Top: Photos courtesy Champion Waste & Recycling Services
Nora Goldstein
Champion Waste & Recycling Services (Champion) in Dallas, Texas opened a food waste composting facility in October 2022. Champion is a hauler as well as an owner/operator of a materials recovery facility (MRF) for commercial recyclables, construction debris (C&D) and wood waste/land clearing processing operation, and the composting site. “My wife and I are third generation in the waste and recycling industry in north Texas and have always seen food waste diversion as something that needed to be addressed, including the packaged food side of things,” notes Paul Kuhar, Champion’s Vice-President. “We have built our company to be vertically integrated. Our hauling division collects the materials that we want to divert from the landfill and our post collection processing facilities create the end products for various markets.”
Champion has been hauling food waste since 2008 and tipping it at several small composting facilities and one company with larger sites that compost green waste with preconsumer vegetative food waste. “In the early days, we primarily focused on food manufacturing waste that is clean with little to no contamination,” adds Kuhar. “The facilities we were tipping at have a very low threshold for contamination.”
Gradually, the company began collecting food waste from a broader range of customers, including hotels, grocery stores, restaurants, food distribution hubs, and chains such as Chipotle and Starbucks. To better service this wide variety of food waste generators, Champion needed a composting facility that could accept pre and postconsumer food waste, along with compostable packaging. “We decided to permit one of our existing sites to house a food waste composting facility,” says Michelle Kuhar, Champion’s President. “The site is where we process wood to make mulches and biomass fuel. We hired SCS Engineers to design and permit the facility, which has capacity to compost about 400 tons/day of food waste along with green waste. It’s a 62-acre site with another 40 acres available for expansion.”
Collection And Preprocessing
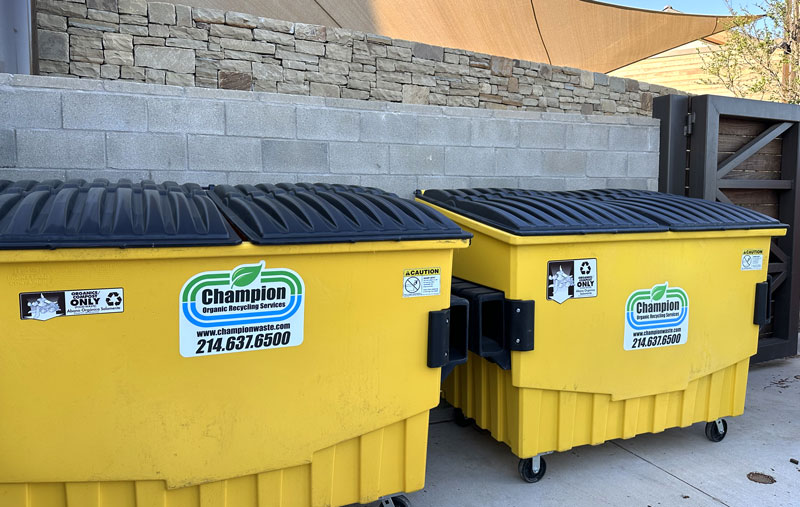
Customers use 96-gallon carts and/or 1-, 2- and 3-cubic yard double walled plastic bins for food waste.
Champion Waste uses specially designed, rear-loading rendering truck bodies for food waste collection. Customers are offered 96-gallon carts and/or 1-, 2- and 3-cubic yard double walled plastic bins. It will service any customer producing food waste, “from large-scale to small mom and pop.” In some cases, Champion also collects trash and recycling from the customer, but will provide only organics service if desired. “Food waste collection is more expensive than what these businesses are paying for trash, but many recognize the environmental benefit of not putting the organics in the landfill,” explains Paul Kuhar. “But separating out the food waste often reduces the frequency of trash collection, which offers a savings. For some customers, food makes up the largest component of their trash stream.”
When designing the facility, the Kuhars wanted the capability to accept packaged food waste that couldn’t be sold or donated, or that had spoiled because the power went out or the coolers broke down. It purchased a Tiger depackager that is housed in the composting facility’s fully enclosed receiving building. It also uses the unit to process loads that may be commingled with conventional plastic packaging. “Sometimes it’s used when we get clean feedstocks, such as fresh cut vegetable trimmings or soup, to create an oatmeal-like slurry that is turned into fresh piles of ground green waste,” says Paul Kuhar. “In other cases, when a load is 100% food manufacturing waste, it is added directly to the windrows and mixed in with the turner.”
He adds that all incoming loads are inspected for contamination on the tipping floor. Contamination, especially glass, is documented. “Green waste is primarily where we see the contamination, such as black plastic bags of leaves in the middle of the load.”
The composting site accepts certified compostable foodservice ware. Loads with those feedstocks do not go through the depackager, which removes it along with other non-food packaging material or contamination. Instead, operators divert those loads directly to the windrows, where they are incorporated with the windrow turner — unless there is noticeable contamination from non-compostable feedstocks.
On America Recycles Day, Champion launched a residential food waste drop-off subscription service. “We researched various approaches to offering residential collection, and opted for the subscription model,” notes Michelle Kuhar. “We are doing a lot of outreach and education, and messaging on social media. Initially, only food waste will be accepted to minimize the potential for contamination. The program kicked off with one drop-off location targeting the surrounding areas in Collin, Denton, and Grayson counties, which are north of Dallas. “We will be launching two more drop-off locations in 2024,” she adds.
Composting, End Markets
Composting is done in turned windrows. To meet pathogen destruction requirements (PFRP), the piles are turned five times over 15 days. Once PFRP has been achieved, operators probe the windrows in eight different locations daily, Monday to Friday. The temperature readings help determine the number of times the rows will get turned after the initial 15 days. Total retention time on the pads is 12 weeks. Material is then moved into static piles for four weeks before screening.
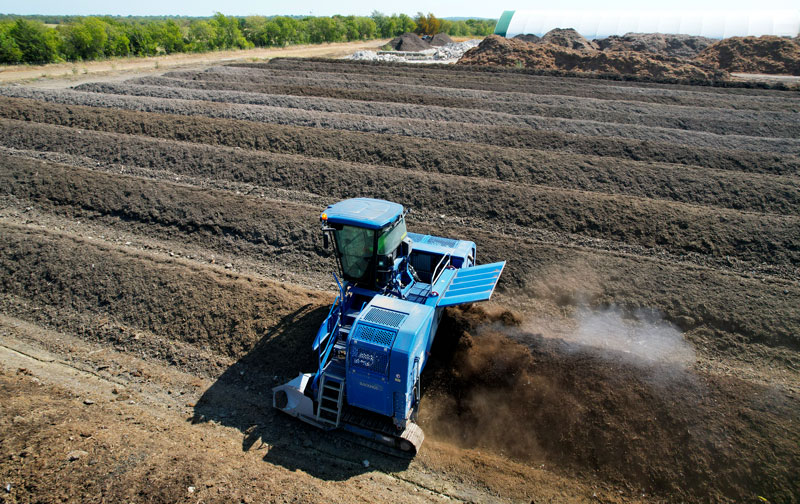
The 62-acre site has capacity to compost about 400 tons/day of food waste along with green waste.
The compost is screened using a trommel and sold in bulk and in bags for landscaping and turf applications to landscapers, nurseries, and homeowners. Compost retail yards have been set up at Champion’s three processing locations (the MRF, C&D site and the composting facility). Bulk purchases are delivered by Champion.
Champion has been making biochar for about two years from nondimensional lumber and green waste using a ROI Carbonator 500. “We use it in our compost blends and also sell it as a soil amendment,” says Paul Kuhar. “It fits in well with both our wood waste recycling and composting operations.”