K.B. Specialty Foods’ new anaerobic wastewater system upgrade adds “ease of operation” to food manufacturing plant.
Dan Emerson
BioCycle October 2018/h6>
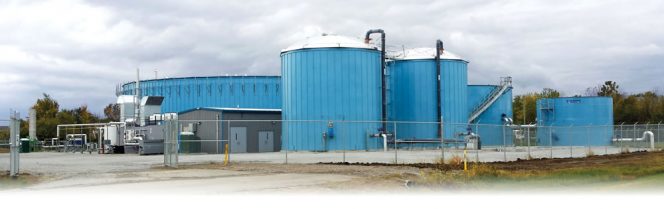
The anaerobic wastewater system receives an average of about 200,000 gallons/day of food processing residuals. The system can handle swings in production.
Earlier this year, the Kroger Co. announced the successful start-up of a new, $9.5 million anaerobic digester to treat wastewater and generate electricity at K.B. Specialty Foods, a manufacturing plant owned and operated by Kroger in Greensburg, Indiana. The plant produces deli salads, cake icing and refrigerated side dishes. It has been a zero waste facility since 2014, diverting more than 90 percent of its waste stream from the landfill annually.
As part of its ongoing environmental sustainability commitment, K.B. Specialty Foods decided to upgrade its conventional (aerobic) wastewater treatment system, which consisted of a primary dissolved air flotation clarifier followed by an activated sludge system.
The new system features a low-rate, anaerobic reactor from Pittsburgh, PA-based Evoqua Water Technologies, which owns the ADI Systems brand. The ADI BVF® reactor treats wastewater streams with moderate to high concentrations of organics (COD/BOD), suspended solids, and fat, oil, and grease (FOG), typically without the need for primary treatment. Food solids entering the system need to be ground up and screened to 56 millimeters — about a quarter-inch, according to Dan Bertoldo, a process engineer with ADI Systems.
The start-up of the new reactor began in September 2017, and included an acclimation period of about two months, during which the amount of material being fed into the reactor was gradually increased. Currently, the anaerobic wastewater system receives an average of about 200,000 gallons/day, notes maintenance engineer Mike Bokelman.
Because wastewater from the plant comes in surges, the system has a wastewater equalization feature to even out the flow. Two 150,000-gallon tanks can store wastewater for periods of time before it is put through the digester. The system is designed for future expansion to treat up to 325,000 gallon/day.
Retention time in the anaerobic reactor — from entry to the wastewater process to discharge to the city sewer — is between two and three weeks. “This is a ‘low flow’ system — which means we retain a relatively large volume compared to the amount entering and discharging each day,” Bokelman explains. Adds Bertoldo: “With the long retention time, changes in performance happen slowly, giving the operator time to observe and react. It also gives the ‘bugs’ more time to digest the organics.”
Wastewater enters the reactor through an influent distribution system beneath the sludge bed. Different environments are created in the reactor tank by adjusting the operation of process equipment over time. This results in a repeating sequence of process events such as filling, mixing, aerating, settling, and decanting. Clarified effluent discharged from the reactor is required to meet the municipal discharge limits on biochemical oxygen demand (BOD, 200 mg/l), total suspended solids (TSS, 200 mg/l), total Kjeldahl nitrogen (TKN, 20 mg/l), fat, oil, and grease (FOG, 100 mg/l), and pH (5-10).
Biogas Capture
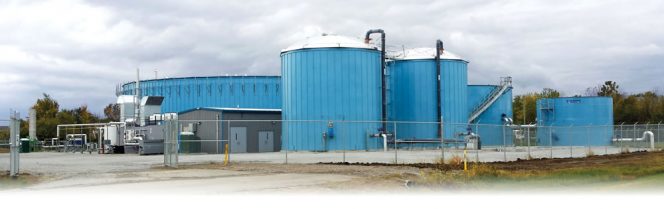
The anaerobic wastewater system receives an average of about 200,000 gallons/day of food processing residuals. The system can handle swings in production.
The anaerobic reactor has a Geomembrane Technologies biogas collection cover. It floats on the surface, enabling operators to vary the amount of liquid in the reactor as the type of food waste changes. The cover also has a half-inch layer of insulation to provide heat retention. The system uses an “iron sponge” method to remove hydrogen sulfide from the biogas and eliminate foul odors.
A 600 kW generator set runs on a blend of natural gas and biogas, to maximize efficiency. Any biogas that is not utilized in the genset is combusted in an enclosed biogas flare. Power generated is sent to the plant’s electrical grid; recovered heat is supplied to the BVF reactor. Sludge that remains as a by-product of the process has a high nutrient content. It will be land applied once enough has accumulated, which should happen sometime in 2019.
K.B. Specialty Foods’ new wastewater system upgrade “has added ease of operation to our facility,” says Bokelman, noting that the previous aerobic facility “was out of capacity due to production increasing and changing over the past 28 years. A different product mix in addition to more production caused the loading to be different at the wastewater facility. The new anaerobic system has more capacity and can handle swings in production much more easily, giving us much more flexibility as a plant. In addition, it handles our wastewater in such a way that we can add fewer chemicals and spend less time managing in a narrow operation window. We also are using less natural gas.”
The installation at K.B. Specialty Foods is Kroger’s second anaerobic digester facility. The first digester was installed in 2013 at the Ralphs-Food 4 Less distribution center in Compton, California (see “Grocery Chain Unveils On-Site Digester,” June 2013). It processes food waste backhauled from grocery stores, as well as wastewater from an adjacent creamery operated by Kroger. The facility has a 2 million gallon reactor tank, and a 250,000-gallon staging tank for incoming material.
Dan Emerson is a Contributing Editor to BioCycle.