Anaerobic digester facility in Ontario is retrofitted to enable processing of a wider range of organics, including food scraps.
Tom Ferencevic
BioCycle August 2016
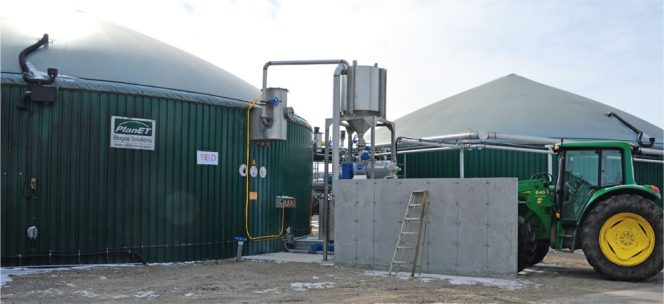
Bayview Flowers’s anaerobic digester was originally designed to process clean organics feedstocks, such as grape pomace and dairy manure.
Over time, however, local supply and demand dynamics made it very difficult for Bayview to find clean, preconsumer organics. To remain competitive, the facility needed the ability to receive a wider range of materials as well as to show some market differentiation to waste haulers. This required: 1) Implementation of a pasteurizing system to meet a higher standard of regulatory requirements; and 2) Installation of contaminant removal equipment to reduce digester downtime and produce a digestate suitable for land application.
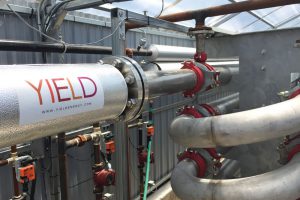
Bayview chose to integrate the Yield/Fitec double tube external heat exchanger behind the second digester vessel to achieve pasteurization in
that tank.
Supply And Demand Dynamics
Ontario has been in a hyper-competitive supply and demand marketplace for organics because of the high density of processing facilities ranging from composting operations to biogas plants, and the absence of provincial regulations requiring diversion of organics from landfills. Additionally, preprocessing or contaminant removal capability is currently limited to only a few digesters; waste services companies have not set up preprocessing facilities (as of July 2016).
Farm-based ADs have been the most disruptive to the organics marketplace since they have the lowest capital and operating cost structure, and therefore can charge the lowest tipping fees to process the organic waste. Yield estimates that at present, municipal, commercial and farm-based anaerobic digesters in Ontario represent about 500,000 metric tons (MT)/year of commercial organic waste processing capacity. This estimate is determined by adding up all existing AD facilities in Ontario and the amount of waste they are permitted to process.
There are variations in permitting between the sites as well as a wide variation in their designs. Digesters in Ontario don’t all have the same technical or operational capability to process the same types of organic waste. All ADs in the province utilize continuous stirred tank reactor (CSTR) type designs.
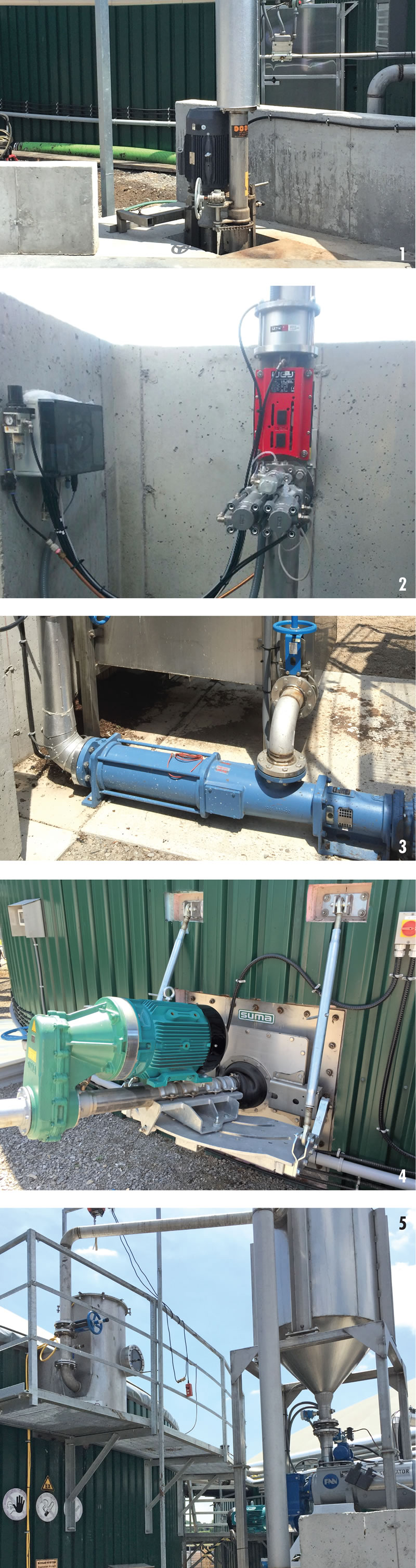
(1) New food waste receiving tank equipped with DODA chopper pump. (2) Yield-Fitec analyzer to monitor biological performance. (3) Wangen pump to transfer digestate into secondary digester. (4) Suma mixer in secondary digester. (5) FAN separator to filter skimmed substrate.
Technology And Design Options
The original design of the 250 kW Bayview biogas plant, built by PlanET Biogas Solutions, consisted of a 1,000 cubic meter (m3) primary digester, and a 1,000 m3 secondary vessel with insulation and a double membrane roof. The primary fermenter is a standard agricultural type design with paddle and submersible mixers, dry feeder, liquid manure feeding, but no pasteurization step. The secondary tank has one mixer, and was not plumbed for heating. The original feedstock mix was (approximate amounts) — on an annual basis — 4,000 MT of grape pomace and tulip bulbs, 2,000 MT of dairy manure, and 1,000 MT of off spec pet food.
Varying feedstock combinations and volumes with existing supplies were modeled using Yield’s AD software program called BioTip, but the total solids (TS) content of the grape pomace was too high and required adding too much dilution water (>25%), to keep the operating TS below 10 percent. It was concluded that the Bayview AD could not generate 250 kW unless food waste could be accessed, which also would keep the digester’s TS below 10 percent. In order to process a wider variety of food waste streams, pasteurization and contaminant removal equipment would have to be installed.
Ontario has two options to achieve pasteurization of feedstocks — treat at 70°C for one hour, or at 50°C for 20 hours (pasteurization rules for farm-based systems). Bayview had the choice of installing a pasteurizer either prior to feeding the digester or post digestion but prior to removal of digestate from the site. Evaluating the energy balance showed that with a 250 kW system, the available engine heat may be inadequate to guarantee 70°C for one hour consistently throughout the year.
Some site space constraints and traffic flows from regular greenhouse facility operations had to be considered, along with existing system feed lines, gas condensation and other buried piping that had to continue to be accessible. Ultimately, Bayview chose to integrate the Yield/Fitec double tube external heat exchanger behind the second vessel, thus converting it into a thermophilic digester as well as a pasteurizer. Advantages to increasing the operating temperature with a high organic total solids feedstock include: Increase in biogas yield of the slowly degradable (cellulosic) fraction of the grape pomace; and Reduction in the viscosity of the contents for easier pumping, mixing and reduced sedimentation.
The existing primary digester could not be retrofitted with an automated grit removal system due to the center column and paddle mixers being fixed to the floor. Thus a side-mount tank skimmer was installed to remove the floating contaminants such as plastics. The compromise is that floating contaminants can be removed, but not the settling/grit fraction. The advantage is the digestate produced will be free from visible contaminants but the digester will still accumulate grit over time and require a shut down for cleanout.
Equipment from a variety of vendors was installed as part of the new design, including: Food waste receiving tank (160 m3) with DODA ME 120 chopper pump; Yield-Fitec fully automated bicarbonate and volatile fatting acids (VFA) analyzer to improve biological performance monitoring; Wangen model KLS-50S pump with adjustable flow rates for transferring filtered digestate to the thermophilic digester; Suma mixer to ensure proper mixing in the secondary digester vessel; and FAN separator with 1 mm (0.04 inch) screen for fine filtering of the skimmed substrate to ensure all digestate is suitable for beneficial reuse.
Other changes include: New overhead pipe to avoid damaging buried ones and provide for easy leak detection; “Borrowed” one 8-inch gas line to “T” into the new flood waste feed line; Automation of all food waste pumping and liquid transfer; Added valve on the existing 12-foot “blub” line to properly isolate the primary digester during pasteurizing; and Installation of 316 stainless pipes for all food waste slurry transport.
The upgraded Bayview anaerobic digester is fully operational and able to process food waste with various supply contracts being negotiated.
Tom Ferencevic is VP Technical Services and Sales with Yield Biogas Inc. in Toronto, Ontario (tom.ferencevic@yieldbiogas.com).