Nora Goldstein
The Caldwell family arrived in Morristown, Indiana in 1946 with the intention to start farming. Shortly after, Elmer Caldwell, the family patriarch, learned that his fields were full of gravel. That gave birth to a business crushing rock, selling gravel and paving, which in turn gave birth to opening a landfill in a gravel pit. Eventually, collection, trucking and recycling were added. The Caldwell family continued to farm and raise livestock on about 1,500 acres, but it was a sideline enterprise.
In 2017, the Caldwell’s sold the landfill and its trash collection routes to Advanced Disposal. Jordan Caldwell, Elmer’s great-grandson, became the general manager of that business unit. In 2019, he decided to leave Advanced Disposal and start a food waste composting company, Caldwell’s Inc. “We always had a yard waste composting operation at the landfill, where we would divert leaves and brush from incoming loads, grind and compost them, and use the end product as landfill cover or on newly seeded areas,” says Caldwell. “A few years before my father sold our landfill company, I was in charge of special waste, which involved bidding on contracts to haul sludges, food waste and liquids. Time after time we lost those bids to composting companies. I kept thinking we should get into composting those materials.”
Morristown is about 20 miles from Indianapolis “as the crow flies.” Several established composting companies service commercial food waste generators in Indianapolis, so Caldwell decided to keep his focus on industrial and food processing streams. He bought farmland from his father and is continuing to raise livestock and grow corn and soybeans. “Caldwell’s, Inc. has three divisions — composting, farming and transportation,” he adds. “We haul special waste, sand and rock, compost and other materials. We can’t pick up trash because of a noncompete agreement with Advanced Disposal, but we can collect organics.”
Composting Logistics
Step one in establishing a composting operation was getting a land application permit — which covers an industrial composting facility — from the Indiana Department of Environmental Management (IDEM). The process took about a year, and Caldwell’s Inc. opened for business in April 2020. The permit allows any material that is food or derived from food to be accepted. Other nonhazardous industrial organic wastes need to be approved by the state, which is about a two-week process.
Caldwell had met Phil Brown of Brown Bear Corporation, who was the first person he spoke with about his plan to open a facility. “Phil took time to explain the mechanics of industrial composting, and helped me put a business plan together,” he notes. “He also provided a lot of how-to composting guidance.”
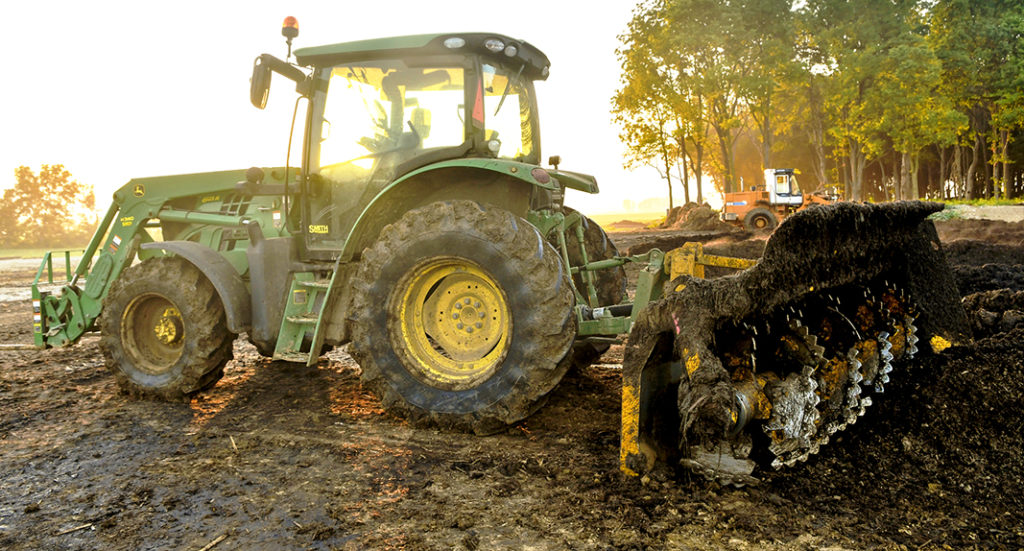
Caldwell’s purchased a Brown Bear Model PTO PA 35-3 — power take-off paddle aerators with a 35-inch rotor diameter. It attaches to a John Deere tractor. Photos courtesy of Caldwell’s, Inc.
The active composting pad is about 3-acres. It has 2 feet of compacted clay, with a soil-stabilized surface to provide year-round access. Two ponds collect leachate and storm water. The facility is sized to accept 5,000 to 10,000 tons/year of industrial food waste; 95% of the food waste is collected by Caldwell’s Inc. Carbon amendments include straw, wood chips and corn “shuckledge.” “After we harvest the corn, we use a combine with a cutter head to cut the stalk to about a 6-inch stub,” explains Caldwell. “The shuckledge blows out the back of the combine. It gets raked up and we use it for bulking agent.”
Incoming loads of food waste are tipped onto a concrete pad that is roughly 20-feet wide and 50-feet long and surrounded on three sides with 3-foot high concrete jersey barriers. A bed of amendment is laid down, and the food waste is unloaded on top. A bucket loader or excavator is used to mix the materials, which are transported to the composting pad and formed into windrows.
Caldwell’s purchased a Brown Bear Model PTO PA 35-3 — power take-off paddle aerators with a 35-inch rotor diameter. It attaches to a John Deere tractor. “As a farmer, Jordan is intimately familiar with agricultural tractors, so it made the most sense to select a turner attachment that is used with a tractor in his fleet,” notes Phil Brown. “The model selected works with a tractor with 100 to 160 horsepower and will handle the volume of feedstocks anticipated in the first one to three years of the operation.”
Brown recommended building windrows that are 10-feet wide at the base and 3.5-4-feet tall. “There were a few hiccups in the beginning because the windrows being built were oversized initially,” adds Brown. “That overloads and overworks the tractor.”
He recalls that the very first batch of material received was ice cream, which is tricky to compost because it becomes odorous quickly. Another challenging feedstock in the early days was corn syrup. “That threw us for a loop, as we were trying to figure out the C:N ratio for corn syrup,” he says. “The C:N ratio got out of proportion but before long we got it figured out.”
The windrows are turned once a week during the active composting phase, which ranges from 30 to 60 days. Material is then moved from the pad and cured for another 30 days. All of the finished compost, which is not screened, is used on the farm. “We test it before we spread it on the fields to be sure it is mature,” says Caldwell. “If there is a hot spot, we are able to go back in time and see what caused it.”
One challenge has been maintaining a proper pH in the aerated collection ponds. Key is keeping the pH at neutral and maintaining low BOD (biological oxygen demand) levels. The ponds have been a source of odors, so Caldwell’s is installing a Byers Scientific odor mitigation system that pumps out an odor neutralizing mist. Pipe to spray the mist has been installed around the perimeter of the entire composting facility.
Next Steps
With a year of composting under his belt, Caldwell is looking to service more food waste generators in the region. The company is in the process of permitting a T30 Scott Equipment depackager to enable it to receive packaged material from food distribution centers and warehouses, as well as food manufacturers.
“IDEM requires that we get a solid waste processing permit for this operation,” notes Caldwell. “Our intention is to recycle the packaging, but IDEM says we will be producing waste and therefore are required to get the processing permit.”
Other equipment on the wish list is a grinder and a screen. “We would like to get the bigger chips out before we land apply the compost,” he adds. “The first batch of finished compost was applied to the fields in March. We want to test the compost first by using it ourselves before we sell it.”