Craig Coker
Seventh of a series of articles on issues to consider when planning a new composting facility in the U.S.
Planning a new merchant organics recycling facility requires considerable thought and investigation. As the old adage goes, “Proper prior planning prevents poor performance.” This facility planning series is oriented to helping you think through the aspects of proper prior planning. Part I dealt with how to develop a Waste Capture Plan. Part II covered methods to assess the markets’ potential to absorb your compost and/or soils products. Part III looked at how to figure out how much room you would need for your new composting facility. Part IV explored how to evaluate different composting approaches or methodologies. Part V examined issues to consider when looking at possible sites for a composting facility. Part VI discussed the various local and state-level approvals and permits that will likely be needed. Part VII covers how to estimate capital and operating costs for your new facility.
Developing sound cost estimates is critical in securing financing for any business enterprise or funding for any municipal operation. While composting is certainly a more environmentally conscious means of handling biodegradable materials than landfilling, the simple reality is that everything revolves around costs. It is necessary to learn how to estimate costs and revenues, evaluate different alternatives on the basis of their long-term costs, and assess the impacts of costs on cash flows and budgets.
Capital Cost Estimating
Capital cost estimating for building, expanding or upgrading a composting facility varies in precision as a function of the extent of detailed design and construction bids. The main categories of capital costs to be estimated include site development, processing equipment (both stationary and mobile), and process monitoring equipment. In early facility planning, site development estimates will have an accuracy of +50%/-30%; following detailed design, accuracy will improve to +25%/-15%; after bid receipts, accuracy improves to +10%/-5%. To accommodate that varying accuracy, you should budget for contingency funds to cover any unforeseen expenses.
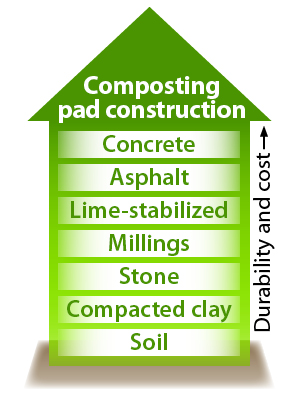
Figure 1. Composting pad options
Site development costs are, obviously, very site-specific. Wooded sites will need more clearing; hilly sites will need more grading. Ultimately, what you want to end up with is a gently graded site (≈ 2-3%), with no cross-slope, that is cleared, graded and compacted. The facility’s working surface will be defined, partly, by regulation, partly by operator preference (I have yet to meet a composter who prefers a bare earth site in rainy or wintry weather), and mostly by budgetary realities. Figure 1 illustrates the relative capital costs of different types of working surfaces.
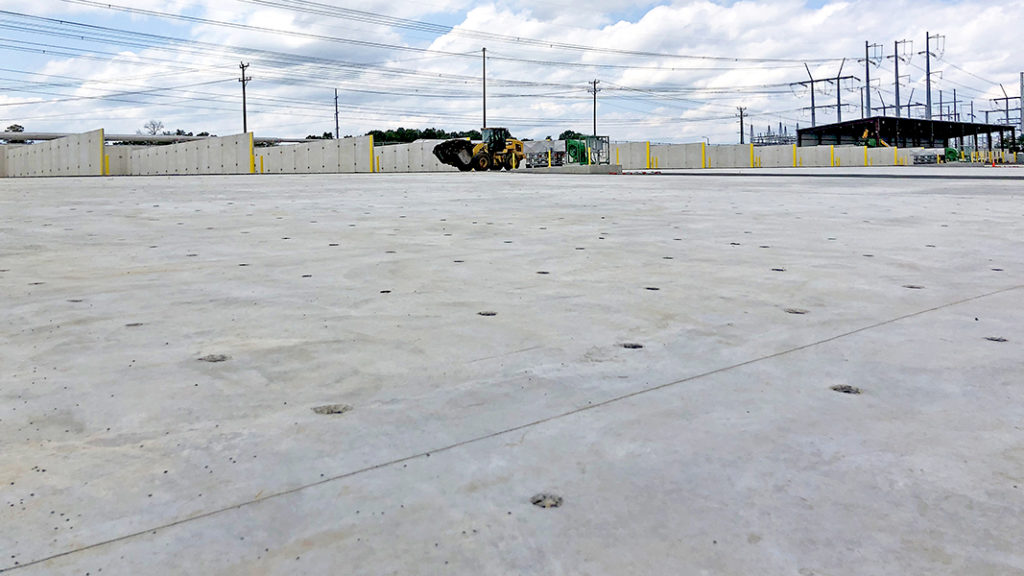
Newly built sparger type floor for the positive aeration mass bed used for curing (foreground). Active composting bunkers and preprocessing building (on far right) are in the background. Photo courtesy of Freestate Farms and Engineered Compost Systems
Utilities are part and parcel of any site development costs. If you are planning on aerated static pile (ASP) composting, you will need three-phase power. Extending three-phase power can be expensive if you are considering a farm-based or rural site for composting. Water and sanitation services will also be needed, which will mean a water well and septic system if your site lies beyond a water and sewer-serviced envelope. Data communication and internet service are increasingly important in any new facility development, along with adequate cell phone coverage, so plan for those costs (e.g., satellite dish) as well if needed. Storm water runoff management is another necessity, so plan for on-site runoff treatment using vegetated Best Management Practices — even if you can connect your site to a municipal separate storm sewer system (often called a MS4).
Site development costs can be estimated with construction estimating software. Because those software programs are intended to be used by construction contractors preparing bids from detailed design drawings and specifications, they can be quite detailed. Programs I have used include Craftsman Cost Estimating Software and R.S. Means. Table 1 shows the projected site development costs for a conceptual 40,000 tons/year municipal composting facility using ASP for industrial food processing residuals in the upper Midwest.
The other big capital cost estimating element to consider is equipment. Processing equipment includes front-end loaders, grinders, turners, mixers, depackagers, blowers and piping, screens, contaminant removal and bagging. Multiple companies in the U.S. offer various types of equipment and most exhibit their wares at composting and solid waste trade shows around the country. Equipment costs vary by size, capacity and technological sophistication. Equipment can be purchased, or, in many cases, leased for several years. If leased, those costs get reflected in your operating costs, not your capital costs. Table 2 shows the projected equipment costs for the conceptual composting facility noted above.
Most of this equipment is available in the used equipment market where capital costs are much less. However operating costs are higher, with larger expenditures due to wear in components.
Process monitoring equipment will include the basic essentials such as a 36-inch dial-face temperature probe ($150-$200) and a tablet ($750-$1,000). More sophisticated monitoring systems include wireless temperature probes ($2,000+) and Supervisory Control and Data Acquisition (SCADA) computer interfaces. Many composting facilities have a weather station to record wind speed and direction and rainfall amounts ($700–$2,000) and a small on-site laboratory for measuring bulk density and free air space, microwave measurement of moisture content, pH tests, and similar process monitoring measurements.
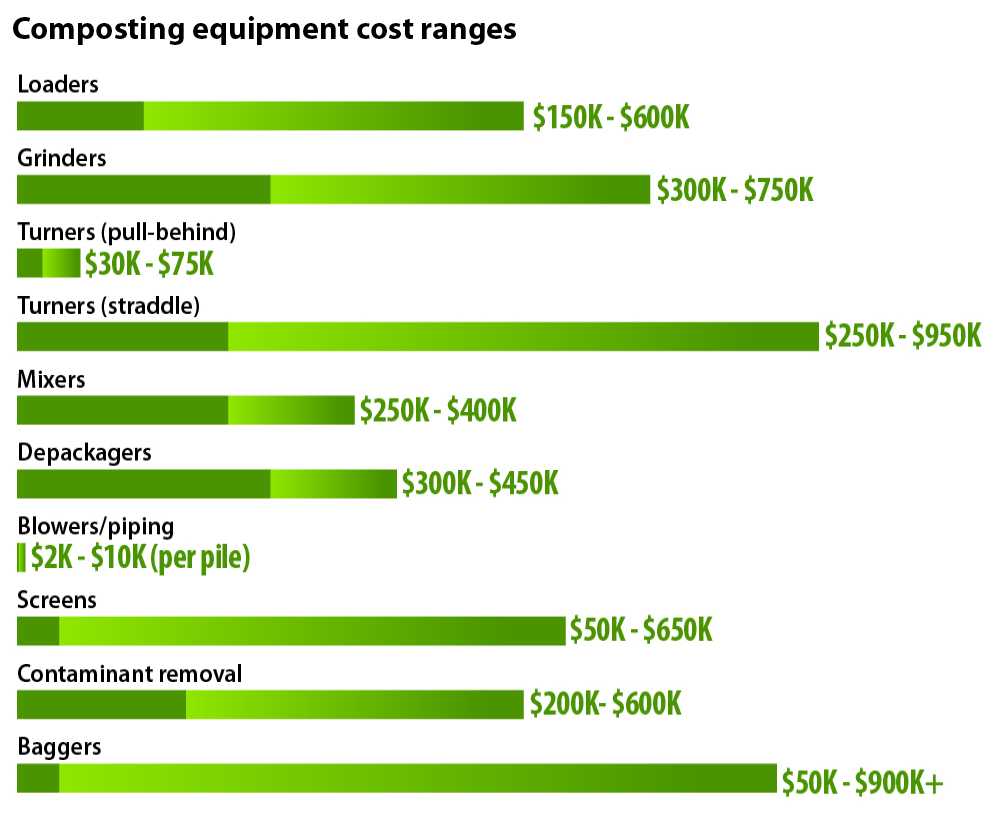
Figure 2. Composting equipment cost ranges
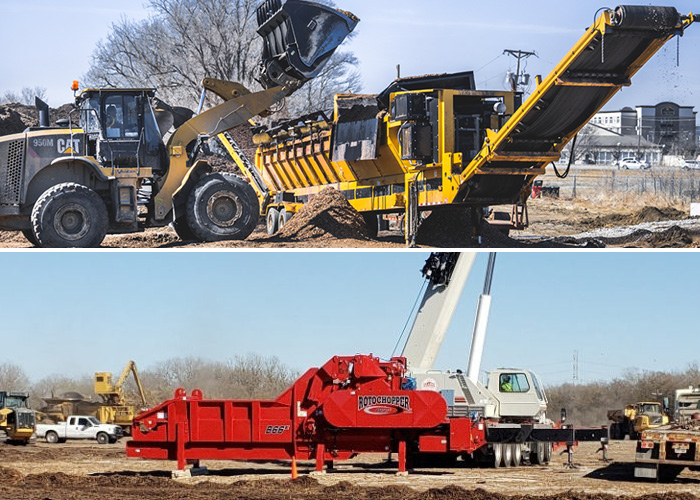
Vermeer trommel screen (top) and Rotochopper horizontal grinder (above) are examples of equipment purchased or leased for compost manufacturing.
Operating Cost Estimating
Composting is essentially a materials handling exercise. It takes a certain amount of time, at a certain cost, to perform each task in the compost manufacturing process. For new facilities, those costs can be estimated with a time-and-motion projection. For existing facilities, operating expenses can be measured in a similar manner along with detailed cost accounting of equipment costs.
An example of performing a costing exercise is shown in Table 3. This estimates the total annual cost of operating the proposed 40,000 tons/year industrial residuals composting facility noted above.
These types of costing exercises can be used to help make equipment decisions, e.g., one composting facility used this approach to decide whether to keep moving compost into the curing area with loaders, or to invest in a dump truck to move the compost. This calculation step is repeated for each task in the compost manufacturing process, then summarized to provide a projection of the entire facility’s annual operating cost.
For operating facilities, this same time-and-motion approach can be used to pin down your actual operating costs. As with projections, the actual cost analysis is based on your actual loaded labor rates plus your measured machine costs. Loaded labor rates include the pay actually paid to the worker, plus amounts needed for employer Federal taxes and State Unemployment Insurance, plus any fringe benefits you pay your workers. The machine rate is the cost of owning or leasing and operating a particular piece of equipment. The machine rate is a compilation of fixed costs, operating costs and labor costs that are expressed over a particular unit factor, usually dollars per hour. The machine rate multiplied by the actual or estimated hours of use in a budget year gives the annual projected cost for that piece of equipment.
Net Present Value Analysis
One method of comparing alternatives such as site development costs for one site versus another, or for one model of specific equipment versus another, is to compute the Net Present Value (NPV) of each alternative over the expected life of the alternatives. To keep the math simpler, I normally use a 10-year economic life. These analyses are relatively simple with an Excel spreadsheet.
NPV analyses are often used in financial investment analyses as they model cash flows in and out over the anticipated life of the investment. In engineered facility projects, they can be used to model only the outgoing cash flow of several alternatives, provided all alternatives have the same economic life and produce the same quantities of outputs. The calculation includes initial capital cost, capital costs of replacements during the modeled economic life, operating costs inflated by the Congressional Budget Office inflation forecast, and avoided costs (if any).
These costs are then expressed in current dollar terms using a discount factor equal to the average weighted cost of equity vs. debt capital (for municipal projects, the bond rate for the municipality can be used). If these assumptions hold true, then the alternative with the least NPV is the best financial alternative. Alternatives with less than a 10% difference between them are considered financially equal at this level of analysis.
Craig Coker is CEO of Coker Composting & Consulting near Roanoke VA and is a Senior Editor at BioCycle CONNECT. He can be reached at ccoker@cokercompost.com.