Top: Compost made by Caldwell’s, Inc. is spread (right) on corn and soy bean fields then incorporated with a vertical tiller (left). Photos by Aleigha Simerly
Caldwell’s, Inc. in Morristown, Indiana — about 20 miles from Indianapolis — is a multi-faceted environmental services company that includes hauling and transfer stations, farming, and a food and agricultural waste composting facility on a 1,500-acre family farm. The origins of Caldwell’s, Inc. are described in a 2021 BioCycle article. Jordan Caldwell, the great grandson of Elmer Caldwell who started the company as a gravel pit operation in the 1940s, decided to open a food waste composting business focused on processing industrial and food processing streams in 2019 on farmland he purchased from his father. It took about a year to obtain a land application permit — which covers an industrial composting facility — from the Indiana Department of Environmental Management, and the facility opened for business in April 2020. The permit allows any material that is food or derived from food to be accepted. Other nonhazardous industrial organic wastes need to be approved by the state, which is about a two-week process. There is no limit on the quantity of food waste the facility can receive annually.
The original active composting pad was about 3-acres. It had 2 feet of compacted clay, with a soil-stabilized surface to provide year-round access. The facility was sized to accept 5,000 to 10,000 tons/year of industrial food waste. Fast forward to 2024: the composting site now has a 4-acre concrete active composting pad that “is full 100% of the time,” says Jordan Caldwell. “The composting site is zoned for 109 acres. We originally used 2 acres and now are using 20 acres. The quantity of incoming feedstock has tripled in the past three years since the original BioCycle article.”
In addition to composting, Caldwell raises livestock and grows corn and soybeans. Incoming food waste is mixed with horse manure, corn shuckledge, wood chips and finished compost. “After we harvest the corn, we use a combine with a cutter head to cut the stalk to about a 6-inch stub,” he explains. “The shuckledge blows out the back of the combine. It gets raked up and we use it for bulking agent. The wood chips are from transfer stations we own. We separate out the clean, untreated wood that comes in. We use a Vermeer grinder to make the wood chips.”
Composting is done in turned windrows. Material stays on the composting pad for 6 to 8 weeks, after which compost is moved into Quonset huts where it cures for an additional 30 days. All of the compost produced is used on 3,000 acres of cropland that Caldwell’s, Inc. cultivates. Originally, the compost wasn’t screened prior to field application. Now it is processed through a trommel screen to remove larger pieces of wood, nails and other contaminants, and to “make the compost fluffy, which is beneficial when we apply it to the fields,” says Caldwell. “If a field has never received compost, we apply 5 tons/acre the first year, then four tons/acre the following year. After that, 2 tons/acre are spread as a maintenance application. We are a no till farm, and use a vertical tiller to work the compost into the soil.”
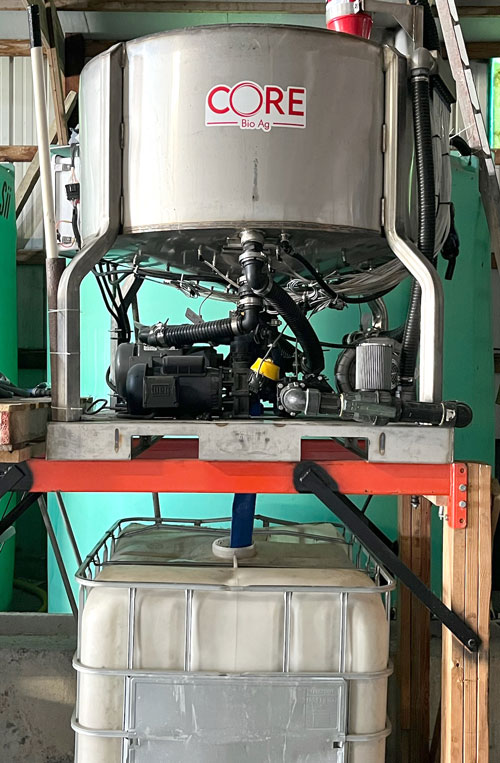
Compost extract, which is used as a starter fertilizer in the planter, is made by putting compost in a vat with water for about 20 minutes.
The farm also makes compost extract, which is used as a starter fertilizer in the planter. To make the extract, compost is put in a vat with water for about 20 minutes. “The extract makes the seed think it is in super rich ground, which helps with faster root penetration,” adds Caldwell. “This has enabled us to cut out all of our synthetic starter. I was nervous the first year we transitioned, but the extract held its own. The yields never dropped, and we saved $100,000 this year by not buying the synthetic starter. Overall, our corn and soy bean yields have gone up by 20%, and we’ve reduced our use of synthetic fertilizer by 30%.”
In 2021, Caldwell’s, Inc. purchased a T-30 Scott Equipment depackager to process packaged food and drinks. The organic slurry is a combination of dry and liquid material, depending on what is being processed. “When the slurry is pumped out of the pit, it passes through a filter to remove contaminants,” he explains. “Then it is blended into the windrows. Employees also pull visible contamination out of the windrows.” Another division of the company, Caldwell Environmental, specializes in doing industrial cleaning at food manufacturing plants. That involves cleaning out tanks and pits that are used for food storage. The contents are brought back to the farm for composting.
The most recent development, notes Caldwell, is installation of an anaerobic digester. It will process food waste and horse manure. Solids will be separated out of the digestate and composted; the liquid will be land applied as a fertilizer. “I got the composting facility rezoned from agricultural to industrial, and obtained an exception to produce renewable natural gas (RNG) at the facility,” he says. “Construction will begin in 2025. There is a Trans Canada pipeline about two miles away. The RNG will be directly injected.”