Top: McGill’s fully enclosed composting facility in Fairless Hills (PA) has capacity to process 170,000 tons/year. Photos courtesy McGill Environmental Systems of NC, Inc.
In March, I had the opportunity to tour McGill Environmental Systems’ newly built, fully enclosed composting facility in Fairless Hills, Pennsylvania — before the doors opened for business. The interior concrete (a total of 9,060 cubic yards over 3 acres were poured) was white and pristine, awaiting the first loads of biosolids and food waste. Fast forward six months, and McGill’s Fairless Hills composting facility is in operation. Its annual capacity of 170,000 tons includes 130,000 tons/year of a range of organic wastes, and 40,000 tons/year of amendment, including yard trimmings and wood chips. About 80,000 to 100,000 cubic yards/year of premium compost and soil products are expected to be manufactured.
The 15-acre site — close to Trenton, New Jersey, and about 25 miles northeast of Philadelphia — is housed on WM’s Warner property; McGill has a long-term lease with WM for the property, and is composting yard trimmings and biosolids brought in by WM. State and local permitting for the facility took almost three years. McGill has contracts with wastewater treatment plants to receive their biosolids. It also contracts with food waste generators in the tri-state area that includes Pennsylvania, New Jersey and New York. “We primarily receive preconsumer commercial and institutional food waste, along with some industrial food processing residuals,” notes Noel Lyons, McGill’s cofounder and president.
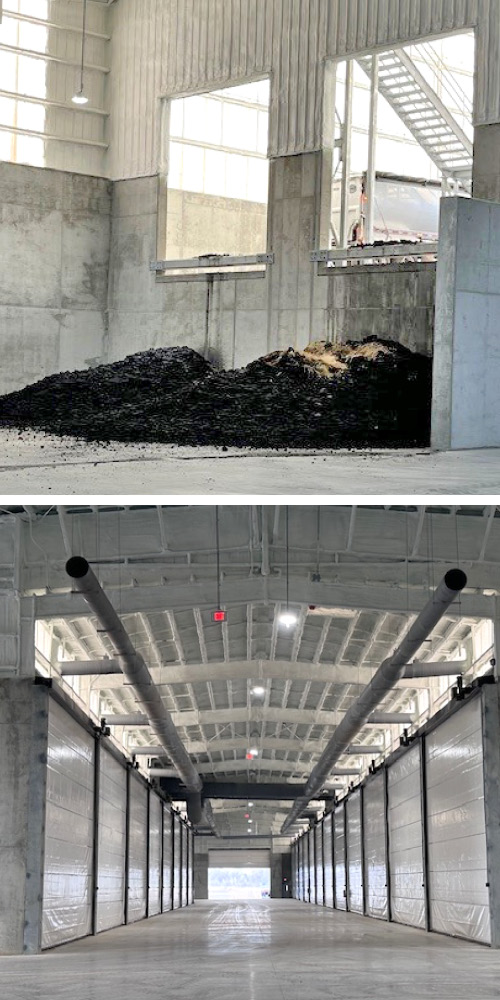
Incoming feedstocks drop into a receiving area below the tip floor and are mixed with amendment (top). Once blended, material is moved into one of 13 aerated bays for the primary composting phase (above).
Trucks unload in a fully enclosed tipping building. Incoming feedstocks drop down into a receiving area, where they are mixed with amendment. After unloading, trucks are washed out and, in some cases, will proceed to the end product storage area to get loaded with compost. The facility has 20 modular aerated bays; 13 are primary (active composting) and seven are used for curing. Each bay is equipped with vinyl doors. More bays can be added in the future as needed. The interior concrete floor design allows for easier cleaning of aeration piping. The floors are sloped in different ways throughout the building to ensure no process liquid leaves the building — an important design for storm water permitting.
Variable fan drives control aeration based on continual temperature feedback. “The constant adjustment of the fans based on the temperature feedback is integral to accelerating the composting process and is why we can compost large volumes on a small footprint,” explains Kate Sullivan, project manager at McGill. “We meet PRFP (Process to Further Reduce Pathogens) quickly and typically keep material at 131°F or above for about eight days for the initial processing. Then the material is screened. Overs are returned to the front-end for use as amendment. The fines go through approximately 15 days of curing, followed by final screening.”
The enclosed facility has three miles of air ducts, adds Lyons. Two biofilters, each 80-feet by 100-feet by 6-feet, treat process air. Coarse wood chips are used for the media. An electric-powered screen is at the end of the processing line inside the building. After screening, material is moved to a covered area that can store up to 15,000 cubic yards of compost. End markets include landscaping, turf and athletic fields, engineered soils for storm water management and erosion control, and agriculture.