Adequate air delivery and distribution are keys to an optimized composting process. In forced air systems, the aeration floor is a key element of that optimization. Part I
Craig Coker and Tim O’Neill
BioCycle June 2017
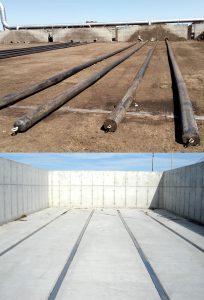
The most common type of aeration floor is a Pipe-On-Grade Sparger (top). In-floor type aeration floors (bottom) are almost always cast in concrete and provide a flat working surface.
Active composting is an oxygen consuming, heat generating process primarily carried out by aerobic bacteria. Temperatures in energetic composting piles will rise rapidly and remain at levels that can inhibit these aerobes, slowing stabilization and increasing odor emissions.
There are two fundamental reasons that high temperatures inhibit efficient composting. First is the fact that high temperatures reduce the supply of oxygen to the aerobic bacteria, which require water, nutrients and oxygen to do their work. These conditions exist in the liquid film that surrounds the particles in a compost pile with adequate moisture (Figure 1). Oxygen, supplied to the free air space, must dissolve into this liquid film so the aerobes can respire. The solubility of oxygen in water goes down as temperatures go up — as they tend to early in composting process when the need for oxygen is highest (Sauer, 2013). In field studies, the authors of this article have measured a clear positive correlation between oxygen saturation levels in the liquid film layer and stabilization rates and odor control.
The second reason is that temperature determines the class of microbes that predominate in the composting process. The two classes of interest in active composting are mesophiles (moderate temperature loving) and thermophiles (high temperature loving). It has been well documented in peer-reviewed literature (Sundberg, 2005; Sundberg and Jonsson, 2008; Sauer, 2013) that when mesophilic temperatures are achieved early in the composting process, the pH rises to above 6 (a key performance indicator), nitrogen is more readily converted to nitrates, odor emissions are drastically reduced, and the rate of bio-oxidation of organic matter increases markedly.
On the other hand, when temperatures rise to, and are maintained in, the thermophilic range the opposite is true. Fortunately, composting is a robust process. A composting pile can spend a few days at the beginning of the active phase at elevated temperatures before it is cooled down to more mesophilic friendly temperatures without causing undue inhibition to the process or emitting unmanageable odors. It should not, however, spend weeks at thermophilic temperatures. Fortunately, temperature is the easiest composting parameter to measure.
Forced Aeration Floors
Prolonged elevated temperatures are an indicator of inadequate pile aeration. Forced aeration, using either the aerated static piles or windrow methods, is one approach to supplying oxygen to the composting process. A key element in a forced aeration system is the aeration floor. It serves as the primary working surface, and distributes air through the compost pile. Keeping the aerobes working efficiently requires that the aeration floor must uniformly and reliably supply enough air to match heat production in the pile.
Aeration floors can be designed to drain away excess water. Mixes with significant food waste content tend to release large volume of leachate early in the process. In addition to being acidic and odorous, this liquid tends to occupy the pore spaces, shown in Figure 1, near the bottom of the pile. This inhibits airflow through, the supply of oxygen to, and removal of gasses from, the free air space. A well-designed aeration floor will serve to efficiently drain off and capture leachate to reduce excess moisture.
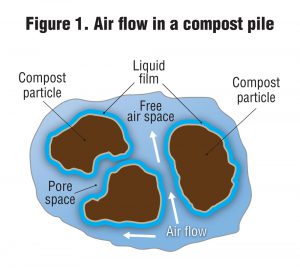
Figure 1. Air flow in a compost pile
Aeration systems come in three basic types: positive, negative or reversing (which alternates between positive and negative). Positive aeration refers to a system where air is forced out of the floor into the material. Negative aeration refers to a system where air is drawn into the floor from the material. Each has its strength: positive aeration is the simplest to implement; negative aeration has the highest air emissions and leachate capture efficiencies; and reversing aeration provides the most uniform conditions throughout the depth of the pile.
There are many variations of aeration floors, but they can generally be organized into the following groups: On-Grade versus In-Floor, and Sparger versus Low Friction.
By far the most common type of aeration floor is a Pipe-On-Grade (POG) Sparger. This aeration floor consists of a series of pipes with a designed series of perforations placed on top of the working surface and connected to an aeration system. These pipes are generally pulled from under the pile before it is broken down, then replaced and reconnected prior to building a new pile. A pipe is a sparger if it uses high back pressure across the orifices to overcome the pressure loss along the pipe and thus get semi-uniform air distribution along the length of the pipe.
In-floor type aeration floors can be either sparger or low-friction. In either case they are almost always permanently cast in concrete and provide a flat working surface that does not interfere with the wheel loader or require regular operator intervention. An aeration floor is low-friction if it relies on a balanced low pressure design to distribute air uniformly. Low-friction aeration floors require only 25 to 50 percent of the fan horsepower required for the same air flow from a sparger floor, but they are somewhat more expensive to build.
Quality Control Management
In quality control management, measuring is the first step. Key process indicators to measure for managing composting process quality are well established. These standard indicators are summarized in Table 1, which includes the addition of a “BMP Scale”. This scale refers to how closely the conditions in the pile comply with the Best Management Practices value for each of these indicators. As the indicators move toward a score of “10” the biology in the pile becomes optimized and biostabilization becomes more efficient and odor emissions diminish. As it moves more towards “0”, the facility will require a very odor tolerant location and lots of area to allow maturation of the final product over an extended period of time.
The first four BMP compliance indicators listed in Table 1 are largely determined by the effectiveness of the forced aeration system in general, and by the aeration floor in particular. The bottom two indicators, C:N ratio and density, are a function of the mix quality (see sidebar). How close to scores of “10” a composting facility needs to be successful depends on a range of factors. Most failed facilities have low scores in most categories. Insufficient aeration is one of the most common underlying factors.
Adequate aeration early in the composting process impacts the whole life cycle of the compost produced. Sunberg’s research showed that using high aeration rates to control temperatures early in the active part of the composting cycle provided significant benefits to stabilization, odor control, and nitrogen conversion that endure beyond primary composting. This means that compost curing can be done effectively with little process management if primary composting is highly BMP compliant.
Maintaining BMP parameters is not a static activity. A compost pile is a highly dynamic microbial system with constantly varying rates of oxygen consumption/heat production. Ideally the aeration system will match these dynamics by varying the amount of cooling air delivered to hold temperatures near a series of operator selected setpoints. Typically the first temperature setpoint needs to be high enough to achieve pathogen control (PFRP, >55°C for 72 hours), followed by a lower temperature setpoint that is more conducive to mesophilic bacteria.
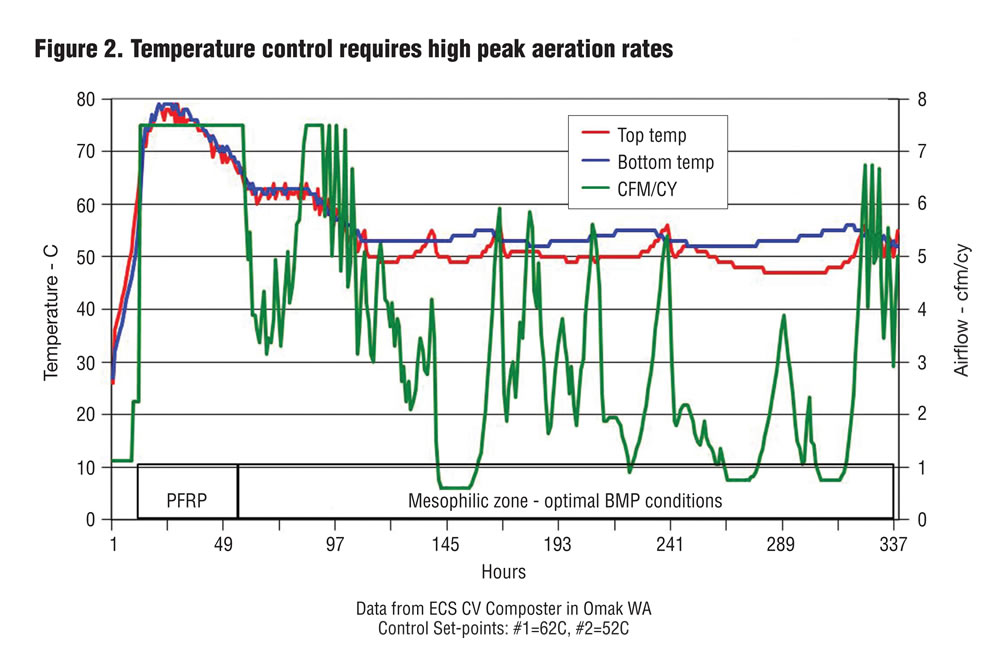
Figure 2. Temperature control requires high peak aeration rates
Figure 2 is a graph of temperature and airflow rate versus time (airflow rate is measured in cubic feet per minute per cubic yard of pile volume, or cfm/cy). This is an example of an aeration system with a wide range of aeration rates and an adaptive temperature-feedback control system that responds to variations in heat generation rates. The control system is based on two temperature setpoints: an initial setpoint of 62°C and a second setpoint at 52°C. This data is from a 40-cy insulated vessel that composts a blend of biosolids and fresh deciduous wood chips. As temperatures exceed the initial setpoint of 62°C in less than 12 hours, the control system turns up the airflow (green line) to the peak rate of 7.5 cfm/cy. It takes another 40-plus hours to bring the temperatures down to the initial setpoint. Once PFRP is achieved, airflow is again automatically increased to bring the temperatures down to the second setpoint of 52°C. Thereafter the aeration control system responds to sudden and unpredictable changes in heat generation, sensed as small temperature changes, by rapidly varying the aeration from a low of 0.5 cfm/cy to peak rate of 7.5 cfm/cy. This dynamic control both limits high temperatures and avoids over-cooling.
If adequate air is supplied for cooling, then there is a surplus of oxygen. Typically, ten times as much air is required for cooling as is required to provide oxygen. In a well-aerated system the oxygen is always greater than 15 percent (normal oxygen content of air is 21%). For example, the measured oxygen concentration in the exhaust stream from the vessel in Figure 2 was consistently in excess of 18 percent.
Part II of this article will examine aeration floor design options and how they impact BMP process performance indicators, operations, and economics.
Craig Coker is a Senior Editor at BioCycle and CEO of Coker Organics Recycling (www.cokercompost.com) near Roanoke VA. He can be reached at ccoker@jgpress.com. Tim O’Neill is the President of Engineered Compost Systems (ECS), an compost technology provider based in Seattle, WA. He can be reached at Tim@compostsystems.com.