Top: Agitator and aerated bays at the Town of Fairfield, CT’s composting facility. Photos courtesy BDP Industries
Hannah Falk and John Bodie
In 1987, Chief Operating Engineer, Richard White and his team conducted a sludge disposal feasibility study for the Town of Fairfield, Connecticut (Spencer, 1989). At the time, sludge was dumped at the Town’s garbage landfill. Fairfield was considering a variety of biosolids disposal methods, including incineration, drying, and composting. The Town decided that a composting system would be best because of the proximity to its Water Pollution Control Facility (WPCF) and the existing brush/yard trimmings drop-off location. This created an opportunity to recycle the yard trimmings, a low-cost amendment for a biosolids composting system.
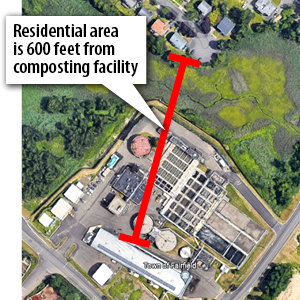
Image ©Google maps
The Town evaluated both outdoor and in-vessel composting technologies. With the closest residential neighborhood just 600 feet away from the facility (see image), odor control was a key factor in determining which system would be used. The town opted for an in-vessel system to limit odor concerns, and in 1987 a request for proposals for in-vessel composting systems was issued.
Composting Process
International Process Systems (IPS) was selected to design and build the Fairfield in-vessel facility located at the WPCF. The composting facility commenced operation in 1988 utilizing an agitated and aerated bay type technology similar to BDP’s In-Vessel Composting System (ICS), shown in Figure 1. The building is fully enclosed and has six concrete bays. One BDP agitator services all six bays with each bay being 6-feet wide by 6-feet tall, and 220-feet long.
WeCare Denali, the Town’s contractor, uses a tub grinder with a 1-¾- to 2-inch screen to process incoming brush and wood into wood chips for amendment. Larger screen sizes result in excess “tailings” that require additional screening and grinding. At that point the reground chips would not add much value to the process and are more labor intensive to produce.
The wood chips are combined with anaerobically digested biosolids using a mixing truck prior to loading the bay. The loading capacity of the bay is 14 cubic yards/day. Each working day, the agitator automatically moves on rails simultaneously shredding, mixing and transferring the material down the length of the bay. Once the agitator reaches the end of the bay, it is automatically transferred to the next bay by using its transfer dolly. With a mostly automated process, the town has just one operator working eight hours a day, Monday through Friday, to process about 4,000 wet tons/year of dewatered biosolids cake.
To ensure the material in the bays achieves the desired temperature of 55°C (to meet pathogen reduction or PFRP), multiple temperature probes are placed within the bay walls — typically the coldest spot in the pile as the walls tend to suck up heat. Temperature monitoring is fully automated via the BDP-supplied AgitatAer Facility SCADA system with the option to override automated wall temperature settings by the operator manually inputting a hand-held probe, usually in the hot middle part of the pile. This is the same approach that would be used in any windrow or aerated static pile composting facility where temperatures are taken in the center of the piles. Blowers push air through stone flooring and into the compost mixture. The original exterior bay walls had a 2-inch layer of fiberglass insulation installed along the length of them in attempt to hold heat in bay. The insulation was eventually abandoned based on cost to maintain versus the benefit.
After the material has completed its 21+ day journey through the bays, the compost is removed and brought to the curing site — the same location near the WPCF where incoming brush and woody debris are processed by WeCare Denali. The company’s contract with the Town also includes managing compost curing and screening, as well as product marketing. The Town receives a percentage of revenue from the sales. While curing, the compost is monitored and tested for stability and other parameters. Once a pile passes testing, it is moved into a “good” pile where it is screened. The compost, which is certified by the US Composting Council’s Seal of Testing Assurance (STA), is used throughout the Northeast region for various purposes such as soil blending, roadside reseeding, and golf course top dressing.
Upgrades And Future Plans
Since the 1988 installation, Fairfield has not faced any significant odor issues, which are generally the main reason composting facilities close. In 2007, the Town of Fairfield did a significant rebuild of its system. The structure was replaced from the concrete up with a new stainless-steel building. New ventilation blowers, floor blowers, and wall sensors and a computer control system were added. A new BDP agitator and dolly system were installed as well. The Town did not consider any alternatives to composting at that time because of its facility in place. The ability to dewater, compost, cure, and market the end product from its site is unique and cuts costs significantly. Most recently, the Town of Fairfield made a significant investment in a new agitator, which was put into service this summer (2023).
The Fairfield in-vessel operation is the only biosolids composting facility in Connecticut. There is great concern within the Northeast regarding biosolids disposal options. The in-state incinerators in Connecticut have “spot” capacity available only, and it is increasingly difficult to obtain a commitment for continued biosolids disposal over the life of a contract. Landfills with available space are hard to find, and tip fees are around $125/ton on average. BDP estimates long-term disposal options would total around $200/ton (tip and haul) within a 100-mile radius. The next closest areas would be Western New York, where landfill capacities are also very limited. The only more reliable option is Ohio landfills. However, the cost to haul that far would increase long term disposal options significantly.
While other towns in Connecticut are trying to find disposal options, Fairfield is fully in control of theirs. Even if compost becomes more difficult to market, the Town can easily convert to a biodrying (composting using biosolids only with no high carbon amendment source) operation to reduce disposal costs.
Hannah Falk is the Sales and Marketing Coordinator for the Composting Division at BDP Industries in Greenwich, New York. John Bodie is Superintendent of the Town of Fairfield, Connecticut’s Water Pollution Control Facility.