Anaerobic digestion systems are being upgraded to accept food waste and FOG to boost energy generation.
Diane Greer
BioCycle July 2012, Vol. 53, No. 7, p. 37
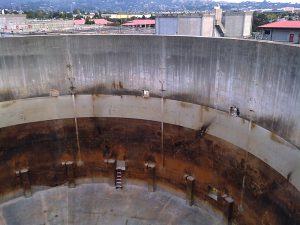
Central Marin Sanitation Agency cleaned out and is upgrading its existing digesters with membrane covers and pump mixing systems (inside of cleaned digester shown above).
Installation of receiving stations for codigestion of hauled-in waste is becoming an increasingly common upgrade at WWTFs. “In just 5 years we went from nobody doing codigestion to just under five percent that are doing this,” says Lauren Fillmore, senior program manager at the Water Environment Research Foundation (WERF). “That’s impressive.”
Upgrades For Codigestion
The Central Marin Sanitation Agency (CMSA) in San Rafael, California, is overhauling its vintage 1985 anaerobic digestion system, installing new covers, mixers, biogas purification equipment and supporting systems. Bundled into the project is a receiving station for hauled-in organic waste for codigestion. Based on projected volumes, codigestion of fats, oil and grease (FOG) and commercial food waste could almost double biogas production. “Hopefully at some point in the future we could become energy independent,” says Jason Dow, CMSA general manager.
CMSA is leveraging about 109 tons/day of excess digester capacity to bring in additional organics to increase biogas production. At current capacity the facilities two digesters produce approximately 140,000-standard cubic feet/day (sscfd) of biogas, enough to run a 750-kW dual-fuel Waukesha engine up to 12 hours a day. “During the other 12 hours a day we buy natural gas for fueling the engine,” Dow says. “If we process 20 tons/day of food waste we should produce enough biogas to see another 5 to 6 hours of run-time.” The addition of FOG and other food waste could increase biogas production sufficiently to operate the facility solely on renewable energy.
Structural work on the receiving station, designed to accept 5,000 gallons/day of FOG and 20 tons/day of food waste, is completed and installation of equipment and the Sulfatreat biogas purification system is underway. Dow expects to start accepting FOG and food waste deliveries from private haulers in late fall.
The first of CMSA’s two digesters has been cleaned and upgrades are replacing the floating cover with a membrane cover and replacing the gas mixing system with a pump mixing system. Work on the second digester will begin in the fall after the first digester is operational. Project completion is slated by early 2013.
In Johnson County, Kansas, installation of a FOG receiving station at the Douglas L. Smith Middle Basin WWTF will help the facility reduce greenhouse gas emissions by increasing production of biogas. Upgrades include two GE Jenbacher 1,060-kW combined heat and power (CHP) cogeneration units, biogas/natural gas fired boilers, a WesTech DuoSphere™ membrane gas holding facility and gas cleaning equipment.
Codigestion of FOG is expected to double biogas output and provide enough fuel for the cogeneration system to satisfy most of the facility’s electrical needs, says Dale Gabel, vice president of CH2M Hill in Englewood, Colorado. Annual power cost savings are estimated at $500,000/year, with greenhouse gas reductions of 9,700 metric tons of CO2-equivalent.
At the City of Gresham’s WWTF in Oregon, sustainability and energy independence are key goals behind the construction of a FOG receiving station. The 20-mgd plant, maintained and operated by Veolia Water NA, set a goal to be 100 percent energy independent by 2014. The goal is in keeping with the City’s objective to achieve 100-percent sustainability. “The City of Gresham has really aggressive sustainability goals,” explains Thad Roth, biomass program manager at the Energy Trust of Oregon. “They see their WWTF as a way to focus attention on the steps they are taking in making progress toward that goal.”
Currently a cogeneration system, fueled by biogas, provides 55 percent of the facility’s energy needs and solar panels provide eight percent. Digesting the FOG should increase biogas production enough to allow the facility to reach near energy independence and save $21,000/month in electric bills. Concurrently the sustainability initiative is targeting energy efficiency measures, such as replacing the digester mixing system and installing high-efficiency aeration blowers, which have reduced energy usage by 10 percent.
Biogas Utilization
When planning digester upgrades more WWTFs are starting to look at alternative uses for biogas. A recent survey done for WERF’s forthcoming report, “Barriers to Biogas Utilization at WWTFs,” found that two-thirds of the facility operators interviewed are currently flaring the gas, but are thinking about how to use it instead, says Beecher of NEBRA, who worked on the survey.
“Currently less than 10 percent of facilities with anaerobic digesters are using the biogas for anything other than the boiler to heat the digester,” Gabel explains. “But with more utilities focused on energy efficiency and energy production there is a desire to use biogas in a beneficial way and the biggest use is generating electricity onsite.”
Calculating the economic benefit of using biogas for onsite generation involves several factors such as power rates, facility size, renewable energy incentives and ROI (return on investment) criteria. In some parts of the country, like the southeast, low power rates and little available money for renewable energy make onsite generation a harder sell. Likewise, smaller scale facilities find it more difficult to make onsite power cost-effective. “The dollars per kilowatt drops as the facility scale increases, just as it does in most processes,” explains Patricia Scanlan, director of residual treatment technologies at Black & Veatch.
The economic criteria used to analyze alternative uses of biogas can also be an impediment. “One big problem in our industry is that many utilities use simple payback as an evaluation tool and then insist that a very short payback term, like 5 to 10 years, is needed to justify a cost-saving project,” says John Willis, vice president of Brown and Caldwell in Atlanta, Georgia. “Wastewater utilities very rarely have opportunities to save money.” The more typical scenario, he continues, is complying with consent orders and tighter permit limits that make them spend more money on equipment, which costs even more to operate once installed. “It’s surprising that when you offer a project that will save money, some utilities may insist on a 5-year payback,” he adds. “We are developing an evaluation as part of the final phase of the Barriers to Biogas project that contrasts simple payback with methodologies more commonly used by private industry like present worth, internal rate of return, and benefit-to-cost ratios that should be used instead.”
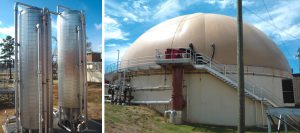
At the Columbus, Georgia Water Works, heat captured from the gas engines heats the CSTR thermophilic digester feeding two plug flow thermophilic digesters (right). A Duosphere biogas storage tank (left) also was installed.
The system, designed by Brown and Caldwell, is called Columbus Biosolids Flow-Through Thermophilic Treatment (CBFT3) and is composed of one CSTR (continuous stirred tank reactor) thermophilic digester feeding two plug flow thermophilic digesters (10-ft in diameter by 30-ft high). From the plug flow digesters, material flows to two existing 1.2-mg mesophilic digesters, which accomplish additional solids reduction and further reduce possible biosolids odors. Extensive testing demonstrated that CBFT3 could meet the EPA’s requirements for producing Class A biosolids with a 6-day minimum retention in the thermophilic digester followed by 30 minutes in the plug flow reactors.
Typically production of Class A biosolids requires sludge to be held in batch tanks for 24 hours at 55°C. “So instead of building 24 hours worth of batch tanks we built 30 minutes worth,” Willis explains. The patented process, owned by CWW, was given to WERF for the public good and use by any other utility. “We firmly believe these types of things should be shared,” Arnett says. “If only 10 percent of utilities were to utilize the technology it has the potential of $2 billion in construction cost savings nationwide.”
Codigesting FOG and conversion to temperature-phased (thermophilic followed by mesophilic) operation is expected to increase volatile solids destruction rates and increase biogas production by 25 to 50 percent. Properly disposing of grease and using it as fuel will eliminate the grease clogging problem in the sewer lines. Long term, the objective is to bring in additional hauled-in organics to enable the South Columbus plant to become energy neutral. Upgrades include a DuoSphere membrane gas holding cover that stores gas on top of the thermophilic digester and two plug flow anaerobic digesters, a gas cleanup system composed of VOC removal and an iron sponge, and a 12,000-gallon FOG receiving station.
The reciprocating engines are expected to produce 50 percent of the facility’s electricity. Previously one-third of the biogas generated was used to fuel boilers heating the digesters; the remainder of the biogas was flared. Heat captured from engines and the sludge exiting the plug flow digesters will maintain the digesters at thermophilic temperatures. “We’re not only improving the carbon footprint by producing renewable power but also eliminating about 5 percent of methane gas going to flare that actually escapes unburned to the atmosphere,” Arnett says. Adds Willis: “The idea was to make a lot of power, meet almost all of our heat demands to get up to our Class A temperatures and make a closed loop system that does not require any outside or fossil-fuel-derived energy.”
Alternative Biogas Uses
A few trail-blazing utilities are looking at advanced biogas uses, including conversion of biogas to vehicle fuel. The option is becoming more attractive when comparing rising vehicle fuel prices to relatively stable electricity prices and natural gas rates. At the same time, the cost to purify biogas to CRNG (compressed renewable natural gas) is dropping. “There are companies developing and supplying relatively low cost cleaning and filling systems to convert biogas to CNG,” Scanlan explains.
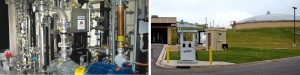
Biogas is conditioned in the BioCNG unit (below), then routed to a CNG fueling station (left) where it is further dried and compressed for vehicle fueling. Photos courtesy of Unison Solutions
CRNG is produced using the BioCNG process, developed by Dubuque, Iowa-based Unison Solutions. The system pipes biogas to a conditioning unit that removes moisture, hydrogen sulfide, VOCs and carbon dioxide (CO2) from the gas. The cleaned gas is then routed to a CNG fueling station where it is further dried and compressed for use in CNG vehicles. As part of the project, the wastewater utility recently purchased four CNG vehicles and plans to replace the remainder of its fleet with CNG vehicles over the next several years. The project, completed in May, was supported by a $125,000 grant from the State of Wisconsin, and is part of a $32 million upgrade and expansion of the Janesville WWTF.
EPCOR, owner and operator of the Gold Bar Wastewater Treatment plant in Edmonton, Alberta, Canada, is considering converting its excess biogas into CRNG. The upgrade would be the last phase of a project intended to increase capacity and improve the performance of its anaerobic digestion system. During the winter, when temperatures can drop to minus 40, there is a high demand for heat to warm the digesters. Due to low electricity rates, EPCOR opted to install two new boilers to heat the digesters instead of a cogeneration system. “There are times when it takes every bit of biogas to heat the digesters,” says Dave Parry, Senior Vice President, CDM Smith. “But they still get a lot of excess biogas during the summer.”
CDM Smith conducted a study to analyze alternative uses for the excess biogas. In Canada, gasoline and diesel are more expensive than in the U.S. due to higher taxes. As a result, offsetting high fuel prices with CRNG is more economical than producing power, Parry explains. “The cost to clean the biogas to pipeline quality is comparable to putting in a CHP system. Then you have the cost to compress it. So it costs about the same or a little bit more to produce CRNG than to buy CNG because natural gas is cheap right now. But they feel there is more value with a renewable fuel and it is in their control.”
A few utilities are considering purifying and upgrading biogas for pipeline injection. Natural gas utilities require very high levels of CO2 removal from the biogas, which makes pipeline injection fairly expensive, Scanlan of Black & Veatch explains. “Typically CO2 removal costs as much as all the other cleaning processes (removing H2S, siloxanes, etc.). That is one of the reasons why CNG looks a little more attractive than pipeline injection. You do not need to meet as stringent CO2 limits.”
The Point Loma Treatment Plant in San Diego, California, recently completed such a pipeline injection project. The facility produces over 1.3 million scfd of excess biogas, about a third of its total gas production. Generating additional electricity from the excess biogas was not economical. The facility already produces more electricity than it uses, selling about 3.5-MW of power to San Diego Gas & Electric (SDG&E). Exporting additional electricity required expansion of the cogeneration facility and an expensive upgrade of the onsite SDG&E substation to increase its export transmission capacity.
The City of San Diego issued an RFP seeking to sell the excess biogas. Biofuels Energy, LLC in Encinitas, California secured the long-term rights to purchase the gas and in February completed a $45 million “direct biogas” project that injects purified biogas into natural gas pipelines for delivery off-site to three fuel cells supplied by Fuel Cell Energy generating 4.5- MW of power (see “Directed Biogas To Power Fuel Cells,” June 2011). A biogas purification skid supplied by Air Liquide Advanced Technologies was installed. The project is made possible by $14.4 million in incentives from California’s Self-Generation Incentive Program along with Federal Investment Tax Credits and New Market Tax Credits.
Diane Greer is a Contributing Editor to BioCycle.