Top: Incoming load of food waste prior to mechanical preprocessing. Photo courtesy of Jim Miller
Jim Miller and Craig Coker
As described in the recent two-part BioCycle CONNECT series on food waste depackaging systems (Part I, Part II), the driving principle underlying mechanically preprocessing food waste for anaerobic digestion (AD) or composting is, in part, a search for order that invariably requires segregating targeted organic materials from a mixture of many waste materials. In its simplest form, separation is a binary process that has one input, the heterogeneous feedstock, and two outputs, the extract (recovered material, e.g., organic slurry or cake) and the rejects (e.g., waste packaging or contaminants). Segregation of organic materials requires identifying the appropriate characteristic (i.e., a “code”) by which separation can be done and optimized. The ability of a system to identify a code and to perform some function, actively or passively, on that material as a result of that information is called “switching” or segregating the material according to that identified code.
The purpose of this two-part facility design article is to take a look at existing food waste preprocessing systems and dive a little deeper into how different systems, including ancillary infrastructure, are tailored for subsequent uses. Part I discusses synergies with the various types of AD technologies. Part II covers residuals management.
Digester Types
Food waste preprocessing systems are designed to produce a feedstock for further treatment. Depending on the downstream technology, desired characteristics and quality of the feedstock may vary significantly. Common goals regardless of ensuing processes are to maximize solids content to maximize biogas production, minimize the amount of water that is being transported, and eliminate as many contaminants as possible. Anaerobic digester types fall into two general categories: wet and high solids.
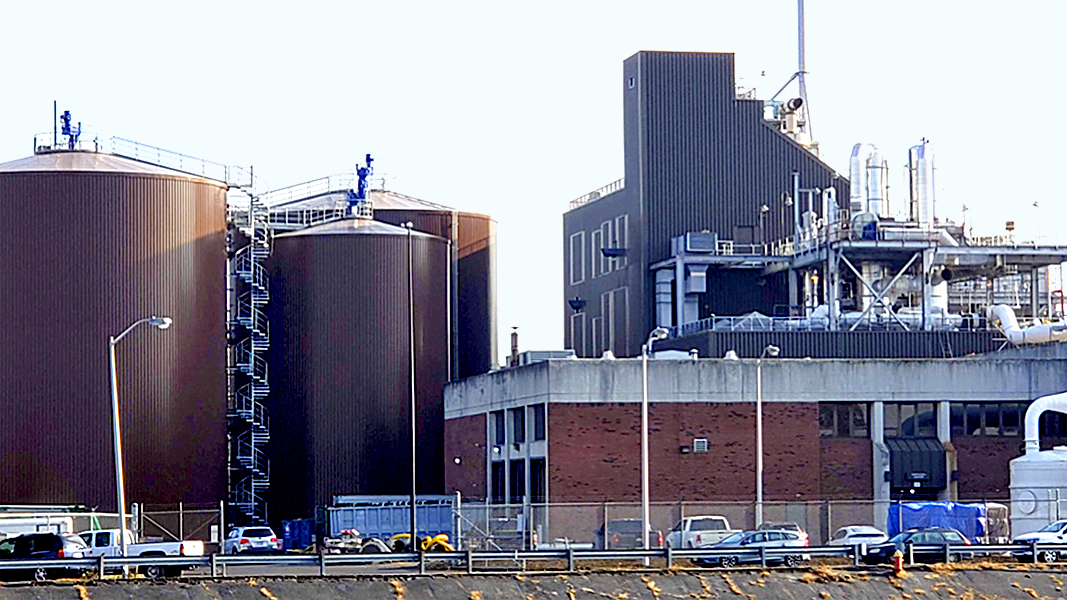
Wet digester system installed at Trenton Biogas in Trenton, New Jersey. Photo courtesy of Trenton Renewables
Wet Digestion: Occurs in a continuously stirred tank reactor, typically a very large vessel with an enormous amount of liquid that sustains the biology. Solids content inside a wet digester is normally in the range of 2% to 5%. Food waste being prepared for wet digestion is typically made into a slurry with a solids content of approximately 15% or less. Material with this range of solids content can be pumped into trucks for transfer and later pumped into the head works or a holding tank at the digester site. Process water may be required to achieve the desired solids content.
For wet digestion, minimizing solid contaminants such as papers, plastics, metals, and inert materials prior to the digester is critical. Depending on the type of separation equipment and the processing capabilities of the receiving facility, this may require an extra step involving a centrifugal separator with finer screening.
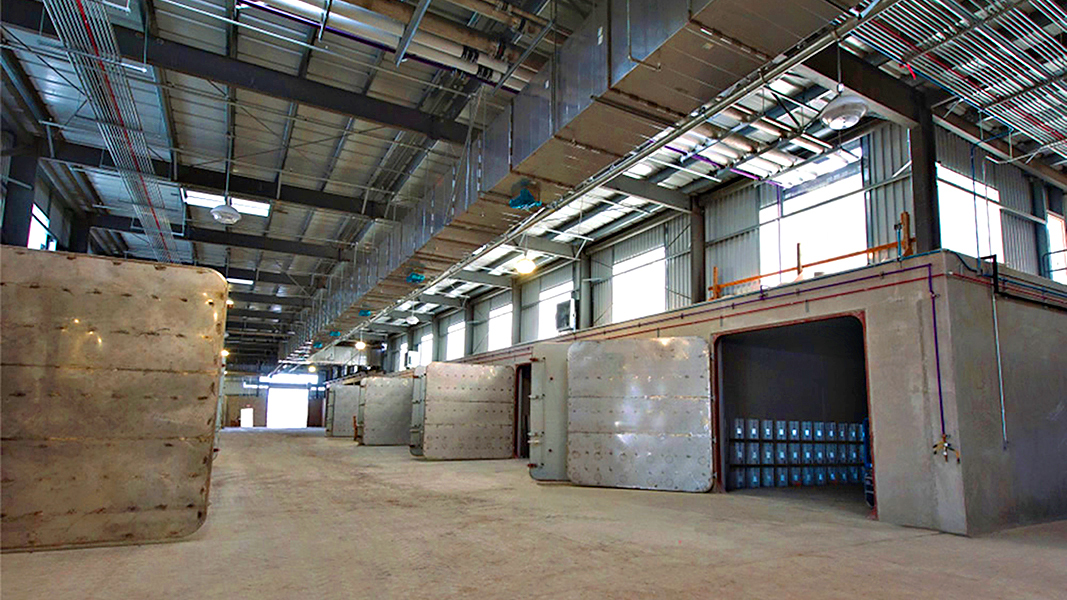
High solids dry fermentation anaerobic digester installed at Zero Waste Energy Development Corporation in San Jose, California. Photo courtesy of ZWEDC
High Solids AD: HSAD consists of two types of technologies: plug flow and dry fermentation (leach bed). These technologies were developed to process biodegradable materials that are not good feedstocks for wet digestion — principally green waste and compostable papers and cardboard. Digestate from HSAD processes is typically composted or aerated for drying purposes and used as a soil amendment or for landfill cover. HSAD (and composting systems) can be a little more forgiving about contaminants, although the cost of contaminant removal from the finished product is a deterrent.
Plug flow AD systems are horizontal or vertical tubular structures with mechanical methods to move substrates through the digestion reactor. They can process feedstocks with a wide range of solids content up to approximately 25% as well as higher levels of solid contaminants. Preprocessed food wastes with higher levels of solids are typically referred to as cake instead of slurry. Food wastes being preprocessed for plug flow digestion are often mixed with shredded green waste to produce a blended feedstock. Inoculation with finished digestate occurs prior to or upon injection into the digesters. The ratio of food waste to green waste to digestate can be altered to produce a feedstock with a targeted consistency that best accommodates the type of digester.
Dry fermentation (leach bed) digesters can process solids contents in the range of 40%. Dry fermentation systems employ large garage-style tunnel reactors with gas-tight hatches and an overhead soaking system that saturates the biomass with inoculant (also called percolate). The resulting biological process purges air from the digester and creates a thriving anaerobic environment. Feedstocks with very high levels of contamination can be processed with dry fermentation technology. Typically, food waste slurry or cake is blended with a high proportion of green waste to produce a feedstock that can be transported with belt conveyors or front-end loaders. To maximize digestion and biogas production, it is important to produce a well-graded, blended feedstock with high porosity to enable the inoculant to reach the maximum amount of material surfaces. This is different from other AD technologies where wastes are typically shredded and screened to produce a feedstock of uniform size.
Eliminating contaminants to achieve purity levels that satisfy governmental regulations or market demands is a challenge for compost from HSAD digestate. Minimizing contamination through better source separation and refusal to accept incoming wastes with contaminant levels above a certain percent is a strategy that is often employed. Removing contaminants from the feedstock during preprocessing may be an economical approach, which is the primary design goal for food waste preprocessing systems. Contaminants that remain after digestion must be removed from the finished compost or digestate.
Due to variations in feedstock and specifics of different preprocessing and digestion technologies, operational cost data for preprocessing and material handling of food wastes are difficult to benchmark and compare. However, it’s clear that for a given waste stream, wet digestion requires the most preprocessing or source separation, dry fermentation the least, and plug flow and direct composting is between the two.
Handling Food Wastes
The footprint and material flow for a food waste preprocessing facility (Puente Hills Materials Recovery Facility) are illustrated in the graphic below. This Puente Hills MRF is owned and operated by the Los Angeles County (CA) Sanitation Districts (Districts). Processed food waste is transported in tanker trucks and taken to the Districts’ wastewater treatment plant for codigestion.
Food wastes may arrive at the processing facility as a relatively dry solid material or as a slurry or liquid. Slurries and liquids are typically pumped or conveyed into holding tanks while solid wastes are placed into bunkers where they can be accessed by mobile equipment. Decisions on whether to make a liquid slurry or a higher solids cake depend on the type of digester to be used, ability of a composting facility to handle slurried food wastes, distances between preprocessing and ultimate recycling, and similar considerations.
Food wastes managed as solids are normally staged in concrete bunkers. The bunkers must be designed to resist acid attack and abrasion from equipment operations. A concrete topping with ultra-fine cement such as EucoFloor 404 is recommended for this application. Concrete mixes for the parent slab should have a low water:cement ratio to minimize shrinkage and surface cracking.
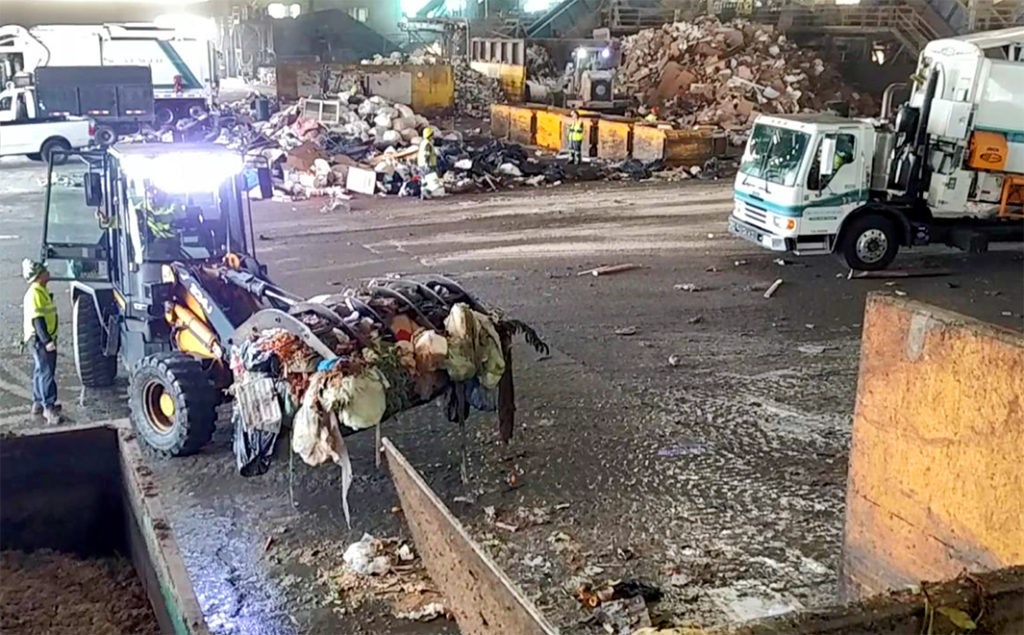
Bunker walls must be designed to retain the fluid pressures from the stacked food waste as well as impacts from equipment. Photos courtesy of Jim Miller
Bunker walls must be designed to retain the fluid pressures from the stacked food waste as well as impacts from equipment. Concrete and steel walls can perform well for this application. For concrete walls, providing an embedded steel plate from floor level up to 4-feet high — where the most abuse and chemical attack occur — is recommended. Receiving hoppers for preprocessing systems are often embedded into or connected to bunker walls depending on the type of construction. Bunkers and the areas under preprocessing systems must also be designed to contain leachate and washdown water. A rolled curb or trench drain can be used for this purpose. Leachate typically has high organic content and is captured and pumped to tanks or equipment for treatment.
For food waste slurries, liquid storage tanks are the most cost-effective storage solution prior to feeding into a digester reactor or to a compost mixing system. Slurry tanks offer the potential to analyze the food wastes and meter them into a digester reactor at controlled rates to minimize potential for ammonia toxicity or digester foaming due to excessive volatile solids. Storage tanks can be fiberglass or glass-lined steel. At the Vanguard Renewables depackaging facility in Agawam, Massachusetts, slurry is sorted into different tanks depending on its “strength.” “We can actually ‘grade’ the feedstocks so we know their energy content and value, e.g., low, medium and high, and then balance out a tankload for a digester,” explains John Hanselman, Founder and Chief Strategy Officer of Vanguard Renewables.
Depending on the volume of materials received, staged and processed, food wastes can be highly corrosive to steel structures and cladding. Food wastes with high moisture contents and washdown water can contribute to a humid atmosphere that may increase corrosion and possibly affect electrical equipment and devices. These effects can be addressed through adequate ventilation, proper sealing of electrical components, and appropriate finishes.
Process water may be needed for food waste preprocessing, depending on downstream requirements. Typically, operators try to avoid this, especially if the slurry is being transported to its recycling destination (adding to shipping costs). Good housekeeping in and around preprocessing systems and receiving bunkers is important for controlling odors and vectors. Floors should be properly sloped with drains provided to catch washdown water. Unreachable areas and voids that cannot be accessed and cleaned should be eliminated.
Jim Miller is CEO of J.R. Miller & Associates, a consulting engineering firm in Brea, CA. He can be reached at jrmiller@jrma.com. Craig Coker is a Senior Editor at BioCycle CONNECT and a Principal at Coker Composting and Consulting near Roanoke VA. He can be reached at ccoker@jgpress.com