BioCycle June 2013, Vol. 54, No. 6, p. 12
The Dalles, Oregon: Composter Benefits From Brewery Residuals
Before Dirt Hugger opened its composting facility several years ago, founders Pierce Louis and Tyler Miller were approached by some local microbreweries in the Hood River region about processing their brewery wastewater. Dirt Hugger composts yard trimmings, clean wood and source separated food waste from commercial generators in positively aerated static piles. Once established, the company reached out to area brewers about receiving their material. “From a composter’s perspective, liquid brewery waste is a great way to add revenue without adding volume,” says Louis. “Hood River ‘unofficially’ has the highest number of breweries per capita, and the wastewater treatment plants will stop taking their liquid waste if the BOD (biological oxygen demand) gets too high. Some of the breweries were trucking their wastewater 60 miles away to Portland to be treated.”
Louis states, “This relationship is win-win because breweries need to get rid of the waste and we need moisture for our piles. We can reduce their costs over wastewater processing because the microbes essentially do the evaporation for free. The added bonus: brewery waste has a small amount of nutrient, which adds to our compost vs. only applying water.”
Camarillo, California: Sharing The Compost — And The Harvest
Farm Share Organics in Camarillo not only turns yard trimmings into compost and works with another company to turn food waste into animal feed, it uses compost and revenue from the sales of animal feed to generate donations to area food banks. Farm Share, launched by CEO Dave Hare in 2009, donates compost to farmers who then donate fresh organic produce to their local food bank. Hare also uses the proceeds from compost sales to buy fresh food or fruits and vegetables for food banks. He operates two sites in an unincorporated, agricultural area of Ventura County — a 750-acre lemon and avocado orchard and a 340-acre certified organic farm. Farm Share, which has been composting for about three years, processes about 200 tons/month of organics, including about 100 tons/month of green waste from local haulers, and produces about 100 tons of compost monthly. Compost is sold in bulk, mostly to lemon, avocado and raspberry growers.
Materials are composted on a clay pad in static piles that are about 6-feet high and 120-feet long, The composting process takes about 12 weeks. Grinding is done using a Vermeer TG-525 tub grinder. “It has a duplex mill which is really forgiving,” Hare explains. “If metal or some other type of foreign object causes damage, we can change a hammer or tooth in 20 minutes.” Compost sales have been growing steadily. Benefits include an approximate 30 percent reduction in water needed to grow crops, and yield increases of at least 30 percent compared to using chemical fertilizers.
Concord, North Carolina: County Approves Composting Contract
On May 20, the Cabarrus County Board approved a contract with Agromatters, Inc. to operate a 15-acre composting site at the county’s Construction and Demolition Landfill in Concord. Agromatters is a private composting firm based in Huntersville, North Carolina. According to Kevin Grant, the county’s sustainability manager, the public/private agreement calls for the county to receive a royalty for the incoming food waste, as well as a percentage of the compost produced at the site. Cabarrus County would use the compost on its athletic fields as well as its incubator farm. “The hope is also that some of this compost can be used at various school garden projects within the county,” Grant says. Agromatters also agreed to offer tours to school classes to learn more about composting.
The next steps include Agromatters obtaining a compost operating permit from the North Carolina Department of Environment and Natural Resources as well signing agreements with the cities of Concord and Kannapolis to send their yard trimmings to the facility. Agromatters is also in the process of initial site preparation. Initially, the company plans to obtain a Type I compost operating permit to begin processing yard trimmings later this fall. About 25,000 tons/year of yard trimmings would be composted. In year two, Agromatters hopes to receive a Type 3 permit, so it can begin composting 15,000 tons of food waste annually, Grant says. Because the county only has about 15 acres of available space, officials are uncertain whether to expand the C & D operation. “It’s valuable land, so it makes sense for the county to get involved in composting rather than just placing waste in the ground,” he adds.
Lake Bluff, Illinois: Compost And Mulch Producer With Longevity
DK Organics has operated a composting and mulch production facility in Lake Bluff for over 20 years. The company was started by David Gorter shortly after the state of Illinois enacted a yard trimmings disposal ban in 1988. Recognizing the potential unfolding, Gorter scrambled to become educated enough to enter the organics recycling business. The company prides itself in creating top quality products. Two years ago, DK Organics was among the first composting and mulch facilities to purchase a Doppstadt DM trommel with a star screen insert. “We had been running a 1.5-inch drum but recognized we weren’t getting the product we wanted in the time we wanted with the quality we aim for,” notes Operations Manager Andrew Mariani. “We are now able to do in a day what had previously taken a week to run. The increase in product quality is also dramatic.”
DK Organics uses only clean, controlled yard trimmings and landscape material. After primary shredding, a variety of mulch products are made, some of which are double or triple ground. Source materials include southern hardwood bark, premium hardwood and leaf mulch. Color and texture is crafted through precision aging. Composts are produced with an initial grind, after which the material is windrowed and aged for two to three months.
Brattleboro, Vermont: Curbside Food Waste Collection Expanded
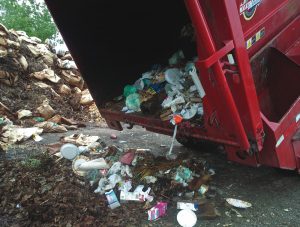
The Town of Brattleboro expanded its residential food waste collection pilot in May to service 800 households.
Triple T unloads the food waste and soiled paper at WSWD’s composting site, located at the District’s closed landfill. Materials are mixed with yard trimmings collected during the fall and the spring and put into static piles that are turned with a front-end loader. “There is a sawmill across the street from our site so we also are getting sawdust and wood chips,” says Spencer. “The food waste we are getting is very clean.” The district charges Triple T $50/ton for the organics. The tipping fee at the landfill the hauler uses is $100/ton.