Digester preprocessing system to be installed by A1 Organics at the Heartland Biogas anaerobic digester in Weld County, Colorado, includes two types of depackaging units.
Nora Goldstein
BioCycle January 2015
About 10 years ago, A1 Organics, headquartered in Eaton, Colorado, began composting food waste at its Rattler Ridge composting site in Keenesburg. “Some colleagues advised us not to do it, citing the potential for increased contamination at the facility,” recalls Bob Yost, A1’s Vice-President and Chief Technical Officer. “Recognizing the need, we went ahead with it but soon ran into challenges with plastic contamination. The effects on our site became significant — primarily litter, but also some product quality issues in terms of what we could remove via screening.”
In addition to stepping up source separation education and training for the generators being serviced, Yost began researching separation equipment to preprocess incoming food waste streams. He learned about the DODA Bio Separator at a trade show, and eventually, A1 moved ahead with purchasing a DODA after it received some grant funding from the State of Colorado. The unit was installed in 2009 at a transfer station that A1 operated at the former Stapleton airport in Denver. “The unit we purchased has an underground vault with about 40,000 gallons of capacity,” explains Yost. “Incoming feedstock goes through a chopper pump at the bottom of the vault, and water and/or another liquid is added to slurry the material, which in turn passes through the Bio Separator to remove contamination. The end product, which is pretty much free of any contaminants, is a 10- to 12-percent food waste slurry. We then transported the slurry by tanker truck to Rattler Ridge.”
The slurry was added to the composting windrows in a ratio of about 80 gallons to 1 cubic yard (cy) of ground yard trimmings, and mixed with a compost turner. “The DODA did a great job removing the contaminants,” he adds. “We saw a significant decrease in litter at the site. We did have a few challenges initially with some of the design elements, e.g., some parts weren’t quite heavy-duty enough in the vault, so those items were replaced. None of the challenges were insurmountable. There is no question that the unit is expensive, but our thinking overall is that what we spent on one end we made back on the other end.”
Digester Preprocessing System
A1 receives source separated organics, including food waste and corrugated cardboard, from restaurants, grocery stores, universities and other institutions and food processors. It offers a tote-based collection service, as well as accepts loads from other haulers. In 2013, the company entered into an exclusive substrate procurement and digested solids marketing agreement with Heartland Biogas, LLC, for Heartland’s anaerobic digester project in Weld County, Colorado. A1 Organics is responsible for delivering food waste, fats, oils and grease, and other non-manure substrates to the digester facility, and working with Heartland to develop high value organic amendments and fertilizer grade products from the digested solids and liquid residuals. The complete mix anaerobic digester is located near a large dairy, and will digest manure in addition to the off-farm substrates. Full-scale operation of the digester is expected to get underway in early 2015.
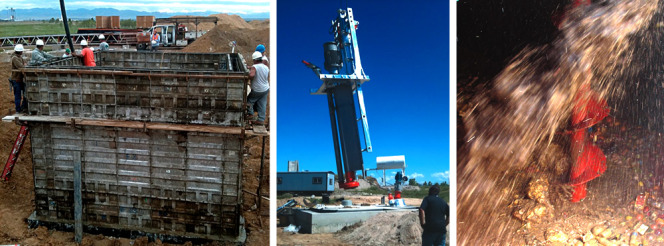
The DODA Bio Separator system has a 40,000-gallon vault (left) with a chopper pump, oscillating serrated auger and other equipment (middle). Incoming feedstock goes through a chopper pump, then water or another liquid is added to create a slurry (right), which in turn passes through the Bio Separator to remove contamination.
Around the same time, A1 also had to start decommissioning its operations at the Stapleton site, which was slated for redevelopment. Plans were made to move the DODA unit to the anaerobic digestion plant as part of a digester preprocessing system (DPS) to be owned and operated by A1. “In designing the DPS, we asked ourselves, ‘What parts of the food waste stream are we not able to process with our current technology?’” says Yost. “One of the limitations of our DODA unit is that lighter materials, such as water bottles and fruit that doesn’t sink, float on top of the contents in the vault, forming a thick layer. The chopper pump is at the bottom of the vault. That material also wasn’t accessible to the oscillating serrated auger the DODA uses to ‘rip open’ containers etc. We also couldn’t put in loads with a high amount of soiled and/or waxed corrugated cardboard. And because of our agreement with Heartland, we had already identified some food waste feedstocks that we couldn’t take because of the commercial packaging, e.g., shrink-wrapped pallets of little cups of cottage cheese or yogurt, and canned or bagged products, etc. that can’t be used for human consumption.”
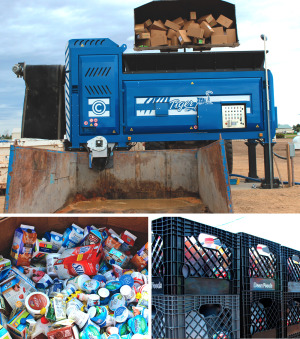
A1 Organics purchased the Ecoverse Tiger HS640 Food Depackager, which has an 8 cubic yard stainless steel hopper that can be fed with a loader (above). Material is pulled into
the vertical mill by augers in the bottom of the hopper; bolt-on paddles, spinning at 1,000 RPMs, remove organics from their packaging. Examples of feedstocks processed include cardboard-packaged dried dog food (in loader bucket above), expired dairy products (bottom left) and gallon jugs of iced tea (bottom right).
The company was approached by Ecoverse, which supplies A1 with the Harvest Quest compost catalyst, about trying out its Tiger HS640 Food De-Packager. The unit has an 8-cy stainless steel hopper that can be fed with a forklift, loader or conveyor. Material is pulled into a vertical mill by two augers in the bottom of the hopper. (The second auger only turns on when it senses the main auger is working too easily and bridging of material may be occurring.) Once in the vertical mill, 19 wear-resistant bolt-on steel paddles, spinning at 1,000 RPMs, remove organics from their packaging, (e.g., Tetra Pak, plastic bags, tin cans, aluminum cans, gallon jugs, plastic pails, etc.). Contaminants are lifted to the top of the mill and extracted by an auger screw. The organics are extruded into a <1-inch (19mm) punch plate screen basket that wraps the entire shaft. At this point, liquid can be added by two incoming lines at the middle of the mill, increasing the percentage of the liquid fraction as needed.
Ecoverse held a demonstration of the Tiger HS640 depackager in September at A1 Organics. Feedstocks processed included cardboard packaged dried dog food, gallon iced tea containers, expired dairy products (milk, yogurt, and cheese), and source separated organics from residential and commercial curbside routes and a large grocery chain. A1 decided to purchase the machine, which will be installed near the DODA unit at the DPS. “With these two systems, we can make a value judgment based on the generator bringing in the material, e.g., cases of gallon jugs of iced tea, or loads heavy in commercial organics,” explains Yost. “And in some cases, we will be able to pull out the soiled or waxed corrugated cardboard and compostable packaging, and divert that to our composting facility as well as have the option to pull out other traditional recyclables (tin, plastic, etc.) for recycling.” Each system processes about 8 to 12 tons/hour of feedstock.
In addition to the DODA and the Tiger, A1 Organics will include maceration pits, pumps, storage tanks and hydration capabilities at the DPS. Press grates and an auger system are being added to break up organic feedstocks that would otherwise float in the DODA unit. “Overall, we’ve designed the DPS so there is lot of redundancy and cross utilization capability,” he adds. “Some incoming streams can go through the DODA and the Tiger, whereas some will only be able to go through one or the other because of the nature of the substrate, the packaging it is in, etc. And some will only need hydration or particle size management without the need to remove packaging. The goal is to deliver substrate material to the digester in the best form possible and not compromise its efficiency by providing substrate with nondigestible heavy solids, glass, etc. so that the digester will generate the most biogas possible.”