Top: Raw biogas is piped to a conditioning system at a farm digester in Vermont.
Sara Martin and Craig Coker
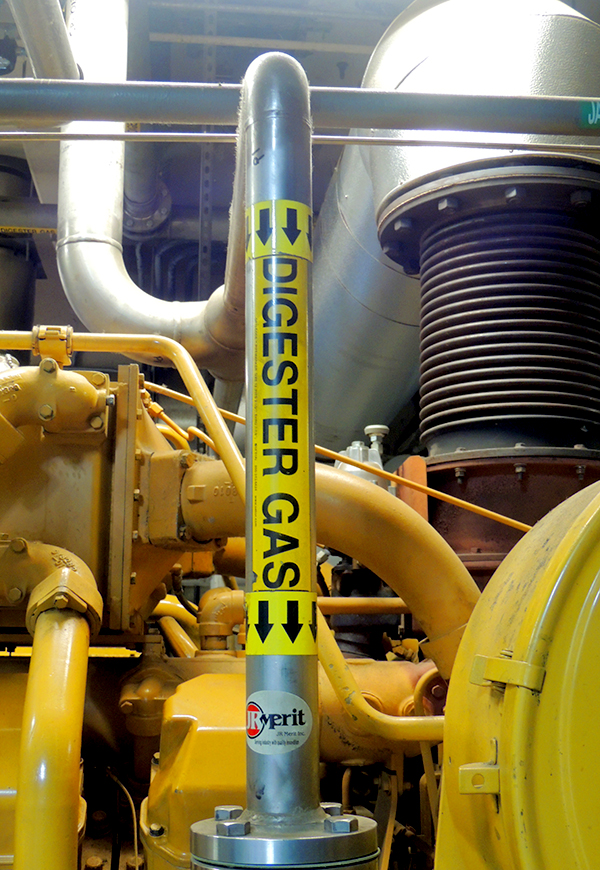
Biogas contains hydrogen sulfide (H2S) and mercaptans that can condense in the form of weak sulfuric acid within the headspace and piping causing rapid corrosion with incompatible materials.
Biogas is primarily composed of methane (CH4) and carbon dioxide, and it contains small amounts of hydrogen sulfide, ammonia, volatile organic compounds, water vapor, and other substances. In certain concentrations, some of these gases may be flammable, explosive, toxic, or asphyxiating. According to U.S. EPA AgSTAR’s Anaerobic Digester/Biogas System Operator Guidebook, “CH4 is combustible with air at concentrations between 5% and 15%, known as the lower explosive limit (LEL) and the upper explosive limit (UEL), respectively. Biogas systems typically produce CH4 concentrations in the range of 45% to 70%, and introducing air into the biogas handling system could bring the CH4 concentration into the explosive range, presenting risk of an explosion in the presence of an ignition source.” Hydrogen sulfide is a toxic gas that can cause severe health effects or death. Adequate safety procedures are necessary to protect workers and equipment.
Two articles in 2016 in BioCycle addressed biogas safety concerns and strategies to assess and minimize risks (see References for links). The first, “Health and Safety Planning In Anaerobic Digestion” (May 2016), discussed how to create a Hazard and Operability Analysis (HAZOP) that addresses measures to avoid asphyxiation hazards, fire and explosion hazards, and accidental releases of biogas or digestate. The second, “Biogas Piping Design And Safety” (June 2016), provided guidance on biogas piping, storage and conveyance.
The June 2016 article provided biogas piping design guidance. This article is an excerpt of principles and practices covered in the guidance — from air entrainment to leaks.
Natural Gas And Biogas Distinctions
Design and safety fundamentals begin with a review of the property differences between natural gas and biogas. Natural gas piping can be operated at pressures much higher than biogas piping. There are many charts and guides for selecting the size of natural gas piping based on flow rate, temperature and pressure.
In comparison, biogas piping prior to conveyance (with a blower, compressor), or gas storage, is considered low pressure piping and is designed differently. The piping is typically sized to use the pressure of the anaerobic digester to “push” the biogas to the conveyance system and avoid pulling biogas out of an anaerobic digester at a faster rate than it is produced (and consequently, risk letting in undesirable air). Since most anaerobic tank vessels, storage systems and covers have physical limitations to hold high pressures, a majority of the biogas piping from these reactors operate at pressures slightly above atmospheric pressure (14.7 pounds per square inch (PSI)) from the reactor to the conveyance system. Landfills operate similarly to avoid pulling a vacuum on the headspace.
Design Guidance
The properties of biogas make design of this piping crucial to protect from the following hazards that can occur:
Air (Oxygen) Entrainment
Biogas piping, storage and conveyance systems need to be sized and controlled to avoid pulling a vacuum at any of the vent points within the system. If this occurs, air can get entrained within the biogas system. Biogas produced under sealed conditions is devoid of oxygen and is not explosive because the CH4 content is too concentrated to ignite (above the UEL of 15%). However, once air is entrained the CH4 content can be diluted within the explosive limit and will contain oxygen, creating conditions that, if exposed to an ignition source, could explode or combust.
Flow and pressure monitoring and switches prevent this from occurring. If these instruments sense the pressure decreasing past a critical point close to vacuum conditions, conveyance devices should be slowed down with variable speed control or a modulating valve and ultimately turned off to prevent further “pulling” of a vacuum on the system.
All drains and low point drip traps should incorporate an automated hydrostatic water level (like the p-trap in a sink drain) and the liquid trap maintained to prevent the pull of air in the system along the biogas piping. Adequately size the trap so it can drain under low pressure conditions. Routinely monitor and inspect these traps.
Flame/Spark Source
Anaerobic digester tanks, storage systems and landfills require vents to regulate pressure and prevent over pressurization and under pressurization of these systems from the biogas generation and conveyance, pumping, and other activities inherent to these systems. Because of this, there is an envelope around each vent that can contain the appropriate dilution of biogas with the explosive limit (5-15% methane) as well as oxygen. Exposure to a spark source near any of these vents could create an explosive condition.
Typical spark sources at digesters are lightning, cigarettes, tools (ideally nonelectrical spark-proof tools), flame torches (used to defrost piping), improperly rated electrical equipment (blowers/compressors/rotating equipment need to be spark-proof) and seal-offs, and even static electricity from clothing. Lightning protection, grounding measures and site safety plans for operations aid to mitigate spark sources. As an added protection, any vent areas should have conservation pressure/vacuum relief devices and flame arrestors to protect tanks, piping and storage systems from sparks. The pressure/vacuum relief devices will prevent escape of the tank headspace during normal conditions.
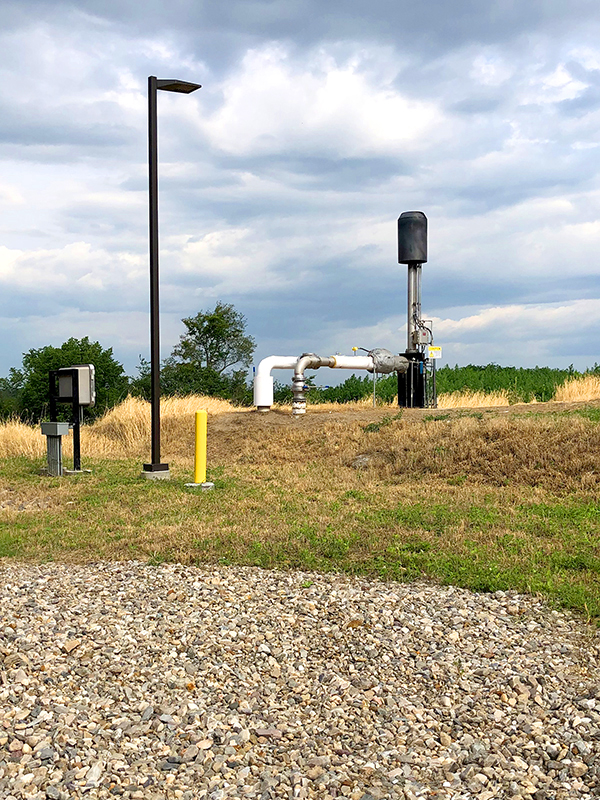
Any downstream spark sources such as the flare (above) need an additional flame arrestor (or flame trap) properly placed within the specified distance between it and the major piping system to prevent flashback within the piping system.
Flame arrestors or flame traps will help dissipate the spark source and/or a deflagration to prevent ignition of the remaining reactor headspace. Any downstream spark sources such as the flare, biogas blower or compressor, boiler, reciprocating engine, etc. need an additional flame arrestor (or flame trap) properly placed within the specified distance between it and the major piping system to prevent flashback within the piping system. These mitigation approaches also are applicable to ancillary vent systems where biogas will still be generated outside of the biogas piping system in potentially hazardous concentrations, such as anaerobic sludge holding tanks.
Moisture
Biogas is a completely saturated gas when it is released from an anaerobic digester, storage system or landfill. As this gas cools, the moisture condenses within the pipe and must be effectively and safely removed from the piping. If it is not removed, it can pool at low points restricting biogas flow. In small bore piping it can completely block flow and therefore passive piping smaller than 3 inches is not recommended except at drain points.
It is recommended that biogas piping have a minimum slope of 2% (or one-quarter-inch per foot per 100 feet of pipe). The initial drop of piping, points of pressure change, and/or major equipment should have a condensate/sediment trap for the higher rate of condensation that can occur at these points and to remove particulates that may be in the biogas. The condensation/sediment trap needs an automatic water trap to continuously drain condensate while preventing escape of biogas.
Install low point drains on every 200 to 250 feet of piping and at elbows. All other low points need drain piping with an automatic drip trap installed. Drip traps should have a water trap to prevent the escape of biogas from the system.
Moisture is problematic for biogas piping in colder climates. If not properly heat traced and insulated, it can freeze and block biogas flow. Biogas safety appurtenances such as flame arrestors, pressure regulating valves and flare ignition components can also freeze from this moisture and should be heat traced (intrinsically safe) and insulated. This also applies to in-line instruments, valves and low point drains. Heat trace should effectively cover all metal parts exposed to moisture.
Corrosion
Biogas contains hydrogen sulfide (H2S) and mercaptans that can condense in the form of weak sulfuric acid (concentration depends on how much H2S is in the biogas) within the headspace and piping causing rapid corrosion with incompatible materials. A material compatible with generation of weak sulfuric acid is recommended for any components in contact with biogas. Typical aboveground piping is metal; stainless steel is commonly used. Other materials that are not as corrosion resistant can be used as a cost-effective solution with some H2S removal technology applied upstream of this piping. Typical treatment methods to remove H2S and other impurities such as mercaptans are adsorption with iron media or granular carbon and/or chilling the gas (to remove excess moisture). A biogas desulfurization technology developed by Paques combines a chemical scrubber with a biological component to remove hydrogen sulfide.
Plastic pipe is corrosion resistant but not recommended as this material does not have the necessary tensile strength and can be statically charged. However, high density polyethylene (HDPE) piping, suitable for natural gas service, can be used for buried piping as those two factors are less of an issue when buried.
Design for any biogas piping should include an extra safety factor in the hydraulic sizing for pitting and corrosion that can occur within the piping. Pitting and corrosion can change the internal diameter of piping, causing flow problems.
It is crucial for all safety appurtenances to be constructed of corrosion resistant material as well, including diaphragm materials. Gaskets and seals must be compatible as well as these will become leaks points if the gaskets corrode and degrade. Only spark proof plastics can be utilized for nonmetallic components such as fan blades. Make certain all downstream drain piping and drip traps are compatible with weak sulfuric acid.
Operators should monitor changes in biogas pressure within piping as these are usually the first signs of moisture build-up or corrosion. Visual inspection of the condensate can also indicate corrosion is occurring. A gas meter can be used at gasket and seal locations to detect escape of gases.
Pressure Regulation
As noted, pressure must be held within the anaerobic reactors, biogas storage and piping systems to prevent release of biogas to the atmosphere and aid in “pushing” biogas to the use point or conveyance system. This is accomplished using various pressure regulating devices throughout the system, including digester vents, storage system vents, flare system and use points. If any of these fail, an over pressurization event can occur resulting in a release at the weakest point of the system (covers, storage systems, etc.).
Conversely, biogas piping from an anaerobic reactor connected to a blower or compressor, if not sized or controlled properly, has the risk of pulling biogas from the reactor. If this negative pressure is not relieved it can also implode (collapse) at the weakest point in system (covers, etc.).
An emergency relief vent can be used as secondary protection to regulate pressure, but caution should be taken to release biogas from these appurtenances safely into an area rated for biogas release where operators or spark sources will not be present. Instrumentation can sense this has occurred and notifies operators that biogas is being released to the atmosphere outside of a controlled flare, and/or can shut down any blowers or compressors to avoid additional air entrainment in vacuum conditions.
Size pressure regulation and relief devices for the worst case credible scenario conditions and subsequent gas flow through them. The biggest risks and most failures are a result of either corrosion or freezing of these pressure relief devices and instruments that monitor or control pressure within the system. Refer to previous sections on corrosion, moisture control and freeze protection.
Leaks
Leaks are mostly from corrosion of piping, gaskets and seals within the system. Periodic sweeping of a biogas system with a gas monitor is recommended to detect any leaks. Safety appurtenances sometimes leak as diaphragm materials and mechanical components wear out or warp. Inspect these appurtenances one to two times per year, especially after winter conditions, to make sure they still seal off gases and do not vibrate in use, or “chatter.”
Any sampling hatches should have a stilling well that dips below the water surface to trap gases and protect operators during sampling and maintenance. In addition, having properly calibrated gas monitors on at all times near biogas piping and equipment is recommended.
As anaerobic digestion infrastructure grows and matures, more attention should be paid to the issues of safe biogas piping and transport. Industry groups should move to develop piping design standards into their best management practices guidance.
Sara Martin, P.E., is a Principal at Critical Path Engineering Solutions, a small woman-owned business specializing in project management and engineering for water, wastewater and facility infrastructure projects. Craig Coker is Senior Editor at BioCycle and a Principal in the firm Coker Composting and Consulting.