Top: Vanguard Renewables’ new AD facility is located on the Goodrich Family Farm, a 900-head dairy. Photo courtesy of Vanguard Renewables.
Nora Goldstein
A third generation dairy farm in Salisbury, Vermont faced a harsh reality in 2009. The Goodrich Family Farm and the Vermont dairy industry overall were hit hard by the 2008 financial crisis. “We recognized that we had to diversify our income, and things were changing in terms of nutrient management requirements related to water quality,” recalls Danielle Goodrich Gingras, who returned in 2009 to work at the family farm. “But we still wanted to be a farm, and have a positive impact on our community.”
Goodrich Gingras’ brother, Chase Goodrich, came back to the farm the same year. They landed on the idea of installing an anaerobic digester, generating revenue from the sale of electricity, reducing manure-related odors, and improving the quality of the digestate in terms of nutrient availability. “We like to say it’s a new project that was more than 10 years in the making,” notes Goodrich Gingras. “We struggled with trying to develop the digester on our own, and then in 2017, Vanguard Renewables approached us about collaborating on installation of a digester to process our manure along with food scraps. Vanguard wanted to generate renewable natural gas (RNG) from the biogas. That led to working with Middlebury College as an RNG purchaser, and Vermont Gas to provide pipeline access and transmission. We all recognized that the positive impact on our community is so much greater working together than if we had worked individually to meet our goals.”
Vanguard Renewables built, owns and operates the anaerobic digester (AD) and related equipment. It leases the land the facility is on from Goodrich Family Farm. The farm, in turn, supplies the manure, and uses the digestate on its cropland. Construction was completed in June 2021, and the grand opening was held in July. The digester, which uses CH4 Biogas technology, has capacity to process more than 180 tons/day of unavoidable food and beverage waste from manufacturers, retailers, and distributors, and 100 tons/day of dairy manure. The Goodrich’s 900 cows provide the manure and Vermont businesses, including Ben and Jerry’s and Cabot/Agri-mark, supply the food waste. Those food waste streams are supplemented with slurried commercial source separated organics processed at Vanguard’s Organics Recycling Facility in Agawam, Massachusetts, and a new Casella Waste depackaging facility in Williston, Vermont.
Facility Tour
I toured the codigestion facility at Goodrich Family Farm in mid-July, several days before the grand opening on July 21. We started at the solids separation building, which is adjacent to the dairy barns. Six years ago, the Goodrich Farm installed solids separation equipment — two screw presses — and began using the solids instead of having to purchase sawdust as bedding for their cows. The barns have a gutter flow system, which are scraped with a skid steer. Some of the separated liquid is used to flush the gutters. The liquid manure is fed directly into the digester tanks.
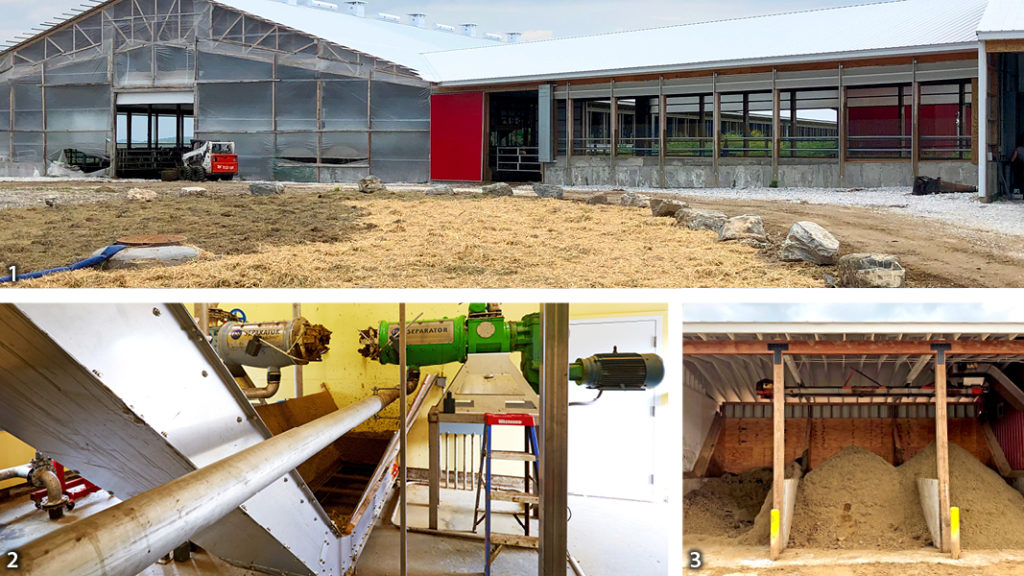
Manure is scraped from the gutters in the dairy barns (1) and pumped to the solids separation building (2). Separated solids (3) are used to bed the cows. The liquid fraction is pumped directly into the digesters.
From the solids separator, we walked to the 264,000-gallon hydrolyzer tank with two deck-mounted mixers. Incoming food waste is unloaded into the tank via a liquid line and a solids receiving tank. Both are equipped with trash screens to capture contaminants. The mixers circulate the contents before they are pumped to the digester tanks. Residence time in the hydrolyzer is about 5 days.
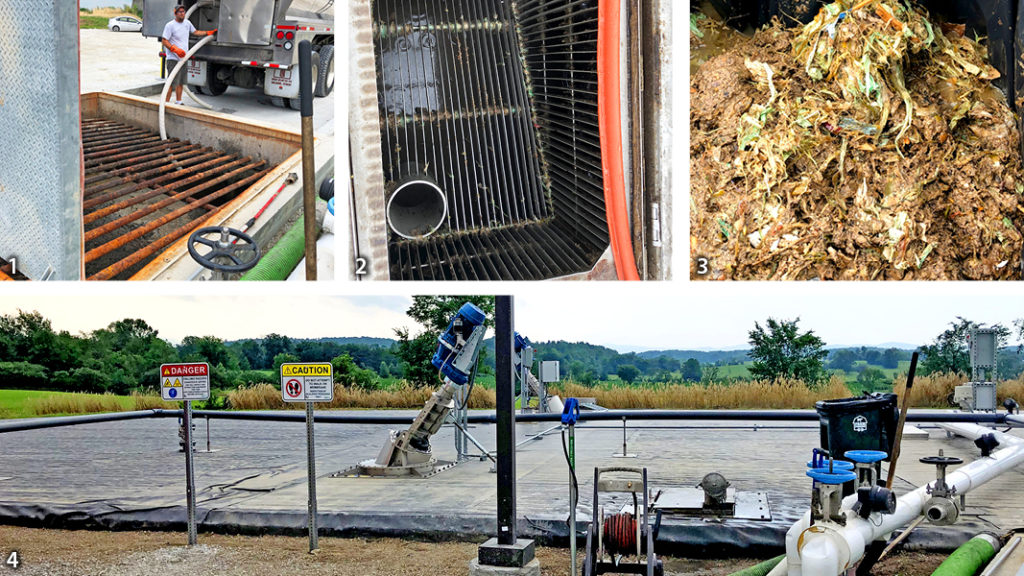
Food waste with solids is unloaded into a receiving tank (1) while liquids flow directly into the hydrolyzer via a feeding line (2). Infeed screens remove contaminants (3). All food waste is captured in the hydrolyzer tank (4) equipped with top-mounted mixers.
“There are over 200 sensors in the plant measuring temperature, volume, height of the contents in the hydrolyzer and flow rate,” explains Billy Connelly, Vanguard Renewables’ Vermont Organics Market Manager. ”In addition, there are alarms to alert our operations team if a valve gets stuck, or the pump isn’t feeding the right quantity to the digester tanks.” The temperature in the hydrolyzer is maintained at 108°F.
He adds that Vanguard samples all food waste feedstocks prior to accepting them, as well as does generator site visits to take samples of all materials they will be receiving. “Our biology team analyzes the samples for COD, BOD (chemical and biological oxygen demand), total volatile solids, nitrogen, phosphate and chloride,” says Connelly. “The goal is to know what we will be receiving when loads come in so we can balance our recipe while materials are in the hydrolyzer. Vanguard also does spot sampling of loads on the trucks to confirm the contents match up to our original samples. Every agreement with the generators also stipulates that if they make any changes to their processes that will affect the biology of the digesters, they need to let Vanguard know.”
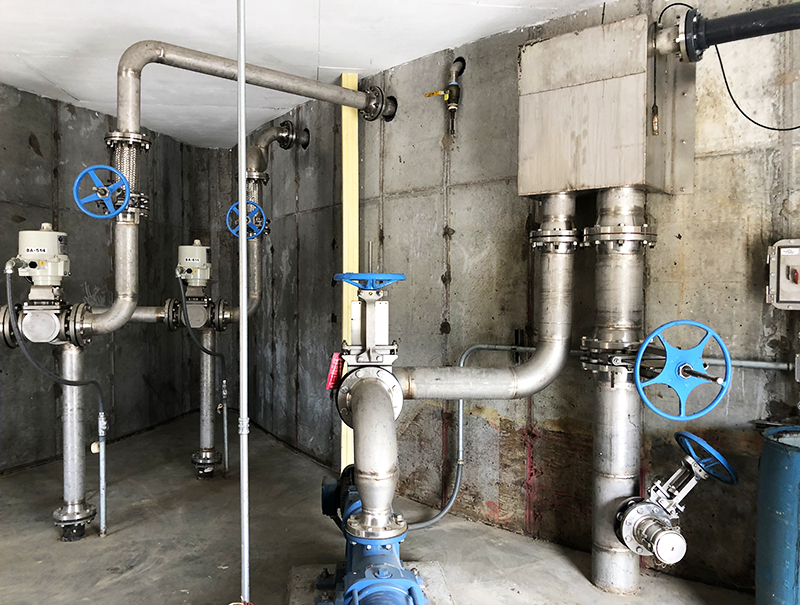
Desired temperatures are maintained in the digester tanks (above) and the hydrolyzer with heat captured from the facility’s 800 kW combined heat and power engine (shown below).
The Goodrich Farm anaerobic digester system includes two digester tanks, each 930,000 gallons. Each tank has a concrete wall in the center, with a mixer on each side of the wall, to create an artificial center for a whirlpool to circulate the contents. Biogas is captured in membranes — two per digester tank. Ferric chloride is fed into the tanks to help precipitate hydrogen sulfide out of the biogas.
Retention time in the digesters is 30 days. The operating temperature averages between 101°F to 102°F. Heat is captured from the facility’s 800 kW combined heat and power engine to maintain desired temperatures in the hydrolyzer and digester tanks. Biogas production averages 545 scfm.
Phosphorus Removal
Digestate flows to a Trident phosphorus removal system, where a trommel screen removes any solids larger than one-quarter-inch; this step also removes any physical contaminants, like wood chips or pebbles. The liquid then flows to a DAF (dissolved air flotation) tank. Polymer is injected; phosphorus binds to the polymer and the air pushes these particles to the top of the surface where they are removed by a skimmer and dewatered by a screw press before being conveyed to a roll-off container. Vanguard is working with composting companies and other partners that are not in areas with excess phosphorus in the soil for reliable outlets for the phosphorus cake.
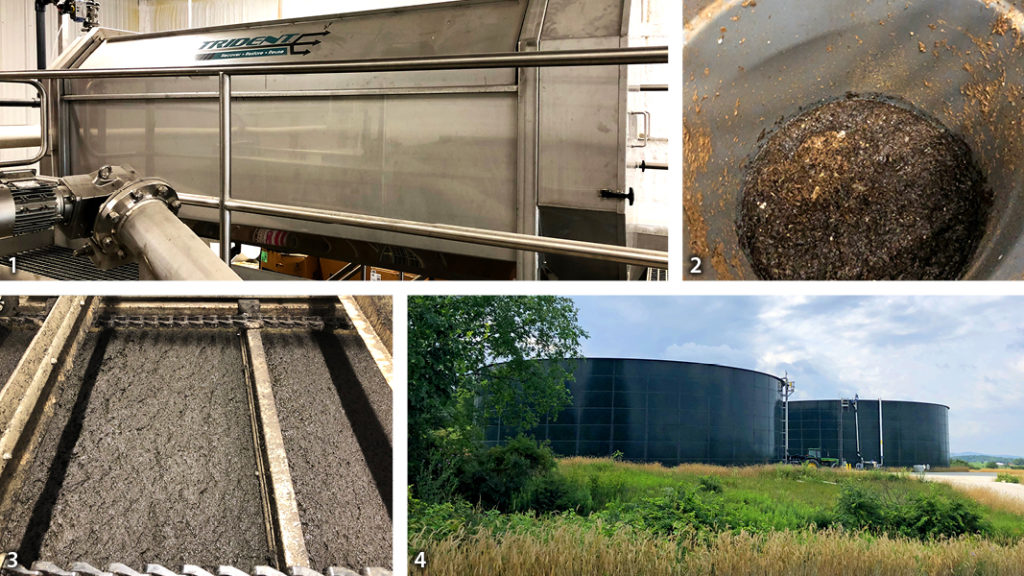
Digestate flows to a phosphorus (P) removal system. A trommel screen (1) removes solids and contaminants (2) larger than one-quarter-inch. The liquid flows to a DAF tank (3) where P is removed. Effluent from the DAF tank is pumped into storage tanks (4) prior to field application.
Remaining liquid is pumped to two 2.5 million gallon effluent storage tanks. The Goodrichs grow 750 acres of corn and 1,750 acres of hay. Some of their acres in corn are 10 miles away so they are installing satellite ponds and transporting the liquid digestate to those sites in a tanker truck. “The P removal system helps keep everything in balance,” says Goodrich Gingras. “Managing manure has become a lot more scientific, and the P removal system is integral to our nutrient management plan.”
RNG Offtake
Vanguard Renewables installed a Quadrogen pressure-swing absorption (PSA) system to upgrade the methane into pipeline quality natural gas. Vermont Gas (VGS) built a RNG injection station on the farm, and installed a pipeline that runs to Middlebury College. The farm has access to the pipeline, as well as neighbors who want to utilize the RNG. Middlebury College signed a 20-year contract with Vanguard Renewables beginning in Fall 2021 to buy 55% of the RNG produced, which will meet one-third of the college’s heating and cooling demands. Middlebury has a biomass gasification plant that supplies the remaining two-thirds. The college plans to transition completely to renewable energy in 2028.
VGS has a voluntary RNG purchase program, “Homegrown Energy,” for its customers. In 2018, it became the first utility in the U.S. to offer customers a retail RNG option. Since no other program like it existed, VGS built the program from scratch, including the accounting, supply management, verifications, and gas quality procedures to introduce this product to the marketplace.
The Goodrich Family Farm facility is the first in the state to produce RNG. Other dairy digesters in Vermont generate electricity. Goodrich Gingras is excited about the opportunity to host Middlebury College students and others to learn about the project and its many facets. The benefits to the community, and the state overall, were articulated by Gov. Phil Scott at the July 21 grand opening: “Think about it — we’ve got a Vermont farm, a Vermont utility, a Vermont College, and national energy innovators all coming together to build a model for our region. And it can be replicated in other parts of the state, and country, as well.”