Composting is never odor-free, even under optimum conditions for aerobic decomposition of organic matter. Here are some tried and true strategies to maintain successful operations.
Craig Coker
BioCycle February 2016
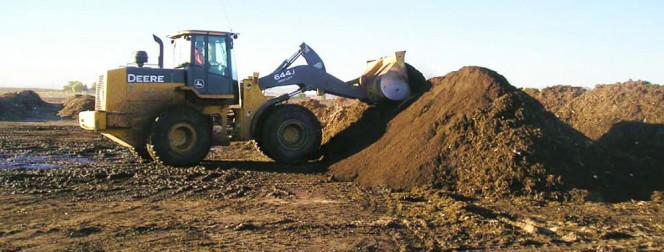
Once a pile or windrow is built, a 3- to 4-inch cap of compost placed over it will act as an in situ biofilter for fugitive emissions.
Odors are gaseous chemicals that are emitted into the air from a variety of sources. Some are considered pleasant by many, like methyl salicylate (the smell of wintergreen Altoids®) or homofuronol (the smell of baked bread). Others are less tolerated, like skatole (the smell of manure) or dimethyl disulfide (the smell of rotting vegetables). These gases are detectable by the human nose at various levels of concentration in the air. Some of these chemicals can be detected at extremely low concentrations.
What’s That Smell?
The human nose has 400 types of odor detectors, called olfactory receptors; each type is paired with a matching olfactory gene in that person’s DNA. By contrast, the human eye has only three types of receptors (blue, green, and red ranges of the color spectrum) and human taste buds have only five types of receptors (sweet, salty, bitter, sour and savory). Humans have around 900 genes that can code olfactory receptors, allowing us to detect up to 10,000 different odors; how each is perceived depends on the DNA sequencing of those 400 types of odor receptors. This is why the smell of 2-heptanone (the smell of blue cheese) is pleasing to some, and unappealing to others. This is also why odor problems at composting and anaerobic digestion facilities are so difficult to resolve.
Organics recycling facilities, whether based on aerobic composting or anaerobic digestion, have one thing in common; they manage the process of decomposition. Decomposition is a biological and chemical process whereby complex biochemical compounds are broken down into their constituent building blocks. Aerobic decomposition is the cornerstone of composting. For example, the main ingredients of food scraps to be composted are proteins, carbohydrates and fats. These three components are made of various combinations of carbon, hydrogen, oxygen, nitrogen and sulfur. Decomposition of these compounds follows a well-evolved sequence of decay events.
Each decay event produces categories of decomposition products that have several subcategories, many of which are intermediate by-products of the process. For example, proteins decompose into their component polypeptides, which in turn, decompose into their component amino acids. At each stage of the decomposition process, there are a variety of different organic compounds produced, each with its own volatility characteristic. Think of the volatility characteristic of a compound as its potential to become a gas and produce odors.
Volatility is the tendency of a substance to vaporize, which is proportional to a substance’s vapor pressure. At a given temperature, a substance with higher vapor pressure vaporizes more readily than a substance with a lower vapor pressure. As an organic material decomposes, the mix of volatile compounds change, so the mix of vapor pressures changes, which can change the characteristic odor. Some odors are produced by the biological changes in compounds by microorganisms; others are due to chemical changes in the composting pile.
A composting pile is a highly dynamic ecosystem, constantly changing over the 21- to 60-day life of the active composting phase. Factors that influence odor generation include: feedstock composition, activity rates of the decomposers doing the work, availability of the nutrients in the feedstocks to the microbes, how well mixed the feedstocks are, and several physical factors, such as moisture content, particle size, oxygen content and diffusion, and temperature. Odors also arise from other areas in the facility, including feedstock receipt and processing, curing and product management and from site conditions like puddles of rainwater.
Blowin’ In The Wind
Good site design and not erring from the fundamentals of compost processing are important factors in minimizing the potential for adverse odor episodes at composting facilities. Successful operations require careful consideration of siting factors that can influence how neighbors react to odor episodes. The first step is to construct a wind rose (Figure 1), an illustration of the direction and speed of the wind.
Once the prevailing wind directions and speeds are known, potential impact of the layout and operation of the site on receptors can be considered. For initial siting and site layout, locate waste management aspects of the facility at least 1,000 feet (and preferably 1,500 feet) from any sensitive receptors in the predominantly downwind direction (south, south-southwest, and southwest in Figure 1). A sensitive receptor can be defined as any place where members of the public may gather, such as a house, a school, a park, a church or a shopping area. Plan on a thickly vegetated buffer of fully developed vegetation in that direction so that vegetative surfaces can intercept and filter particulate matter that may contain odorous compounds. Orient the site so that odor-producing activities are sheltered by trees, hills, buildings, walls and other features that break up the wind pattern to create turbulence.
Other site planning and development steps that can reduce potential for odor problems include: leaving room for equipment to get to piles or windrows for implementing odor best management practices as needed (such as installing a compost cap or watering windrows prior to turning), and designing the site for rapid and effective runoff and drainage management to prevent odorous puddles from forming.
Best You Can Be
Composting is never odor-free. Even under optimum conditions for aerobic decomposition of organic matter, odors are going to form. However, failure to maintain conditions for the optimum microbial environment is guaranteed to make odors worse, particularly those odorants that people find annoying or unpleasant. The more odors that are formed due to poor composting conditions, the more quantities of that odorant escape into the atmosphere, and it becomes much harder to disperse those quantities below annoyance thresholds.
Microbes live in a thin watery biofilm around each particle in the pile and draw their life-sustaining oxygen from the air flowing through the pore space in the pile (Figure 2). So the first step in controlling the microbial activity is a mix that adheres to good Best Management Practices: the right nutrient balance between carbon and nitrogen (at least 25 parts of carbon (C) for each part of nitrogen (N), on a weight basis), adequate moisture to form and maintain the biofilm (around 50-55%) and enough structural porosity to ensure a free air space of at least 40 percent to keep oxygen levels above a 8 to 10 percent minimum.
Water, Water Everywhere
Assuming the C:N ratio is dialed-in correctly, the correct moisture content advances the rate of decomposition. If the biofilm around the particles dries out, microbial activity will go dormant and composting will stop. As piles dry out, the concentration of potential odorants in the biofilm increases, with a risk of odor emissions. Conversely, if moisture is allowed to climb above 60 percent or so, the free air space channels between the particles clog with water. This thicker biofilm reduces the amount of oxygen available to the microorganisms on the surface of the particle as the rate of oxygen transfer in water is much slower than the rate of transfer in air. Material with an optimum moisture content of around 50 to 55 percent has the consistency of a wrung-out sponge that is wet but not freely dripping water. One of the challenges in composting food scraps with large amounts of vegetable and fruit material is that the plant cell walls break open readily under the heat of initial decomposition, flooding the pile with water. Without adequate structural porosity to allow that flush to drain out, the pore spaces in the pile will fill with water and risk formation of anaerobic conditions.
The transfer of oxygen across the biofilm requires a steady flow of air through the pile. Whether by natural or passive means, or forced through a pile by a blower, aeration serves several critical functions in process management, including replenishment of oxygen, removal of carbon dioxide (and volatile odorants), and removal of heat. Composting piles and windrows have both macro-aeration and micro-aeration characteristics. Macro-aeration refers to the overall uniformity of the structural porosity of a pile. A composting pile of wet dairy manure mixed with sawdust has low macro-aeration characteristics. A composting pile of chipped tree waste has good macro-aeration characteristics. Good macro-aeration characteristics are necessary where passive aeration is the primary means of oxygen transfer, like in windrows. Micro-aeration characteristics refer to how well air moves inside the pile. Fine particles, such as those produced by processing woody wastes with a hammermill, can impede aeration rates in various areas in a pile, creating air-starved sections.
In addition to good site design and good process management, there are a number of proactive, positive strategies compost site managers and staff can implement that will greatly reduce the risk of off-site odor episodes. It is helpful to break down the various composting process activities that cause odors into a series of discrete elements, and then analyze each activity within that specific element to identify ways odors are being formed, volatilized, and dispersed off-site. By investigating each processing step composters may be able to identify specific management practices that could help minimize these odors.
Do We Really Want This?
An important first step is to understand the odor-causing potential of each feedstock and either reject it or be sure the facility can effectively handle the material. A feedstock acceptance protocol is a good tool to understand the nature of incoming materials before deciding to accept them. A sample of a potential feedstock can be put into a sealed bag in order to mimic the anaerobic decomposition process. Place the sealed bag in a warm place for two to three days (a car dashboard works well) and then have someone whose sense of smell has not been compromised by working at the composting facility open the bag and give an indication of the intensity and unpleasantness of the smell. If objectionable odors are noticed, then the composting facility operator will know to have plenty of coarse bulking agent on hand when this feedstock arrives, in order to ensure that aerobic conditions prevail during composting.
Prompt handling of feedstocks is another important odor-minimizing strategy. If possible, the operator should get incoming feedstock processed and mixed with amendment within one hour of receipt. If that is not possible, then the pile of feedstock should be covered with a 3- to 4-inch layer of unscreened compost or woody grindings. In any case, mixing and emplacing of those feedstocks in a windrow or in an aerated pile should be attempted by the end of the day. If a load comes in late, it might be necessary to cover it with compost or grindings and then mix it up first thing the following morning.
As noted, getting the mix right and keeping piles aerobic is the most important aspect of process management in odor control, but there are other operational considerations that will help. Watch the loader operators to be sure they are not driving up on a pile or windrow to place materials, which will compact under the weight of the loader and compress out the free air space. Once a pile or windrow is built, put a 3- to 4-inch cap of compost over it to act as an in situ biofilter for fugitive emissions. If windrow composting, don’t turn that windrow for the first 7 to 10 days. This allows primary decomposition of highly degradable organics to occur with some degree of control. (Note: piles must have good structural porosity for this to work.) For those windrows with adequate free air space, and assuming there are no regulatory obstacles, consider reducing turning frequencies for the first two weeks, turning only to distribute moisture from a rainstorm or for improving water distribution when irrigating.
Keeping an eye on the weather, the calendar and the clock also will help. Activities that generate odors, like mixing, turning windrows, and moving fresh piles, should be minimized at certain times, provided that operations can tolerate the disruptions. For example, when the air is heavy and still — which can be defined as a wind speed below 4 miles/hour and a less-than-10°F difference between the ambient and dew point temperatures — keep odor-causing activities to a minimum. In addition, conducting odor-producing activities between 10 AM and 3 PM, when the sun has heated the atmosphere to promote good vertical mixing, and refraining from those activities late in the afternoon on Fridays and the days before holidays (when neighbors are likely to be out in their yards or at public places) can also minimize odor episodes.
Keep It Clean
The two most important site management practices to reduce odors are rigorous housekeeping and water management. Housekeeping is always important at a composting facility, as every bit of stray organic matter not incorporated into a pile is a potential odor source. It requires dedication to focus an hour per day on housekeeping patrol, where stray bits of mashed food scraps or clumps of grass clippings are picked up and put into a pile. Managerial complacency about housekeeping can quickly spread through the facility workers, and soon, there are so many potential fugitive odor emissions that it becomes almost impossible to get the site cleaned up and back into shape.
Rainwater puddles and storm water ponds are a potentially onerous source of odors. Compost fines wash into every puddle and pond on a site. They exert strong biological and chemical oxygen demand that will quickly deplete the dissolved oxygen (DO) in the water — faster than the oxygen can be replenished across the water-air interface. This creates anaerobic conditions in the water with the resultant formation of hydrogen sulfide. Larger storm water ponds, if not mixed and aerated, will stratify during the summer into different levels of temperature and DO. Compost fines washed into those ponds will accelerate consumption of DO, so, in the fall season when stratification ends with cooler temperatures, the layers in the pond will mix together, bringing anaerobic waters to the surface with a release of odors.
Managing odors in composting is never easy and requires a constant vigilance. Failure to do that, however, is usually a prescription for headaches, negative public relations and regulatory problems that can quickly lead to fines and shut down orders. As the great American, Benjamin Franklin, once said, “An ounce of prevention is worth a pound of cure.”
Craig Coker is a Senior Editor at BioCycle. He can be reached at ccoker@jgpress.com.