Emerald Coast Utilities Authority did the math and determined that composting its biosolids and yard trimmings and selling the compost made the most economic sense.
Mitch Kessler and Nathalie Bowers
BioCycle May 2017
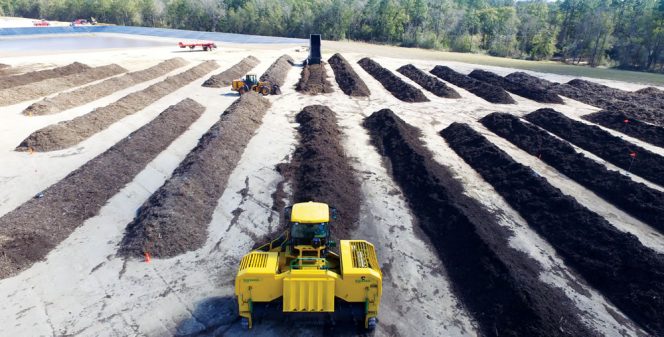
ECUA uses the Modified Static Aerobic Pile composting method, which incorporates a Harvest Quest inoculant. A Backhus compost turner mixes the blend of yard trimmings and biosolids (3:1 ratio, by volume) and forms a windrow (above). Inoculant is added, and the windrow is capped with a layer of screened overs or freshly ground yard trimmings. Photo courtesy of ECUA and Kessler Consulting, Inc
As a wastewater utility provider, ECUA manages approximately 120 wet tons/day of biosolids. It had been either land applying or drying the biosolids to produce a pelletized fertilizer, costing ECUA over $1 million a year. At the same time, ECUA was paying nearly $28/ton to dispose of the yard trimmings it collects.
Realizing the high costs associated with existing operations, ECUA decided to reassess its biosolids processing and yard trimmings disposal procedures. In 2011, it contracted with Kessler Consulting, Inc. (KCI) to conduct a study to determine the feasibility and benefits of constructing a Biosolids Composting Facility (BCF) on land adjacent to its Central Water Reclamation Facility (CWRF). The study identified the synergistic and cost saving opportunity to put both yard trimmings and biosolids to a higher and better use by composting these materials together. ECUA began moving forward with the planning, design and development of a biosolids composting facility in 2014.
Situated on 2,200 acres of undeveloped land safely above Category 5 hurricane elevation minimums, CWRF’s location provides an ideally large buffer zone that beneficially separates the facility from neighboring commercial and residential properties, and is large enough to allow for future additions to increase the size of the BCF. Locating the BCF in such close proximity to the CWRF optimizes efficiency, including removing the need for transporting biosolids over a long distance between facilities, and eliminating any expenses that transporting of biosolids would incur. The study concluded that the advantages of being able to compost biosolids and yard trimmings within a BCF located on CWRF property outweighed any costs associated with building the facility.
Composting Method
Once the site was selected, ECUA needed to determine which composting method to employ, a crucial decision driving all other components of the facility, including capacity, size, capital costs, operational costs and regulatory compliance. After evaluating the turned windrow (TW) and aerated static pile (ASP) methods, ECUA decided to go with the Modified Static Aerobic Pile (MSAP®), developed by Harvest Quest, a division of Ecoverse. The MSAP® is a hybrid windrowing method that borrows practices from both TW and ASP composting. It incorporates a proprietary inoculant, marketed to accelerate and enhance the biological process of composting.
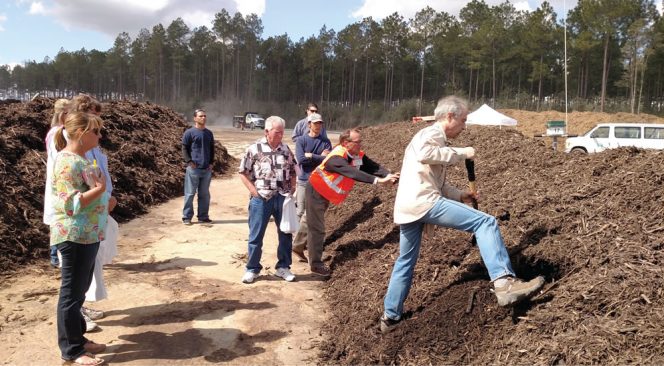
A field day was held at the facility for potential end users of the compost, including landscapers, nursery growers, farmers and Florida DOT. Photo courtesy of ECUA and Kessler Consulting, Inc
The fee to dispose yard trimmings was $27.69/ton at Escambia County’s Class I landfill. ECUA collects an average of 2,166 tons/month of yard trimmings, which equates to a monthly cost of $60,000. Therefore the total net “business as usual” cost is approximately $177,000/month. The BCF has an estimated monthly operating cost of $65,175 at its current capacity. To double capacity to handle all of ECUA’s biosolids, operating costs would be $130,350/month.
Cost savings can be realized by the MASP method because it requires only two turnings, reducing labor, fuel and equipment maintenance costs. The composting cycle time is also reduced (and therefore, the facility footprint), requiring 60 days to produce a stable compost product as opposed to a minimum of 120 days for traditional methods. According to Harvest Quest, the inoculant of highly active composting microorganisms spreads across the windrow surface, where the microorganisms act as tiny syphons to allow oxygen to enter the pile, essentially biologically simulating the ASP composting method.
Full-Scale Operations
By fall of 2015, a MSAP composting pilot was underway; the facility began full-scale operations in March 2016. Employing the MSAP Method gives the BCF capacity to compost 400 wet tons of biosolids and 500 tons of yard trimmings per week at its 24.5 acre facility. This equates to processing approximately 50 percent of the biosolids generated at ECUA facilities each week (the other 50% continue to be dried), and 100 percent of yard trimmings collected weekly.
ECUA tips its biosolids (dewatered to 16-18% solids) onto a three-sided bunker of ground yard trimmings, which are processed on-site using a Morbark 1300 tub grinder. More ground yard trimmings are added on top of the biosolids in a ratio of three parts yard trimmings to one part biosolids by volume, which makes a biosolids “Twinkie.” A Backus A-55 windrow turner then runs over the pile, mixing the material and forming a windrow that is 7- to 8-feet high and 16- to 20-feet wide. After mixing, the inoculant is added to both ends of the windrow and the entire windrow is covered with a 12-inch capping layer of screened overs or fresh ground yard trimmings. Optimal moisture content for the initial windrow is 45 to 50 percent.
For the first 30 days, the windrows are static piles; the first turning occurs on day 30, although at ECUA the timing depends on progress of the decomposition process, e.g., windrows are sometimes turned for the first time after less than 24 days. After turning, the windrows are recapped and remain static for another 15 days, when they are turned again. At that point, active composting is concluded and the compost is moved to a screen to separate finished compost from overs. The finished compost then cures for an additional 30 days before distributing for use. The minimal amount of turning combined with the use of a yard trimmings capping layer also significantly reduces odors emitted by the windrows.
Keeping It Clean
To maximize the usability of all yard trimmings at the BCF, ECUA launched a residential community-wide educational campaign in Spring 2015, as construction of the BCF was underway. Entitled “Brown is the New Green, Leaf the Plastic Behind!”, the campaign’s primary message is to encourage its residential customers to switch from plastic bags to compostable paper bags or reusable containers for setting out residential yard trimmings. ECUA made 18-gallon compostable brown paper bags branded with the campaign logo and imagery available for yard trimmings; the brown bags were distributed at any community event in which ECUA participated, as well as were available at a number of retail establishments.
As a result of this outreach, ECUA is seeing marked reduction in the amount of plastic bags in its residential yard trimmings. This, combined with the instructional guidelines printed on the back of brown bags, has helped to create a behavioral change among its residential customers.
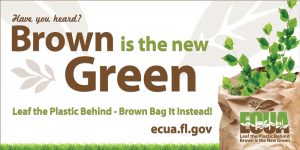
An educational campaign was launched to encourage ECUA’s residential customers to use compostable paper bags or reusable containers for setting out yard trimmings. Six trucks had 4-foot by 9-foot panels (above) on each side to serve as mobile billboards on collection routes.
ECUA’s Public Information staff promotes the program extensively through community events, offers composting facility presentations and tours, and does radio and TV interviews with local media. It also has a YouTube video of their facility and its process on their website. These video and PowerPoint presentations give ECUA an opportunity to promote the campaign as well as find potential end users for the compost. More importantly, ECUA sees the BCF as being an integral part of helping the community work towards its core values by creating a sustainable path for yard trimmings and biosolids.
Building Product Awareness
ECUA anticipates about 30,000 cubic yards (cy) of compost will be produced annually. Producing usable compost is essential to the success of the BCF. Large, noncomposted woody materials must be separated from the finer, composted material. To do this, ECUA purchased a Komptech Multistar L3 Star Screen, a 3-fraction screen — a large fraction (>1-1⁄4-inches) of noncomposted woody overs, a medium textured fraction (5⁄8 to 1-1⁄4-inches) and a fine-textured compost (<5⁄8-inches). A 1⁄4-inch product is also available. Overs are returned to the active compost area to be used as the capping material on the windrows or sold as a mulch. Medium textured compost is ideal for soil blending or topsoil incorporation, while the fine texture is ideal for top dressing, especially on turf. The L3 has a throughput capacity of 325 cubic yards (cy)/hour.State of Florida regulations (64-630.850 FAC) require compost to be registered as a fertilizer for distribution, unless it is both certified under the US Composting Council’s (USCC) STA® (Seal of Testing Assurance) program and is outside the Lake Okeechobee, St. Lucie River, and Caloosahatchee watersheds (in Central and South Florida). ECUA has enrolled in the STA program and is limiting distribution to northwest Florida and surrounding areas, thereby not requiring it be registered as a fertilizer.
In February 2016, ECUA held a field day at the BCF for potential end users of the compost to kick off its marketing outreach. Attendees included nursery growers, sod farmers, landscapers, community garden organizers, Escambia County Parks and Recreation, and Florida Department of Transportation. The open house provided end users a chance to learn how the BCF operates, see equipment in action, and become familiar with the final compost product. It also allowed ECUA to initiate partnerships with some of these end users for compost trials.
Since ECUA began marketing the material in March 2016 (initially selling compost from the pilot), sales went from zero to approximately 5,400 cubic yards of finished compost (Figure 1) in less than a year’s time for revenue of $41,400 (Figure 2). Cumulative compost distribution is shown in Figure 3. BCF currently makes Emerald Coast bloom available for purchase to landscapers, environmental contractors, churches, golf courses, homeowner associations, local extension service, residents, local and regional farms, and nurseries. Price for Emerald Coast bloom, sold in bulk, is $10/cy (0-10 cy); $7/cy (10-40 cy); $4/cy (40+ cy). Delivery is available to certain areas for $2/cy. Residents will continue to be educated about procuring and using the brown bag program to reduce contamination and the ECUA compost team will continue to pursue and expand sales on the South’s Emerald Coast.
To identify the target audience, KCI performed a marketing research analysis and compiled a database of potential end users in the Emerald Coast area in 13 industry categories. A comprehensive marketing packet for end users was created — as well as a website — with more detail about the product and educational information about using compost.
Mitch Kessler is President of Kessler Consulting, Inc. (913-971-8333). Nathalie Bowers is Public Information Officer for the Emerald Coast Utilities Authority.