In California, WRRFs have capacity to help provide food waste recycling infrastructure. Elsewhere in the U.S., facilities are ramping up to codigest these high strength feedstocks.
Nora Goldstein
BioCycle March/April 2018
About five years ago, the Water Environment Federation (WEF) formally began using the term, water resource recovery facility (WRRF), in place of wastewater treatment plant. WEF noted that the name change reflects a changing paradigm in the water sector, focusing on recovery of water, nutrient and energy resources. In a press release announcing the change, WEF referenced codigestion as a resource recovery practice at WRRFs.
Increasingly, WRRFs in the U.S. with anaerobic digestion capacity are opening their gates to high strength organics such as commercial food waste and fats, oils and grease (FOG). “One driver in some regions is regulatory, where states are beginning to require generators over a certain size to divert food waste from landfill disposal,” notes Peter Loomis, a Technical Advisor with CDM Smith. “Another driver is economics. For a relatively small capital investment, WRRFs can get financial returns.”
The California Association of Sanitation Agencies estimates that existing infrastructure at government-owned WRRFs in California could accept up to 75 percent (7 million wet tons) of the food waste stream being landfilled in the state. The California Air Resources Board carried out a geospatial analysis indicating that food waste and wastewater treatment excess capacity are spatially correlated throughout California. The analysis found that all food waste currently landfilled could theoretically be consumed by wastewater treatment plants within 30 miles of these landfills.
“In our experience, whether a WRRF moves forward with codigestion is a top-down decision,” says Loomis. “Senior management needs to buy into the plan first, and then the operations and plant management will look at options to optimize the existing facility. In general, there is not a huge impact on the operations of the digester itself but more monitoring is needed.”
Codigestion Considerations
The primary capital investment related to codigestion is food waste and/or FOG receiving. Capability should be in place to remove heavy rocks, silverware and other items that come in with the loads. WRRFs receiving FOG will need screening, heated storage and transfer pumps, adds Loomis. “After food waste receiving, the next investment will be odor control in the receiving area and then gas handling. Food waste and FOG receiving facilities have historically demonstrated significant odors, potentially generating complaints. Odor control is needed on the front end, and more input to the digester will result in more gas production on the back end.”
Another consideration is the nutrient impact on the liquid stream that gets recycled back to the treatment plant after biosolids dewatering. “Generally speaking, there is a high ammonia load,” explains Loomis. “With biosolids, normally the ammonia load that returns to the liquids stream is in proportion to what is being processed. As a rule of thumb, there is one dry ton of solids for every one million gallons of sewage treated. Liquid separated from the solids — the centrate — is in proportion, nutrient wise, to the solids that are taken out. When WRRFs incorporate high strength organics and food waste, instead of one dry ton/million gallons of sewage, they are processing 1.25 to 1.5 dry tons for every million gallons, so there is more ammonia going back in the centrate.”
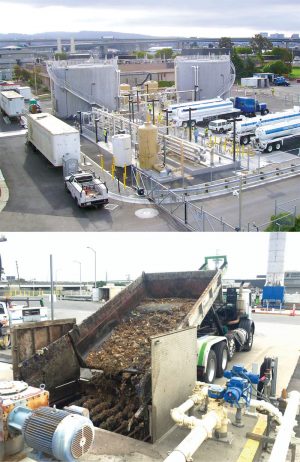
The high strength organics (HSO) receiving area (top) at the East Bay Municipal Utility District (EBMUD) was built in 2014, along with a new HSO blending facility. Most of the HSOs arrive as a liquid. Feedstocks higher than 15 percent solids (example above) have to be slurried after being unloaded. Photos courtesy of EBMUD
East Bay Municipal Utility District
One WRRF examining the impact of excess nutrients from trucked in loads of high strength organics (HSOs) is the East Bay Municipal Utility District (EBMUD) in Oakland, California. EBMUD provides primary treatment for up to 320 million gallons/day (MGD), and secondary treatment for a maximum flow of 168 MGD. On average, about 63 million gallons of wastewater is treated every day.
EBMUD was a pioneer in codigestion of food waste, receiving its first trucked in load in May 2004 (see “Green Energy From Food Wastes At Wastewater Treatment Plant,” January 2008). EBMUD now receives about 4,000 truckloads per month for treatment and digestion, which enabled the utility to become the first WRRF in North America to produce more electricity onsite than is needed to run the treatment plant.
“We have about 250 customers, and service about 100 to 150 trucks per day,” notes Michael Hyatt, Associate Engineer, Resource Recovery, at EBMUD. “Two-thirds of the trucked in waste has low COD [chemical oxygen demand] and goes to the head of the plant. Of the one-third we take that is high strength, by volume it is 15 percent FOG, one percent food waste, although this is much more concentrated than the rest, 10 percent is animal protein waste and the remaining 74 to 75 percent are various types of process water, e.g, from the dairy and wine industries.”
Most of the HSOs arrive as a liquid. Food waste that is greater than 15 percent solids has to be slurried. All HSOs are loaded into two concrete cylinder blending tanks. The blending facility was built in 2014, along with a new receiving area. “We blend all the material going to the digesters to try to ensure a more uniform feed and avoid sudden variations,” explains Hyatt. All of the digesters receive the codigestion mix. This includes all of the trucked waste as well as the domestic wastewater treatment streams (primary sludge and waste activated sludge. He adds that in the earlier days of codigestion, “we would get a load of high strength material and put it into one digester, which could lead to an upset.”
The food waste is almost all from commercial generators, but EBMUD does get a small amount of preprocessed residential material that is delivered as a liquid. Generally food waste is around 30 percent solids, and in addition to slurrying, needs preprocessing to remove contamination before it is sent to the blend tanks.
EBMUD tests the first load of any new HSO being received, and sometimes inspects the waste stream generator’s production facility (e.g., if it is something less familiar to EBMUD). Constituents being measured include sulfur, salt and nitrogen. After testing the first loads, operators will spot check loads to track the content over time. “The dairy loads, for example, can be very salty,” says Hyatt. “Cheese waste has a high COD, which is good for the digester, but it does impact the level of salt in the centrate after dewatering.” Salt also is high in the trucked in brine waste (a low strength liquid) that is unloaded at the head of the plant.
Anaerobic digestion breaks down the proteins and the organics, but doesn’t remove sodium, phosphate or magnesium ions in the total dissolved solids (TDS), he adds. This can result in precipitation of some of the salts in the digestion tanks and on the pipe walls. EBMUD is evaluating the impact of the TDS levels on recycling of treated water. For example, cooling towers require low TDS whereas when recycled water is used for irrigation, the level can be higher. “We could put in a reverse osmosis membrane to remove the TDS but that is a very expensive option,” says Hyatt.
To manage hydrogen sulfide (H2S), EBMUD adds ferric chloride to the digester tanks, as the plant has limited ability to remove H2S in the gas phase. “With the growth of codigestion, we have had to monitor this much more closely and try to anticipate loads as the ferric addition takes some time to affect the process,” he notes.
Of the total nutrient load from wastewater treatment plants to the San Francisco Bay (where EBMUD’s treated water is discharged), EBMUD contributes approximately 20 percent, which is high relative to EBMUD’s flow, according to Hyatt. “This is due to nutrients in the trucked waste coming to the plant. The most effective place to add a treatment step would be on the centrate line, after digestion but before returning to the rest of the plant. Sidestream treatment on the centrate line is something we are actively researching.”
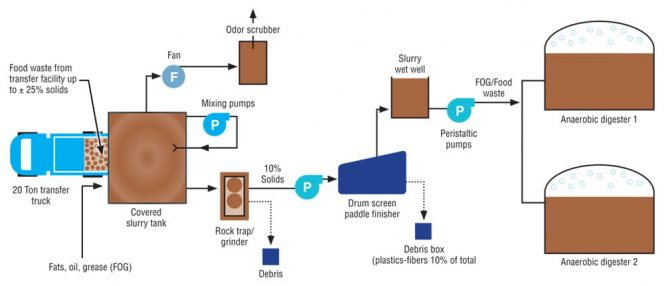
Figure 1. Food waste receiving and processing system at Central Marin Sanitation Agency (CMSA). Source: CMSA
Central Marin Sanitation Agency
In January 2008, the city manager of San Rafael, California received a letter from Pacific Gas & Electric (PG&E) saying grant monies were available for feasibility studies of projects that would reduce greenhouse gases. Anaerobic digestion was on the list of fundable projects. The city manager contacted the Central Marin Sanitation Agency (CMSA) in San Rafael because he was aware that the WRRF had anaerobic digesters. “We spoke about the grant opportunity and the city manager asked if we would be interested in applying,” recalls Jason Dow, CMSA’s General Manager. “I was aware of EBMUD’s codigestion project, so said yes. We have two anaerobic digesters with a combined capacity of about 2 million gallons/day, and were utilizing about 25 percent of that for biosolids treatment.”
The city manager convened a meeting with PG&E, CMSA, Marin Sanitary Service (MSS) and other local city managers. MSS’ service area overlapped with CMSA’s service area, and it was decided to design an organic waste receiving facility at CMSA based on the equipment and processes used at EBMUD. CMSA and MSS applied for and received the grant, and formed a public/private partnership to create the Central Marin Commercial Food-2-Energy Initiative (F2E). “I didn’t even think of working with a waste hauler to initiate a codigestion program,” notes Dow. “And most municipal solid waste agencies aren’t aware of WRRFs’ anaerobic digestion capacity for food waste processing. That’s changing now in California because of new state regulations that mandate reduction of organics disposal in landfills.”
The CMSA WRRF’s average dry weather flow is approximately 7 MGD and peak wet weather flow is approximately 100 MGD. An article in BioCycle in June 2015 (see “Boosting Biogas And The Bottom Line at WRRFs”) describes the infrastructure put in place for codigestion of commercial food waste at CMSA and MSS. Briefly, the F2E design was incorporated into a larger digester rehabilitation project at CMSA, and included replacing the original two floating steel covers on the digesters with membrane covers, replacing the digester’s gas mixing system with a pump mixing system, and installing additional biogas purification equipment to remove H2S. Capital costs were $2 million.
MSS invested about $530,000 in food waste preprocessing equipment supplied by West Salem Machinery that includes a conveyor system, magnet to remove metal contaminants, a hand sorting area to remove other contaminants, and a hammer mill grinder to reduce the material size. The preprocessed food waste is trucked about a half-mile down the street to CMSA, where it is unloaded into an underground slurry tank, and mixed with Vaughan chopper pumps. The first load of food waste was delivered in January 2014.
“Most contamination is removed at MSS, but we do occasionally receive small pieces of plastic, such as the labels on produce, and fibrous materials like corn husks that are removed by a screening system, called a paddle finisher,” says Dow. “The tank is cleaned out every three months. MSS picks up this material, which is mixed with green waste and domestic food waste for composting.” Currently, MSS is collecting food waste from almost 200 generators and is delivering an average of 7.5 tons/day, up to 6 days a week, to CMSA. In addition, the WRRF receives up to 20,000 gallons/day of FOG, up to six days a week. “The digester pump mixing system breaks up FOG that would otherwise form a layer in the digester,” he adds. Figure 1 depicts the flow of food waste receiving and treatment at the WRRF.
The volatile solids average for the FOG is 93 percent; food waste is 91 percent. The digester hydraulic residence time average is 35 days. Since codigestion began, CMSA has seen an increase in biogas generation from 127,000 ft3/day (5-year average) to over 300,000 ft3/day. Biogas from the digesters goes through a Biorem SulfaTreat scrubber to remove H2S. Next, the gas is conditioned to remove the moisture and siloxane, and then combusted in a 750 kW combined heat and power (CHP) engine. “We are receiving enough organics to produce about 23-plus hours/day of energy to power our facilities, and in the near future we anticipate receiving more material to max out the 750 kW engine capacity and deliver excess power to the grid,” explains Dow, noting that the WRRF utilizes about 625 kW. “We have been working with PG&E on a new interconnection agreement to allow the Agency to deliver renewable power. Historically, the interconnection agreement prohibited power delivery.”
PG&E did an electrical system evaluation of its utility infrastructure around CMSA, and determined that it could receive power from the 750 kW CHP engine with only minor improvements to its system. “Part of the agreement we’ve been working on with PG&E involves CMSA paying for those improvements, e.g., a power delivery meter at a cost of $80,000,” he adds. “Once the PG&E and on-site improvements are completed, CMSA will receive authorization to deliver the power. At that point, we need an entity to sell the power to, and are in discussions with two utilities. One has a better power purchase rate structure, so we may proceed with that utility.”
Rahway Valley Sewerage Authority
The Rahway Valley Sewerage Authority (RVSA) in Rahway, New Jersey, owns and operates a 50 MGD plant (average flow, with 105 MGD peak flow), has three anaerobic digesters with about 30 percent unused capacity, and an underutilized CHP system. It opted to proceed with codigestion, and the Authority issued an RFP for a feedstock supply partner. “We wanted a long-term contract that provides consistent feedstock,” notes James Meehan, Executive Director of RVSA. “Waste Management (WM) was selected as our feedstock supply partner under a 10-year contract with up to a 10-year renewal. The agreement is set up as a public/private partnership. The goal is to optimize digester operations, reduce the risk of losing [feedstock] supply to lower cost competing facilities, obtain a guaranteed revenue stream, minimize the need to purchase third party natural gas for plant operations, and to increase the facility’s sustainability and resiliency while decreasing its carbon footprint.”
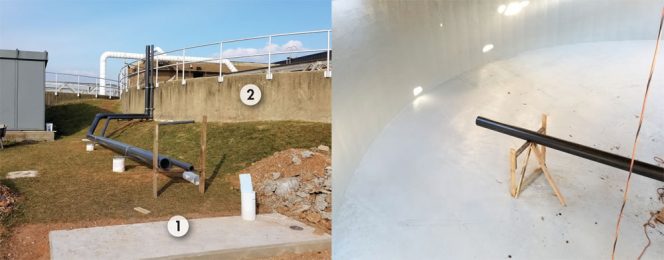
Concrete slab in foreground (1) in photo (left) will hold a control panel and station where tanker trucks delivering slurried food waste will connect to a pipe to unload. The feedstock will be transported a short distance to a receiving tank (2).
The receiving tank (right) had been used by Rahway Valley Sewerage Authority as a gravity thickener. The tank’s interior has been retrofitted with jet nozzles. A coating was applied to the concrete surface to prevent corrosion.
RVSA secured a loan from New Jersey’s Clean Water State Revolving Fund (SRF) to finance the retrofits. “It was a challenging process to do a design/build through a SRF,” says Rick Sapir, a partner at the law firm of Hawkins, Delafield & Wood, which also negotiated the public/private partnership with WM and helped with the financing. “The regulations are set up based on a traditional design-bid-build contract, where the public agency hires a design engineer to do the design that is approved by the state agency administering the SRF, and then the public entity puts it out for the lowest responsible bidder. We succeeded in navigating the process, which resulted in a loan with an approximate one percent interest rate.”
Waste Management is installing its patented CORe® food waste slurry system at its Flora Street solid waste facility in Elizabeth, New Jersey, about 5 miles from the RVSA WRRF. The Flora Street facility is permitted to receive 500 tons/day of food waste but is only installing capacity for processing 250 tons/day. The process includes depackaging and contaminant removal, followed by slurrying the food waste. The material goes into tanks, where WM creates an Engineered BioSlurry (EBS®) for codigestion that meets acceptable ranges for key parameters, including BOD [biological oxygen demand] COD, pH and metals. “The plan is to bring in 6,000 gallons/day of EBS to start, with total solids between 7 and 15 percent, and then ramp it up during the year,” says Meehan. “We are still in construction, including the installation of membrane covers on the digester. We expect to be nearly completed with one of the digesters by April or May.”
WM estimates that it produces 330 gallons of EBS per wet ton of food waste processed. By year 4 of the contract, WM is guaranteeing it will deliver 200,000 gallons/week, according to RVSA, but anticipates the amount to be closer to 252,000 gallons, or about 764 tons/week. The maximum loading to the RVSA digesters is 318,400 gallons/week or 965 tons/week. WM is paying a tipping fee to RVSA to codigest the food waste. “There is a requirement for WM in the contract to use best efforts to separate contaminants from the specified feedstock, and a requirement for WM to reimburse the Authority for costs incurred due to the introduction of contaminants as well as reimbursement for the cost of disposal of residuals above a stipulated level,” adds Meehan.
Biogas production is currently 250,000 ft3/day. That quantity is anticipated to at least double, hopefully triple once codigestion reaches the full quantity of food waste the plant is designed to receive. The facility owns four 1.55 MW CHP engines, and will use all the power generated from the biogas to run the plant. The treatment plant power demand ranges from 1.5 MW to 3.0 MW.