Top: The new 3-acre windrow pad is used for compost curing. Photo by Nora Goldstein
Nora Goldstein
In 2008, the Chittenden Solid Waste District (CSWD), which includes Burlington, Vermont and surrounding communities, purchased a composting facility from The Intervale Center, which had started the site in 1997 at the Intervale, a 700-acre tract along the Winooski River in Burlington. The facility, called Intervale Compost Products, started by composting leaves from the City of Burlington, and gradually expanded to accept food waste streams from commercial and institutional generators, and several food manufacturers, along with manures and other source separated organics.
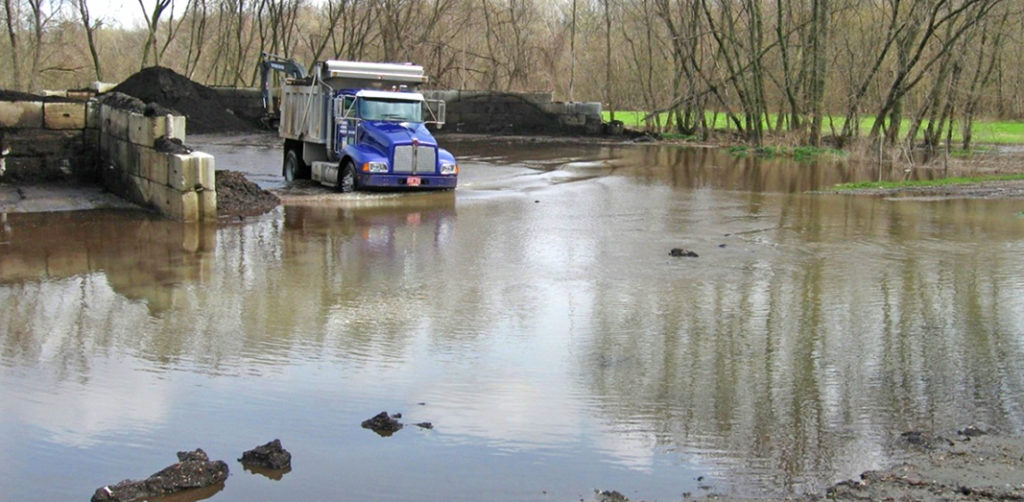
The original composting site in the Intervale had to be relocated as it had expanded to a point where it was within a flood zone.
Around the time CSWD acquired the composting site, new permitting requirements made it clear that a new location was needed. Many years of growth led to expansion beyond its original footprint along the Winooski River. In 2011, CSWD moved the facility to a new location in Williston near its main office. A year later, CSWD changed the name of its composting facility from Intervale Compost Products to Green Mountain Compost (GMC).
The new facility has six aerated static pile bunkers under a roof with in-ground pipes, and two bunkers for food waste tipping and blending with amendment. Each bunker can hold 330 cubic yards of material. Phase 1 of active composting takes place in the bunkers, followed by a second phase in aerated static piles on an adjacent uncovered pad with moveable above ground aeration pipes. The fresh piles in the bunkers are covered with a layer of Phase 2 compost to mitigate odor generation. The site had limited space with only 7.2 acres dedicated to organics processing so following active composting, material was screened and then moved into a larger static pile for curing in an adjacent sandpit with unimproved surfaces. Throughout this time period, incoming food waste was mixed with leaves and yard trimmings and/or wood chips in a mechanical mixer. Piles were then turned with an excavator and front-end loaders.
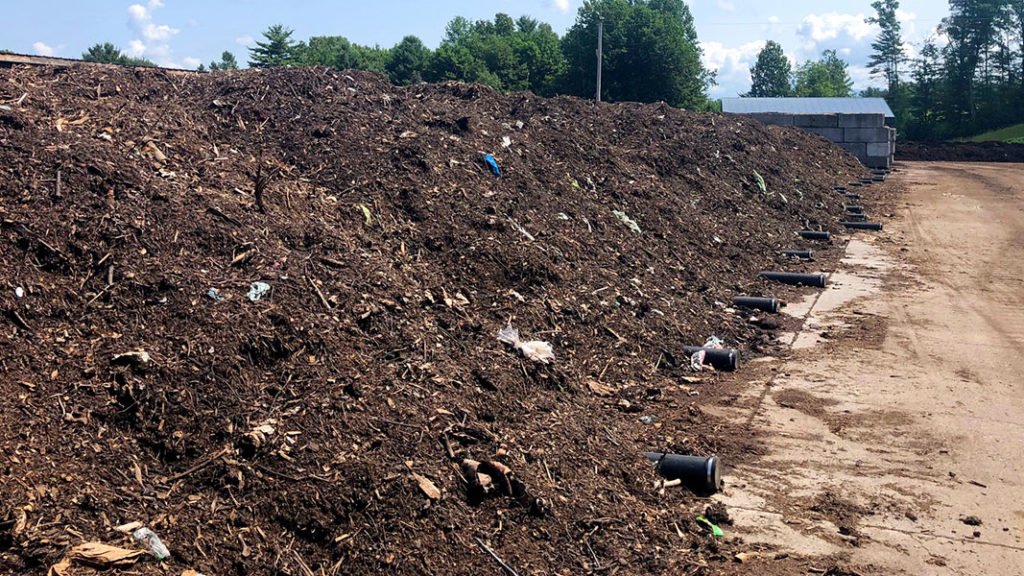
The second phase of active composting is done on an open pad with moveable, above ground aeration pipes. Residence time in Phase 2 is three weeks.
Food Waste Flow
Green Mountain Compost is Vermont’s largest food waste composting facility. The state’s Universal Recycling Law, passed in 2012, bans disposal of all food waste in landfills. Mandatory compliance was phased in over six years, beginning with the largest generators of organic waste (104 tons/year of food scraps generated) on July 1, 2014 — if an organics recycling facility was within 20 miles, had available capacity, and was willing to accept the food residuals. Generation thresholds gradually decreased over the years and compliance based on distance from an organics recycling facility was phased out. All food scraps were banned from landfill disposal as of July 1, 2020, including from the residential sector.
“The incoming quantity of food waste plummeted when restaurants closed in spring 2020 due to the pandemic, but by the summer and into the fall of 2020, the flow of food waste increased,” recalls Dan Goossen, CSWD’s Director of Composting. “We were on track to receive around 7,500 tons of food waste for the year. It had reached a point where it was a challenge to match that quantity with the needed carbon amendment.”
Anticipating this impact from a full ban on food waste from disposal, CSWD had contracted with SCS Engineers to do a business assessment of its operations, along with a design for an upgraded facility to successfully manage the increased volume of food waste. Notes a summary by SCS Engineers of the situation, “The increase in materials, coupled with the layout and design of the Organics Diversion Facility (ODF), led to inefficiencies. The facility operations required excessive materials handling, extensive residency times for the compost, and low yields of the finished compost. In addition, CSWD was using a two-phase ASP process, followed by screening and curing. Early-stage screening resulted in a low fines yield.”
The firm’s recommendations included:
- Combining ASP and turned windrows to achieve process and cost efficiencies. Purchase and use of a windrow turner and dump truck, in conjunction with CSWD’s existing Phase 1 ASP system, would create a versatile system that efficiently produces high quality material.
- Grading and surface improvements for both the windrow pad and the sales area to allow year-round use, processing, and materials sales.
The upgrade increased the facility’s composting space to 13 acres, and will enable GMC to sustainably process more than 6,000 tons of food scraps annually. However, food waste flow to the composting site decreased in the first part of 2021 when Casella Waste Management opened a food waste depackaging facility, also in Williston, that January. “The depackaging facility ramped up the quantity of food waste it was receiving in April and May 2021, redirecting material Casella had previously been bringing to GMC,” says Goossen. “In all, we received 4,500 tons of food waste in 2021. That ended up working well, as the flow better matched our available carbon.”
Site Sustainability
Construction of the upgraded facility was completed in February 2021. The expanded curing pad and screening/retail area were built on the old sand pit that had been used for curing and compost screening. It took 1,000 trailer loads of stone to bring up the sides of the pad and level the surface. “We now have about 7 acres of improved surfaces,” notes Goossen. “The windrow curing pad takes up about 3 of those acres while the remainder are dedicated to screening, blending, storage, and customer loading.”
Two key pieces of equipment were procured: a $380,000 Backhus windrow turner and a used 20 cubic yard-capacity landfill truck. Inspired by the multiple windrow turner applications in place by Ken Newman at Royal Oak Farms in Virginia, GMC opted to maximize the windrow turner in all aspects of production — as a replacement for the mechanical mixer on the front end of the process, turning curing windrows after ASP, and finally mixing screened compost with other materials for producing soil blends. Previously, two old trommels were used exclusively for blending and screening value-added soil blends with compost. The truck replaced having to move compost in loader buckets, one at a time, for the relatively long haul from the active composting pad to the curing area.
The turner also is used between Phase 1 and Phase 2 during active composting. Partially composted material is moved out of the bunker to the center working area (in between the Phase 1 and 2 locations) and turned twice with the windrow turner. Moisture can be added if necessary.
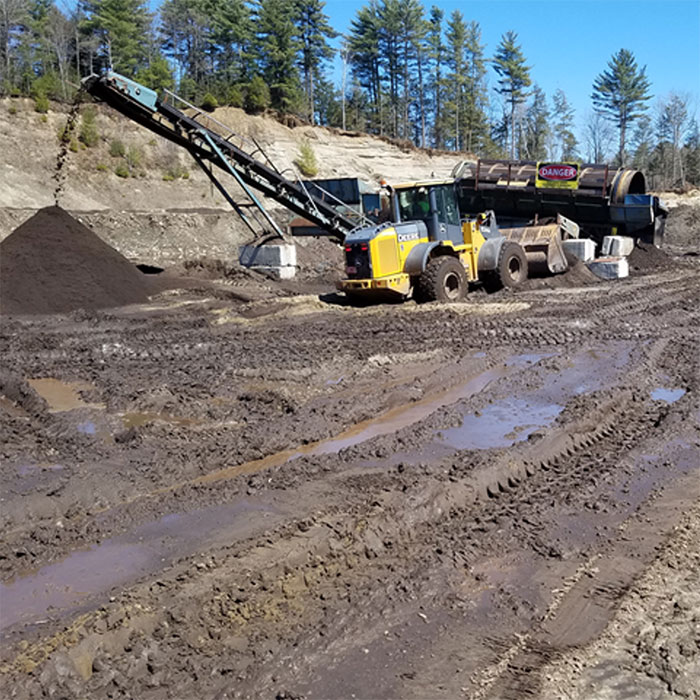
Prior to site upgrades, curing and compost screening were done on an unimproved pad situated in a sand pit. Photo by Greg McCarron, SCS Engineers
Windrows for curing are 8-feet tall and 16-feet wide. The piles are turned 8 to 10 times prior to screening. “It used to take about two weeks to turn the curing compost piles,” notes Goossen. “Now it takes about three hours!” He adds that the turner chews up plastic that is in the compost, blowing out particles that accumulate between the windrows. Staff have tried all manner of contamination removal including utilizing leaf blowers to help gather it up. “The amount of contamination increased significantly when the final phase of the disposal ban went into effect in July 2020,” he says. “We stopped accepting certified compostable bioplastics in January 2022, with the idea that it would reduce the amount of look-alike conventional plastic items. While we don’t have data to prove it, we’re happy to report that the piles are already noticeably better, with less overall obvious contamination.”
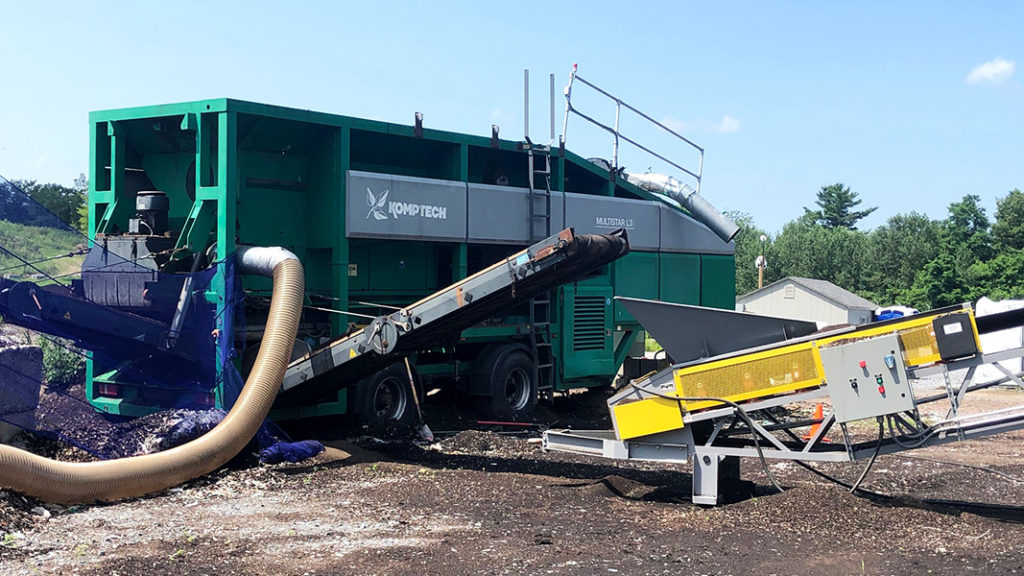
A star screen equipped with a windsifter located on the improved surface area on top of the sand pit.
Total cost of the upgrade was about $1.36 million, which was offset by a $500,000 grant from the Vermont Agency of Natural Resources. In addition to purchasing the turner and truck, GMC got a stacking conveyor for its screening area, which enables more efficient materials handling during screening. With reductions in incoming plastics, GMC can now recycle some of the screened overs back into the composting process. A trommel followed by a star screen equipped with a windsifter are used for the screening process. GMC is awaiting delivery of a new trommel that will be used to screen out large fractions (mostly film plastic) between the ASP and windrowing phases.
Overall, downsides to the changes include the need to add additional moisture to the windrows during curing, and the chopping of plastic contamination when turning. Conversely, compost yield has improved, the finished compost is more homogenous and made in a shorter timeframe, and having the turner reduces the costs of labor, fuel, and equipment maintenance.
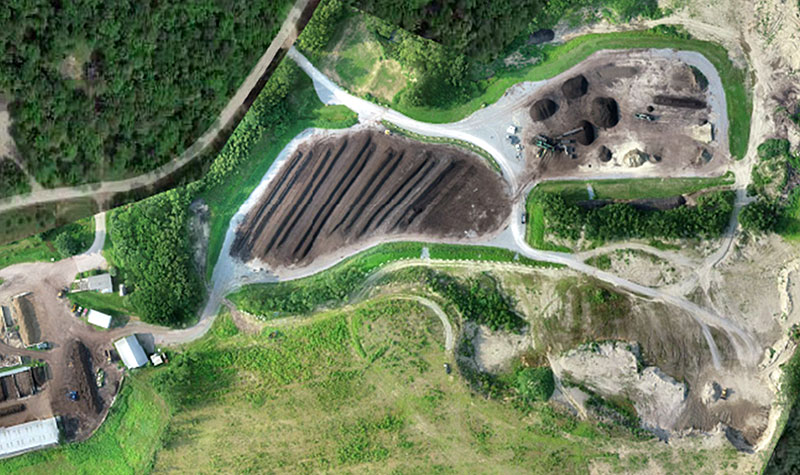
The new windrow composting pad (center) and screening/retail yard (upper right) are on about 7 acres of improved surface. The covered bunkers and a portion of the aerated static pile pad are visible in the lower left corner. Photos courtesy of Green Mountain Compost
The tipping fee for source separated food waste is $65/ton. There is no fee for yard trimmings. Several years ago, GMC stopped bagging its compost product and now sells in bulk only. “We sold out of compost in 2020 and 2021 — two record sales years in a row,” says Goossen. “We make a garden blend and a topsoil blend, and supply about a dozen garden centers and a number of landscapers. This year, we’ve been surprised to reach similar sales volumes as demand continues to be stronger than expected. We’re happy to report that we’ve made it through the peak spring sales season without running out of inventory, but it may very well happen again before the summer is out.”