Virginia mining company purchases compost to meet certain soil and amendment blend specifications.
Molly Farrell Tucker
BioCycle July 2016
Luck Stone, a mining company headquartered in Richmond, Virginia, has started a new business that incorporates by-products from its quarries into amendments and blends for golf courses, baseball fields, storm water management, streambed restoration, gardens and landscaping. The new business, Luck Ecosystems, was 20 years in the making.
Luck Stone is the largest division of family-owned Luck Companies, which was founded in 1923 by Charles S. Luck, Jr. Luck Stone has 500 associates and mines rocks and sand from its 16 quarries. All are located in Virginia except one quarry is in Pittsboro, North Carolina. The company also has four distribution yards in Virginia.
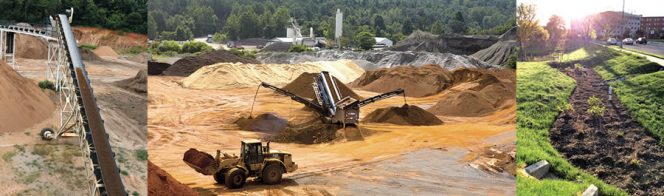
In 2015, Luck Ecosystems incorporated over 11,000 cubic yards of compost into its products at its blending and screening facility (above), including a biofiltration media (left) used in rain gardens (right).
Virginia Tech’s Department of Crop and Soil Environmental Sciences in Blacksburg analyzed several overburden samples and found that Luck Stone’s Greene County Quarry in Ruckersville, Virginia had high quality and consistent material. “That was the beginning of Luck Ecosystems,” recalls Carnahan. “It was a small business for 20 years with two to three associates. However, as we added new associates who were passionate about our products and the positive impact they could have, our purpose transformed into a multifaceted business.”
Luck Ecosystems was officially launched in August 2015. It offers four “families” of products. “Part of the reason to develop product families is because our customers include golf course superintendents, sports field managers, contractors and engineers, and each has unique interests and needs,” he adds. For example, FieldGem mixes are created specifically for ball fields, ranging from local municipal fields to professional team fields. They include blends for the infield and the warning track.
CourseScience products, which contain both sand and compost, are used at municipal and private golf courses for root zones, topdressing and bunker sand. GreenScience growing media, which includes compost in its recipe, is created for construction projects, sports field applications, landscaping projects, and community green spaces. RainScape filtration mixes are designed for storm water management to filter nutrients and sediments during drainage. This product line includes custom-designed biofiltration media, streambed restoration materials, structured soil, compost-amended soil and green roof mixes. “Biofiltration is generally a mix of soil, sand and compost,” notes Carnahan. “Green roof blends are much more complex and include lightweight aggregate that we must import.”
In 2015, Luck Ecosystems repurposed almost 70,000 tons of overburden into its products. “Most of the recipes were developed internally,” he adds. “We regularly produce custom blends for specific jobs and applications. In those cases, we work collaboratively with engineers, designers and customers.” The mixes are tested by several third party laboratories.
Sourcing Compost
Several types of compost are used in the mixes, including yard trimmings, biosolids and paper mill by-products. Luck Ecosystems does not make its own compost. “We work with several compost vendors depending on the product,” says Carnahan. “We have found that specific types and producers of compost work better for some of our products than others. Specifically, in the production of biofiltration soil, we have to be very selective in our choice of compost to meet state specifications. We are required to produce material with low nutrients including less than 40 ppm of phosphorus and greater than three percent organic matter, which is difficult. In our growing media, we source compost that helps the soil retain moisture.”
Luck Ecosystems’ specifications for the compost depend on the product and most often come from the state or municipality where the final product will be used. For example, the specification for compost used in biofiltration media is dictated by the Virginia Department of Environmental Quality.
Luck Ecosystems purchases compost in bulk and arranges transportation with its fleet of contracted haulers. “We regularly meet with compost suppliers to provide demand forecasts to give them enough time for their compost production cycles,” he adds. Most of its products are sold in bulk as well, although some materials are bagged at Luck’s production facilities.
The Greene quarry in Ruckersville is the primary production facility. In the early 2000s, Luck Stone repurposed aggregate processing equipment into an automated blending facility at the Greene Plant that has the ability to accurately proportion up to six raw materials at a time, using pug mill mixer. This past spring, Luck Ecosystems began production of growing media and storm water management products at several additional quarries throughout Virginia.
Molly Farrell Tucker is a Contributing Editor to BioCycle.