Florida county conducts pilot project to gauge its ability to manage yard trimmings and biosolids using internal resources — and to confirm marketability of the finished compost.
Beth Schinella and Bruce Clark
BioCycle March/April 2016
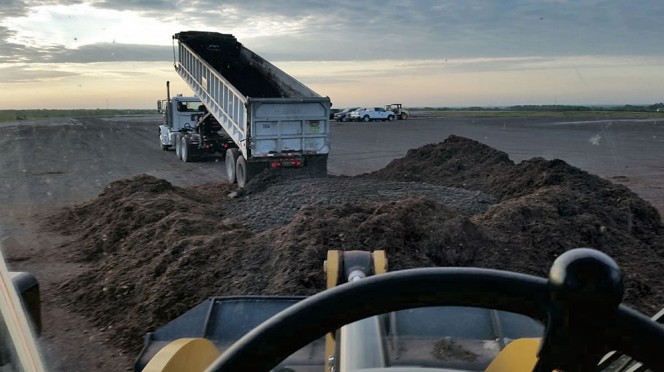
Yard trimmings ground to 6-inch minus are mixed with dewatered biosolids
(15-16% solids) in a 3:1 ratio. Photos courtesy of Hillsborough County and SCS Engineers
The pilot facility covered approximately 3 acres and was operated on an inactive lined cell on top of the 162-acre regional Southeast County Landfill. This landfill primarily receives ash from the County’s waste-to-energy plant. The closest residential occupancy to the landfill is more than a mile away.
The Public Utilities Department’s primary means of handling dewatered biosolids from its Falkenburg Road Advanced Wastewater Treatment Facility has been hauling it to various landfills for disposal using 22-ton capacity trailers. The pilot — which composted 2,640 wet tons of biosolids and 2,226 tons of yard trimmings in two batches — resulted in a reduction of the Plant Operations Division’s biosolids disposal costs and enhanced the Solid Waste Division’s landfill waste diversion goals by providing a beneficial product used as a soil additive for local farmers.
Success of the pilot led Hillsborough County to proceed with construction of an expanded composting facility that essentially doubles composting capacity. The larger operation covers approximately 7 acres within the same lined landfill area. The entire 7-acre pad will be made from continuous milled asphalt (asphalt left over from County paving projects), and includes the active composting windrows, the curing piles and the product screening area. The pad will be sloped to promote runoff, with the runoff from the active curing area (the 4 acre area) being separated from the runoff in the balance of the pad. The active area runoff is considered “leachate” and will be taken for treatment; the balance runs off over the landfill cover as storm water. The annual design capacity (biosolids and yard trimmings) of the full-scale system is approximately 29,000 tons.
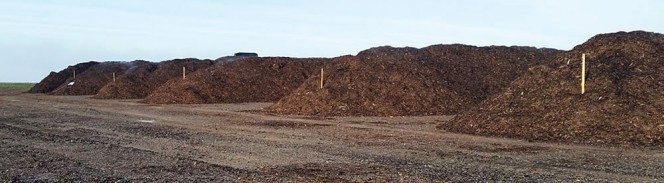
The pilot facility covered about 3 acres and was operated on an inactive lined cell on top of the county’s 162-acre Southeast Landfill. Photo courtesy of Hillsborough County and SCS Engineers
Composting Methodology
The pilot facility utilized the modified static aerobic pile (MSAP®) methodology originally developed by A1 Organics in Eaton, Colorado and Harvest Quest (an Ecoverse company). The MSAP method involves forming windrows of the mixed feedstocks, adding the Harvest Quest catalyst to the surface of the pile and capping each windrow with a layer of ground green waste or unscreened finished compost. The proprietary catalyst is an inoculant consisting of a variety of enzyme-producing bacteria, as well as fungi, contained in a natural organic carrier material that accelerates the decomposition process. The microbes multiply and move rapidly, initially populating the outer edges of the windrows just beneath the capping layer, and then working their way toward the center of the pile.
The ratio of green waste to dewatered biosolids (15% to16% solids) is 3:1. Hillsborough County contracts out grinding at its 3 yard trimmings collection sites to a particle size of 6-inch minus for adequate porosity in compost windrows. Materials are mixed with a loader and placed into the windrows. The capping layer helps to maintain internal heating of the pile and reduce generation of odors. The windrows sit undisturbed for approximately 30 days, then are mechanically turned twice in the final 15 days to ensure moisture distribution, material consistency and promote air transfer through the pile. There is a curing phase following the first 45 days — about 45 to 60 days more after which the compost is typically ready for screening and distribution.
The Florida Department of Environmental Protection (FDEP) allows use of the MSAP method as a modification of the Class A windrow process, not a separate equivalency for pathogen reduction. Operators need to record temperatures and demonstrate compliance with the standard PFRP method (U.S. EPA’s CFR40 Part 503 Process to Further Reduce Pathogens) for biosolids composting in windrows — minimum 15 days at 55°C (131°F) at each depth (10, 20, 30 and 40 inches).
Composting equipment used during the pilot program included a Backhus 21.55 self-propelled straddle-type compost turner, a Doppstadt SM 720 trommel screen with half-inch holes and a Caterpillar 950G front loader. The front loader was used to form the windrows and storage piles and load the finished product. Approximately 1,870 tons of finished compost were produced in the pilot program.
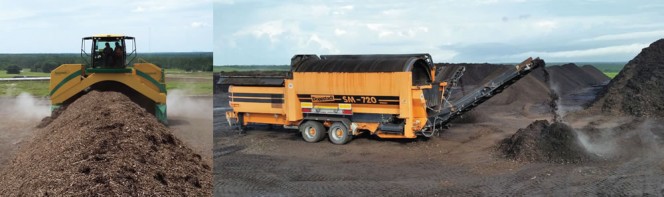
The pilot tested the Modified Static Aerobic Pile™ method, where active windrows sit undisturbed for about 30 days, then are turned twice (Backhus straddle turner, left) to assure moisture distribution and material consistency. After 45 to 60 days of curing, the county used a Doppstadt trommel (right) to screen finished compost. Photos courtesy of Hillsborough County and SCS Engineers
Although side by side comparisons to other composting methods were not pursued, County staff visited both traditional turned windrow facilities and MSAP operating facilities and determined that the projected cost savings, high quality end product and significant reduction in odors associated with MSAP facilities supported the decision to proceed with the pilot scale and larger scale operation.
Pilot Operating Data
The County collected operating data to monitor performance of the windrows, demonstrate regulatory compliance and confirm the quality of the finished compost product. A summary of the data is provided below.
Temperature: Except for a 7-day period at initial start-up, the active windrow piles recorded no temperatures less than 140°F at any sampling depth from 10 inches to 40 inches from the outside edge of the pile and moving inward at 10 inch increments. Over a period of approximately 7 weeks, the measured temperature of the piles was not less than approximately 150° to 160° F, except for 3 days. These results confirm compliance of the active windrow piles with U.S. EPA PFRP requirements for time and temperature (i.e., 131°F for 15 consecutive days) to demonstrate pathogen reduction.
Odor: Throughout the pilot project, both qualitative and quantitative odor assessments were conducted. Qualitative assessments were performed by on site personnel immediately upon arriving at the site by conducting a walk around of the project area. Minimal odors were detected at the onset of windrow construction but rapidly dissipated to nondetectable levels. Hydrogen sulfide (H2S) monitoring results showed primarily low concentrations with some infrequent erratic spikes believed to be the result of landfill based H2S in the general area.
The County recorded measurements of ammonia and dimethyl sulfide at the surface of the windrow piles shortly after construction of Batches 1 and 2 during the pilot. Drager tube sampling for ammonia and dimethyl sulfide detected concentrations at the windrow surface ranging from 0.25 to 27.5 parts per million (ppm) and 0.75 to 5.0 ppm, respectively. The higher ammonia concentrations were noted in Batch 2 and are believed to be associated with higher levels of nitrogen compared to Batch 1.
Chemical Characterization: The County collected and tested four samples of material from two batches of finished product. The sample from each batch included an unscreened and screened sample. Based on these test results, the finished compost can be classified as a FDEP Class AA product, the highest quality identified in the FDEP regulations. The Agricultural Index was determined to be greater than 10. This value means that the product is suitable for unlimited use on most all soils, as the chloride and sodium concentrations are low as to be of no concern.
Operating Issues, Future Plans
The composting partnership between Hillsborough County’s Public Utilities and Public Works Departments is expected to decrease current biosolids transportation and disposal costs by approximately 36 percent. Although the compost product generated by the pilot program was provided at no cost to two local sod farmers for application as a soil amendment, the County intends to market the product once the facility expansion is complete. The current average price for Class AA compost in Florida is approximately $11/ton.
For the most part, the composting program went smoothly. Notes Ron Wiesman, the County’s facility manager and operator: “This pilot has proven that composting with the MSAP process is very attainable in Florida’s wet conditions and provides a high-quality compost exceeding the FDEP requirements for Class AA compost. Obstacles noticed during the pilot were water retention on the pad near the active composting area that affected operations and timely rental of equipment before major weather conditions. These conditions have been addressed in the next phase as we move out of the pilot and into a production mode.”
While the impact of heavy rains and the associated runoff are known challenges for most open air composting operations, the design of the MSAP windrows with their characteristic capping layers is considered to have provided protection to the interior of the constructed piles thereby mitigating, to a certain degree, the negative impact associated with extreme wet weather events.
Hillsborough County is in the process of constructing the 7-acre expanded composting facility that is expected to operate on the inactive lined landfill cell for the next several years, until the cell area is needed for future waste disposal. In accordance with a Master Plan being finalized for the entire landfill site, the County then plans to proceed with construction of a more permanent facility on land owned and located adjacent to the current landfill. The heavy composting equipment to be used at the expanded operation is being competitively bid as a lease or lease-purchase arrangement. The end product has demonstrated market appeal and will be competitively bid for marketing and distribution.
The expanded composting facility is scheduled to be operational in April 2016. It is expected to save the Public Utilities Department, Plant Operations Division approximately $1.5 million in biosolids transportation and disposal costs over the next 5 years.
Beth Schinella is Division Director of the Hillsborough County Public Utilities Department-Plant Operations Division and a SWANA Certified Manager of Compost Programs. Bruce Clark, P.E. is a Project Director with SCS Engineers and SWANA certified (www.scsengineers.com).