Top: Heat from the composting process warms the the radiant floor in the greenhouse. Nutrients from the fish waste (tanks in background) are processed to fertilize the crops. Images courtesy of Country Oaks Landscape Supply
Nora Goldstein
Country Oaks Landscape Supply (Country Oaks) in Burton, Michigan, founded in 1987, began composting yard trimmings in the mid-2010s. The turned windrow composting operation complemented an existing mulch production facility, expanding product offerings. Mark Cherry, second generation owner of Country Oaks since 2001, took a compost operator training course to learn the fundamentals. “I was more interested in the end product than the tipping fees,” he recalls. “There is not a lot of composting infrastructure in this part of the state.”

Panoramic view of Country Oaks Landscape Supply, showing, from left to right, the end of the composting pad, new greenhouse, biofilter, CAHR unit, the shop and sales building, and back to the composting pad and recessed channels. Photo by Jason McCune-Sanders, Agrilab Technologies Inc.
The facility ran into odor challenges, primarily when turning piles that had become anaerobic. Odor complaints ultimately led to the municipality issuing a warning that if Country Oaks did not address the situation, its composting operation would be shut down. “I knew that to solve the problem, my best option was to switch to an aerated static pile system,” notes Cherry. “I took a class on compost pile aeration at the US Composting Council Conference in 2019, as well as did a lot of research — including the option of combining aeration with compost heat recovery. I decided it made sense to go with that option, as I could use the recovered heat in a pole barn we had built for product storage and a sales office.”
Cherry connected with Brian Jerose, owner of Agrilab Technologies, Inc. (AGT) in Enosburg Falls, Vermont, which designs and installs compost aeration and heat recovery (CAHR) equipment. AGT installed an AGT Compost Hot Box 250-8R unit, which has 8 compost zone intakes and vapor recirculation capability. The composting pad is 100 feet by 200 feet. “The system, which began operating in February 2020, runs on two 3-HP aeration blowers that can push or pull airflow through the pipes installed in concrete trenches in the aeration floor under each zone,” explains Jerose. “When operating in the negative aeration mode, vapor comes through the pipes [ductwork], passes through a sump tank to remove condensate, and then goes into the heat exchanger. Water and glycol circulate through the heat exchanger, which capture the thermal energy in the vapor stream. That tubing connects via an underground insulated pipe to the radiant floor in the pole barn.”
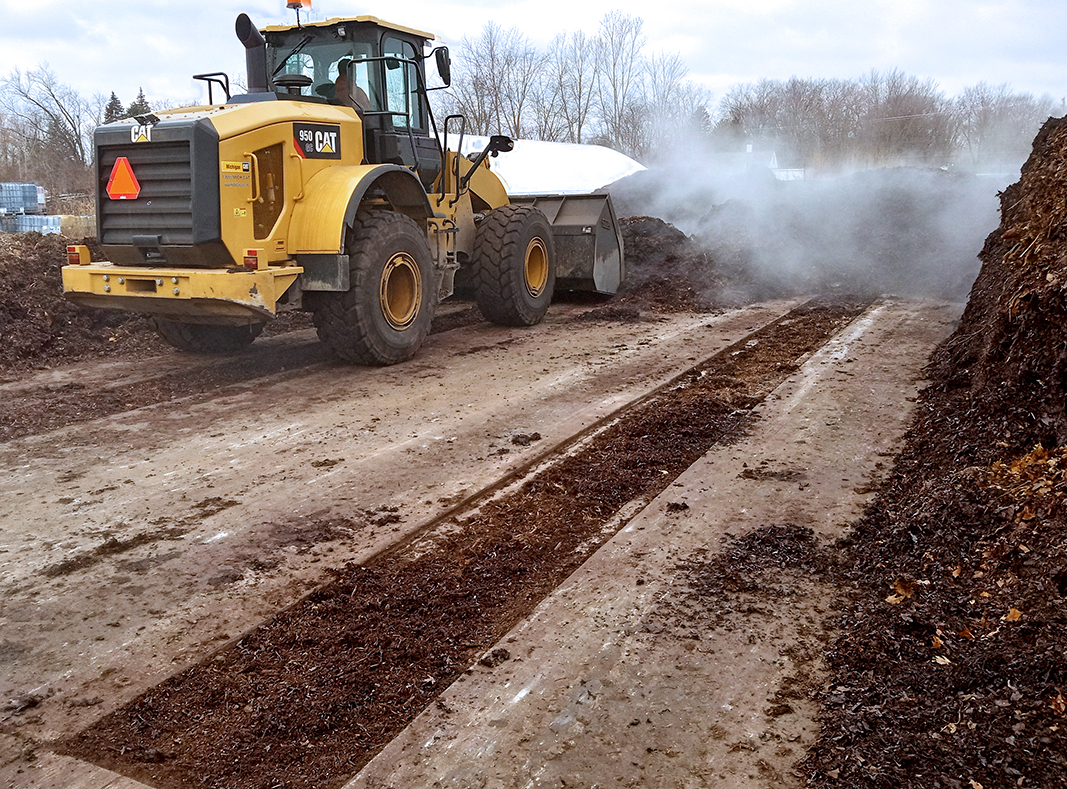
The 100 foot by 200 foot, 8 zone composting pad has pipes in the trenches of the aeration zones (above). The system runs in both positive and negative aeration modes.
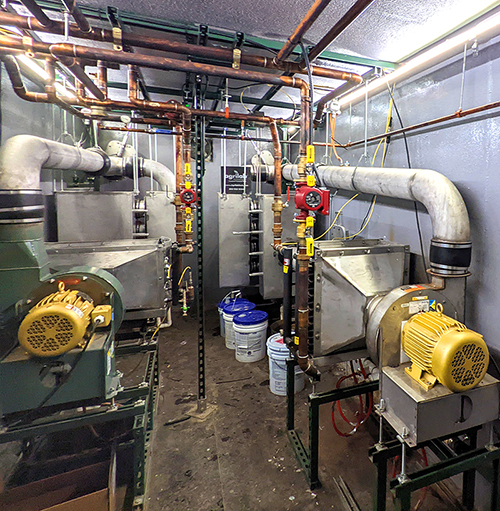
Heat exchangers and piping inside the AGT Compost Hot Box 250-8R. Photo courtesy Agrilab Technologies, Inc.
The recovered condensate can be used to irrigate the compost biofilter. The airflow also can operate in the positive mode to maintain a minimum of 10% oxygen in the active compost or to have hot exhaust recirculated into new compost piles to give the temperature a boost. Country Oaks starts new piles on positive aeration to build up the heat, and then switches to negative aeration. The company contracts with AGT to remotely monitor and manage the composting aeration system, including optimizing the use of positive/negative operating modes and heat recovery. Since the CAHR system was installed, the facility has not received any odor complaints.
Food Waste Collection
Country Oaks composts 10,000 to 15,000 tons/year of source separated organics, or between 30,000 to 35,000 cubic yards/year. “About 97% of incoming feedstocks are yard trimmings, and the rest is food waste that we collect from commercial generators,” says Cherry. “We purchased a truck with a cart lifter, which tips the food waste into the top of the truck. All food waste is accepted, as well as soiled paper and BPI-certified compostable products. Customers are provided 32- and 64-gallon carts for their food waste. We’ve only been collecting and composting food waste for about 10 months so are relatively new to it.”
The active aerated composting phase is about four to five weeks. The curing phase is anywhere from three to eight months. The piles are turned during curing to homogenize the compost after the static aerated phase. Country Oaks has two trommel screens; one is primarily used for mulch production, and the other for compost screening. “During the winter, however, we use both screens for compost so that we build up plenty of inventory for the spring season,” explains Cherry.
Products include a wide range of soil blends, including compost-based soils for storm water management and erosion control. Country Oaks owns a Rotobagger unit (manufactured by Rotochopper) that can be used to fill sediment control socks. It also supplies mulches, compost and soil blends in bulk and in bags to area garden centers.
The CAHR has increased compost process efficiency and significantly cut diesel fuel costs, adds Cherry. “It also saves on labor. The entire process is more hands off, especially as AGT oversees aeration and heat exchanger management.”
Aquaponics Venture
The ability to recover and circulate heat combined with Cherry’s ongoing interest and willingness to diversify Country Oaks’ offerings, led to the launch of an aquaponics enterprise in 2021. A 3,500 sq. ft. greenhouse was constructed, along with two 1,000-gallon fish tanks to raise tilapia. Cherry worked with Jim Gill, founder of Aqua Growers of Michigan, to build and manage the aquaponics system. A second heat exchanger was installed in the AGT Compost Hot Box 250-8R to recover additional thermal energy from the composting process to heat the aquaponics operation. The glycol and water tubes inside insulated Badger pipe run underground from the heat exchanger to the fish tanks. The desired temperature in the fish tanks is 73°F to 78°F; the warm air also is used to provide radiant heating in the greenhouse.
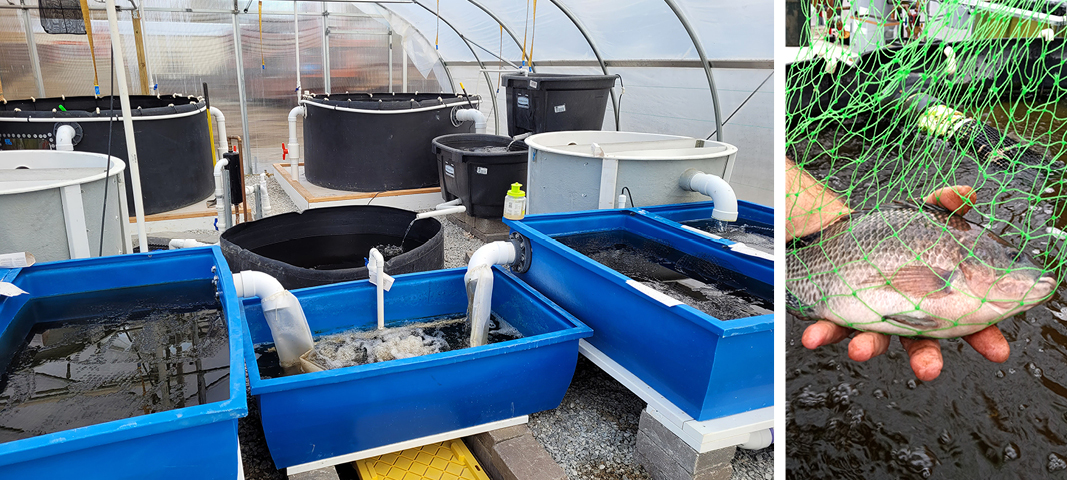
Fish waste in the tanks (rear) flows into clarifiers (center) to separate the solids from the nitrites. Microbes on floating biofilters (foreground) consume the nitrites and convert them to nitrates for the plants to absorb. Greenhouse-raised tilapia on right (inset).
The fish waste in the tanks goes through a clarifier to separate the solids from the nitrites. (The solids are removed and composted.) Microbes on a floating biofilter consume the nitrites and convert them to nitrates for the plant roots to absorb. “We are definitely on a learning curve since we started up the system last fall,” notes Cherry. “The tilapia requires specific conditions to thrive, and the plants require specific nutrients to grow, so optimizing the process for both fish and plants is critical. Everything is going well. We are growing lettuce, herbs, kale, tomatoes and other plants and selling the produce to restaurants and other customers. At this point, we do not have a market for the tilapia.”
All in, Country Oaks has invested about $500,000 in the transition from windrow composting to aerated static piles with heat recovery and the aquaponics enterprise (view process in this video on Facebook). Around $350,000 of that amount was for the CAHR equipment, biofilter and working pad improvements.The labor, heat and fuel savings are significant, and compost and soil blends sales are strong. The CAHR system enabled the site to increase total production on a smaller physical footprint. “It’s too early to gauge our return on investment,” says Cherry. “But we have achieved our goal of creating a full-circle, closed loop enterprise that contributes to building healthy soils, generating renewable energy, and growing fresh food.”