Top: Digester tanks at dairy farm in Idaho. Photo courtesy of Biogest
Paul Greene
A key to properly sizing and modeling a biogas digester’s performance is having a good handle on a variety of design factors and waste characterization parameters that play into how large biodigesters must be for a given project and how much gas they will likely make. It is also helpful to be conversant in several different scientific units. This 101 article starts with a quick tutorial on the core design parameters that are in play in the anaerobic digestion process before walking through an example of how to calculate digester sizing and gas yield.
Total And Volatile Solids
Feedstocks are characterized in one of several ways. First the Total Solids (TS) and Volatile Solids (VS) are useful measures whose values are determined by two different drying tests. Total Solids, which is synonymous with the term Percent Dry Matter (DM), is measured by drying a sample of feedstock at 220°F for an hour. The difference between the starting weight and the final weight is the amount of water that was evaporated. The TS percentage is calculated by dividing the final sample weight by its beginning weight. A sample with a final weight of 5 grams, for example, and a starting weight of 20 grams would have TS of 25% — calculated by dividing 5 by 20.
VS is the fraction of the feedstock that the bacteria in a digester will see as a good food source and convert much of it to biogas. As with TS, VS can be determined by measuring the volatile portion of the total feedstock by cooking the dried solid matter at a very high temperature of 1,000°F. This high temperature condition converts all carbonaceous matter into the gas phase. If the 5-gram sample above was converted to one gram of ash particle, the VS of the feed would be 80% as calculated by taking the starting weight (5 grams) and subtracting the end weight (1 gram) and dividing by the starting weight. VS is commonly presented as a percentage of the TS. An analogy would be to overcook something like a pizza in an oven. The TS would be calculated once the pizza was dried after baking too long compared to its uncooked weight. The VS would be calculated if you turned the oven temperature as high as it would go and cook the pizza until there was only black ashes remaining.
Chemical Oxygen Demand (COD)
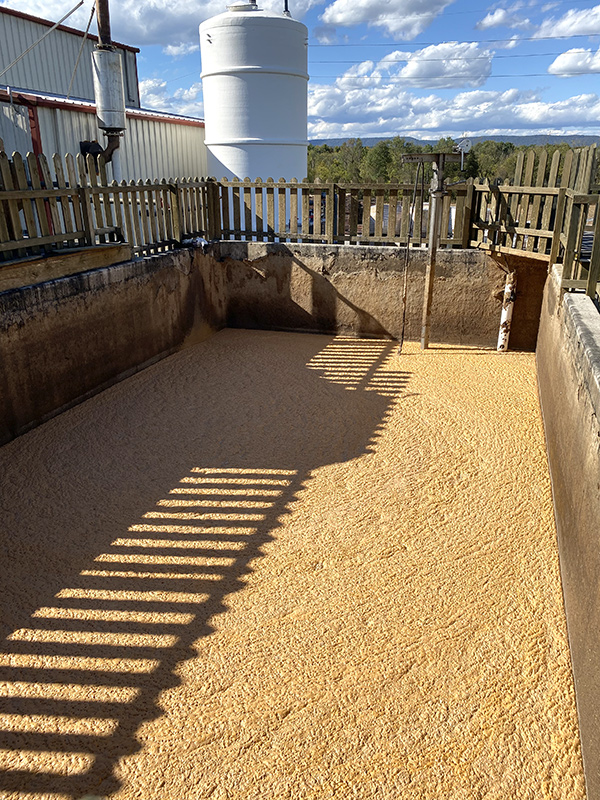
Depackaged food waste slurry to be blended with manure and codigested. Photo courtesy of Reinford Farms
Another useful tool for monitoring feedstock composition is the Chemical Oxygen Demand or COD. COD is measured by adding a powerful chemical oxidant to a sample such as potassium permanganate. The more oxidant a sample consumes, the more carbon is in that sample. Thus, the higher the quantity of oxidant a sample consumes to fully convert to carbon dioxide (CO2), the higher its COD value. Operators will commonly monitor feedstock COD to maintain a steady recipe of feedstock mix to keep the system biology in proper balance. Units of COD are expressed as milligrams per liter of material diluted in water and are commonly in the 100,000 to 300,000 mg/liter range for digester feeding.
When food waste is a feedstock the removal of any packaging or contaminants is monitored. TS, VS and COD are all operational measures at the operator’s fingertips. Typical digesters are run in the 5% to 15% TS range. COD levels should be kept consistent as possible in a consistent recipe to ensure digester health. Projects may need to add water to maintain target feed COD levels.
Additional Key Parameters
OLR (Organic Loading Rate): OLR is the amount of dry matter that is fed to a given volume of digester tank each day. OLR is expressed in metric units as kilograms dry matter/cubic meters (kg/m3)/day and in Imperial units as pounds of dry matter feed to a cubic foot of digester volume each day (lb/ft3/day). A typical OLR is roughly about 3 kg of COD/m3/day or about 0.3 lbs of dry matter/ft3/ day.
Percent Methane: The journey that a sample of organic feedstock takes on its way to becoming biogas includes several discrete biochemical reactions. The outcome is biogas that is a mix of mostly methane (CH4) and CO2. Typical methane levels are 55% to 65% in biogas.
BMP (Biomethane Potential): This is the amount of either methane or biogas that a unit of feedstock is expected to yield per unit of feed. Metric units of BMP are liters of either methane or biogas per kilogram of feedstock (L/kg). Dairy manure, for example, commonly has a BMP of roughly 240 L of CH4/kg of feed (Labatut, 2011). Other feedstocks such as food waste can have a BMP of about 500 L of CH4/kg of feed (Source: StMELF). Imperial units for BMP are expressed as cubic feet of either methane or biogas per pound (ft3/lb) of feed VS. The Imperial equivalent BMP for dairy manure that has 240 liters methane/kg of VS applied would be (240 L/kg) x ( kg/2.2 lbs) x ( ft3/28.3 L) = 3.85 ft3 of CH4 yield/lb of VS applied. Tables 1 and 2 illustrate the BMP of dairy manure and food waste.
VSR (Volatile Solids Reduction): The VSR across a digester is tied to the ratio of easy to digest feed such as fats or carbohydrates or hard to digest material like starches, cellulose and hemicellulose that are in a feedstock. VSR is commonly in the 40% to 80% range. VSR can be fairly subjective and open to interpretation and needs further study in good operating facilities. Having a sense of established data from credible industry literature and from other operating facilities is critical.
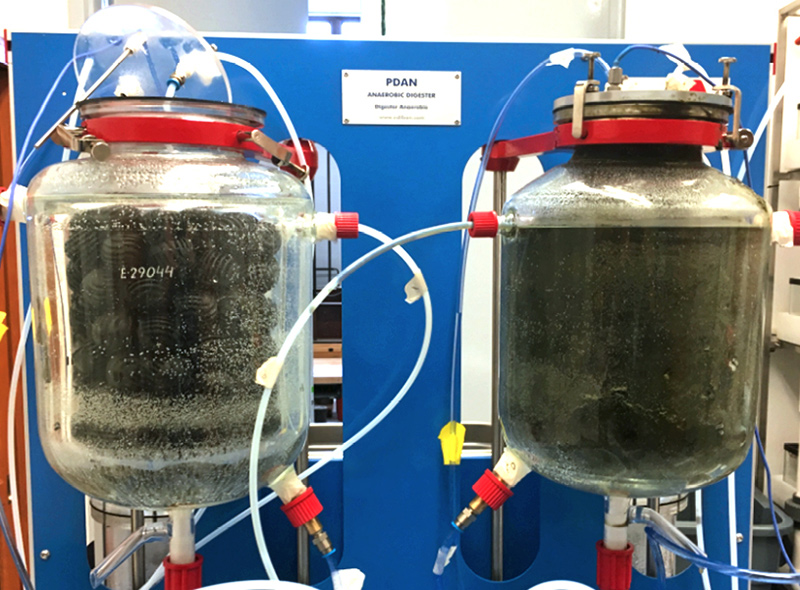
Lab-scale anaerobic digestion tests can be used to estimate biomethane potential of feedstocks. Photo courtesy of U.S. EPA Region 4.
HRT (Hydraulic Residence Time): Digesters can commonly be sized from 20 to 40 days total residence time. The longer the material is held in a digester the more gas is produced. Running BMP trials on a waste can show that gas yield rates will generally rise sharply in 10 to 15 days, start to level off after roughly 18 days and continue to make gas even beyond 40 days. In terms of tank sizing and maximum biogas yield, the key consideration is the BMP test, which shows how a different feedstock will make biogas over time. You get the most bang for your buck in the first two weeks of residence time, and then gas yield starts to flatten out.
Maximum Gas Yield
Ideal Gas Law tells us that one mole (mol) of a gas at standard conditions occupies 22.4 liters of volume. One mol of methane has a molecular weight of 16 and will thereby occupy 22.4 liters. This mass of methane produced can be calculated based on knowing the COD of the waste and the relationship of COD conversion to methane generation. The molecular weight of CH4 is 16 and the molecular weight of the oxygen required to oxidize that methane in a COD test is 64. Conversion of COD in a digester is thereby calculated as:
- COD equivalent of a mole of methane with a molecular weight of 16:
CH4 + 2 (two) O2 => CO2 +2H2O;
16 g of CH4 = 64 g of COD
- 1 g of COD = 0.25 g of CH4
Digester Sizing and Gas Yield Example
How much food waste can be fed to a one million gallon (MG) food waste digester and how much gas might be made? Step 1 is to calculate the feed rate. Step 2 is to calculate the gas yield. Figure 1 illustrates the example provided.
Calculate feed rate:
- Assume:
- Digester is fed at an OLR of 0.3 lbs of dry matter daily per ft3 of digester tank volume per established industry norms
- Feedstock is 24% TS average and 20% VS
- Target feed %TS is 12% per vendor specifications
- Therefore:
- Water (H2O) to be fed at a 1:1 ratio with the feed to maintain proper feed TS%
- 1 MG digester is equal to 133,694 ft3/established conversion
- Math: 0.3 lbs DM/ft3/day digester loading rate x 133,694 ft3 digester volume = 40,108 lbs of DM to be fed daily as the proper feed rate
- 40,108 lbs/day of DM/ 25% TS = 160,432 total wet weight of feed daily = Approximately 80 tons/day of feed material
- 160,432 lbs of feed at 25% + 160,432 lbs of H2O to dilute 1:1
- Total weight of 320,000 lbs of feed at 12% is 38,000 gallons by established conversion.
- To calculate HRT 1 MG digester/38,000 gallons feed/day = 26 day Hydraulic Residence Time — which complies with industry norms
Calculate Gas Yield:
- 40,108 lbs of DM/day in the feed
- From industry references the gas yield of food waste is:
- (BMP is 850 L of biogas per kg of feed) x (kg/2.2 lb) x (1 ft3/28.3 L) = 13.6 ft3 of biogas/lb of VS fed (same as “Dry Matter”)
- Therefore 40,108 lbs/day of DM x 13.6 ft3 biogas/lb of VS added = 545,000 ft3 of biogas/day (yields measured in standard cubic feet/minute (scfm) and metric million British Thermal Units (MMBtu)
- Assume typical 60% CH4 concentration and 600 btu/ft3 of biogas
- Equals 379 scfm of biogas created
- Equals 327 mmbtu/day of fuel value created
- Assume 137,000 btu/gallon of diesel fuel
- Math: 327,000,000 btu per day/137,000 btu per gallon of diesel fuel = 2,386 gallons/of diesel fuel equivalent energy/day
Ultimately, a biogas developer must assess the types of feedstocks and available sources of those feedstocks within a reasonable distance from the AD facility to determine the optimum size digester tank capacity needed for their project and, ultimately, the return on investment. When viewing tank sizing and maximum RNG yield potential from an investment standpoint, there is usually a sweet spot in terms of cost/benefit of building a larger or smaller project. Understanding the direct connection between feedstock composition, feed rate, digester tank capacity, and project gas yield is of paramount importance when considering how large of a project to consider constructing.
Paul Greene is Principal at GreeneTec, LLC and advisory service serving the anaerobic digester RNG market. He has a Chemical Engineering degree from Lafayette College and was the first elected Chair of the American Biogas Council.