedstocks, including packaging, and move them to a depackaging unit. These organics are digested. After biogas conditioning, the RNG is injected into the Baltimore Gas & Electric pipeline.
The City of Hermitage (PA) Municipal Authority operates a Food Waste to Energy and Wastewater Reclamation Facility (WRF). The City of Hermitage’s Organics Recovery Program at the WRF is operated as a complementary business that provides revenues and cost savings to support the Authority’s core mission — water quality. About 75% of incoming food waste is preprocessed in one of three depackagers. The plant codigests about 10,000 gallons/day of food waste — about 30% of its daily throughput. Revenues from tipping fees have averaged $150,000 to $200,000/year. Hermitage is able to produce sufficient additional biogas via codigestion for the facility to achieve energy neutrality (i.e., it runs the plant without any power from the grid). Digested biosolids (Class A) generated at the plant are land applied on nearby farms.
CET Resources
CET’s two-year NADA project concludes in Fall 2022. Resources and trainings developed for NADA are available on CET’s website. Additionally, CET can assist AD solution providers by:
- Training existing customers in proper source separation practices and/or developing educational materials for their customers to utilize
- Mapping specific food waste generators in an anaerobic digester’s service area
- Helping AD solution providers collaborate with local governments that want to initiate and/or expand food waste recycling programs